the Creative Commons Attribution 4.0 License.
the Creative Commons Attribution 4.0 License.
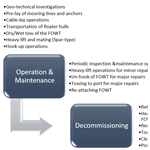
Floating wind turbines: marine operations challenges and opportunities
Rahul Chitteth Ramachandran
Cian Desmond
Frances Judge
Jorrit-Jan Serraris
Jimmy Murphy
The global floating offshore wind energy industry is rapidly maturing, with several technologies having been installed at pilot and demonstration scales. As the industry progresses to full array-scale deployments, the optimization of marine activities related to installation, operation and maintenance, and decommissioning presents a significant opportunity for cost reduction. This paper reviews the various marine operations challenges towards the commercialization of floating wind in the context of spar-type, semi-submersible and tension leg platform (TLP) technologies. Knowledge gaps and research trends are identified along with a review of innovations at various stages of development, which are intended to widen weather windows, reduce installation costs, and improve the health and safety of floating-wind-related marine operations.
- Article
(2858 KB) - Full-text XML
- BibTeX
- EndNote
Wind turbines are moving further offshore to deeper waters and are exploiting higher wind speeds in harsher environments (McCann, 2016). This trend creates additional challenges in the design, installation, operation, maintenance and decommissioning phases of an offshore wind farm. Numerous investigations for developing efficient and optimum floating offshore wind turbine (FOWT) platforms and various innovative design concepts have been evolving in the last few years (Uzunoglu et al., 2016; EWEA, 2013). Several pilot- and demonstration-scale floating wind farms are now operational in different parts of the world (e.g. WindFloat Atlantic – Portugal (25 MW), Hywind Scotland (30 MW)), and there is a robust pipeline of projects which is expected to deliver 250 GW installed floating capacity by 2050 (DNV, 2020; James and Ros, 2015).
To realize this ambition, significant reductions in LCOE (levelized cost of energy) will be required across all key stages in the development of a floating wind farm. Numerous marine operations are required in the last three stages of the floating-wind-farm life cycle (see Fig. 1). Marine operations represent a significant proportion of the offshore wind energy costs. Approximately 15.2 % of CAPEX (capital expenditure), 50 % of OPEX (operational expenditure) and 80 % of DECEX (decommissioning expenditure) are directly related to marine operations for a bottom-fixed wind farm (Judge et al., 2019). Comparative figures for the floating-wind-energy industry are unavailable due to a lack of projects; however, investigations by Castro-Santos (2016) show that approximately 36 % of the total floating project costs are incurred during the installation, exploitation and dismantling activities. Castro-Santos et al. (2018a) have revealed that the size of the floating wind farms has a considerable impact on installation costs and LCOE. It was found that the LCOE reduces as the farm size increases.
Given the nascent nature of the floating-wind-energy industry and the lack of established best practices, these operations present a significant scope for optimization and cost reduction. The FOWT industry has a significant second-mover advantage and can benefit from the technical expertise and innovations developed in the offshore oil and gas (O & G) and fixed-wind-energy industries. However, the deployment of highly dynamic unmanned floating platforms is unprecedented and requires the development of bespoke solutions to reduce the cost and increase the safety of installation-, operation and maintenance (O & M)-, and decommissioning-related marine activities.
There is overlap across the life cycle for the various technologies and procedures for floating offshore wind turbines. For example, assessment and prediction of metocean conditions are always required for installation, O & M and decommissioning of floating wind farms. Towing vessels are also required in all these operational phases of a wind farm. So, it is beneficial to combine all the studies in those areas and investigate all of them together instead of treating them separately. The marine operations vary depending on the floater used; hence while selecting the floater, it is important to have a firm understanding of the marine operations required in each phase of its life cycle. Since marine operations represent a significant proportion of the total costs incurred for a wind farm, this knowledge aids the precise modelling of the costs. Many innovations have been recently introduced or adapted from other industries to take advantage of array-scale deployments possible for FOWTs. These innovations are also needed to be examined from a marine operation point of view. Since the floating-wind domain is new and maturing, there is a shortage of literature that focuses on marine operations. This paper examines the various challenges and opportunities concerning marine operations during installation, O & M and decommissioning phases of a floating wind farm.
Floating wind platforms can be mainly classified into three broad categories according to the restoring mechanism for attaining hydrostatic equilibrium. They can be ballast-stabilized, buoyancy-stabilized, mooring-stabilized or combinations of these (Leimeister et al., 2018; Banister, 2017; Booij et al., 1999). Figure 2 demonstrates how the different FOWTs developed around the world fit into a stability triangle.
Generally, the installation of floating wind turbines requires a greater number of vessels compared to bottom-fixed wind turbines, but the vessels are cheaper to hire and easily available (Crowle and Thies, 2021). Even though many floating-wind concepts have been developed, only a few have been successfully deployed and commissioned at a commercial level. In the following sections, a review of the projects that have reached the Technology Readiness Level 7 (TRL7) (EC, 2017) or above is provided with a focus on the marine operation strategies which they employed.
2.1 Spar type: Hywind Scotland project
Hywind Scotland is a floating offshore wind farm which has a rated capacity of 30 MW, produced from five 6 MW turbines, and has been functioning since 2017 (Equinor, 2022b). The spar-type floater, namely the Hywind concept, was developed by Equinor ASA (Equinor, 2022b; Skaare, 2017). A 2.3 MW demo (TRL 8) (OREC, 2015) was deployed on the west coast of Norway in 2009 for a test run of 2 years (Butterfield et al., 2007; Equinor, 2022b). Following the demonstration, a wind farm was installed 30 km off the coast of Aberdeenshire, Scotland. The farm has an area of approximately 4 km2 and an annual average significant wave height of 1.8 m (Mathiesen et al., 2014).
The spar-type substructures have high draughts which require the use of offshore assembly. The installation phase also requires sheltered coastal waters (maximum significant wave heights are up to 0.5 m and a Beaufort wind force 4; DNV, 2015) for some operations. This is a challenge as sheltered waters with high depths are required near the construction sites due to the high draught of the floaters. They should either be available near the ports or be made by dredging. Figure 3 shows that the first marine operation was the installation of the suction anchors and the mooring lines. The floaters were first wet-towed out into a sheltered area using tugboats. Then they were upended using water ballast. Later, the water was pumped out and solid ballast (magnetite) was filled using a rock installation vessel. The tower-and-rotor assembly was mated with the floater later (Jiang, 2021). This was done using the heavy-lift vessel, Saipem 7000 (Saipem, 2017). A notable feature of the Hywind installation was the use of this expensive heavy-lift vessel. Significant cost cuts may be achieved by innovative installation methods in the future by avoiding the use of such vessels. After the mating, the wind turbines were towed to the location of the wind farm. They were then connected to the pre-installed mooring lines, and final ballast corrections were performed.
Metocean assessments were performed before the commencement of the project to check for suitable weather windows for marine operations. The duration characteristics of marine operations were predicted for various limiting conditions of wind and waves for a full year (Mathiesen et al., 2014). The months from April to September were found to have the widest operational time windows. The inshore assembly (upending, solid ballasting, heavy lift) and offshore installation operations (anchor and mooring, transfer and installation of wind turbine generators, cables) were scheduled and carried out in this period.
The operation and maintenance of the wind turbine mounted on the spar-type substructure are similar to that of a bottom-fixed offshore wind turbine. A campaign-based inspection and monitoring scheme is planned for the FOWTs. Maintenance and repairs of the sub-sea systems (foundation, mooring system, cables) will follow a different approach. Periodic sub-sea inspections and maintenance will be performed using ROVs (remotely operated underwater vehicles). Scour might also be an issue concerning the Hywind spar-type platforms as they employ suction anchors. Heavy component exchanges up to 2 t will be performed using the platform crane and a crew transfer vessel (CTV). Heavier components like the transformer can be exchanged using a dynamically positioned offshore service vessel. In the case of even larger components, the turbines have to be towed to a sheltered region, and exchange will be carried out using heavy-lift vessels (H. H. Hersleth, 2016).
The decommissioning of the spar-type platforms could be more expensive compared to other types of platforms. The platform has to be partially decommissioned in deep water due to the high draughts before getting towed to the quayside. The blades, nacelle and tower can be dismantled using a heavy-lift vessel; this incurs additional costs. The mooring lines and anchors also must be retrieved. Easily recoverable anchors can reduce decommissioning costs and time. There is scope for further investigations to develop cheaper and easy decommissioning strategies of spar-type FOWTs.
2.2 Semi-submersible type: WindFloat Atlantic and Kincardine projects
In 2011, Principle Power installed a prototype semi-submersible FOWT, namely WindFloat, 5 km off the west coast of Portugal (Roddier et al., 2010). This was followed by the installation of a 25 MW floating wind farm on the west coast of Portugal. The wind farm consists of three MHI Vestas 8.4 MW turbines mounted on Principle Power’s semi-submersibles (Banister, 2017). The installation operations were carried out with the help of tugs, AHTS (anchor handling tug supply) vessels and ROV-support cable-lay vessels supplied by Bourbon Offshore (Ocean-Energy-Resources, 2020). The towing operation took 3 d, taking the completely assembled FOWT from the port of Ferrol, Spain, to the farm located 20 km off the coast of Viana do Castelo, Portugal. The AHTS, Bourbon Orca (Ulstein, 2022), was used for the operations, which is an advanced vessel with a bollard pull of 180 t and a maximum speed of 17.1 kn. Most AHTSs were constructed to serve the O & G industry, but they make a good choice for floating-wind-farm installation since there is good availability, and they can be used for the installation of anchors and for towing purposes. One of the floaters was loaded out and floated off using a semi-submersible barge, Boskalis Fjord. Compared to the Hywind project, specialized expensive heavy-lift crane vessels were not employed here. Castro-Santos et al. (2013) has observed that the installation of anchoring and mooring systems is less expensive using an AHTS compared to a combination of barges and tugboats.
The Kincardine offshore floating wind farm is another project which employs semi-submersible floaters for the wind turbines (offshorewind.biz, 2021). The wind farm is located 15 km off the coast of Aberdeen, Scotland. It features a wind farm with a nameplate capacity of 50 MW. All of the floaters were constructed in Fene, Spain, and transported to Rotterdam for mounting the 9.6 MW wind turbines (Umoh and Lemon, 2020).
