the Creative Commons Attribution 4.0 License.
the Creative Commons Attribution 4.0 License.
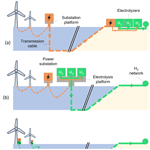
A critical review of challenges and opportunities for the design and operation of offshore structures supporting renewable hydrogen production, storage, and transport
Claudio Alexis Rodríguez Castillo
Baran Yeter
Shen Li
Feargal Brennan
Maurizio Collu
The climate emergency has prompted rapid and intensive research into sustainable, reliable, and affordable energy alternatives. Offshore wind has developed and exceeded all expectations over the last 2 decades and is now a central pillar of the UK and other international strategies to decarbonise energy systems. As the dependence on variable renewable energy resources increases, so does the importance of the necessity to develop energy storage and nonelectric energy vectors to ensure a resilient whole-energy system, also enabling difficult-to-decarbonise applications, e.g. heavy industry, heat, and certain areas of transport. Offshore wind and marine renewables have enormous potential that can never be completely utilised by the electricity system, and so green hydrogen has become a topic of increasing interest.
Although numerous offshore and marine technologies are possible, the most appropriate combinations of power generation, materials and supporting structures, electrolysers, and support infrastructure and equipment depend on a wide range of factors, including the potential to maximise the use of local resources. This paper presents a critical review of contemporary offshore engineering tools and methodologies developed over many years for upstream oil and gas (O&G), maritime, and more recently offshore wind and renewable energy applications and examines how these along with recent developments in modelling and digitalisation might provide a platform to optimise green hydrogen offshore infrastructure. The key drivers and characteristics of future offshore green hydrogen systems are considered, and a SWOT (strength, weakness, opportunity, and threat) analysis is provided to aid the discussion of the challenges and opportunities for the offshore green hydrogen production sector.
- Article
(1681 KB) - Full-text XML
- BibTeX
- EndNote
The climate emergency has prompted research, development, and commercialisation of new renewable energy technologies on an unprecedented scale. Offshore wind in northern Europe has to date become a tremendous success, surpassing most commercial and technical expectations. This success has buoyed investor and political confidence and led to even greater ambitions for sustainable electricity generation. Such a large proportion of electricity from a variable renewable energy resource, however, highlights the importance of energy storage in ensuring a reliable and resilient whole-energy system. Local storage of energy can address the necessity to transport electricity over longer distances, and using alternative energy vectors such as hydrogen and ammonia can help manage the output energy variability, as the stored energy can be fed back into the grid when needed. In addition, it can offer the potential to make more sustainable those sectors that are difficult to decarbonise, such as renewable heat, heavy industry, and transport.
Ocean renewable energies have a vast yet barely developed potential that includes not only the most well-known sources such as wind, waves, and tides but also others such as solar, thermal, or chemical (e.g. salinity gradient) resources. Numerous technologies have been investigated and developed to varying degrees, but only a few have reached a level of maturity high enough to allow for commercial development.
The following sections review pertinent studies that may potentially support offshore hydrogen production and associated functions such as storage and transport from an offshore support structure perspective. Rather than directly consider current offshore wind technology as the default solution for offshore hydrogen production as in Apostolou and Enevoldsen (2019), d'Amore-Domenech and Leo (2019), Dinh et al. (2021), and Jang et al. (2022), our approach is to perform critical analyses to identify challenges and opportunities based on knowledge and experience from closely related sectors such as offshore oil and gas (O&G) and offshore wind applications. Fundamental scientific and engineering understanding for the conversion of ocean renewable energy to liquid and/or gaseous fuels is set out so that optimal offshore structural solutions can be developed. Challenges and opportunities considered are those specifically related to “green” fuel production, including storage and transportation, and not to those already addressed for offshore wind electricity generation such as in Asim et al. (2022), Bashetty and Ozcelik (2021), Leimeister et al. (2018), and Otter et al. (2021).
2.1 Concepts proposed
In recent years, several offshore hydrogen demonstration projects based on wind energy have been reported, the most prominent being ERM Dolphyn (Caine et al., 2021), the Vattenfall project (Vattenfall, 2022), and Lhyfe (Rem, 2022), but much earlier concepts were proposed in the 1970s using ocean thermal energy conversion (OTEC) devices (Dugger and Francis, 1977) and, later, wave energy converters (Boscaino et al., 2015; Colucci et al., 2015) or other marine renewable energy devices (Turner et al., 2009; Patterson et al., 2019; Temiz and Javani, 2020). The use of offshore wind energy to produce alternatives has attracted most research with some earlier studies reported in Young et al. (1976), Steinberger-Wilckens (2002), Dutton (2003), and Kassem (2003). The majority of those studies considered the fuel production onshore from electricity generated offshore. Murahara and Seki (2008), in a pioneering fashion at the time, proposed offshore wind energy integrated with hydrogen production within a single offshore facility. A “megafloat” offshore electrolysis plant that utilised offshore wind energy to produce sodium as solid fuel to then obtain hydrogen was proposed. The system concept was presented together with estimates of the power required to operate the plant and of the amount of chemical byproducts that could be commercialised. A similar concept for the floating structure was also proposed in Tsujimoto et al. (2009), designed as a “sailing” wind farm. The offshore wind farm accommodated hydrogen production equipment along with a storage capacity of 9900 t of hydrogen in the form of organic hydride.
The proposed use of more conventional arrangements of offshore wind turbines (OWTs) to produce green fuels has since been reported by several authors. Most use the terms “stand-alone” or “integrated” to refer to offshore wind generation connected to a hydrogen production plant located onshore and powered by local, non-grid-connected electricity. Zhao et al. (2011) was found to be the earliest study of a remote offshore wind energy system that stores energy in the form of hydrogen and chlorine. Additionally, a dynamic analysis model that considered the variability of wind energy production to address the performance of hybrid wind–hydrogen systems was proposed. The thermodynamic energy balance, the energy management strategy, the performance of the wind energy conversion, the electrolyser array, the modified PEM (proton exchange membrane) electrolysis fuel array, and the hydrogen storage systems were also detailed.
With the success of onshore wind turbines and more recently offshore wind, an increasing number of papers concerning offshore wind–hydrogen systems have been published. Some of the most relevant and prominent are detailed in the references (Rogeau et al., 2023; Lee et al., 2023; Kumar et al., 2023; Bonacina et al., 2022; Ibrahim et al., 2022; Henry et al., 2022; Jang et al., 2022; Mehta et al., 2022; Lucas et al., 2022; Dinh et al., 2021; Franco et al., 2021; Song et al., 2021; Woznicki et al., 2020; Caglayan et al., 2019; Hou et al., 2017; Ioannou and Brennan, 2019; Serna et al., 2015; Meier, 2014). These are mainly concerned with techno-economic aspects of wind–hydrogen systems; feasibility studies; sensitivity analyses of costs; different scenarios for hydrogen production, storage, and transportation; comparisons between distributed, centralised, and onshore hydrogen production; comparisons of electrolyser technologies; the use of alternative energy vectors for hydrogen exportation such as ammonia and liquid organic hydrogen carriers; modelling and simulations of energy management or control strategies for the generated energy; the balance between produced hydrogen and consumed energy; and other related topics related to the levelised cost of hydrogen (LCoH2).
In addition to offshore wind turbines, alternative concepts/technologies to harness wind energy to produce hydrogen have also been proposed and developed. In Schmitz and Madlener (2015), a fully automated “Powership” towed by a so-called “Sky Wing” (a kite) was proposed in which energy could be stored in the form of compressed air or hydrogen. An economic feasibility analysis concluded that compared to stationary floating wind, this concept avoids the need for foundations or mooring systems. It is suggested that maintenance and repair can be done in sheltered harbour/coastal areas and has the mobility potential to locate to more favourable sites depending on seasonal/other factors. Gilloteaux and Babarit (2017) proposed a wind-driven catamaran dedicated to hydrogen production using Flettner rotors to propel a ship and hydro-generators to convert the kinetic energy of the water flow into electricity and then into hydrogen by electrolysis (Fig. 1). The numerical case studies demonstrated that an 80 m long catamaran could produce net power of almost 500 kW at a forward speed of 8 m s−1. Clodic et al. (2018) not dissimilarly investigated a wind energy ship concept dedicated to hydrogen production by analysing the advantages and limitations of four different technologies – rigid sails, kite wings, air foils, and Flettner rotors – and concluded that all the selected technologies are capable of converting wind energy into kinetic energy and then hydrogen. Based on those findings, Babarit et al. (2018) report the techno-economic feasibility of fleets of wind-driven sailing ships and platforms for far-offshore hydrogen production. Different scenarios for hydrogen production, transportation, and (compressed or liquified) storage were assessed. Due to the low volumetric energy density of hydrogen at standard temperature and pressure, the high costs of transportation and distribution were identified as the most challenging. In Babarit et al. (2019), other fuel options such as synthetic natural gas, methanol, Fischer–Tropsch fuel, and ammonia were considered, and it was concluded that in terms of energy and economic performance, methanol may be the best energy vector for far-offshore wind energy ships systems, despite the costs associated with CO2 production. Another alternative but not dissimilar concept for offshore hydrogen production and onboard storage of wind energy was proposed in Alexander (2019) (Fig. 2).
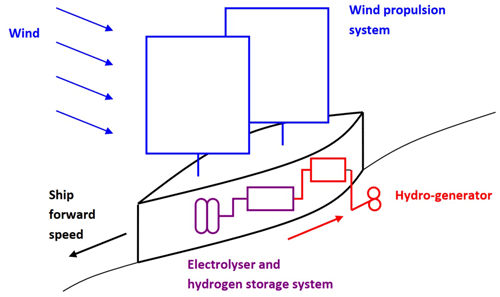
Figure 1Working principle of a wind-driven ship dedicated to hydrogen production. Reproduced from Gilloteaux and Babarit (2017) with permission from the American Society of Mechanical Engineers.
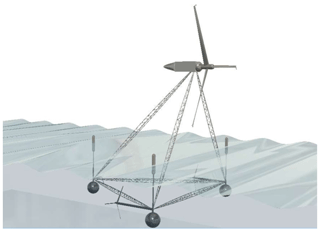
Figure 2Alternative concept of an offshore wind-energy–hydrogen-integrated production system. Reproduced from Alexander (2019) with permission from the American Society of Mechanical Engineers.
From the literature review reported above, it can be seen that the majority of research to date in this area has unsurprisingly focused upon the techno-economics of offshore wind–hydrogen systems and in particular on whether a centralised or distributed system is likely to be optimal. Offshore wind turbines on fixed-bottom support structures are currently the most mature technology for harnessing offshore wind energy and probably the best option for integration of hydrogen production into shallow waters in the near future; however, larger wind energy deployments are taking place in deeper waters where floating systems are the only available option. Given this development, it would seem prudent that further investigations and analyses need to be performed not only in terms of thermodynamics, energy generation, and consumption associated with hydrogen production but also regarding the stability and sea- and station-keeping performance of potential floating support structures. The sizing and adaptation of conventional offshore marine energy support structures to allow for containing hydrogen production equipment, storage, and offloading facilities has yet to be addressed. In contrast to offshore wind facilities for electricity generation where fixed monopiles and jacket structures are broadly accepted for shallow-water turbine support and semi-submersibles, spars and barges seem to be the preferred options for deep waters; further research needs to be conducted to study which support structural configuration better matches the requirements of offshore hydrogen production systems.
2.2 System configuration strategies
A number of studies have analysed and compared possible typologies or scenarios for the hydrogen system configuration, i.e. onshore, centralised offshore, distributed offshore, shared with O&G platforms, and partially (surplus energy) or fully dedicated. For example in Jepma et al. (2018), the net present economic value for the following scenarios was analysed:
- (a)
offshore wind energy farm plus shared hybrid O&G platform that includes electrolysers and export pipelines and cables
- (b)
offshore wind farm plus shared O&G platform or direct connection to the grid
- (c)
hydrogen production integrated into each wind turbine (distributed hydrogen production) plus the O&G platform (for hydrogen compression and offloading).
It was concluded that locating electrolysers together with wind turbines (a distributed hydrogen scenario) is likely to be economically superior to other alternatives due to significant cost savings in AC/DC (alternating current/direct current) conversions and cables for electricity transportation. Jang et al. (2022) also compared the net present value among three configurations for the connection of wind power plants with hydrogen production facilities, namely, centralised onshore, distributed offshore, and centralised offshore. Based on Rogeau et al. (2023), Ibrahim et al. (2022), and Jang et al. (2022), the following configurations are envisaged for generic ocean renewable hydrogen system facilities:
- (a)
Centralised onshore means the ocean renewable energy farm produces electricity which is sent ashore, powering the hydrogen plant. Assuming a remote location, it is required to gather the AC electricity output from each ocean energy device to a substation to be converted to DC so that it can be sent ashore via submarine cables. Once onshore, a new electricity conversion from DC to AC is likely to be needed to power the electrolyser plant (Fig. 3a).
- (b)
Centralised offshore is similar to centralised onshore but with the hydrogen production on an offshore large-scale electrolysis floating platform near the ocean renewable energy farm. The hydrogen production platform is likely to contain desalination units, electrolysers, cooling units, compression units (depending on the type of electrolyser), a hydrogen buffer tank, and a backup battery system. The electricity from each of the ocean energy devices would be delivered via electric cables to an offshore substation where the total electricity is combined to power the centralised hydrogen production platform. The produced hydrogen can then be exported (Fig. 3b).
- (c)
Distributed (decentralised) offshore means that the equipment necessary for hydrogen production is accommodated by each individual ocean energy device. A typical layout for the electrolysis facility is likely to include a desalination unit, an electrolyser, a cooling unit, a compression unit (if a PEM electrolyser is not adopted), a hydrogen storage tank (as a buffer), and a battery storage system as backup power for the facility. The individual (hydrogen) production from each device is delivered through risers and can be collected in a subsea manifold to be exported (Fig. 3c).
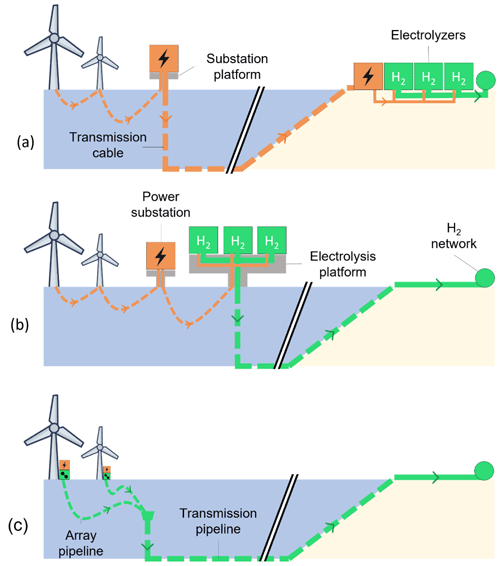
Figure 3Configurations considered for deployment of green hydrogen: (a) onshore, (b) centralised offshore, and (c) decentralised offshore. Reproduced from Rogeau et al. (2023) with permission from Elsevier B.V.
In either distributed or centralised hydrogen configurations, a liquefaction unit can be integrated into the facility so that liquified hydrogen can be produced and stored offshore to be later exported. According to Jang et al. (2022), for offshore wind turbines, the distributed hydrogen production was found to be the most economical alternative with an LCoH2 of USD 13.34 per kilogram of H2, followed by the centralised (USD 13.66 per kilogram of H2) and the onshore (USD 14.1 per kilogram of H2) concepts. Ibrahim et al. (2022) extensively discuss the advantages and disadvantages of the above configurations and for offshore wind turbines also focus on the electrolyser technology, the floating platform, and the energy transmission vector (electrical power or offshore hydrogen pipelines). The study suggests “offshore centralised” may compete well compared with the “offshore decentralised” configuration because of reduced complexity and greater flexibility for upgrading hydrogen equipment. However, it would have the additional capital expenditure (CAPEX) of a floating platform to accommodate the relevant equipment and would represent a single point of failure. In terms of total lifetime cost, Rogeau et al. (2023) report that onshore electrolysis is the most economical option, followed by the centralised offshore and decentralised offshore schemes, but in terms of LCoH2, the offshore electrolysis options are much cheaper, particularly for far-from-shore locations. Indeed, especially for deep waters (over a 100 m), the decentralised option shows increasingly preference over the centralised scheme for the coming years.
Bonacina et al. (2022) analysed a centralised hydrogen system assuming that a redundant O&G platform is reused to accommodate hydrogen production, liquefaction, and storage systems. It is concluded that a dedicated offshore-wind-farm-powered system for ship refuelling purposes would be able to achieve an LCoH2 of less than EUR 4 per kilogram of H2, depending on the electrolyser-to-wind-capacity ratio and the wind farm power capacity. Concerning the latter, Mathur et al. (2008) have suggested that 100 MW is the minimum capacity for economically feasible hydrogen production using offshore wind turbines. Clearly, under the current costs of offshore wind and natural gas, these conclusions deserve to be revisited. Also, the above configurations should be investigated further by considering other ocean energy devices, as well as the integration with liquefaction and storage facilities.
As for O&G and conventional offshore wind structures, a set of key requirements will drive the design and selection of an offshore green hydrogen system. Some are more general and are strongly related to the techno-economics of the system, such as geographical location, resource characteristics, and the payload of the offshore system (energy production facilities, including the hydrogen system), while other design aspects are more specific to the support structure of the floating system, such as the environmental conditions, hydromechanics, structural performance of the system, and risk tolerance. The more general considerations are addressed in the following subsections, and those more specific to floating system characteristics are dealt with in Sect. 4.
3.1 Site conditions and resource compatibility
For typical offshore O&G and renewable energy projects, the available resources (e.g. oil, gas, wind energy, wave energy) dictate the optimal geographical location of the offshore facility. Once the location is determined, a set of site-specific characteristics (area, water depth, distance to shore, etc.) drive the design and selection of the offshore system as a whole. These will be certainly applicable for an offshore hydrogen system, but the availability of existing infrastructure at or near the proposed location (e.g. O&G platforms, depleted O&G reservoirs, power cables, pipelines, subsea layout) may also play an essential role in the economic feasibility of an offshore hydrogen system. Several studies have demonstrated that LCoH2 can be significantly reduced and become commercially competitive if existing facilities can be repurposed/shared. For example, Peters et al. (2020) addresses the benefits of a cost-effective, balanced, and secure transition of the North Sea from O&G towards renewable energy production through the PosHYdon project; McKenna et al. (2021) consider the integration of the O&G and renewable energy sector for North Sea-neighbouring countries and proposes the repurposing of O&G platforms into hydrogen production facilities that could deliver hydrogen to shore via existing and/or new purpose-built pipelines. Zulkifli et al. (2022) similarly consider the reuse of ageing fixed offshore platforms in Malaysia as OTEC power plants. Depleted O&G reservoirs and pipelines could also be used to store hydrogen, as suggested in Pearson et al. (2019).
Different from O&G, where the available resource is largely independent of the environmental conditions, green offshore hydrogen systems are inherently related to the environmental resource and therefore temporally and spatially variable. Consequently, the characterisation of and compatibility with energy demand is critical for the economic operation of these systems.
3.1.1 Metocean and geotechnical conditions
In the present context, metocean conditions refer to wind, wave, or current regimes used to characterise the environment apart from the economic energy resource aspects, while geotechnical conditions refer to seabed characteristics and soil properties. Those conditions define the requirements for the design of the offshore system (support platform, mooring system, cables and riser systems, etc.) and dictate performance under operational and survival conditions. From the perspective of environmental loads on the support structure, the assessment of metocean conditions is similar to other offshore platforms.
3.1.2 Renewable energy source compatibility
Wind energy as the primary resource for offshore green hydrogen production systems should not be taken for granted based solely on the maturity of offshore wind turbine technology. In addition to the resource potential (the theoretical amount of energy that can be exploited during a given time frame in each location), resource variability and resource predictability are key considerations for hydrogen production systems. Resource variability refers to how the resource changes in the short (hours or days) and the long (months or years) term, whereas resource predictability is the accuracy of forecasts and prediction models (d'Amore-Domenech and Leo, 2019). Although resource characteristics are intrinsic to a given location, each energy resource (wave, wind, current, solar, etc.) will exhibit independent short- and long-term characteristics (for example, from season to season, year to year).
The characteristics of the available resource potential and variability should define the type(s) of technology to harness the energy from the energy resource (wind, wave, tidal, solar, etc.) for a given site. The size, power capacity, and operational requirements of the hydrogen equipment should then be selected according to the hourly, daily, monthly, and/or yearly available resources. Caglayan et al. (2019) explain that the choice of the weather year for the design of a hydrogen production system can significantly affect the total annual cost of the system. Another study (Mehta et al., 2022) concluded that designing turbines specifically for hydrogen production (LCoH2 optimised) tend to have a higher specific power over the LCoE-optimised (levelised cost of energy) turbine designs, but oversizing the electrolyser compared to the turbine rating would be a better design strategy. The variability of the energy resource and its compatibility with the performance characteristics of both the energy extraction devices and the hydrogen production equipment are critical aspects that deserve further research.
3.2 Support structure payload
The “payload”, sometimes indicated as “topside” in offshore O&G engineering, refers to all the equipment that is not the support structure. For a hydrogen system, this equipment refers to the energy extraction devices and the hydrogen facilities.