Semi-submersibles are buoyancy-stabilized floaters. The stabilizing righting moment is contributed either by the large water-plane area of the hull or small cross-sectional areas at some distances from the central axis (Leimeister et al., 2018). They can be fully constructed and assembled onshore. The installation of mooring systems is less expensive compared to other types of floaters, which makes semi-submersibles one of the most cost-effective solutions from an installation point of view (Liu et al., 2016). However, the construction costs are higher compared to other types of floaters since they are larger and heavier structures (James and Ros, 2015). The semi-submersible wind turbines are completely constructed onshore and towed to the wind farm location and connected to the pre-installed mooring lines. Light drag-embedded anchors can be used for semi-submersibles. The main challenge in the installation process is finding the right weather window for the marine operations as they are more sensitive to wave heights during towing (Banister, 2017). The installation of the three FOWTs in the WindFloat project took place in October 2019, December 2019 and May 2020, respectively (EDP, 2019, 2020). It is very important to assess the weather windows and downtime before commencing marine operations. Another important aspect to be considered is the safe havens. Towing of FOWTs is a continuous operation, and it is difficult to halt the operation during the process. Safe havens should be identified along the route of the towing operation to avoid difficulties in case of harsh weather. Some of the floaters in the WindFloat and Kincardine projects were constructed at a different location and transported to the assembly port using specialized heavy-transport vessels. This can be avoided by carefully choosing the right port with shipyard facilities where the complete construction and assembly of the FOWT can be carried out.
Operation and maintenance activities can be carried out either offshore or onshore (Banister, 2017). The periodic inspections, preventive maintenance and repair activities will be performed in situ (i.e. at the platform location). In case of large corrective maintenance or repair activities, the platform can be towed to a sheltered location or port. No heavy-lift vessels are required, and local vessels can be used for towing. This is beneficial in terms of promoting the use of local content and adhering to regulations such as the Jones Act (B.Cheater, 2017), which requires the usage of US-built ships for marine operations in the US waters. Due to the large size of the floater, helipads can be constructed aboard, which make access by helicopters possible. During decommissioning, the platform can be towed to shallow water or taken out of the water completely inside a dry dock and dismantled.
2.3 Other upcoming projects
The Floatgen project by Ideol (France) is another project that employs barge-type substructures (Alexandre et al., 2018; Ideol, 2021). They can be fabricated using steel and concrete, which can help promote the use of local content and employment. The damping pool technology developed by Ideol is designed to stabilize the floater in harsh sea conditions. Two demonstration projects have been in operation since 2018, and pre-commercial and commercial projects are expected to be launched in the coming years (Ideol, 2021).
Another floater concept is the tension leg platform (TLP), which is widely used in the offshore O & G industry. This concept has also been adapted from the O & G industry for the FOWTs. Tension-leg-platform wind turbines (TLPWTs) are well suited for intermediate water depths. The depth varies from 70 m, which is an approximate upper limit for fixed wind turbines, to 200 m, beyond which the spar-type platforms are considered to be the most economical option (Bachynski and Moan, 2012).
In 2008, Blue H Technologies successfully installed a prototype in Italy as a predecessor of commercial-scale TLPWTs (Adam et al., 2014). Even though many concepts have been developed, and a few prototypes have been reported, commercial-scale TLPWTs are still not a reality. The installation of a conventional TLP system is a complex process. The tendons, which hold the platform in place, are usually installed before the platform. The TLP floater is constructed onshore and towed to the location using tugboats or transported using a bespoke barge. The platform is ballasted and connected to the pre-installed tendons. Finally, the platform is de-ballasted to a draught where the tendons attain the optimum tension, and the TLP is secured. The nacelle acceleration and the dynamic tension on the mooring lines are the critical operational parameters here. Low nacelle accelerations are required for the reliable operation of the wind turbine, and low mooring line tensions ensure low weights of gravity anchors and longer fatigue lives. Sclavounos et al. (2010) investigated the hydrodynamic performance of the TLP in various significant wave height and water depth conditions. It was found that the TLP is safe to be installed in waters deeper than 50 m and significant wave heights up to 14 m. Figure 4 illustrates the main components involved in the installation.
The main challenge involved in the installation of a conventional TLP is its unstable behaviour before connecting to the tendons. For the installation of an O & G TLP, bespoke barges are often used for transportation and positioning of the system, which incurs additional expenditure (James and Ros, 2015). The anchors and mooring line system used in TLPs are designed to handle high tensions and are thereby more complex than the semi-submersible and spar-type platform systems. The tendons are susceptible to fatigue failure, which makes TLPs expensive from an O & M point of view also. Decommissioning of a TLP system is also expected to pose some challenges due to the complexity of the mooring system. The platform has to be carefully released from the tendons and towed back to the shore. The mooring lines and anchors are removed later.
The GICON TLP (Adam et al., 2014; Kausche et al., 2018) is another innovative concept. The TLP system is placed on a floating slab and dry-towed to the location. The slab is then ballasted, which submerges the TLP into the required final draught. Figure 5 shows this installation method proposed by GICON. Analyses by Hartmann et al. (2017) found that the transportation of the GICON TLP should be performed only at a wind speed below 12 m s−1 and a maximum towing speed of 5 kn. There are many upcoming concepts that are designed to allow alternative installation methods. An example is the TetraSpar concept (Borg et al., 2020), which features a tetrahedral floating structure equipped with a keel, which can be ballasted and lowered into a certain depth on-site. The keel can be air-ballasted and towed to the offshore location. Once the mooring lines are hooked, the keel is lowered, and the system starts acting like a spar-type platform. The TetraSpar has been developed with the aim to implement large-scale industrial production as it consists only of cylindrical tubes bolted together. These platforms do not require specialized vessels for installation since they can be towed using low-cost and widely available tugs (Andersen et al., 2018). The towing vessels and the FOWT must satisfy the stability criteria set by a classification society (Hartmann et al., 2017; DNV, 2021). Even though small tugs can be used for towing, this might not always be feasible for installation in deeper seas, where higher waves may be encountered. It is advisable to use larger towing vessels for such installations. During the sinking operation of the ballast, the structure will be susceptible to current loads also. Detailed analysis is required to ascertain the motion and the loads on the tendons during this operation.
As mentioned above, different types of FOWTs have advantages and disadvantages when it comes to installation, O & M and decommissioning. Table 1 summarizes them according to the type of floater. Significant wave height, current and wind speed restrictions apply to all marine activities. Some are more sensitive to this, but generally, it is important to overcome this restriction by precise weather monitoring and forecasting (Emmanouil et al., 2020) or using innovative ships and technologies.
Table 1Advantages and disadvantages concerning installation, O & M and decommissioning of different floater types of FOWTs (Leimeister et al., 2018; James and Ros, 2015; Liu et al., 2016).
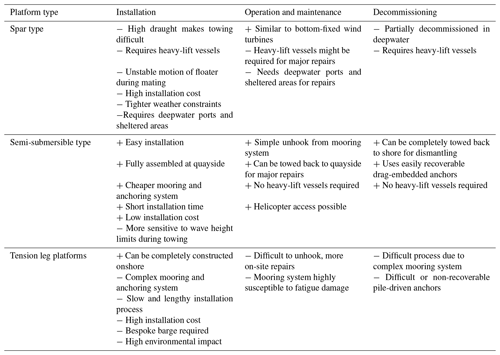
+: relative advantage; −: relative disadvantage.
Marine operation is defined as “a generic term covering, but not limited to the following activities, which are subjected to the hazards of the marine environment: Load-out/ load-in, Transportation/ towage, Lift/Lowering (Offshore/Inshore), Tow-out/tow-in, Float-over/float-off, Jacket launch/jacket upend, Pipeline installation, Construction afloat” (DNV, 2011a). Clearly, many of the operations listed here are applicable for floating wind farms.
DNV (Det Norske Veritas) (DNV, 2011a, b) classifies marine operations into weather-restricted and weather-unrestricted. The operation period TR is defined as
TR is the operation reference period, TPOP is the planned operation period, and TC is the estimated maximum contingency time for the marine operation. Weather-restricted operations are marine operations with TR less than 96 h and TPOP less than 72 h. This is the maximum period for which the weather forecast is sufficiently reliable. Precise weather forecasts and continuous monitoring are required for weather-restricted operations. Towing operations must be analysed based on this (DNV, 2011a). For the Kincardine project, the towing took approximately 9–10 d (Bridget Randall-Smith, 2021). This can be considered to be a weather-unrestricted operation (DNV, 2011a). Statistical extremes of metocean conditions must be considered for planning such an operation according to Table 2.
As mentioned before, the marine operations vary according to the type of floater used. The challenge here is the optimization of the unavoidable marine operations throughout the life cycle of the wind farm. The installation locations of FOWTs present considerable challenges in terms of harsh weather conditions and catastrophic events such as tsunamis. There is a significant opportunity to transfer knowledge and technology from the mature O & G industry, for example, the optimized marine operations, resource assessment and the prediction of offshore weather conditions. The general approach for planning a marine operation is described in Fig. 6.
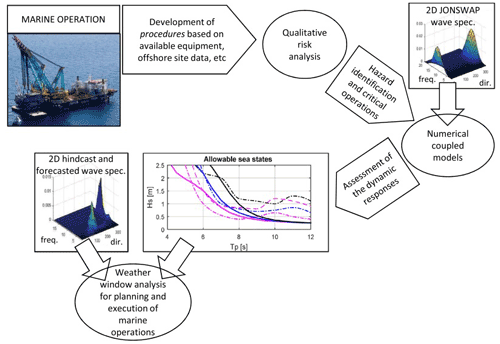
Figure 6General procedure of assessing operational limits for an offshore marine operation (Acero et al., 2016).
There is a lack of consensus on installation approaches, costs and time for each task for floating offshore wind farms. Multiple installation, O & M and decommissioning approaches have been suggested for bottom-fixed wind turbines, and many of them can be adopted for floating wind farms. But FOWTs also present additional challenges, for example dynamic cables, mooring lines and longer real-world operational windows. The most significant challenges and the opportunities for addressing them are discussed in the following sections.
3.1 Metocean assessment and analysis
One significant challenge associated with FOWTs is predicting the optimum meteorological and ocean conditions for design as well as operation of FOWTs. In general, metocean data are required for planning installation, operation, maintenance and decommissioning activities by predicting the suitable weather window and associated costs based on wind, wave and current data (Jacobsen and Rugbjerg, 2005). Moreover, metocean conditions play an important role in site selection, calculation of design loads for floaters and mooring systems also. Wave and wind conditions also present safety concerns during the transfer of the crew to the floating platforms. The uncertainty associated with various environmental variables is of interest to all offshore operations concerning renewables as well as the O & G industry. The high complexity of the ocean environment makes it even harder to predict the operating conditions due to the presence of numerous variables. Also, the availability of metocean data for a particular location and period affects calculations. It is very important to have a general understanding of the metocean conditions of a particular geographical area to plan the construction of wind farms. There are four main sources of metocean data:
-
in situ measurements
-
numerical modelling
-
satellite measurements
-
pre-existing statistics and reports.