3.2.1 Energy extraction devices
The devices for energy harvesting are focused on a single energy resource and are usually categorised according to their working principle. Abundant literature can be found on available device types as well as on their current development stage (e.g. Blanco-Fernández and Pérez-Arribas, 2017; IRENA, 2020; ITTC, 2017, 2021). Several of the key drivers for the selection of the energy-harnessing system for offshore hydrogen are the same as for conventional electricity generation, with the most relevant being the technology readiness level (TRL) and LCoE. Indeed, several feasibility studies have concluded that LCoH2 is strongly dependent on LCoE (d'Amore-Domenech and Leo, 2019; Franco et al., 2021; Raut and Goudarzi, 2018). Other characteristics such as the area and volume “footprint” (in kW m−2 and kW m−3, respectively) of the device and its capacity factor also remain as essential features for hydrogen production.
On the other hand, there are additional aspects of the device that become crucial when considering the hydrogen production scenario, the available deck/internal compartments surface area and volumes, to accommodate the relevant equipment and possibly for product storage. In the same context, another desirable feature of an energy device is scalability, i.e. the flexibility of the device to be redimensioned or adapted, to allow for the fulfilment of the requirements for the accommodation of the hydrogen facilities.
3.2.2 Hydrogen facilities
In the context of the present work, the hydrogen facilities refer to, among others, electrolysers, the desalination plant, compression and/or liquefaction machines, storage tanks, offloading machinery, and pipelines, i.e. all the facilities that are not present in a solely conventional offshore (electricity) energy generation system.
Electrolyser technology
The choice of electrolyser technology is a primary consideration, and several papers discuss and critically analyse available technologies (Buttler and Spliethoff, 2018; d'Amore-Domenech and Leo, 2019; d'Amore-Domenech et al., 2020; Meier, 2014). Alkaline electrolysis (AEL) and proton exchange membrane (PEM) electrolysis have both been reported as preferred solutions in most studies (Bonacina et al., 2022; Henry et al., 2022; Ibrahim et al., 2022; Lucas et al., 2022), with an increasing tendency to the latter due to its compact design, pressurised operation, load flexibility, and fast response, despite being more expensive than AEL (Buttler and Spliethoff, 2018; d'Amore-Domenech et al., 2020).
Indeed, operational characteristics of the electrolyser, such as power consumption, water consumption, minimum loading, or hydrogen output, are essential aspects for the power management strategy of the whole offshore hydrogen system, i.e. the control algorithm used to allocate the available power to the different components of the system (desalination, compression and/or liquefaction units, storage system, etc.). If a decentralised system is considered, challenges arise from the fact that this equipment may be subject to displacements, velocities, and accelerations during operation, which usually do not occur in an onshore setting. The effects of motion on electrolyser performance are not well understood and need to be investigated and, if necessary, mitigated against. For an offshore hydrogen plant powered by offshore wind energy, in addition to considering the wind turbine performance as a function of average wind speed, the electrolyser (and its auxiliary equipment) performance depends on input power and its instantaneous variability. Electrolyser sensitivity or otherwise to the minimum input power requirement, power intermittency, and start-up time are some of the characteristics that need to be considered. In the context of the ERM Dolphyn project, a systematic review of a typical PEM electrolyser package identified that minor adaptations would be necessary to operate that electrolyser on an offshore floating semi-submersible platform (Caine et al., 2021), including protection from environmental damage and some modifications in ancillary equipment (e.g. fluid level gauges). Thus, PEM electrolysers have been considered for that project, particularly due to their better suitability for variable electrical input and low OPEX (operational expenditure; associated with the reduced need for manual intervention) compared to alkaline technology.
Desalination unit
Both AEL and PEM electrolysers need processed water to operate (they cannot directly use seawater). In the offshore setting, the processed water is obtained from seawater using desalination units, which might be powered by the available ocean renewable energy. Distillation and reverse osmosis are the main mature and proven technologies for desalination. The former produces higher purity water (i.e. requires less post-treatment for demineralisation) but at a higher thermal energy consumption, while the latter is the most widely used technology, being slightly more efficient but requiring chemical treatment before being used for electrolysis. For the analyses of offshore hydrogen systems, some authors (d'Amore-Domenech and Leo, 2019; Meier, 2014) expressed a preference for distillation technology, while others (Bonacina et al., 2022; Ibrahim et al., 2022) have preferred reverse osmosis. Indeed, for the design of Dolphyn's 2 MW scale prototype, reverse osmosis was considered due to its lower CAPEX, smaller physical footprint, and lower weight and energy compared to that required for thermal desalination, while, for the design of Dolphyn's 10 MW commercial-scale demonstrator, thermal desalination was selected due to its low maintenance requirements (suitable for long-term unoccupied operations) compared to reverse osmosis technology (Caine et al., 2021). In any case, the volumetric seawater inflow and the power required for seawater pumps, compressors, and auxiliary systems for the desalination unit should be balanced against the output power of the ocean energy device(s). Operational characteristics and component limitations of the desalination unit as well as the potential use of waste heat to power the desalination unit need to be carefully addressed.
Storage and transportation
The delivery of hydrogen either as compressed gas or liquid or in the form of another fuel, for instance, ammonia or methanol, is another essential element within the offshore green hydrogen system. Each alternative has technical benefits and limitations as well as the underlying challenge to achieve an economically feasible green fuel. Such choices directly affect the requirement for compression, liquefaction, and storage facilities. In Babarit et al. (2018) a comparison is made between compressed hydrogen (CH2) and liquefied hydrogen (LH2), concluding that CH2 scenarios have the best energy efficiency; current cost estimates for LH2 and CH2 were similar, but LH2 is considered the most promising in the longer term due to expected cost reduction (up to 50 %) and much greater flexibility for delivery. d'Amore-Domenech et al. (2021) have analysed several scenarios for bulk power transmission at sea from a 600 MW offshore platform to land (equivalent to a centralised configuration), considering CH2, LH2, and electricity, concluding that the best solution is to transport liquified hydrogen by ship. According to Miao et al. (2021), the small-scale fluctuations in hydrogen production (due to, for example, the hourly or daily variability of the ocean energy resource) can be handled by a short-term storage system (e.g. buffer tanks); however, seasonal variations (potentially due to the mismatch between supply and demand) require large-scale energy management solutions. For the distributed (decentralised) configuration, the inner volumes within the floater's hull or eventually over the deck could be used as buffer tanks for short-term CH2 storage, such as in the HyFloat concept (12toZero, 2023). However, the platform layout should be carefully designed to prevent the accumulation of flammable gas releases. Several HAZOP (hazard and operability), fire, and explosion analyses and quantitative risk assessments would be required. Offshore production and storage of LH2 could be a viable alternative, allowing for its exportation to remote markets via ships or delivery as fuel for marine transportation (Bonacina et al., 2022). In this case, liquefaction, cryogenic storage, and offloading facilities are required and should be installed together or near the hydrogen support platform. In addition, the offshore layout of the hydrogen system (including the ocean energy production farm) should allow for the access of shuttle hydrogen tankers to the storage platform(s). Under this scenario, a centralised configuration seems to be more suitable than a distributed one.
The economic feasibility of energy transportation via power cables and gas (compressed hydrogen) pipelines has been also investigated and concluded that, for long distances, pipeline transmission is cheaper than electrical cables (according to d'Amore-Domenech et al., 2021, over 1000 km for a 2 GW deep-water power transmission) and pipelines have higher energy transmission capacity and lower energy losses. A typical CH2 infrastructure is comprised of gas buffer storage tanks, compression units, and gas pipelines. According to Jepma et al. (2018), a pressure of 100 bar is expected to be enough for long-distance hydrogen transportation and suitable for typical existing O&G pipelines. Furthermore, if hydrogen is obtained from PEM electrolysers, the cost of compressors could be avoided or significantly reduced because the produced hydrogen based on PEM technology comes already pressurised (Ibrahim et al., 2022; Mehta et al., 2022). Another advantage of CH2 is that is that the pipelines for transportation have low operational costs and long expected lifetimes (40 to 80 years; Birol, 2019). Indeed, according to DNV (2022), between 50 % and 80 % of hydrogen pipelines are expected to be repurposed from natural gas pipelines with a cost of just 10 %–35 % of new construction costs. In general, exported CH2 is expected to be delivered for immediate utilisation or to be stored in large-scale facilities. Currently, low utilisation and a lack of energy storage capacity are some of the main reasons for the high cost of CH2. Regarding storage of CH2, some authors have proposed the use of existing offshore O&G pipelines (Pearson et al., 2019); underground subsea storage considering several storage durations (Dinh et al., 2021); or depleted offshore gas fields, saline aquifers, or salt caverns (Scafidi et al., 2021).
The transportation of hydrogen by means of alternative energy carriers such as ammonia, methanol, or a different liquid organic hydrogen carrier (LOHC) is another option (Birol, 2019; Henry et al., 2022; Ibrahim et al., 2022) that would require additional equipment to support, for example the methanation and/or hydrogenation processes and their products: methane and/or methanol, respectively. The main advantage of the alternative energy carriers is the cost reduction in transportation and storage by using existing infrastructure (pipelines, ships, storage tanks, etc.).
Regarding the export of hydrogen through risers and pipelines, an important aspect is the dynamics of flexible lines. The O&G industry has a long history of analysing and designing flexible pipelines; however existing flexible risers have not been formally certified for use with pure hydrogen (Caine et al., 2021). Flexible pipelines consist of leakproof thermoplastic barriers and steel wires resistant to corrosive environments, whose design and characteristics are well understood. For instance, the maximum motion envelope of the substructure should consider the minimum bending radius (MBR) of the riser and be a key interface point with the mooring system design.
Nevertheless, there are still concerns about the structural performance of flexible pipelines regarding the combined loading, such as internal and external pressure, bending, axial tension, and torsion. Miyazaki et al. (2018) demonstrated with the numerical analysis supported by experimental tests that the current design methodology ensures a robust design. Nevertheless, undetected defects and imperfections can still cause trigger failure mechanisms. For instance, the numerical model developed by Zhu et al. (2021) confirmed that even under ovalisation developed prior to operation, the tensile rigidity was not affected as long as it was less than 1 %, highlighting the importance of the manufacturing and installation control process. Hameed et al. (2018) gave a list of potential failure modes of flexible pipelines, such as external sheath damage, damage of tensile armours due to fatigue, kinks due to corrosion, and over-bending. The study argued that a risk-based inspection methodology can establish a cost-effective strategy for inspection and monitoring to achieve structural safety above the expected level. Although the risk-based methodology is promising, the effectiveness of the existing subsea inspection techniques to detect defects and damages is highly questionable due to the complexity involved in the multi-layered flexible pipes and their interacting failure mechanisms. For this reason, a risk-based design methodology with rigorous control during manufacturing is the recommended practice for the flexible pipelines for hydrogen transportation.
Support structure considerations are specifically related to site characteristics and functional requirements, including structural reliability.