Among these, the in situ measurements provide the most reliable metocean data. Even though in situ measurements cannot provide long-term data and incur costs, it is advisable to start taking in situ measurements once the location is decided for a wind farm. Predictions using numerical models can be validated and augmented using in situ measurement data or satellite measurements. Long-term metocean data can also be generated using hindcast data for a particular region. A careful combination of all these will serve as a reliable data set for planning installation, O & M and decommissioning activities. Wind, waves and current are the most important metocean parameters to be monitored and analysed for offshore wind installations. Wind, being the primary source of power, can be measured using lidar or a satellite scatterometer (Ahsbahs et al., 2018; Remmers et al., 2019); the former has proved to be more accurate and continuous for a particular region of interest. Waves can be measured using multiple buoys deployed at a particular location, microwave radar systems (Teleki et al., 1978) or satellites. Current measurements are made using current meters mounted below buoys or using microwave radars. Large-scale geostrophic currents can be measured using satellites (Dohan and Maximenko, 2010). Shore-mounted HF (high-frequency) radars can measure winds, waves and currents in coastal waters over a range of 120 km from the shore (Wyatt, 2021). Various numerical models exist for the precise calculation of metocean conditions. SWAN (Booij et al., 1999) is a third-generation wave model that can calculate random, short-crested waves in shallow waters and ambient current.
3.2 Environmental limits for installation, O & M and decommissioning
The installation, O & M and decommissioning activities require precise monitoring and assessment of metocean conditions in the planning phase itself. FOWTs are installed far offshore to utilize the higher wind speeds. As wind speed and wave heights are directly related, the installation and O & M of a floating wind turbine can be more challenging compared to a bottom-fixed wind turbine. Many pre-hook-up activities like site inspection surveys, installation of anchors, cable laying etc. are possible only during calm sea states. Periodic maintenance and repairs also depend on the weather conditions for safe crew transfer. Special operations, such as the mating of a spar-type platform with a wind turbine, are difficult when the platform is unstable. The installation of TLPs also poses similar challenges as the platform itself is relatively unstable before the connection to the tendons. Waiting for suitable weather conditions can raise the costs, so a precise weather forecast is essential. Figure 7 shows the metocean limitations during assembly, transit and installation of different kinds of platforms.
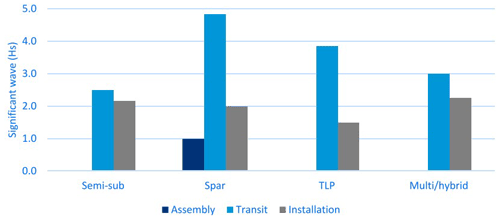
Figure 7Significant wave height limitation during assembly, transit and installation (James and Ros, 2015).
DNV (2021) has defined the motion criteria for various marine operations. Anchor handling operations can be considered hazardous due to the high unexpected mooring loads in adverse sea conditions. For safe performance, it is important to define detailed operation and suspension criteria for anchor handling operations. For example, the 3 h maximum roll angle criterion can be used to compute the probability of exceeding a limiting roll angle of 15∘, which should remain below 10−4. This criterion will ensure that the vessel will not capsize during anchor handling operations (Wu and Moan, 2017).
The operational limits and operability of marine operations are largely dependent on the critical events and the corresponding response parameters (Acero et al., 2016). For example, for the lifting of the fully assembled wind turbine for mating with a spar-type floater using a heavy-lift vessel, the critical event is the failure of the lifting wire. The tension on the wire varies according to the prevailing environmental conditions. The tension on the wire has to be determined, and care should be taken to keep it below the breaking load (including a factor of safety). Using numerical analyses, the allowable environmental conditions that lead to the breaking load should be determined, and they should be avoided. This operation is similar to the mating of the transition piece on a monopile foundation in the case of a bottom-fixed wind turbine (Acero et al., 2017). The only difference is the relative motion between the floating foundation and the wind turbine. The motions of the foundation should also be considered in the analyses. The installation of a wind turbine on a floating substructure using a floating crane vessel is a complex procedure. Cozijn et al. (2008) determined the operational limits of a similar installation operation. The lifting and lowering of two topside modules onto an FSU (floating storage unit) were analysed, and the critical parameters were identified. Impact loads during the lowering phase were also calculated. The impact loads acting on the floater tip during the mating procedure can also be a critical factor depending on the structural design of the floater tip.
Towing is another marine operation that is significant during the installation, operation and maintenance, and decommissioning of FOWTs. Here the critical response parameter is the tension on the towing line, which has to be kept below the breaking load during the operation. During the towing of fully assembled FOWTs, one large towing vessel provides the required bollard pull for towing, and two or three smaller tugs stabilize the motion of the floater and maintain a straight-line course. DNV (2021) has provided the allowable motion and acceleration limits for these vessels used in the operation. In all these cases, it is important to ascertain the environmental conditions corresponding to the limiting value of the response parameter. These conditions should be compared with the metocean forecasts, and the decision of whether the operation can be executed or not should be taken. For long-duration projects a weather window analysis is performed to predict the periods when the weather parameters that affect the operations are below the threshold limits. Using hindcast data of a particular location, the weather downtime (WDT) can be predicted, and decisions on important marine operations can be made (Lambkin et al., 2019).
Significant wave height and wind speed are two major factors that affect workability. Depending on the marine operation, multiple environmental factors need to be considered. For example, wind speed is important for lifting operations, and wind and current speeds are important for towing operations (Acero et al., 2016). Transfer of the crew for maintenance activities becomes difficult in high wave heights. Beyond a significant wave height of 1 m, marine operations become difficult, and most operations halt at a swell of 1.5 m (Lange et al., 2012). Raising this limit is essential for all marine activities concerning offshore structures. Table 3 shows the significant wave height and wind speed limits for various vessels used for marine operations involving FOWTs. These limits can be raised by developing innovative ship designs that have better hydrodynamic performance in rough seas; walk-to-work vessels are one example. The possibility of outfitting existing vessels with motion-compensated gangways should also be investigated. At the same time, specialized vessels are expensive to hire, which would raise the costs.
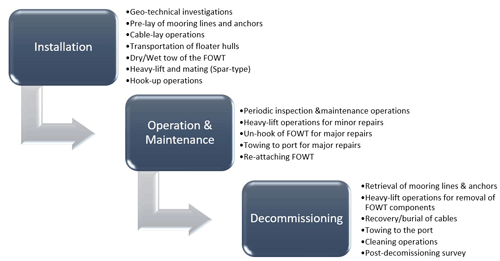
Figure 8Important factors to be considered for the financial modelling of FOW (floating offshore wind) marine operations (Judge et al., 2019).
Table 3Operability of various vessels used in the FOW domain (Paterson et al., 2018; Ahn et al., 2017).
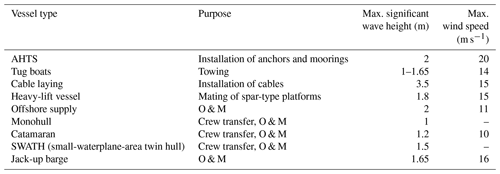
3.3 Cost modelling of floating-wind marine operations
Installation, O & M and decommissioning costs depend on a variety of factors and stakeholder engagements. It is very important to model the costs accurately over the whole life cycle of wind farms. Figure 8 shows the important factors and inputs to be considered while modelling the costs of a floating wind farm. To optimize marine operations, precise modelling of the associated costs is required. The cost modelling of marine operations concerning FOWTs requires a detailed analysis of each phase of the life cycle and the vessels involved in the processes. For array-scale deployments, innovations like shared mooring and anchor systems can be implemented, which would bring down costs. For O & M purposes, modern vessels like service operation vessels (SOVs) and walk-to-work vessels fitted with motion-compensated gangways should be used considering the harsh sea conditions in the deep seas where the FOWTs will be installed. Many good models exist for bottom-fixed wind turbines. Figure 9 shows the breakdown of costs associated with a floating wind farm compared to a bottom-fixed wind farm. They can be extended into floating wind farms depending on the type of floater and the methodology of the various operations. The floating-wind costs are less developed at the moment; hence new and improved models are required for precise calculation of the costs.
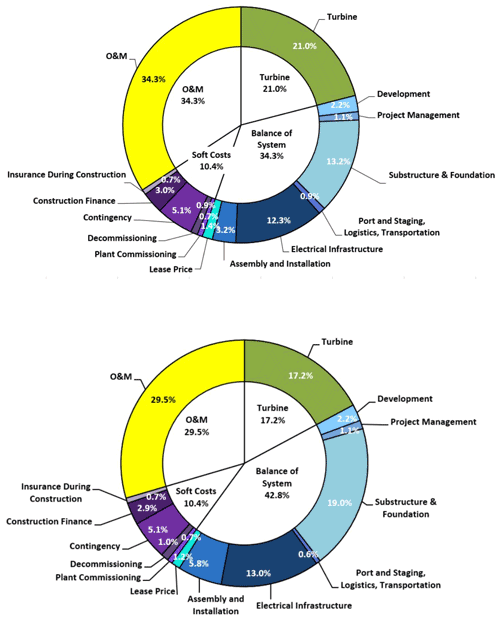
Figure 9Comparison of component-level LCOE contribution for fixed-bottom (top panel) vs. floating wind (bottom panel) farms operating for 25 years (Stehly et al., 2020).
The installation costs consist of costs incurred for the installation of the wind turbine, floating platform, electric system, mooring and anchoring systems, and the start-up cost (Castro-Santos et al., 2016). The installation costs of the floating offshore wind platform depend on the port and shipyard costs, transportation and towing costs, and site installation costs. Draught restriction applies to many ports depending on the type of floater used. The spar-type platforms and TLPs have higher draughts compared to semi-submersibles. In such cases they have to be stored in a special storage area (Castro-Santos et al., 2018b), or the port needs to be dredged, which incurs additional costs. The electric system installation costs are composed of cable installation costs and sub-station installation costs. For the installation of mooring and anchoring systems, it is economical to use an anchor handling vessel (AHV) compared to using barges and tugs (Wayman et al., 2006). The costs vary according to the number of anchors used in the wind farm. By the end of the installation of all the systems, the wind farm is commissioned, and start-up costs are also incurred during its connection to the electrical grid.
Installation costs strongly depend on the site location of the wind farm. Maienza et al. (2020) investigated how the factors like distance from the coast, distance from the nearest port and sea depth influence the total cost of a wind farm in Italian waters. A cost map for Italian national waters was produced, indicating the total costs for a wind farm consisting of 12 TLP FOWTs. Preliminary analysis showed that the number of wind turbines has a considerable effect on the total cost. Doubling the number of turbines increased the cost by 35 %, but quadrupling or increasing eightfold increased the costs by 60 % and 80 %, showing a decrease in the rate at which the total costs increase. The LCOE was found to decrease with an increase in the farm size (Castro-Santos et al., 2018a; Myhr et al., 2014). According to Castro-Santos and Diaz-Casas (2015), the distance from the shore has a 36.3 % influence on installation cost and 14.2 % on dismantling cost. As the wind turbines move further into the sea, it is expected that they will grow in size too to fully utilize the higher wind speeds; 15 MW wind turbines are predicted to be used from around 2030 and 20 MW turbines from 2037 in the UK floating offshore wind sector (OREC, 2015). The wind turbine diameter is found to have a 15.9 % influence on the dismantling cost (Castro-Santos and Diaz-Casas, 2015).