4.1 Metocean conditions
The characterisation and assessment of metocean conditions is perhaps the most critical aspect in the design of offshore structures. Unlike dedicated offshore energy extraction devices, where the characterisation of the energy resource (wind, wave, current, etc.) is typically done in terms of monthly, seasonal, or yearly averages to obtain mean power and capacity factors, for hydrogen production systems' shorter-term characterisation is required to address the compatibility of the instantaneous generated power with the operational characteristics of hydrogen production equipment (electrolysers, desalination units, etc.). Floating offshore wind structures need to be designed taking into account the complex structural aerodynamics of the rotor coupled with the hydrodynamics of the floater excited by the wind, wave, and machine dynamic characteristics.
In summary, similar to the design of conventional offshore floating wind energy systems, metocean conditions define the capacity of the energy extraction devices to be installed on board, which determines the payload of the support structure and consequently minimum primary dimensions. Other aspects such as stability, motion responses, storage capacity, or additional onboard equipment will also influence the main dimensions of the support structure and will be discussed further below.
4.2 Hydromechanics
From a hydromechanics perspective, for the distributed scenario, the additional hydrogen production and storage systems may have an important impact on platform mass distribution and possibly on the wet geometry affecting stability and sea-keeping and station-keeping performance. In other words, the safety and operability of the whole system may be substantially impacted, and therefore the primary dimensions of the platform may need to be increased. The freeboard, air gaps, motion, resonance periods, accelerations, and velocities at certain locations of sensitive equipment (e.g. wind turbine nacelle, electrolysers, separators, etc.); loads due to liquid motions inside storage and buffer tanks; and interactions between platforms, risers (pipelines), cables, and mooring lines are some of the aspects that should be carefully assessed, as should the survivability under extreme weather conditions. Despite their crucial importance these aspects do not appear to have been addressed yet in the literature.
4.3 Structural design and asset management
Currently, the majority of operational offshore wind farms are situated in the relatively shallow southern North Sea and are in the main monopile structures. As the wind industry moves to deeper seas with more powerful and larger turbines, jacket-type support structures are becoming a strong alternative for intermediate water depths since these have a higher load-bearing capacity and offer structural redundancy that a monopile lacks. Floating substructures for offshore wind turbines are the only viable option for water depths beyond approximately 70 m (Wu et al., 2019; Veers et al., 2023). These floating support structure solutions can be grouped into four types: (a) semi-submersibles, (b) tension leg platforms (TLPs), (c) spars, and (d) barges (see Fig 4).
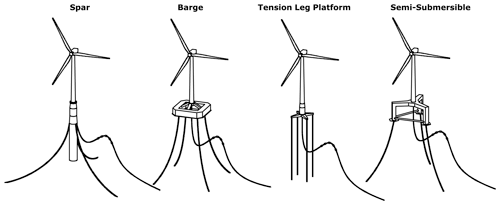
Figure 4Floating offshore wind turbine substructure design classes. Reproduced from Scheu et al. (2018).
In recent years, numerous review studies have been reported on the past, present, and future support structures used for offshore wind (Leimeister et al., 2018; Igwemezie et al., 2019; Wu et al., 2019). The design of offshore support structures is commonly based on the standards prepared by the certification authorities and sector bodies such as Det Norske Veritas (DNV, 2014), the American Bureau of Shipping (ABS, 2020), the International Electrotechnical Commission (IEC, 2019), and the American Petroleum Institute (API, 2019), combining the accumulated know-how gained by experience and engineering models supported through experimental and numerical tests.
The critical design limit states can vary depending on the type of the structure employed along with the site conditions. For example, according to Sunday and Brennan (2021), structural dynamics (avoiding resonance with blade-passing frequencies) and geotechnical issues (soil-structure interaction, scour, liquefaction, pile drivability), which are part of the serviceability limit state (SLS), were invariably found to be the limiting design criterion for monopiles as opposed to the fatigue limit state (FLS) or ultimate limit state (ULS).
As far as hydrogen production and storage on the floating wind support structure are concerned, ULS and FLS can also have a significant impact on the structural design. In an attempt to design a lighter support structure with more space to accommodate hydrogen production and storage units, the diameter-to-thickness ratio () of the constituent tubular members and joints is expected to increase. Consequently, with the increase in the slenderness ratio, the local buckling phenomenon becomes more pronounced (Guo et al., 2013). Moreover, the high- structures are much more sensitive to geometric imperfections (Li and Kim, 2022). Thus, the quantification of typical geometric imperfections (both magnitude and shape) for as-built and in-service offshore structures is necessary.
Progressive fatigue damage is a paramount concern for all dynamically sensitive offshore (wind) structures with welded tubular joints operating under harsh offshore environments (Dong et al., 2011; Yeter and Garbatov, 2022). Under sufficient load cycles, every welded tubular joint on an offshore structure can be a potential source of stress hotspots, leading to crack initiation and subsequent propagation through thickness. As far as the fatigue damage assessment for offshore structures is concerned, both time-domain and frequency-domain (spectral-based) approaches are important tools in understanding criticality or otherwise.
4.3.1 Time-domain approach
The time-domain load analysis and structural response simulation have emerged as the recommended practice for floating and fixed offshore wind. This is only because time-domain simulations carried out by powerful numerical tools (Otter et al., 2022) can capture the coupling effects arising from wind turbine dynamics, wind-induced loadings, wave-induced loadings, boundary conditions, and their interactions (Patryniak et al., 2022). Based on the design load case (power production) defined for FLS, wind-induced loading is the predominant factor for total fatigue damage, and the interaction between waves and wave-induced loading cannot be omitted, as shown by both Dong et al. (2011) and Fan et al. (2020).
The time-domain approach is expected to remain the preferred solution for offshore wind structures for hydrogen production. Kvittem et al. (2011) reported that waves reduced the resonant effect of the wind-induced loading for a semi-submersible offshore wind turbine, which highlighted the nonlinear nature of the dynamic behaviour of floating wind and the importance of fully coupled analysis. Xu et al. (2019) not only agreed that wind-induced loading is indeed the dominating factor for fatigue consideration during operational conditions but also pointed out that fatigue damage was found to be more sensitive to wave load, especially in high sea states, for the mooring line. Similarly, Marino et al. (2017) found a relatively low impact from waves onto fatigue loads during power production conditions, whereas a substantial underestimation was expected for the fatigue load due to the linear wave modelling during the parked condition.
Although Haid et al. (2013) and Stewart et al. (2013) were not inclined to give any conclusive recommendation in terms of simulation length for fatigue analysis, Kvittem and Moan (2015) calculated a 10 min simulation and 1 h simulation and underestimated the 3 h base simulation by approximately 10 % and 4 %. Both overestimations that come from unidirectional wind and waves as well as the underestimation that comes from omitting wave–wind–current interactions (Kvittem and Moan, 2015; Kvittem et al., 2011) should be considered.
In addition, considerable effort has been given to decreasing the computational effort required for fully coupled time-domain simulations to estimate the total fatigue damage. Katsikogiannis et al. (2021) developed a lumping process to design load cases through damage-equivalent contour lines, showing a significant improvement in the computational effort by 93 %, with a 6 % deviation from the complete scatter analysis, which was estimated to be between 40 %–80 % for the frequency-domain approach in Katsikogiannis et al. (2022).
4.3.2 Frequency-domain (spectral-based) approach
Prior to today's powerful software for the design, the time-domain fatigue analysis has deemed to be too cumbersome as it deals with complex structural models of offshore platforms solved for a high number of possible load combinations. This statement is still valid as far as the multi-disciplinary design optimisation problem of offshore wind turbines is concerned (Patryniak et al., 2022). Alternatively, the frequency-domain fatigue damage analysis can offer a quick and satisfactory solution to analyse and design for the ship and offshore structures depending on the loading bandwidth (Yeter and Garbatov, 2022).
A recent study reviewed the spectral methods for fatigue analysis from a historical point of view by Dirlik and Benasciutti (2021). Although other spectral methods were also discussed, the review gave more emphasis on the models developed by Dirlik and improved by the Tovo–Benasciutti method – regarded as the most used methods.
It has been argued in many studies that the effectiveness of the spectral methods varies depending on the relevant power spectral density characteristics (i.e. multi-mode, spectral width, closed mode). Mrsnik et al. (2013) revealed that the Zhao–Baker method was more appropriate for the automotive industry spectra, whilst Yeter et al. (2016) showed that the Tunna spectral fatigue model developed for the railway industry could also be adopted for offshore wind. Nevertheless, the consensus has been that the Tovo–Benasciutti and, especially, the Dirlik method are the most effective methods to replace computationally expensive time-domain solutions as far as the OWTs are concerned, as supported by Arany et al. (2014). The advantage of the success of the Dirlik method stems from the fact that it involves many bandwidth-related parameters, making the model very flexible; hence, the statistical model gains higher predictive power.
In light of the studies mentioned above, it can be argued that the degree to which this overestimation manifests itself depends on the load bandwidth. For example, an offshore structure used for hydrogen production and storage is more dominantly exposed to wave- and current-induced loading, and the influence of wind-induced loading might diminish for the fatigue-prone structural details below the still water level, in particular.
4.3.3 Corrosion considerations in the structural design
For effective asset management, it is imperative to have adequate models to predict corrosion severity in terms of pit depth and corrosion loss (Melchers, 2019). The knowledge acquired regarding corrosion degradation and corrosion-induced failure mechanisms for ship structures, offshore structures, and pipelines is almost transferable for the new generation of offshore green hydrogen production structures as well as offshore hydrogen storage and transportation. In this context, Melchers (2019) recently gave a comprehensive review of the development of corrosion models for marine structures.
The nonlinear corrosion model presented by Garbatov and Guedes Soares (2019) accounts for the loss of corrosion protection or coating, which can also be quite useful for offshore wind support structures. Moreover, the model also includes some influential environmental factors such as humidity, chlorides, and temperature. Alternatively, a very realistic corrosion model is the model introduced by Melchers (2018) explaining the multi-phase nature of long-term corrosion development. On the other hand, it is a widely accepted design assumption that uniform corrosion degradation is approximately 0.1 mm yr−1 for steel in a marine environment (DNV GL, 2016; Moan, 2018).
To be able to study the effect of corrosion, corrosion degradation needs to be modelled using probabilistic methods such as the random field model (Silva et al., 2013; Shojai et al., 2022) because there can be a large scatter in corrosion rates even within the same corrosion zone, especially in the splash zone and tidal zone as reported by Pakenham et al. (2021).
Momber (2011) pointed out that the corrosion degradation coupled with a cyclic load (corrosion fatigue) and constant load (stress corrosion cracking) was the most significant threat to the integrity of offshore wind structures, especially for the internal part of many legacy monopiles that were designed not to have any coating protection as reported by Hilbert et al. (2011).
4.3.4 Corrosion-induced failure mechanisms
Regarding corrosion, corrosion protection, and control for the offshore wind industry, there is a lack of guidance as the development of current standards has relied very much on the experience in the offshore O&G industry, as also claimed by both Duguid (2017) and Black et al. (2015). This highlights the importance of a good understanding of corrosion degradation, corrosion-related failure mechanisms, and control/mitigation strategies.