O & M costs mainly consist of the corrective and preventive maintenance costs throughout the whole life cycle of the wind farm (Castro-Santos, 2016; Sperstad et al., 2016). To minimize these costs, it is important to design reliable systems and efficiently monitor the health conditions of the turbine system, floater, electrical installation, and mooring and anchoring system. This is of high importance as the failure of main components could result in considerable downtime as the FOWT might not be accessible due to a lack of suitable weather windows. A preliminary analysis by Dewan and Asgarpour (2016) considered using SOVs and towing vessels for O & M of a floating offshore wind farm consisting of fifty 8 MW semi-submersible wind turbines and investigated the costs and downtime. The availability was found to be 91.4 %, which was lower than fixed-bottom wind turbines, because of the towing of the platform to the shore for major repairs. A detailed investigation is pending in this area to improve the downtime by using better vessels (e.g. walk-to-work vessels), helicopters (Maples et al., 2013) etc. for different types of floaters. Easy-coupling-and-decoupling systems should be developed to facilitate easy attachment and detachment of FOWTs during major repairs. Advancements in robotics have paved the way for the usage of robots for inspection and maintenance; iFROG (Offshore-Engineer, 2020) is an amphibious robot developed by InnoTecUK, ORE Catapult, TWI Ltd. and Brunel University London which can clean corrosion and bio-fouling from monopile surfaces. Using remote condition-monitoring systems, crack initiation and propagation, corrosion, pitting, rubbing etc. can be detected (Tchakoua et al., 2014). Remote visual inspection devices and acoustic emission detectors can record and transmit data to the shore, and the data can be analysed using machine learning models to enable accurate prediction of developing hazards (Stetco et al., 2019).
Decommissioning is an environment-sensitive activity. It is better to incorporate decommissioning studies in the design phase to avoid complications in the final years of the wind farm life cycle (20 years or more) (James and Ros, 2015; Castro-Santos, 2016). A reverse-installation approach can be used for calculating the decommissioning costs of a wind farm (Topham and McMillan, 2017). The main components are the dismantling costs of the wind turbine, floating platform, electric system, mooring and anchors. Some anchors, e.g. drag-embedded anchors, are easily recoverable, which would save costs and time (González and Diaz-Casas, 2016). There is an additional cost due to the cleaning of the wind farm site which is of environmental concern (Castro-Santos et al., 2016). Some materials can be sold as scrap, e.g. steel from the floater and copper from the electric cables, which would result in a negative cost (income) (Castro-Santos et al., 2016).
Various stakeholders are involved in the construction of an offshore wind farm. Proper planning and optimum utilization of resources are very important in bringing down costs. Weather restrictions during the marine operations would cause the logistic costs to increase exponentially (Lange et al., 2012). Often hiring offshore support vessels from abroad invites large hiring costs. Specialized vessels also raise costs; see Table 4. Depending on the location, optimized use of local vessels and port facilities would help bring down the associated costs.
3.4 Health, safety and environment (HSE)
One of the non-technical challenges that needs to be addressed is improving the HSE conditions during the complete life cycle of floating offshore wind farms. HSE factors must be considered during all phases of the development of the wind farm, but only the installation, O & M and decommissioning phases are considered in this section. Since the floating-wind technology is in its infancy, there is a shortage of dedicated applicable rules and standards. Until the development of such standards, it is advisable to follow component- and process-specific standards used in the bottom-fixed-wind-turbine industry or O & G industry (Hutton et al., 2016). Marine operations in general can follow the various safety standards, codes and classification society rules accordingly.
Theoretically, the installation of FOWTs is less environment-sensitive compared to fixed offshore wind turbines as most of them are constructed completely onshore and towed to the offshore sites. Again, the type of floater is a deciding factor here. The installation of anchors and mooring lines can have a negative impact on the environment. Spar-type platforms and semi-submersibles employ catenary moorings with long mooring lines that have a larger footprint on the seabed, while TLPs do not because they employ taut mooring lines (James and Ros, 2015). Heavy-lift vessels are used during the installation of spar-type platforms, which invites additional safety issues, but there are well-defined guidelines and standards available for this operation. The installation of drag-embedded anchors has less of an environmental impact compared to suction or pile-driven anchors. The noise impact during hammer piling is also an issue. However, the underwater noise during the installation of FOWTs is less compared to bottom-fixed wind turbines (Koschinski and Lüdemann, 2013). The noise during hammer piling can be mitigated by carefully engineering the piling process. By using the right specification of piles and drivers the noise can be reduced. Bubble curtains can be created using underwater bubble pipes to attenuate the blast and piling noise. Vibropiling is another technique employing vibratory pile drive machines that drive the pile by applying rapidly alternating forces, which are quieter than impact piling machines (Nedwell et al., 2003). Long-term post-installation noise measurements are required to understand the effects of operational noises of large wind turbines fitted on floating foundations (Farr et al., 2021; Koschinski and Lüdemann, 2013). The effects on fish populations and marine mammals need to be studied separately. Protected marine areas, migratory birds’ paths and migratory marine life paths should be avoided while selecting sites for offshore wind farms (Díaz et al., 2019).
The most challenging safety concern is access and egress of personnel to and from FOWTs during repair and maintenance activities. The FOWT and the vessel form a floating–floating couple which makes access and egress challenging. Bump and jump can only be safely accomplished in low wave heights, whereas walk-to-work systems increase this wave height limit while providing safer means of access and egress. For crew transfer onto FOWTs, SOVs with relative-motion compensation are preferred over CTVs due to higher operability limits and established practices. A precise weather forecast is also required for planning O & M operations to avoid difficulties during the operations. Aboard a FOWT, even the small motions of the floater get amplified into large displacements at the nacelles and blades. This contributes to severe motion sickness or reduced efficiency of the personnel working on such structures. In the long-term, these factors have to be considered in the design phase of the FOWT itself to reduce the dynamic response in waves. Remote O & M can also be considered to reduce the O & M visits. FOWTs can be towed back to shore for O & M, which makes them attractive from an HSE point of view.
After decommissioning, it is important to leave the site in a similar condition as it was before the deployment of the wind turbines. After the wind turbines are transported to the shore, the mooring lines and anchors have to be removed. Certain types of anchors offer easy removal, while others are difficult or impossible to remove. Extreme care should be taken while removing cables from the sea. The complete removal of cables can cause severe damage and disruption to the seabed and in most cases, they are left buried on-site (Topham and McMillan, 2017). Following decommissioning, it is important that equipment is well below the seabed and does not pose a risk to fishing or other marine activities. Where this is not possible, these locations must be recorded and reported to relevant local authorities. Post-decommissioning surveys are conducted to ensure that no debris is left behind, and the buried remnants are not causing obstructions.
Significant research is currently being conducted in the development of efficient and optimal floating wind turbines. To decrease the costs associated with installation, O & M and decommissioning operations, many innovative designs, procedures and technologies along with established best practices are required. Some aspects can be adopted from the O & G industry; however, the unique nature of FOWTs requires dedicated research and development. Some of the innovations applicable in this domain are discussed in this section. These innovations are targeted at improving the operability of vessels, widening weather windows, improving HSE factors and reducing the need for complex marine operations.
4.1 Shared-mooring and shared-anchoring systems
For large floating offshore wind farms, the mooring lines and anchors can be shared with multiple FOWTs, reducing total mooring line length, saving construction material for anchors and reducing the need for marine operations by optimizing utilization of the installed infrastructure. In a shared-mooring system (Fig. 10), the FOWTs are interconnected using mooring lines, reducing the frequent connections to the seabed using anchors. In a shared-anchor system, a single anchor takes multiple mooring lines, and the number of anchors can be reduced. Both these systems are practical for large wind farms, and significant cost reductions are achievable due to the savings in material and installation costs.
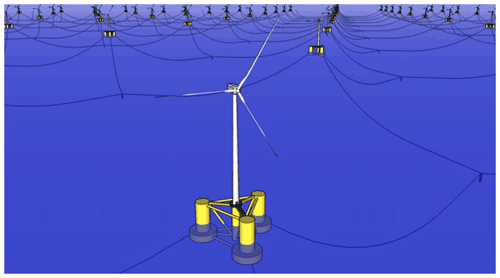
Figure 10Shared-anchor system (Fontana et al., 2018).
Many researchers have worked on these concepts for application in the floating offshore wind domain. The technical know-how of integrated mooring systems can be transferred from the O & G industry. They have been employed in the floating O & G platforms, and the technology is relatively mature. Musial et al. (2004) have observed that individual mooring and anchor costs are significant for single-turbine systems compared to a shared system.
Fontana et al. (2016) investigated the hydrodynamic performance and loading analysis of shared anchors for various FOWT configurations and found that shared anchors must be structurally strong enough to handle loading from unexpected directions. Anchors with a directional preference in their holding position and capacity are generally not suited for multi-line moorings, but they can be adapted by extra structural outfitting for handling mooring loads in various directions (Diaz et al., 2016). The type of floater is also found to have a significant influence on the anchor forces. Balakrishnan et al. (2020) analysed and compared the anchor forces on a semi-submersible floater system and a spar-type floater system and found that the anchor forces on the latter were less. This is because spar-type platforms have less surface area interacting with waves compared to that of a semi-submersible.
Goldschmidt and Muskulus (2015) investigated the performance of coupled-mooring systems involving 1, 5 and 10 floaters in various configurations. Semi-submersible floaters were arranged in a row and triangular and rectangular configurations separately, and the system dynamics were studied. It was found that mooring system cost reductions up to 60 % and total system cost reductions up to 8 % were achievable using shared moorings. However, it was noted that the displacements of the floaters were higher when the number of floaters in the system increased, which would be a problem for large wind farms. Further investigation is required to improve the behaviour of floaters in larger wind farms. One of the main challenges in adopting a multi-line system for FOWTs is the reduction in system reliability. Failure of the multi-line system components can cause a large number of FOWTs to detach and stay adrift. Hallowell et al. (2018) investigated the reliability of a multi-line system (100 wind turbines in a configuration of 10 rows and 10 columns) compared to a conventional single-line system. It was found that the reliability of a multi-line system reduced considerably in extreme load conditions due to progressive failures. Further research is required in this area to increase the reliability of multi-line systems for FOWTs.
Geotechnical investigations are carried out at the anchor site prior to the installation of anchors. Dedicated geotechnical investigation vessels are used for this. The cost of geotechnical investigations is a function of water depth, site conditions, pre-existing survey data and method of investigation. The geotechnical site investigation costs are also dependent on the number of anchors (Fontana, 2019). In a wind farm with shared anchors, there is a significant reduction in the number of anchors. This would help to bring down geotechnical site investigation costs. Fontana (2019) compared the costs of installation and geotechnical site investigation for different farm sizes. It was found that a multi-line configuration reduces the installation cost for wind farms with 36 or more wind turbines. The geotechnical site investigation costs also get reduced with an increase in the size of the wind farm but taper due to the diminishing of the perimeter effect (anchors in the perimeter share fewer FOWTs). In a shared-mooring system, mooring lines can be interconnected instead of connecting to the seabed. The critical parameters are the tensions in the mooring lines and the loads acting on the anchors. As mentioned before, the system is susceptible to loading from multiple directions, and the reliability of the system is dependent on the line taking the maximum tension. The tension on the mooring line must be below the breaking load in all environmental conditions as well as extreme events. The pad eye on the anchor is also subjected to loads in various directions (Hallowell et al., 2018). Shared mooring can also make access by large vessels difficult. When FOWTs are interconnected, it can cause hindrance for such vessels with high draughts to approach the platform and transfer the crew. The mooring architecture has to be designed in such a way that vessels can safely pass between the FOWTs. Available depth at the farm location and the point at which the mooring line is connected to the floater are deciding factors here.
Detailed analyses are required to ascertain the dynamic performance of a shared-mooring system and estimate the increase in extreme and fatigue loads (Hall et al., 2014). The feasibility of using shared-mooring systems for pilot-scale floating wind farms was investigated by Connolly and Hall (2019). It was found that significant cost reductions can be achieved by proper selection of wind farm layouts, mooring line properties and platform displacements. The Hywind Tampen is an upcoming floating wind farm that employs shared anchors (Reuters, 2020). The optimized array-scale installation procedure for the shared-mooring and shared-anchoring systems and its effect on costs and time are yet to be investigated.
4.2 Dynamic positioning for FOWTs
The FOWTs are generally positioned in the deep sea using mooring lines. They have to be pre-installed using offshore support vessels, which are expensive, and the process is time-consuming. Precise engineering calculations are required to design the mooring lines and anchors for offshore structures.
The water depth is a decisive factor that determines the length of mooring lines and the costs associated with them. In many cases, the seabed has to be analysed and prepared depending on the type of anchors used for installation. Semi-submersibles and spar-type floaters are moored using a longer but simpler mooring system compared to TLPs, but the TLPs employ complex anchors and vertically loaded tendons with high load-bearing capacity. The conventional steel tendons are heavy and thereby costly and impractical for ultra-deep installations (Cummins and McKeogh, 2020). Large expensive vessels will be required for transporting and installing them in an array-scale wind farm, which would increase the costs. A mooring system is considered impractical and uneconomical for water depths greater than 1000 m (Yamamoto and Morooka, 2005). At the moment, researchers agree that the practical water depth limit for floating wind turbines should be between 700 and 1300 m (Musial et al., 2016). Developing a cable system for transferring electricity from such depths is difficult and impractical. But with the development of better electricity storage technology, e.g. efficient hydrogen production and storage (Cummins and McKeogh, 2020), FOWTs can be deployed in deeper waters. Mooring systems will be less effective for station-keeping in such cases.
Dynamic positioning has been often used for station-keeping of ships and offshore structures in the O & G industry for years. Offshore support vessels actively employ dynamic positioning systems (DPSs) for a variety of offshore activities. Employing DPSs can be considered for FOWTs in deeper waters. The water depth and sea-bottom conditions do not affect the DPS; hence it can save mooring line, seabed preparation and anchoring costs. The disadvantage of the DPS is that it consumes a considerable amount of energy the turbine produces. Xu et al. (2021) proposed the feasibility of a dynamically positioned semi-submersible 5 MW floating wind turbine in their paper. It was found that the DPS utilized approximately of the total generated energy when the current forces are not considered, and the ratio becomes when current forces are taken into account (Xu et al., 2021). The concept has not been experimentally evaluated, and the economics of the DP system have not been optimized.
Another scenario where the DPS can be useful is during the crew transfer from an offshore support vessel to the FOWT during operation and maintenance activities. Even with the mooring lines attached, the platform is subject to motions which make the transfer of personnel difficult. In such cases, the DPS would help to stabilize the FOWT and help the safe transfer of the crew. Heavy-lift vessels can also employ the DPS during heavy-lift operations in the deep sea (e.g. mating of spar-type platforms, O & M). The economics of using such systems for FOWTs are yet to be investigated.
4.3 Walk-to-work for FOWTs
Operation and maintenance of offshore platforms are often challenging due to the difficulty in accessing the platforms. Safe transfer of the crew is essential for all kinds of maintenance activities concerning offshore structures. Access to O & G platforms and bottom-fixed wind platforms has always been challenging. In the case of floating platforms, it is even more challenging as the platform and the crew transfer vessel are in relative motion during transfer. Since floating wind technology is relatively new, it is necessary to use the knowledge acquired in the O & G and fixed-wind domain for floating platforms (Santos et al., 2016).
Walk-to-work (W2W) vessels are equipped with motion-compensated gangways (MCGs) that enable crew transfer in higher wave heights. They help to widen operational weather windows and eliminate the waiting time, which saves time and expenses. They can also be employed during installation activities for the transfer of the crew. The MCGs employ a technology known as active motion compensation (Chung, 2016). Accurate motion sensors detect vessel motions and counteract them using a sophisticated hydraulic hexapod on which the gangway is mounted. Motion detection and hydraulics are governed by an automated control system. MCGs allow crew transfer in significant wave heights up to 3.5 m and wind speed up to 20 m s−1 (Salzmann et al., 2015).
Guanche et al. (2016) investigated the hydrodynamic performance of a catamaran crew transfer vessel (CTV24) with a fender and a platform support vessel (PSV80) with an MCG, and the operating significant wave height conditions were compared. It was found that access was theoretically possible with wave heights up to 2 m using the catamaran and 5 m using the PSV in head seas (Guanche et al., 2016). In a separate study, accessibility was calculated for a semi-submersible located off the coast of Portugal using hindcast data from 1980–2013. Safe access was possible up to 20 % and 76 % of the time using the catamaran and PSV, respectively (Martini et al., 2016). Li (2021) further investigated the operability of such systems by also taking second-order drift motions into consideration. It was noticed that the general wave height limit reduces to 2–3 m when nonlinear drift forces were involved. Both investigations revealed that beam seas are to be avoided in all cases when employing W2W vessels for access. However, all these studies indicate that W2W vessels equipped with MCGs are considerably advantageous over conventional access systems for floating-wind-platform access. The complex motion of the multi-body system requires further studies to ensure the safety of the crew during such operations.
4.4 Specialized ships for FOWT-related marine operations
Even though many FOWTs do not need specialized installation vessels, innovative vessel designs that could simplify the installation processes are worth investigating. Many of the floater types can be constructed onshore and towed to the location by using tugs. An exception to this is the spar-type platforms. They need heavy-lift vessels for the platform–turbine mating process. There is potential for developing innovative ship designs that can facilitate cheaper and safer marine operations compared to the existing methods. One public competition we can examine to give insight into this happened in 2014, when Statoil (now Equinor ASA) presented the “Hywind Installation Challenge” (Equinor, 2022a) that sought out innovative installation technologies and methods for the installation of the Hywind wind turbines.
Stavanger-based Windflip AS proposed an innovative vessel design that can be used for the installation of floating offshore wind platforms (Maritime-Journal, 2012). The proposal was based on a specialized barge that can transport a fully assembled spar-type platform to the location and unload by flipping. The turbine is loaded in an almost-horizontal position, and the barge is towed to the offshore location. The aft side of the barge is then ballasted, taking the whole barge–turbine system into a vertical position. The turbine is then connected to the mooring lines, and the barge is towed back to the quayside for reloading. Windflip AS claims that the vessel can operate in shallow waters, which is an advantage when it comes to the installation of spar-type platforms.
Another concept was proposed by Jiang et al. (2020) to aid the installation of spar-type platforms. A floating dock (Fig. 11) was specifically designed for shielding a wind turbine during the installation of the tower, nacelle and rotor onto a spar-type platform. Hydrodynamic evaluation showed that the floating dock was able to reduce the pitch and heave response of the spar-type platform, which aids mating of the blades.
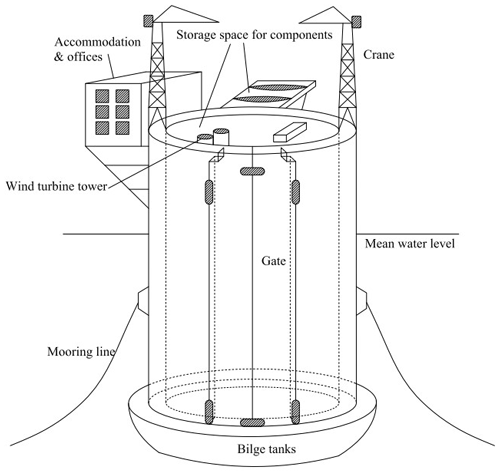
Figure 11Floating dock concept (Jiang et al., 2020).
Two different spar designs of different geometrical properties were tested during the analyses. The RAO (response amplitude operator) plots show that the shielding provided by the floating dock helps to reduce the motion of the spar platforms inside (Fig. 12). However, sloshing mode and piston mode resonances were observed, which was a result of the small inner diameter of the dock. Even though the floating dock is theoretically feasible, the towing and ballasting operations are not yet studied. The structural design of the floating dock is also required for analysing the internal compartment and fatigue of the gate and storage modules. Detailed cost analyses are also required to check whether the construction, hiring and operation of the floating dock are economically feasible.
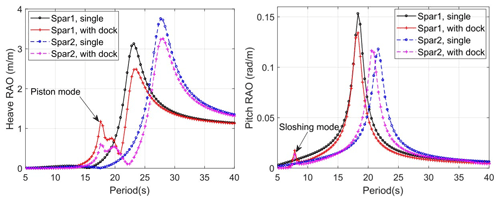
Figure 12Comparison of the spar RAOs with and without the floating dock (Jiang et al., 2020).
Jiang et al. (2018) investigated another concept, a catamaran wind turbine installation vessel equipped with grippers that aid the installation of spar-type platforms. The vessel can carry a maximum of four wind turbines and minimize or eliminate the use of heavy-lift vessels and thereby reduce installation time. Figure 13 explains the various stages in the installation of a spar-type platform using the catamaran vessel. Jiang et al. (2018) studied the hydrodynamic performance of the system involving the catamaran, a spar foundation, mechanical couplings, mooring lines and a dynamic position system using the multi-body approach. The success of the mating is largely dependent on the relative motion between the spar and the wind turbine tower. The relative-motion radius (distance between the spar and wind turbine tower), gripper forces and the mooring line tension were the critical parameters in this process. The system was simulated under various significant wave height, peak period, wind speed and blade pitch conditions. The significant wave height was found to be the most important environmental parameter that affects the performance of the system. A maximum significant wave height of 3 m was used for the analyses, and the mating process was found to be successful. The disadvantage here is the complex mechanical structural arrangement and various dynamic loads acting on the system.