In addition to negatively affecting other failure mechanisms (Adedipe et al., 2017; Feng et al., 2020), corrosion can be the origin point of a structural-integrity issue, which can occur in two distinct manners. These are corrosion pitting or a slip band under cyclic load and stress corrosion cracking under sustained tensile stress, which was deemed a severe threat to the structural integrity by Momber (2011) for offshore wind structures lacking necessary corrosion protection. In this regard, Nøhr-Nielsen (2018) identified the main concerns for the internal side of the substructure as stress corrosion cracking, hydrogen-induced stress cracking, and microbiologically influenced corrosion around the mud zone, whereas for the external side, the durability of the coating, clashing with support vessels, distance to the anodes, and high current demand were deemed to be the primary concerns.
4.4 Risk-based approaches
The structural integrity of offshore structures (O&G and offshore wind) has been discussed in multiple studies such as Amirafshari et al. (2021), Fajuyigbe and Brennan (2021), and Yeter and Garbatov (2022). These reviews demonstrated a general framework for estimating the remaining life based on the reviewed technical papers. These studies primarily overlapped in describing the best practice in the structural-integrity assessment. However, while Amirafshari et al. (2021) gave more emphasis to the design and inspection-planning optimisation, Fajuyigbe and Brennan (2021) put more effort into the flaw acceptability assessment and sensitivity of the failure mechanism related to the crack depth to thickness ratio and Yeter and Garbatov (2022) focused more on the retardation effect and probabilistic structural-integrity assessment. This section attempts to compile best practices regarding the fitness-for-purpose assessment for offshore steel structures.
4.4.1 Reliability-based design, inspection, and maintenance
The probabilistic structural assessments concerning critical failure mechanisms are necessary to define the probability of failure and the failure consequence thoroughly so that an accurate risk-based assessment can be performed. In this regard, structural reliability methods can be used to incorporate the most relevant uncertainties as stochastic variables into mathematical models developed to perform the structural assessments, and the probability of failure can be calculated.
Wang et al. (2022) gave a very extensive review of the reliability analysis for OWT support structures by quantitative probabilistic methods (first-order reliability method, FORM; second-order reliability method, SORM; and a Monte Carlo simulation with enhanced sampling methods). The review argued that a reliability analysis had been an integral part of the design, code calibration, multi-hazard analysis, monitoring-based updating, and inspection planning for offshore wind support structures.
In addition to these quantitative probabilistic methods, Leimeister and Kolios (2018) reviewed the qualitative methods applied in the offshore wind industry. They identified some of the challenges with reliability methods, such as dynamic system characteristics, nonlinearities, and site-specific environmental conditions leading to higher uncertainties, data confidentiality, and computational effort. The increasing need for reliability-based analyses to evaluate the structural performance accounting for uncertainties was also acknowledged by Shittu et al. (2021). For complex and highly nonlinear structural problems such as fracture-mechanics-based structural-integrity assessment, Shittu et al. (2021) suggested combinational approximation methods (e.g. multi-layer artificial neutral networks and FORM) can offer an effective solution for complex, nonlinear, and time-dependent structural problems such as probabilistic fracture-mechanics-based structural integrity. An example of such an application was reported by Shittu et al. (2020). More details on the machine-learning-based methods in structural reliability analysis can be found in Saraygord Afshari et al. (2022).
4.4.2 Risk-based damage-tolerant framework
A reliability-based approach offers an efficient tool to assess the structural integrity of offshore structures in a probabilistic manner, which can be updated by available information obtained by in-service inspections so that necessary actions (maintenance and repair) may be planned. The inspection capability can be characterised by the probability of detection with a given confidence level (Brennan, 2013). This is because inspection quality and success depend greatly on inspectors' experience, the fidelity of nondestructive inspection technologies employed, environmental conditions, accessibility, etc.
The probability of failure and cost associated with the action to determine the optimal time to conduct an inspection, maintenance, or repair are important elements of a damage-tolerant design philosophy. The overall life-cycle cost is targeted to be minimised by developing an optimal inspection and maintenance plan. The risk-based inspection and maintenance planning for offshore wind structures has been addressed in several studies (Nielsen and Sørensen, 2021; Shafiee and Sørensen, 2019; Sørensen, 2012; Nielsen and Sørensen, 2011; Yeter et al., 2020; Thöns, 2018). Such a framework can be adopted in a more holistic approach where the damage-tolerant design principles can be adopted from the design stage (Yeter et al., 2019; Thöns et al., 2013; Frangopol, 2011). This is even more so for integrated offshore wind to green hydrogen systems because any damage occurring in the support structure or hydrogen unit may cause a significant monetary and/or safety consequence.
4.5 Digitalisation potential
4.5.1 Digital-twin applications for offshore support structures
The concept of condition-based maintenance combined with structural health monitoring (SHM) systems, artificial intelligence (AI), and autonomous sensing has a vast potential within a damage-tolerant design and structural-integrity framework. AI-based big-data analytics offer damage detection and identification by means of pattern recognition for operators to decide which measures need to be taken and when to act to alleviate safety concerns and open opportunities for damage-tolerant design and operation.
Moreover, structural health monitoring data can be integrated with a physics-based or data-driven model of the physical asset, e.g. a finite-element model in the context of structural-integrity assessment. Through this integration, the counterpart of the physical asset in a digital world, i.e. the digital twin, can be developed. The digital twin has been an active research area in recent years, with various definitions given in the literature to clarify the underlying concept (VanDerHorn and Mahadevan, 2021; Tuegel et al., 2011).
In essence, a digital twin would contain the same structural conditions of the physical structures in real time (i.e. structural configuration, detailed scantling, material property, macro and micro degradation) and can exhibit the same structural response and damage under a given scenario. Twinning would be a process of reducing the uncertainty between the physical structures and their digital counterpart. This is achieved by updating the digital counterpart using real-time monitoring data, which effectively removes the modelling assumptions. However, Liu et al. (2021) indicated that a digital twin is not a specific technology but a concept that can be implemented with many different advanced technologies with different levels of sophistication, as categorised by Wagg et al. (2020).
In comparison with conventional structural health monitoring in which damage detection may be confined to a well-recognised pattern, the digital-twin concept can be better suited to structural failure with an unknown mechanism, which may be critical for novel applications such as offshore hydrogen production. Additionally, the capability of providing structure-wide understanding enables comprehensive health condition diagnostics and prognostics for both monitored and unmonitored structural details. This offers great advantages in the application of risk-based inspection planning for offshore structures. A key aspect of a successful risk-based inspection approach is an accurate and timely recording of the asset condition so that this information can be used effectively to make decisions about how to utilise the available inspection and maintenance resources.
Whilst the development of digital twins is centred around structural-integrity management, there will be an impact on the structural design at the initial stage because of an improved understanding of structural-integrity management. Within the context of the design of offshore floating structures, the primary aim of a digital twin is to reduce risk and uncertainties by incorporating component/subsystem data and, where possible, shorten the testing and validation phase for the entire system based on the assumed reduction in uncertainty (Wagg et al., 2020). Moreover, Salvino and Collette (2009) suggested that the monitoring of the real-time response and digital-twin-based health condition can assure innovative design. It would be reasonable to consider that a relaxation of partial safety factors removes unnecessary structural redundancy, leading to a more cost-effective structural design. It is also worth noting that the standardisation of monitoring is also highly relevant, as indicated by Chen et al. (2021).
Different sensors would have different specifications such as the measurement range, sampling rate, uncertainty tolerance, and size. In an uncontrolled environment, such as offshore, the data are subjected to a great deal of noise. Dedicated data quality assurance is, therefore, necessary to derisk the offshore application. In addition, prior to training supervised and unsupervised machine learning models, big data must be cleansed of noise and outliers using digital signal-processing techniques. Currently, no guidance is available for the specification of monitoring units applied to digital-twin-based structural-integrity management.
4.5.2 Artificial-intelligence-aided structural asset management
From the standpoint of offshore wind, there is a vast body of literature on big-data collection and analysis for SHM systems, damage identification, signal processing, and machine learning. Martinez-Luengo et al. (2016) claimed that supervised and unsupervised machine learning techniques are effective not only for pattern recognition and outlier detection (diagnostics) but also for building predictive (prognostic) models once noisy data are treated appropriately.
In addition to machine learning algorithms, Antoniadou et al. (2015) showed that advanced signal-processing techniques can be used for vibration-based analysis for feature extraction, feature selection, dimensionality reduction, and pattern recognition. Some recommended methods to clean the noisy data are Gaussian filtering, median filtering, principal component analysis, short-long fast Fourier transformation, spectrogram, and least-square averages, whilst nonparametric statistical analysis can be employed to confirm the appropriateness of the SHM data preprocessing (Yeter et al., 2021).
The effort combining various monitoring techniques, advanced signal-processing methods, and machine learning algorithms is also acknowledged in Stetco et al. (2019). Jiménez et al. (2018, 2019) reported a good example of combining machine learning techniques with the wavelet transformation to detect and diagnose the delamination of the blade structure. Provided that the sensors are optimally placed (Liu et al., 2018), structural performance can be explained based on the acceleration responses (Gomez et al., 2013) as a result of the successful training of operational data.
The development of such complex systems is in its infancy, and there is so much room for improvement. Furthermore, the long-term economic implications of using AI-aided structural health monitoring systems have yet to be studied thoroughly.
5.1 Main knowledge gaps
This review considers that offshore wind is currently the most promising technology for offshore green hydrogen production systems. However, unlike the current shallow-water monopile installations, hydrogen systems are more likely to be deployed in relatively remote deep-water locations, and these barges and semi-submersible floaters seem to be more interesting alternatives due to their inherent available space that could accommodate the hydrogen process system equipment. Current design practice and guidance for offshore wind (electrical) energy systems are not necessarily applicable to offshore hydrogen systems. For example, the characteristic that the larger the turbine rating, the lower the LCoE for offshore wind may not hold for LCoH2. Lower but less variable power inputs seem more desirable for electrolyser systems. Indeed, recent studies indicate that dedicated hydrogen production systems are attractive over systems that only produce hydrogen from surplus electricity. Berg et al. (2021) reported that exploiting excess energy from wind farms to produce hydrogen is not cost-competitive. Moreover, according to Bonacina et al. (2022) and Dinh et al. (2021), dedicated offshore hydrogen systems could fully exploit offshore wind potential because they can be installed at any appropriate location and without the need to connect to a power grid. Mehta et al. (2022) suggested that differentiated LCoH2-optimised turbines design may provide an advantage over LCoE-optimised turbines in the future.