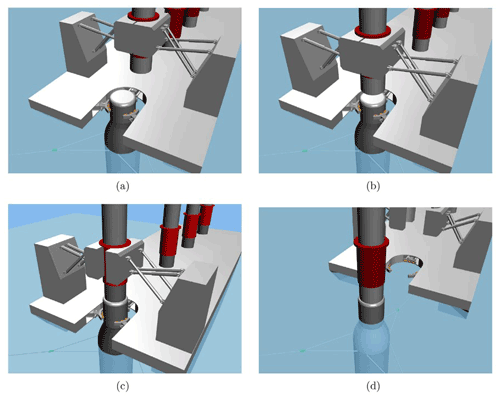
Figure 13Stages in the installation of a wind turbine using the catamaran vessel: (a) transfer of the assembly, (b) monitoring of relative motion, (c) mating of the tower with the floater, (d) release of the foundation (Jiang et al., 2018; Hatledal et al., 2017).
Vågnes et al. (2020) proposed an improved system using winches and wires instead of grippers. This system can reduce the structural requirements of the lifting system and improve the handling of the wind turbines. The system will be installed aboard a catamaran vessel which can be used for the installation of spar-type platforms. The low-height lifting system is controlled by an active heave compensation system and tension tugger wires to ensure the balance of the tower during the mating process. Preliminary hydrodynamic analyses of the system under various weather conditions and operational layouts showed that the system is feasible and can be efficiently used for the installation of spar-type platforms. The system was tested for various significant wave height and peak period conditions. The tensions on the lifting, stabilizing and attachment wires were the critical parameters. The natural periods of the FOWT were unlikely to be present at common installation locations, but those of the catamaran and spar are likely to be present. The analyses were focused only on the positioning of the wind turbines; detailed analyses of the lowering and mating processes are necessary to evaluate the feasibility of the system. The performance of the system under various wind, wave and current conditions and experimental validation of these results are also pending.
The importance of focussing research on the marine operations concerning installation, O & M and decommissioning of FOWTs is discussed in this paper. As the industry matures, much research is needed to frame innovative methods and technologies to reduce the costs and LCOE. Compared to the O & G industry, offshore wind turbines provide opportunities for batch production and deployment. These opportunities should be utilized for the full commercialization of floating wind farms. Semi-submersibles are observed to be the most cost-efficient design from an installation, O & M and decommissioning point of view, but broader research is needed to consider all the factors applicable to the whole life cycle of the wind farms. Several challenges are yet to be addressed to reduce the costs concerning spar-type platforms and TLPs. It is very important to consider the ease of installation, O & M and decommissioning in the design phase of the floater concepts for the practical realization of these concepts. There is also plenty of room for innovation to cut costs, reduce environmental impact and improve the safety of the personnel associated with the industry.
Many challenges need to be addressed, and much research is pending in the FOW domain. Some of the challenges are specific to the type of floater, but others apply generally. There is much research to be done for the easy and cost-effective installation, O & M and decommissioning of TLPs. It is important to introduce and implement innovative and cost-effective methods and technologies in this domain. Marine operations, due to the involvement of human life, environment and marine life, are of paramount importance. They are most dependent on metocean conditions, so accurate prediction is important. In situ measurements should be encouraged for getting accurate weather data throughout the life cycle of the wind farm. Sharing of these data across multiple platforms should also be encouraged for the metocean analyses of upcoming wind farms and further research. Marine operations can be improved in two different ways, i.e. either by developing better metocean prediction models, for example, analytical models augmented by in situ measurements, or improving the operability of vessels in harsh seas by implementing innovative technologies and methods. Specialized vessels are expensive, but by reducing costs in other areas they can lead to reductions in the overall LCOE. Generally, O & M operations have stricter weather restrictions compared to installation operations (e.g. towing). Emphasis should be given in this area, and the O & M weather conditions should be used as limiting cases for the metocean assessments. As the industry matures, it is very likely that there will be a huge demand for offshore support vessels (OSVs), AHTSs, SOVs etc. in the near future. The industry should be able to supply the vessels according to the demand or else the costs will rise. Marine operations and vessel utilization must be optimized to reduce the LCOE of floating offshore wind energy and increase competitiveness with other energy sectors.
No data sets were used in this article.
RCR did the reading and literature review and wrote the paper. CD reviewed and edited the initial drafts of the paper and contributed actively. FJ also helped review the drafts. JJS and JM supervised the work.
The contact author has declared that neither they nor their co-authors have any competing interests.
Publisher's note: Copernicus Publications remains neutral with regard to jurisdictional claims in published maps and institutional affiliations.
This research has been supported by Horizon 2020 (STEP4WIND, grant no. 860737).
This paper was edited by Amir R. Nejad and reviewed by Wilson Guachamin and one anonymous referee.
Acero, W. G., Li, L., Gao, Z., and Moan, T.: Methodology for assessment of the operational limits and operability of marine operations, Ocean Eng., 125, 308–327, 2016. a, b, c
Acero, W. G., Gao, Z., and Moan, T.: Methodology for assessment of the allowable sea states during installation of an offshore wind turbine transition piece structure onto a monopile foundation, J. Offshore Mech. Arct. Eng., 139, OMAE-16-1039, https://doi.org/10.1115/1.4037174, 2017. a
Adam, F., Myland, T., Dahlhaus, F., and Großmann, J.: Gicon®-TLP for wind turbines – the path of development, in: The 1st International Conference on Renewable Energies Offshore (RENEW), November 2014, Lisbon, Portugal, 24–26, https://doi.org/10.1201/b18973-92, 2014. a, b
Ahn, D., Shin, S.-C., Kim, S.-Y., Kharoufi, H., and Kim, H.-C.: Comparative evaluation of different offshore wind turbine installation vessels for Korean west–south wind farm, Int. J. Naval Architect. Ocean Eng., 9, 45–54, 2017. a
Ahsbahs, T., Badger, M., Volker, P., Hansen, K. S., and Hasager, C. B.: Applications of satellite winds for the offshore wind farm site Anholt, Wind Energ. Sci., 3, 573–588, https://doi.org/10.5194/wes-3-573-2018, 2018. a
Alexandre, A., Percher, Y., Choisnet, T., Buils Urbano, R., and Harries, R.: Coupled analysis and numerical model verification for the 2 MW Floatgen demonstrator project with IDEOL platform, in: International Conference on Offshore Mechanics and Arctic Engineering, vol. 51975, American Society of Mechanical Engineers, V001T01A032, 2018. a
Andersen, M. T., Tetu, A., and Stiesdal, H.: Economic Potential of Industrializing Floating Wind Turbine Foundations, in: International Conference on Offshore Mechanics and Arctic Engineering, vol. 51203, American Society of Mechanical Engineers, V001T01A045, 2018. a
Bachynski, E. E. and Moan, T.: Design considerations for tension leg platform wind turbines, Mar. Struct., 29, 89–114, 2012. a
Balakrishnan, K., Arwade, S. R., DeGroot, D. J., Fontana, C., Landon, M., and Aubeny, C. P.: Comparison of multiline anchors for offshore wind turbines with spar and with semisubmersible, J. Phys.: Conf. Ser., 1452, 012032, https://doi.org/10.1088/1742-6596/1452/1/012032, 2020. a
Banister, K.: WindFloat Pacific Project, US Department of Energy, https://doi.org/10.2172/1339449, 2017. a, b, c, d
B.Cheater: U.S. Jones Act Compliant Offshore Wind Turbine Installation Vessel Study, Tech. rep., USA, https://www.cesa.org/resource-library/resource/u-s-jones-act-compliant-offshore-wind-turbine-installation- (last access: 11 April 2022), 2017. a
Berg, P. W. S.: A Discussion of Technical Challenges and Operational Limits for Towing Operations, MS thesis, NTNU, https://ntnuopen.ntnu.no/ntnu-xmlui/bitstream/handle/11250/2453421/17059_FULLTEXT.pdf?sequence=1&isAllowed=y (last access: 11 April 2022), 2017. a
Booij, N., Ris, R. C., and Holthuijsen, L. H.: A third-generation wave model for coastal regions: 1. Model description and validation, J. Gephys. Res.-Oceans, 104, 7649–7666, 1999. a, b
Borg, M., Walkusch Jensen, M., Urquhart, S., Andersen, M. T., Thomsen, J. B., and Stiesdal, H.: Technical definition of the tetraspar demonstrator floating wind turbine foundation, Energies, 13, 4911, https://doi.org/10.3390/en13184911, 2020. a
Bridget Randall-Smith, C. O.: More moorings to be installed at Kincardine floating wind farm, https://www.4coffshore.com/news/more-moorings-to-be-installed-at-kincardine-floating-wind-, last access: 16 August 2021. a
Butterfield, S., Musial, W., Jonkman, J., and Sclavounos, P.: Engineering challenges for floating offshore wind turbines, Tech. rep., NREL – National Renewable Energy Lab., Golden, CO, USA, https://www.osti.gov/biblio/917212 (last access: 11 April 2022), 2007. a
Castro-Santos, L.: Life-Cycle Cost of a Floating Offshore Wind Farm, in: Floating Offshore Wind Farms, Springer, 23–38, https://doi.org/10.1007/978-3-319-27972-5_2, 2016. a, b, c
Castro-Santos, L. and Diaz-Casas, V.: Sensitivity analysis of floating offshore wind farms, Energ. Convers. Manage., 101, 271–277, 2015. a, b
Castro-Santos, L., Ferreño González, S., and Diaz-Casas, V.: Methodology to calculate mooring and anchoring costs of floating offshore wind devices, in: International Conference on Renewable Energies and Power Quality (ICREPQ), vol. 1, 20–22 March 2013, Bilbao, Spain, p. 45, https://www.icrepq.com/icrepq'13/276-castro.pdf (last access: 11 April 2022), 2013. a
Castro-Santos, L., Filgueira-Vizoso, A., Carral-Couce, L., and Formoso, J. Á. F.: Economic feasibility of floating offshore wind farms, Energy, 112, 868–882, 2016. a, b, c
Castro-Santos, L., Filgueira-Vizoso, A., Álvarez-Feal, C., and Carral, L.: Influence of size on the economic feasibility of floating offshore wind farms, Sustainability, 10, 4484, https://doi.org/10.3390/su10124484, 2018a. a, b
Castro-Santos, L., Filgueira-Vizoso, A., Lamas-Galdo, I., and Carral-Couce, L.: Methodology to calculate the installation costs of offshore wind farms located in deep waters, J. Clean. Product., 170, 1124–1135, 2018b. a
Chung, Y. C.: Dynamic Analysis of the Ampelmann G25 Gangway, https://repository.tudelft.nl/islandora/object/uuid:d009326a-63c6-489d-9e91-eaba76f4dbd0 (last access: 11 April 2022), 2016. a
Connolly, P. and Hall, M.: Comparison of pilot-scale floating offshore wind farms with shared moorings, Ocean Eng., 171, 172–180, 2019. a
Cozijn, J., van der Wal, R., and Dunlop, C.: Model testing and complex numerical simulations for offshore installation, in: The Eighteenth International Offshore and Polar Engineering Conference, OnePetro, 6–11 July 2008, Vancouver, Canada, https://onepetro.org/ISOPEIOPEC/proceedings-abstract/ISOPE08/All-ISOPE08/ISOPE-I-08-080/10594 (last access: 11 April 2022), 2008. a
Crowle, A. and Thies, P.: Installation Innovation for floating offshore wind, https://ore.exeter.ac.uk/repository/handle/10871/125194 (last access: 11 April 2022), 2021. a
Cummins, V. and McKeogh, E.: Blueprint for offshore wind in Ireland 2020–2050: A Research Synthesis, EirWind project, MaREI Centre, ERI, University College, Cork, Ireland, Zenodo, https://doi.org/10.5281/zenodo.3958261, 2020. a, b
Dewan, A. and Asgarpour, M.: Reference O & M Concepts for Near and Far Offshore Wind Farms, ECN, Petten, https://repository.tudelft.nl/islandora/object/uuid:34af4079-528d-487d-a6ef-10eeead62a6d/datastream/URL/download (last access: 11 April 2022), 2016. a
Diaz, B. D., Rasulo, M., Aubeny, C. P., Fontana, C. M., Arwade, S. R., DeGroot, D. J., and Landon, M.: Multiline anchors for floating offshore wind towers, in: IEEE OCEANS 2016 MTS/IEEE Monterey, 19–23 September 2016, Monterey, CA, USA, 1–9, https://doi.org/10.1109/OCEANS.2016.7761374, 2016. a
Díaz, H., Fonseca, R., and Guedes Soares, C.: Site selection process for floating offshore wind farms in Madeira Islands, https://doi.org/10.1201/9780429505324, 2019. a
DNV: Offshore Standard – DNV-OS-H101, Marine Operations, General, https://rules.dnv.com/servicedocuments/dnv/#!/home (last access: 16 August 2021), 2011a. a, b, c, d, e
DNV: Offshore Standard – DNV-RP-H103, Modelling And Analysis Of Marine Operations, https://rules.dnv.com/servicedocuments/dnv/#!/home (last access: 16 August 2021), 2011b. a
DNV: DNV-OS-H202, Sea transport operations, https://rules.dnv.com/servicedocuments/dnv/#!/home (last access: 16 August 2021), 2015. a
DNV: Floating Wind: The Power to Commercialize, Tech. rep., https://www.dnv.com/Publications/floating-wind-the-power-to-commercialize-192334 (last access: 11 April 2022), 2020. a
DNV: DNV-ST-N001, Marine operations and marine warranty, https://rules.dnv.com/servicedocuments/dnv/#!/home, last access: 16 August 2021. a, b, c
Dohan, K. and Maximenko, N.: Monitoring ocean currents with satellite sensors, Oceanography, 23, 94–103, 2010. a
EC: General Annexes, Work Programme 2016–2017, https://ec.europa.eu/research/participants/data/ref/h2020/other/wp/2016-2017/annexes/h2020-wp1617-annex-ga_en.pdf (last access: 11 April 2022), 2017. a
EDP: WindFloat Atlantic begins the installation of the first floating wind farm, https://www.edpr.com/en/news/2019/10/21/windfloat-atlantic-begins-installation-first-floating-wind-farm (last access: 11 April 2022), 2019. a
EDP: WindFloat Atlantic, https://www.edp.com/en/innovation/windfloat (last access: 11 April 2022), 2020. a
Emmanouil, S., Aguilar, S. G., Nane, G. F., and Schouten, J.-J.: Statistical models for improving significant wave height predictions in offshore operations, Ocean Eng., 206, 107249, https://doi.org/10.1016/j.oceaneng.2020.107249, 2020. a
Equinor: Hywind installation, https://www.equinor.com/en/how-and-why/innovate/the-hywind-challenge.html (last access: 16 August 2021), 2022a. a
Equinor: Hywind Scotland, https://www.equinor.com/en/what-we-do/floating-wind/hywind-scotland.html (last access: 16 August 2021), 2022b. a, b, c
EWEA: Deep water, The next step for offshore wind energy, Tech. rep., https://windeurope.org/about-wind/reports/deep-water/ (last access: 11 April 2022), 2013. a
Farr, H., Ruttenberg, B., Walter, R. K., Wang, Y.-H., and White, C.: Potential environmental effects of deepwater floating offshore wind energy facilities, Ocean Coast. Manage., 207, 105611, https://doi.org/10.1016/j.ocecoaman.2021.105611, 2021. a
Fontana, C.: A Multiline Anchor Concept for Floating Offshore Wind Turbines, https://doi.org/10.7275/13483708, 2019. a, b
Fontana, C. M., Arwade, S. R., DeGroot, D. J., Myers, A. T., Landon, M., and Aubeny, C.: Efficient multiline anchor systems for floating offshore wind turbines, in: International Conference on Offshore Mechanics and Arctic Engineering, vol. 49972, American Society of Mechanical Engineers, V006T09A042, 2016. a
Fontana, C. M., Hallowell, S. T., Arwade, S. R., DeGroot, D. J., Landon, M. E., Aubeny, C. P., Diaz, B., Myers, A. T., and Ozmutlu, S.: Multiline anchor force dynamics in floating offshore wind turbines, Wind Energy, 21, 1177–1190, 2018. a
Foxwell, D.: Day rates for SOVs likely to continue upward course, https://www.rivieramm.com/news-content-hub/news-content-hub/day-rates-for-sovs-likely-to-continue-upward-course-54572 (last access: 11 April 2022), 2019. a
Goldschmidt, M. and Muskulus, M.: Coupled mooring systems for floating wind farms, Energy Procedia, 80, 255–262, 2015. a
González, S. F. and Diaz-Casas, V.: Present and future of floating offshore wind, in: Floating Offshore Wind Farms, Springer, 1–22, https://doi.org/10.1007/978-3-319-27972-5_1, 2016. a
Guanche, R., Martini, M., Jurado, A., and Losada, I. J.: Walk-to-work accessibility assessment for floating offshore wind turbines, Ocean Eng., 116, 216–225, 2016. a, b
Hall, M., Buckham, B., and Crawford, C.: Evaluating the importance of mooring line model fidelity in floating offshore wind turbine simulations, Wind Energy, 17, 1835–1853, 2014. a
Hallowell, S. T., Arwade, S. R., Fontana, C. M., DeGroot, D. J., Aubeny, C. P., Diaz, B. D., Myers, A. T., and Landon, M. E.: System reliability of floating offshore wind farms with multiline anchors, Ocean Eng., 160, 94–104, 2018. a, b
Hartmann, H., Walia, D., Adam, F., Ritschel, U., and Großmann, J.: One Step Installation of a TLP Substructure: Requirements, Assumptions, Issues, in: International Conference on Offshore Mechanics and Arctic Engineering, vol. 57786, American Society of Mechanical Engineers, V010T09A066, 2017. a, b
Hatledal, L. I., Zhang, H., Halse, K. H., and Hildre, H. P.: Numerical study for a catamaran gripper-monopile mechanism of a novel offshore wind turbine assembly installation procedure, in: International Conference on Offshore Mechanics and Arctic Engineering, vol. 57779, American Society of Mechanical Engineers, V009T12A030, 2017. a
H. H. Hersleth: Hywind Scotland Pilot Park Project Plan For Operation and Maintenance, Tech. rep., Norway, http://marine.gov.scot/sites/default/files/00516548.pdf (last access: 11 April 2022), 2016. a
Hutton, G., Torr, R., Proskovics, R., and Fong, T.: LIFES50+ D6.1 Risk management for deep water substructures, Tech. rep., UK, http://lifes50plus.eu/wp-content/uploads/2015/11/GA_640741_LIFES50_D6.1.pdf (last access: 11 April 2022), 2016. a
Ideol: Our Projects, https://www.bw-ideol.com/en/our-projects (last access: 11 April 2022), 2021. a, b
Jacobsen, V. and Rugbjerg, M.: Offshore wind farms–the need for metocean data, Copenhagen Offshore Wind, http://www.waterforecast.com/-/media/microsite_waterforecast/publications/about/waterforecast_offshorewindfarms-theneedformetoceandata.pdf (last access: 11 April 2022), 2005. a
James, R. and Ros, M. C.: Floating Offshore Wind: Market and Technology Review, Tech. rep., https://www.carbontrust.com/resources/floating-offshore-wind-market-technology-review (last access: 11 April 2022), 2015. a, b, c, d, e, f, g
Jiang, Z.: Installation of offshore wind turbines: A technical review, Renew. Sustain. Energ. Rev., 139, 110576, https://doi.org/10.1016/j.rser.2020.110576, 2021. a, b, c, d, e, f
Jiang, Z., Li, L., Gao, Z., Halse, K. H., and Sandvik, P. C.: Dynamic response analysis of a catamaran installation vessel during the positioning of a wind turbine assembly onto a spar foundation, Mar. Struct., 61, 1–24, 2018. a, b, c
Jiang, Z., Yttervik, R., Gao, Z., and Sandvik, P. C.: Design, modelling, and analysis of a large floating dock for spar floating wind turbine installation, Mar. Struct., 72, 102781, https://doi.org/10.1016/j.marstruc.2020.102781, 2020. a, b, c
Judge, F., McAuliffe, F. D., Sperstad, I. B., Chester, R., Flannery, B., Lynch, K., and Murphy, J.: A lifecycle financial analysis model for offshore wind farms, Renew. Sustain. Energ. Rev., 103, 370–383, 2019. a, b
Kausche, M., Adam, F., Dahlhaus, F., and Großmann, J.: Floating offshore wind-Economic and ecological challenges of a TLP solution, Renew. Energy, 126, 270–280, 2018. a
Koschinski, S. and Lüdemann, K.: Development of noise mitigation measures in offshore wind farm construction, Commissioned by the Federal Agency for Nature Conservation, 1–102, https://www.researchgate.net/profile/Sven-Koschinski/publication/308110557_Development_of_Noise (last access: 11 April 2022), 2013. a, b