In terms of the overall configuration, despite the available literature on typologies, necessary equipment, and costs, no studies addressing the best type of floating support platforms or required adaptations on the internal arrangement of the hull and decks have been found. Hydrogen facilities also represent an increase in the payload and, likely, in the total weight of the platform, thus modifying its centre of gravity and inertia, consequently, also stability and sea-keeping and station-keeping characteristics. Furthermore, operational performance criteria imposed by the hydrogen production and storage equipment could be more restrictive than those of the wind turbine alone. Regarding the construction and assembly, to minimise operations at sea (e.g. heavy lift), it would be desirable to install wind turbines and hydrogen equipment before the deployment at sea. For a centralised typology, minor modifications would take place on the each of the support platforms of the wind turbines, but a new (hub) support structure would be required for the hydrogen facilities and the electrical substation where the electricity from all the platforms is to be gathered. No studies concerning this floating hub and its particularities have been found.
The operations and maintenance strategy will also affect the design of the support structure; i.e. if the facilities are to be occupied, stricter requirements will be applied regarding stability, safety, and human exposure to motion, with respect to a typical offshore wind turbine that is usually considered an unoccupied system. However, even if considered unoccupied, human exposure limits should be satisfied during maintenance activities (Scheu et al., 2018) and need to be further investigated along with access systems.
Although most recent studies refer only to hydrogen in either a compressed or a liquified form, the choice of the hydrogen energy carrier should not be overlooked. Ammonia, methane, methanol, or other synthetic energy carriers can be produced from offshore hydrogen. Ammonia, methane, and methanol, for example, have advantages regarding the maturity of the production technology, the availability and affordability of transportation and storage facilities, and potential markets for industrial applications (among others, nitrogen fertilisers; manufacturing of chemicals, plastics, and textiles; mining industry; pharmaceuticals; refrigeration; waste treatment; air treatment). Ammonia is also being proposed as a carbon-free fuel for the maritime transportation industry (Hasan et al., 2021; IRENA and AEA, 2022). Therefore, if alternative energy carriers are to be considered, the necessary facilities and their operational limitations should be accounted for in the design of offshore hydrogen systems.
Structural and materials-related challenges due to the loads imposed by the hydrogen production and storage facilities on the support platform should also be carefully assessed, especially regarding compartments subjected to high-pressure or cryogenic temperature, sloshing impacts due to liquid motions inside tanks and compartments, corrosion, and other factors.
The offshore wind industry has adopted some of the standards, recommended practices, techniques, and numerical tools for load and resistance analysis developed for the O&G industry, which has been beneficial but potentially limiting. This previous know-how has allowed for substantial growth and significant cost reduction but has also resulted in knowledge gaps and misconceptions regarding offshore wind structures' design and asset management.
Given that offshore wind farms considered for hydrogen production are likely to be located in sites further offshore, with higher wind energy potential, harsher conditions are likely to be encountered, leading to higher loads. Sea states with higher wave heights can also affect the ultimate load limit state, for which the definition of design load cases becomes essential. In this regard, for the uncertainty analysis of fatigue and ultimate loads, the partial safety factors used need to be revised because the risk associated with the offshore structure to produce or store hydrogen may be more significant than for an “unoccupied” offshore wind structure.
Both fatigue and ultimate strength analyses rely heavily on the accurate definition of sea states and their statistical nature. The offshore and shipping industry has come a long way regarding environmental load statistics and predictions using state-of-the-art remote sensing instruments such as satellites and lidar (laser imaging, detection, and ranging), as well as deep learning methods. However, the industry is still in its infancy in terms of understanding the effects of climate change on short- and long-term wave and wind statistics. Moreover, more caution is needed when dealing with structural response under abnormal environmental conditions, storms, rouge waves, and extreme wind gusts, which might have not only short-term effects such as plastic deformation and early crack initiation but also long-term effects on the remaining fatigue life of an offshore structure.
Since the risk for offshore hydrogen systems is more significant than for conventional offshore wind structures, uncertainty analyses of fatigue and ultimate loads are much needed to update design safety factors. The power production load cases constitute a challenging engineering problem since when the energy production is at its peak, the risk of structural stress getting near the permissible design level increases. When the structure is subjected to its limit load, it is exposed to either tension failure or buckling or both – an elastic structural analysis does not fully explain the structural behaviour under extreme loads. Such specific events should be part of design load cases and dealt with one-way coupled (sequential) simulations.
There is substantial room for improvement in multi-physics code development integrating fully coupled aero-hydro-servo-elastic simulations with detailed structural response analysis for design optimisation. Such code developments require very reliable wind turbine data and floaters design, whose development is more diverse, and changes happen more rapidly. The remedy for such a challenge is the collaboration involving partners from academia, research institutes, classification societies, and industry.
Last but not least, digital twins are expected to pave the way for innovative structural designs and structural-integrity management incorporating the latest development in structural engineering (i.e. advanced structural configuration), material science (i.e. novel materials), manufacturing capability (i.e. 3D printing, additive manufacturing), or fulfilling the requirement of new operations. Likewise, mitigation of the production of a substandard design can be provided by the application of digital twins and its diagnostic and prognostic capabilities to increase the transparency of the consumed fatigue life and cumulative damage of critical structural locations. Preventive actions can then be taken to avoid catastrophic failure.
5.2 SWOT analysis: challenges and opportunities
Based on the above discussion, a SWOT (strength, weakness, opportunity, and threat) analysis for offshore green hydrogen systems has been performed and summarised in Table 1. Most of the challenges experienced by other offshore industries are likely to be experienced by offshore hydrogen systems. Moreover, incorporating novel technologies or using reliable technologies in new environments should bring even more challenges. Nevertheless, it is only reasonable to argue that ever-increasing computational power (cloud-based), digitalisation (SHM, digital twin), and strong AI (supervised and unsupervised machine learning) present themselves as opportunities to deal with these emerging challenges, which were not available in the past.
A comprehensive review of offshore green hydrogen systems has been conducted from the perspective of offshore structures and the applicability of recent developments in methods and tools available to support the design of these new structures. The present literature review provides a critical assessment of the knowledge gaps, challenges, and opportunities, complemented by a SWOT analysis for offshore support structures for green hydrogen systems. The main conclusions are as follows.
-
Distinct from offshore wind electricity generation, hydrogen systems require additional areas and volumes within support platforms including the onboard complex power management of energy production and consumption, fulfilling different stability and sea-keeping and station-keeping limitations, and complying with potentially stricter requirements imposed by the additional equipment.
-
The knowledge and experience of the offshore O&G and offshore wind industries can be adapted and modified for the development of reliable and resilient offshore green hydrogen structures.
-
As an alternative to prescriptive offshore design standards, case-specific standards can offer flexibility in dealing with structural design technical challenges and asset management of offshore structures, especially those at a low TRL, such as emerging green hydrogen production, storage, and transportation technologies.
-
Offshore-wind-powered green hydrogen production is expected situated in areas with high wind energy potential, which inevitably leads to a higher environmental load for both FLS and ULS.
-
Research needs to focus on the definition of relevant design load cases of projected wind and wave statistics, both in the short and long term, taking into account climate change and the dynamic behaviour of floating structures under harsher sea states and corresponding nonlinear structural response.
-
The time-domain load analysis and fatigue damage assessment are inherently heavily reliant upon high-fidelity simulations for the floating support structure, which increases the time required for design optimisation. Nevertheless, the spectral method, with the aid of machine learning, might provide a useful alternative for design optimisation.
-
New materials, AI, and digital twins with diagnostic and prognostic capabilities offer a significant opportunity to be more flexible in terms of design standards and regulations, which can clear the way for innovative structural designs and operation and maintenance strategies, leading to a safe, sustainable, and value-adding life cycle of offshore support structures.
-
Given the complex scenario for the design, construction, installation, operation, and maintenance of the hydrogen systems as a whole, i.e. not only the support structure and the hydrogen facilities but also the subsea equipment, the consideration of unoccupied operation should be carefully considered as this can be critical for the achievement of cost-competitive LCoH2 and a safe, responsible sector.
ABS | American Bureau of Shipping |
AC/DC | Alternating current/direct current |
AEL | Alkaline electrolysis |
AI | Artificial intelligence |
API | American Petroleum Institute |
CAPEX | Capital expenditure |
CH2 | Compressed hydrogen |
DNV | Det Norske Veritas |
Diameter-to-thickness ratio | |
EUR per kilogram of H2 | Euro per kilogram of hydrogen |
FLS | Fatigue limit state |
FORM | First-order reliability method |
GFRP | Glass-fibre-reinforced polymer |
GW | Gigawatt |
HAZOP | Hazard and operability |
IEC | International Electrotechnical Commission |
kW | Kilowatt |
kW m−2 | Kilowatt per square metre |
kW m−3 | Kilowatt per cubic metre |
LCoE | Levelised cost of energy |
LCoH2 | Levelised cost of hydrogen |
LH2 | Liquefied hydrogen |
Lidar | Laser imaging, detection, and ranging |
LOHC | Liquid organic hydrogen carrier |
MBR | Minimum bending radius |
mm yr−1 | Millimetre per year |
MW | Megawatt |
O&G | Oil and gas |
OPEX | Operational expenditure |
OTEC | Ocean thermal energy conversion |
OWT | Offshore wind turbine |
PEM | Proton exchange membrane |
SHM | Structural health monitoring |
SLS | Serviceability limit state |
SORM | Second-order reliability method |
SWOT | Strength, weakness, opportunity, and threat |
TLP | Tension leg platform |
TRL | Technology readiness level |
ULS | Ultimate limit state |
USD per kilogram of H2 | United States dollar per kilogram of hydrogen |
No data sets were used in this article.
CARC, BY, and SL: conceptualisation, data curation, formal analysis, investigation, writing (original draft preparation), writing (review and editing). MC and FB: conceptualisation, funding acquisition, project administration, resources, supervision, writing (review and editing).
At least one of the (co-)authors is a member of the editorial board of Wind Energy Science. The peer-review process was guided by an independent editor, and the authors also have no other competing interests to declare.
Publisher’s note: Copernicus Publications remains neutral with regard to jurisdictional claims made in the text, published maps, institutional affiliations, or any other geographical representation in this paper. While Copernicus Publications makes every effort to include appropriate place names, the final responsibility lies with the authors.
This work was funded by the UK Engineering and Physical Sciences Research Council (EPSRC) as part of the Ocean-REFuel (Ocean Renewable Energy Fuels) programme grant (no. EP/W005212/1) awarded to the University of Strathclyde, Newcastle University, the University of Nottingham, Cardiff University, and Imperial College London.
This research has been supported by the Engineering and Physical Sciences Research Council [grant no. EP/W005212/1].
This paper was edited by Alessandro Bianchini and reviewed by Laura Serri and one anonymous referee.
12toZero: HyFloat patented design combines buoyancy & storage in one foundation for the most reliable & cost-effective floating hydrogen supply: https://www.12tozero.com/why-hyfloat/, last access: 20 Dezember 2023.
ABS: Guide for Fatigue Assessment Of Offshore Structures, American Bureau of Shipping, https://ww2.eagle.org/en/rules-and-resources/rules-and-guides.html?q=offshore (last access: 20 September 2022), 2020.