Lambkin, D., Wade, I., and Stephens, R.: Estimating Operational Weather Downtime: A Comparison of Analytical Methods, in: International Conference on Offshore Mechanics and Arctic Engineering, vol. 58851, American Society of Mechanical Engineers, V07BT06A003, 2019. a
Lange, K., Rinne, A., and Haasis, H.-D.: Planning maritime logistics concepts for offshore wind farms: a newly developed decision support system, in: International Conference on Computational Logistics, Springer, 142–158, https://doi.org/10.1007/978-3-642-33587-7_11, 2012. a, b
Leimeister, M., Kolios, A., and Collu, M.: Critical review of floating support structures for offshore wind farm deployment, J. Phys.: Conf. Ser., 1104, 012007, https://doi.org/10.1088/1742-6596/1104/1/012007, 2018. a, b, c
Li, B.: Operability study of walk-to-work for floating wind turbine and service operation vessel in the time domain, Ocean Eng., 220, 108397, https://doi.org/10.1016/j.oceaneng.2020.108397, 2021. a
Liu, Y., Li, S., Yi, Q., and Chen, D.: Developments in semi-submersible floating foundations supporting wind turbines: A comprehensive review, Renew. Sustain. Energ. Rev., 60, 433–449, 2016. a, b
Maienza, C., Avossa, A., Ricciardelli, F., Coiro, D., and Georgakis, C.: Sensitivity analysis of cost parameters for floating offshore wind farms: an application to Italian waters, J. Phys.: Conf. Se., 1669, 012019, https://doi.org/10.1088/1742-6596/1669/1/012019, 2020. a
Maples, B., Saur, G., Hand, M., Van De Pietermen, R., and Obdam, T.: Installation, operation, and maintenance strategies to reduce the cost of offshore wind energy, Tech. rep., NREL – National Renewable Energy Lab., Golden, CO, USA, https://doi.org/10.2172/1087778, 2013. a
Maritime-Journal: A flipping good idea for floating turbines, https://www.maritimejournal.com/news101/marine-renewable-energy/a-flipping-good-idea-for-floating-turbines (last access: 16 August 2021), 2012. a
Martini, M., Jurado, A., Guanche, R., and Losada, I. J.: Evaluation of walk-to-work accessibility for a floating wind turbine, in: International Conference on Offshore Mechanics and Arctic Engineering, vol. 49972, American Society of Mechanical Engineers, V006T09A038, 2016. a
Mathiesen, M., Meyer, A. K., and Kvingendal, B.: Hywind Buchan Deep Metocean Design Basis RE2014-002, Tech. rep., Norway, http://marine.gov.scot/sites/default/files/metocean_design_basis_hywind_buchan_deep_mdb_rev2_0.pdf (last access: 11 April 2022), 2014. a, b
McCann, J.: Annual Report – International Energy Agency (IEA), Tech. rep., https://www.iea.org/reports/world-energy-outlook-2016 (last access: 11 April 2022), 2016. a
Musial, W., Butterfield, S., and Boone, A.: Feasibility of floating platform systems for wind turbines, in: 42nd AIAA aerospace sciences meeting and exhibit, 5–8 January 2004, Reno, Nevada, p. 1007, https://doi.org/10.2514/6.2004-1007, 2004. a
Musial, W., Heimiller, D., Beiter, P., Scott, G., and Draxl, C.: 2016 offshore wind energy resource assessment for the united states, Tech. rep., NREL – National Renewable Energy Lab., Golden, CO, USA, https://doi.org/10.2172/1324533, 2016. a
Myhr, A., Bjerkseter, C., Ågotnes, A., and Nygaard, T. A.: Levelised cost of energy for offshore floating wind turbines in a life cycle perspective, Renew. Energy, 66, 714–728, 2014. a
Nedwell, J., Langworthy, J., and Howell, D.: Assessment of sub-sea acoustic noise and vibration from offshore wind turbines and its impact on marine wildlife; initial measurements of underwater noise during construction of offshore windfarms, and comparison with background noise, Subacoustech Report ref: 544R0423, published by COWRIE, http://users.ece.utexas.edu/~ling/2A_EU1.pdf (last access: 11 Apirl 2022), 2003. a
Ocean-Energy-Resources: Bourbon collaborates in installation third floating wind turbine for Windfloat Atlantic, https://ocean-energyresources.com/2020/05/29/bourbon-collaborates-in-installation-third-floating-wind-turbine (last access: 16 August 2021), 2020. a
Offshore-Engineer: iFROG: Robot for Cleaning and Inspection of Offshore Wind Monopiles Completes Trials, https://www.oedigital.com/news/483611-ifrog-robot-for-cleaning-and-inspection-of-offshore (last access: 16 August 2021), 2020. a
offshorewind.biz: Largest Floating Offshore Wind Farm Stands Complete, https://www.offshorewind.biz/2021/08/24/largest-floating-offshore-wind-farm-stands-complete/, (last access: 11 January 2022), 2021. a
OREC: Floating wind: technology assessment, Interim findings, Tech. rep., https://ore.catapult.org.uk/app/uploads/2018/01/Floating-wind-technology-assessment-June-2015.pdf (last accessed: 16 August 2021), 2015. a, b
Paterson, J., D'Amico, F., Thies, P. R., Kurt, R., and Harrison, G.: Offshore wind installation vessels – A comparative assessment for UK offshore rounds 1 and 2, Ocean Eng., 148, 637–649, 2018. a
Remmers, T., Cawkwell, F., Desmond, C., Murphy, J., and Politi, E.: The potential of advanced scatterometer (ASCAT) 12.5 km coastal observations for offshore wind farm site selection in Irish waters, Energies, 12, 206, https://doi.org/10.3390/en12020206, 2019. a
Reuters: Shared anchors slice cost of floating wind parts, vessels, https://www.reutersevents.com/renewables/wind/shared-anchors-slice-cost-floating-wind-parts-vessels (last access: 16 August 2021), 2020. a
Roddier, D., Cermelli, C., Aubault, A., and Weinstein, A.: WindFloat: A floating foundation for offshore wind turbines, J. Renew. Sustain. Energ., 2, 033104, https://doi.org/10.1063/1.3435339, 2010. a
Saipem: Hywind, https://www.saipem.com/en/projects/hywind (last access: 16 August 2021), 2017. a
Salzmann, D. C., Prezzi, J., ten Haaf, S., and Groenteman, S.: Walk to work offshore using motion compensated gangways, in: OTC Brasil, OnePetro, https://doi.org/10.4043/26197-MS, 2015. a
Santos, F. P., Teixeira, Â. P., and Soares, C. G.: Operation and maintenance of floating offshore wind turbines, in: Floating Offshore Wind Farms, Springer, 181–193, https://doi.org/10.1007/978-3-319-27972-5_10, 2016. a
Sclavounos, P. D., Lee, S., DiPietro, J., Potenza, G., Caramuscio, P., and De Michele, G.: Floating offshore wind turbines: tension leg platform and taught leg buoy concepts supporting 3–5 MW wind turbines, in: European wind energy conference EWEC, 20–23 April 2010, Warsaw, Poland, http://web.mit.edu/flowlab/pdf/EWEC2010.pdf (last access: 16 August 2021), 2010. a
Skaare, B.: Development of the Hywind concept, in: International Conference on Offshore Mechanics and Arctic Engineering, vol. 57779, American Society of Mechanical Engineers, V009T12A050, 2017. a
Sperstad, I. B., McAuliffe, F. D., Kolstad, M., and Sjømark, S.: Investigating key decision problems to optimize the operation and maintenance strategy of offshore wind farms, Energy Procedia, 94, 261–268, 2016. a
Sperstad, I. B., Stålhane, M., Dinwoodie, I., Endrerud, O.-E. V., Martin, R., and Warner, E.: Testing the robustness of optimal access vessel fleet selection for operation and maintenance of offshore wind farms, Ocean Eng., 145, 334–343, 2017. a
Stehly, T., Beiter, P., and Duffy, P.: 2019 Cost of Wind Energy Review, Tech. rep., NREL – National Renewable Energy Lab., Golden, CO, USA, https://doi.org/10.2172/1756710, 2020. a
Stetco, A., Dinmohammadi, F., Zhao, X., Robu, V., Flynn, D., Barnes, M., Keane, J., and Nenadic, G.: Machine learning methods for wind turbine condition monitoring: A review, Renew. Energy, 133, 620–635, 2019. a
Tchakoua, P., Wamkeue, R., Ouhrouche, M., Slaoui-Hasnaoui, F., Tameghe, T. A., and Ekemb, G.: Wind turbine condition monitoring: State-of-the-art review, new trends, and future challenges, Energies, 7, 2595–2630, 2014. a
Teleki, P., Shuchman, R., Brown, W., McLeish, W., Ross, D., and Mattie, M.: Ocean wave detection and direction measurements with microwave radars, in: IEEE OCEANS'78, 6–8 September 1978, Washington, DC, USA, 639–648, https://doi.org/10.1109/OCEANS.1978.1151082, 1978. a
Topham, E. and McMillan, D.: Sustainable decommissioning of an offshore wind farm, Renew. Energy, 102, 470–480, 2017. a, b
Ulstein: Bourbon Orca, https://ulstein.com/references/bourbon-orca, last access: 21 January 2022. a
Umoh, K. and Lemon, M.: Drivers for and barriers to the take up of floating offshore wind technology: a comparison of Scotland and South Africa, Energies, 13, 5618, https://doi.org/10.3390/en13215618, 2020. a
Uzunoglu, E., Karmakar, D., and Soares, C. G.: Floating offshore wind platforms, in: Floating offshore wind farms, Springer, 53–76, https://doi.org/10.1007/978-3-319-27972-5_4, 2016. a
Vågnes, D., Monteiro, T. G., Halse, K. H., and Hildre, H. P.: Low-Height Lifting System for Offshore Wind Turbine Installation: Modelling and Hydrodynamic Response Analysis Using the Commercial Simulation Tool SIMA, in: International Conference on Offshore Mechanics and Arctic Engineering, vol. 84317, American Society of Mechanical Engineers, V001T01A030, 2020. a
Wayman, E. N., Sclavounos, P., Butterfield, S., Jonkman, J., and Musial, W.: Coupled dynamic modeling of floating wind turbine systems, in: Offshore technology conference, OnePetro, https://doi.org/10.4043/18287-MS, 2006. a
Wu, X. and Moan, T.: Dynamic behaviour of anchor handling vessels during anchor deployment, J. Mar. Sci. Technol., 22, 655–672, 2017. a
Wyatt, L.: Spatio-temporal metocean measurements for offshore wind power, J. Energ. Power Technol., 3, 2690-1692, https://doi.org/10.21926/jept.2101005, 2021. a
Xu, S., Murai, M., Wang, X., and Takahashi, K.: A novel conceptual design of a dynamically positioned floating wind turbine, Ocean Eng., 221, 108528, https://doi.org/10.1016/j.oceaneng.2020.108528, 2021. a, b
Yamamoto, M. and Morooka, C.: Dynamic positioning system of semi-submersible platform using fuzzy control, J. Brazil. Soc. Mech. Sci. Eng., 27, 449–455, 2005. a