Adedipe, O., Brennan, F., Mehmanparast, A., Kolios, A., and Tavares, I.: Corrosion fatigue crack growth mechanisms in offshore monopile steel weldments, Fatigue Fract. Eng. M., 40, 1868–1881, https://doi.org/10.1111/ffe.12606, 2017.
Alexander, W.: A Low Specific Mass, Free Floating Wind Energy Concept up to 40 MW, Proceedings of the ASME 2019 2nd International Offshore Wind Technical Conference, ASME 2019 2nd International Offshore Wind Technical Conference, St. Julian’s, Malta, 3–6 November 2019, V001T01A015, ASME, https://doi.org/10.1115/IOWTC2019-7590, 2019.
Amirafshari, P., Brennan, F., and Kolios, A.: A fracture mechanics framework for optimising design and inspection of offshore wind turbine support structures against fatigue failure, Wind Energ. Sci., 6, 677–699, https://doi.org/10.5194/wes-6-677-2021, 2021.
Antoniadou, I., Dervilis, N., Papatheou, E., Maguire, A. E., and Worden, K.: Aspects of structural health and condition monitoring of offshore wind turbines, Philos. T. R. Soc. A, 373, 2014.0075, 2015.
API: Recommended Practice for Planning, Designing and Constructing Fixed Offshore Platforms – Load and Resistance Factor Design (API RP 2ALRFD), https://www.api.org/products-and-services/standards/digital-catalog (last access: 4 March 2024), 2019.
Apostolou, D. and Enevoldsen, P.: The past, present and potential of hydrogen as a multifunctional storage application for wind power, Renewable and Sustainable Energy Reviews, 112, 917–929, https://doi.org/10.1016/j.rser.2019.06.049, 2019.
Arany, L., Bhattacharya, S., Macdonald, J., and Hogan, S.: Accuracy of frequency domain fatigue damage estimation methods for offshore wind turbine support structures, in: Vulnerability, Uncertainty, and Risk: Quantification, Mitigation, and Management, 1293–1302, https://doi.org/10.1061/9780784413609.130, 2014.
Asim, T., Islam, S. Z., Hemmati, A., and Khalid, M. S. U.: A Review of Recent Advancements in Offshore Wind Turbine Technology, Energies, 15, 579, https://doi.org/10.3390/en15020579, 2022.
Babarit, A., Gilloteaux, J.-C., Clodic, G., Duchet, M., Simoneau, A., and Platzer, M. F.: Techno-economic feasibility of fleets of far offshore hydrogen-producing wind energy converters, Int. J. Hydrogen Energ., 43, 7266–7289, https://doi.org/10.1016/j.ijhydene.2018.02.144, 2018.
Babarit, A., Body, E., Gilloteaux, J.-C., and Hétet, J.-F.: Energy and economic performance of the FARWIND energy system for sustainable fuel production from the far-offshore wind energy resource, 2019 Fourteenth International Conference on Ecological Vehicles and Renewable Energies (EVER), Monte-Carlo, Monaco, 1–10, https://doi.org/10.1109/EVER.2019.8813563, 2019.
Bashetty, S. and Ozcelik, S.: Review on Dynamics of Offshore Floating Wind Turbine Platforms, Energies, 14, 6026, https://doi.org/10.3390/en14196026, 2021.
Berg, T. L., Apostolou, D., and Enevoldsen, P.: Analysis of the wind energy market in Denmark and future interactions with an emerging hydrogen market, Int. J. Hydrogen Energ., 46, 146–156, https://doi.org/10.1016/j.ijhydene.2020.09.166, 2021.
Birol, F.: The future of hydrogen: seizing today's opportunities, IEA Report prepared for the G20, https://www.iea.org/reports/the-future-of-hydrogen (last access: 4 March 2024), 2019.
Black, A. R., Mathiesen, T., and Hilbert, L. R.: Corrosion protection of offshore wind foundations, NACE International, Houston, TX, USA, ISBN 5896 2015 CP, https://store.ampp.org/corrosion-protection-of-offshore-wind-foundations (last access: 4 March 2024), 2015.
Blanco-Fernández, P. and Pérez-Arribas, F.: Offshore Facilities to Produce Hydrogen, Energies, 10, 1–14, https://doi.org/10.3390/en10060783, 2017.
Bonacina, C. N., Gaskare, N. B., and Valenti, G.: Assessment of offshore liquid hydrogen production from wind power for ship refueling, Int. J. Hydrogen Energ., 47, 1279–1291, https://doi.org/10.1016/j.ijhydene.2021.10.043, 2022.
Boscaino, V., Cipriani, G., Curto, D., Di Dio, V., Franzitta, V., Trapanese, M., and Viola, A.: A small scale prototype of a wave energy conversion system for hydrogen production, IECON 2015 – 41st Annual Conference of the IEEE Industrial Electronics Society, 9–12 November 2015, 003591-003596, https://doi.org/10.1109/IECON.2015.7392658, 2015.
Brennan, F.: Risk Based Maintenance for Offshore Wind Structures, Proc. CIRP, 11, 296–300, https://doi.org/10.1016/j.procir.2013.07.021, 2013.
Buttler, A. and Spliethoff, H.: Current status of water electrolysis for energy storage, grid balancing and sector coupling via power-to-gas and power-to-liquids: A review, Renewable and Sustainable Energy Reviews, 82, 2440–2454, https://doi.org/10.1016/j.rser.2017.09.003, 2018.
Caglayan, D. G., Heinrichs, H. U., Linssen, J., Robinius, M., and Stolten, D.: Impact of different weather years on the design of hydrogen supply pathways for transport needs, Int. J. Hydrogen Energ., 44, 25442–25456, https://doi.org/10.1016/j.ijhydene.2019.08.032, 2019.
Caine, D., Wahyuni, W., Pizii, B., Iliffe, M., Whitlock, Z., Ryan, B., and Bond, L.: ERM Dolphyn Hydrogen: Phase 2 – Final Report, Environmental Resources Management (ERM), 106, https://assets.publishing.service.gov.uk/media/61f953e08fa8f53894502152/Phase_2_Report_-_ERM_-_Dolphyn.pdf (last access: 4 March 2024), 2021.
Chen, B., Soares, C. G., and Videiro, P.: Review of digital twin of ships and offshore structures, in: Developments in Maritime Technology and Engineering, CRC Press, 445–451, https://doi.org/10.1201/9781003216582-50, 2021.
Clodic, G., Babarit, A., and Gilloteaux, J.-C.: Wind propulsion options for energy ships, Proceedings of the ASME 2018 1st International Offshore Wind Technical Conference, ASME 2018 1st International Offshore Wind Technical Conference, San Francisco, California, USA, 4–7 November 2018, V001T01A002, ASME, https://doi.org/10.1115/IOWTC2018-1056, 2018.
Colucci, A., Boscaino, V., Cipriani, G., Curto, D., Di Dio, V., Franzitta, V., Trapanese, M., and Viola, A.: An inertial system for the production of electricity and hydrogen from sea wave energy, OCEANS 2015 – MTS/IEEE Washington, 19–22 October 2015, 1–10, https://doi.org/10.23919/OCEANS.2015.7404569, 2015.
d'Amore-Domenech, R. and Leo, T. J.: Sustainable Hydrogen Production from Offshore Marine Renewable Farms: Techno-Energetic Insight on Seawater Electrolysis Technologies, ACS Sustain. Chem. Eng., 7, 8006–8022, https://doi.org/10.1021/acssuschemeng.8b06779, 2019.
d'Amore-Domenech, R., Santiago, Ó., and Leo, T. J.: Multicriteria analysis of seawater electrolysis technologies for green hydrogen production at sea, Renewable and Sustainable Energy Reviews, 133, 110166, https://doi.org/10.1016/j.rser.2020.110166, 2020.
d'Amore-Domenech, R., Leo, T. J., and Pollet, B. G.: Bulk power transmission at sea: Life cycle cost comparison of electricity and hydrogen as energy vectors, Appl. Energ., 288, 116625, https://doi.org/10.1016/j.apenergy.2021.116625, 2021.
Dinh, V. N., Leahy, P., McKeogh, E., Murphy, J., and Cummins, V.: Development of a viability assessment model for hydrogen production from dedicated offshore wind farms, Int. J. Hydrogen Energ., 46, 24620–24631, https://doi.org/10.1016/j.ijhydene.2020.04.232, 2021.
Dirlik, T. and Benasciutti, D.: Dirlik and Tovo-Benasciutti Spectral Methods in Vibration Fatigue: A Review with a Historical Perspective, Metals, 11, 1333, https://doi.org/10.3390/met11091333, 2021.
DNV: RP-C203: Fatigue design of offshore steel structures, https://www.dnv.com/oilgas/download/dnv-rp-c203-fatigue-design-of-offshore-steel-structures.html (last access: 4 March 2024), 2014.
DNV: Hydrogen Forecast to 2050: Energy Transition Outlook 2022, Det Norske Veritas®, 114, https://www.dnv.com/focus-areas/hydrogen/forecast-to-2050.html (last access: 4 March 2024), 2022.
DNV GL: DNVGL-RP-0416 Corrosion protection for wind turbines, recommended practice, https://www.dnv.com/energy/standards-guidelines/dnv-rp-0416-corrosion-protection-for-wind-turbines.html (last access: 4 March 2024), 2016.
Dong, W. B., Moan, T., and Gao, Z.: Long-term fatigue analysis of multi-planar tubular joints for jacket-type offshore wind turbine in time domain, Eng. Struct., 33, 2002–2014, https://doi.org/10.1016/j.engstruct.2011.02.037, 2011.
Dugger, G. and Francis, E.: Design of an ocean thermal energy plant ship to produce ammonia via hydrogen, Int. J. Hydrogen Energ., 2, 231–249, 1977.
Duguid, L.: Offshore Wind Farm Substructure Monitoring And Inspection, PN000205-LRT-001, https://ore.catapult.org.uk/wp-content/uploads/2018/01/Offshore-wind-farm-substructure-monitoring-and-inspection-report-.pdf (last access: 4 March 2024), 2017.
Dutton, A.: The Hydrogen Economy and Carbon Abatement–Implications and Challenges for Wind Energy, Wind Engineering, 27, 239–256, 2003.
Fajuyigbe, A. and Brennan, F.: Fitness-for-purpose assessment of cracked offshore wind turbine monopile, Mar. Struct., 77, 102965, https://doi.org/10.1016/j.marstruc.2021.102965, 2021.
Fan, T.-Y., Lin, C.-Y., Huang, C.-C., and Chu, T.-L.: Time-Domain Fatigue Analysis of Multi-planar Tubular Joints for a Jacket-Type Substructure of Offshore Wind Turbines, Int. J. Offshore Polar, 30, 112–119, https://doi.org/10.17736/ijope.2020.jc762, 2020.
Feng, L., He, J., Hu, L., Shi, H., Yu, C., Wang, S., and Yang, S.: A parametric study on effects of pitting corrosion on steel plate's ultimate strength, Appl. Ocean Res., 95, 102026, https://doi.org/10.1016/j.apor.2019.102026, 2020.
Franco, B. A., Baptista, P., Neto, R. C., and Ganilha, S.: Assessment of offloading pathways for wind-powered offshore hydrogen production: Energy and economic analysis, Appl. Energ., 286, 116553, https://doi.org/10.1016/j.apenergy.2021.116553, 2021.
Frangopol, D. M.: Life-cycle performance, management, and optimisation of structural systems under uncertainty: accomplishments and challenges 1, Struct. Infrastruct. E., 7, 389–413, https://doi.org/10.1080/15732471003594427, 2011.
Garbatov, Y. and Guedes Soares, C.: Spatial Corrosion Wastage Modeling of Steel Plates Exposed to Marine Environments, J. Offshore Mech. Arct., 141, 031602, https://doi.org/10.1115/1.4041991, 2019.
Gilloteaux, J.-C. and Babarit, A.: Preliminary Design of a Wind Driven Vessel Dedicated to Hydrogen Production, Proceedings of the ASME 2017 36th International Conference on Ocean, Offshore and Arctic Engineering, Volume 10: Ocean Renewable Energy, Trondheim, Norway, 25–30 June 2017, V010T09A065, ASME, https://doi.org/10.1115/OMAE2017-6140, 2017.
Gomez, H. C., Gur, T., and Dolan, D.: Structural condition assessment of offshore wind turbine monopile foundations using vibration monitoring data, Proc. SPIE 8694, Nondestructive Characterization for Composite Materials, Aerospace Engineering, Civil Infrastructure, and Homeland Security 2013, 86940B, 11 April 2013, https://doi.org/10.1117/12.2018263, 2013.
Guo, L., Yang, S., and Jiao, H.: Behavior of thin-walled circular hollow section tubes subjected to bending, Thin Wall. Struct., 73, 281–289, https://doi.org/10.1016/j.tws.2013.08.014, 2013.
Haid, L., Stewart, G., Jonkman, J., Robertson, A., Lackner, M., and Matha, D.: Simulation-length requirements in the loads analysis of offshore floating wind turbines, Proceedings of the ASME 2013 32nd International Conference on Ocean, Offshore and Arctic Engineering, Volume 8: Ocean Renewable Energy, Nantes, France, 9–14 June 2013, V008T09A091, ASME, https://doi.org/10.1115/OMAE2013-11397, 2013.
Hameed, H., Sun, G., and Bai, Y.: An Overview of Risk-Based Inspection Planning for Flexible Pipeline, Proceedings of the ASME 2018 37th International Conference on Ocean, Offshore and Arctic Engineering, Volume 5: Pipelines, Risers, and Subsea Systems, Madrid, Spain, 17–22 June 2018, V005T04A028, ASME, https://doi.org/10.1115/OMAE2018-78563, 2018.
Hasan, M. H., Mahlia, T. M. I., Mofijur, M., Rizwanul Fattah, I., Handayani, F., Ong, H. C., and Silitonga, A.: A comprehensive review on the recent development of ammonia as a renewable energy carrier, Energies, 14, 3732, https://doi.org/10.3390/en14133732, 2021.
Henry, A., McCallum, C., McStay, D., Rooney, D., Robertson, P., and Foley, A.: Analysis of wind to hydrogen production and carbon capture utilisation and storage systems for novel production of chemical energy carriers, J. Clean. Prod., 354, 131695, https://doi.org/10.1016/j.jclepro.2022.131695, 2022.
Hilbert, L. R., Black, A. R., Andersen, F., and Mathiesen, T.: Inspection and monitoring of corrosion inside monopile foundations for offshore wind turbines, Paper no: 4730, EUROCORR 2011 Conference, Stockholm, Sweden, https://eurocorr.org/2011.html, 4–8 September 2011.
Hou, P., Enevoldsen, P., Eichman, J., Hu, W., Jacobson, M. Z., and Chen, Z.: Optimizing investments in coupled offshore wind -electrolytic hydrogen storage systems in Denmark, J. Power Sources, 359, 186–197, https://doi.org/10.1016/j.jpowsour.2017.05.048, 2017.
Ibrahim, O. S., Singlitico, A., Proskovics, R., McDonagh, S., Desmond, C., and Murphy, J. D.: Dedicated large-scale floating offshore wind to hydrogen: Assessing design variables in proposed typologies, Renewable and Sustainable Energy Reviews, 160, 112310, https://doi.org/10.1016/j.rser.2022.112310, 2022.
IEC: Technical Specification IEC TS 61400-3-2: Wind energy generation systems – Part 3-2: Design requirements for floating offshore wind turbines, Ed. 1.0 2019-04, International Electrotechnical Commission (IEC), BSI Standards Limited, ISBN 978 0 580 87990 6, ICS 27.180, 2019.
Igwemezie, V., Mehmanparast, A., and Kolios, A.: Current trend in offshore wind energy sector and material requirements for fatigue resistance improvement in large wind turbine support structures – A review, Renewable and Sustainable Energy Reviews, 101, 181–196, https://doi.org/10.1016/j.rser.2018.11.002, 2019.
Ioannou, A. and Brennan, F.: A preliminary techno-economic comparison between a grid-connected and non-grid connected offshore floating wind farm, Offshore Energy and Storage Summit (OSES), Brest, France, 1–6, https://doi.org/10.1109/OSES.2019.8867350, 2019.
IRENA: Innovation outlook: Ocean energy technologies, International Renewable Energy Agency Abu Dhabi, ISBN 978-92-9260-287-1, 2020.
IRENA and AEA: Innovation Outlook: Renewable Ammonia, International Renewable Energy Agency, Abu Dhabi, Ammonia Energy Association, Brooklyn, ISBN 978-92-9260-423-3, 2022.
ITTC: The Specialist Committee on Hydrodynamic Modelling of Marine Renewable Energy Devices: Final Report and Recommendations to the 28th ITTC, https://www.ittc.info/media/7823/18-sc-hydrodynamic-testing-marine-renewables.pdf (last access: 4 March 2024), 2017.
ITTC: The Specialist Committee on Hydrodynamic Modelling of Marine Renewable Energy Devices: Final Report and Recommendations to the 29th ITTC, https://ittc.info/media/10940/volume-ii.pdf, 2021.
Jang, D., Kim, K., Kim, K.-H., and Kang, S.: Techno-economic analysis and Monte Carlo simulation for green hydrogen production using offshore wind power plant, Energ. Convers. Manage., 263, 115695, https://doi.org/10.1016/j.enconman.2022.115695, 2022.
Jepma, C., Kok, G., Renz, M., Van Schot, M., and Wouters, K.: North Sea Energy D3.6 towards sustainable energy production on the North Sea-Green hydrogen production and CO2 storage: onshore or offshore, As part of topsector energy TKI Offshore Wind & TKI New Gas, https://north-sea-energy.eu/static/fc2fba594593abe1330f8b80eeaad756/NSE1_D3.6-Towards-sustainable-energy-production-on-the-North-Sea_final-public.pdf (last access: 4 March 2024), 2018.
Jiménez, A. A., Gómez Muñoz, C. Q., and García Márquez, F. P.: Machine learning for wind turbine blades maintenance management, Energies, 11, 13, https://doi.org/10.3390/en11010013, 2018.
Jiménez, A. A., Márquez, F. P. G., Moraleda, V. B., and Muñoz, C. Q. G.: Linear and nonlinear features and machine learning for wind turbine blade ice detection and diagnosis, Renew. Energ., 132, 1034–1048, https://doi.org/10.1016/j.renene.2018.08.050, 2019.
Kassem, N.: Offshore wind farms for hydrogen production subject to uncertainties, Proceedings of the International Joint Power Generation Conference collocated with TurboExpo 2003, International Joint Power Generation Conference, Atlanta, Georgia, USA, 16–19 June 2003, 857–864, ASME, https://doi.org/10.1115/IJPGC2003-40046, 2003.
Katsikogiannis, G., Sørum, S. H., Bachynski, E. E., and Amdahl, J.: Environmental lumping for efficient fatigue assessment of large-diameter monopile wind turbines, Mar. Struct., 77, 102939, https://doi.org/10.1016/j.marstruc.2021.102939, 2021.
Katsikogiannis, G., Hegseth, J. M., and Bachynski-Poliæ, E. E.: Application of a lumping method for fatigue design of monopile-based wind turbines using fully coupled and simplified models, Appl. Ocean Res., 120, 102998, https://doi.org/10.1016/j.apor.2021.102998, 2022.
Kumar, S., Arzaghi, E., Baalisampang, T., Garaniya, V., and Abbassi, R.: Insights into decision-making for offshore green hydrogen infrastructure developments, Process Saf. Environ., 174, 805–817, https://doi.org/10.1016/j.psep.2023.04.042, 2023.
Kvittem, M. I. and Moan, T.: Time domain analysis procedures for fatigue assessment of a semi-submersible wind turbine, Mar. Struct., 40, 38–59, https://doi.org/10.1016/j.marstruc.2014.10.009, 2015.
Kvittem, M. I., Moan, T., Gao, Z., and Luan, C.: Short-Term Fatigue Analysis of Semi-Submersible Wind Turbine Tower, Proceedings of the ASME 2011 30th International Conference on Ocean, Offshore and Arctic Engineering, Volume 2, Structures, Safety and Reliability, Rotterdam, The Netherlands, 19–24 June 2011, 751–759, ASME, https://doi.org/10.1115/OMAE2011-50092, 2011.
Lee, J., Park, B., Kim, K.-H., and Ruy, W.-S.: Multi-objective optimization of liquid hydrogen FPSO at the conceptual design stage, International Int. J. Nav. Arch. Ocean, 15, 100511, https://doi.org/10.1016/j.ijnaoe.2022.100511, 2023.
Leimeister, M. and Kolios, A.: A review of reliability-based methods for risk analysis and their application in the offshore wind industry, Renewable and Sustainable Energy Reviews, 91, 1065–1076, https://doi.org/10.1016/j.rser.2018.04.004, 2018.
Leimeister, M., Kolios, A., and Collu, M.: Critical review of floating support structures for offshore wind farm deployment, J. Phys. Conf. Ser., 1104, 012007, https://doi.org/10.1088/1742-6596/1104/1/012007, 2018.
Li, S. and Kim, D. K.: Ultimate strength characteristics of unstiffened cylindrical shell in axial compression, Ocean Eng., 243, 110253, https://doi.org/10.1016/j.oceaneng.2021.110253, 2022.
Liu, K., Yan, R.-J., and Guedes Soares, C.: Optimal sensor placement and assessment for modal identification, Ocean Eng., 165, 209–220, https://doi.org/10.1016/j.oceaneng.2018.07.034, 2018.
Liu, M., Fang, S., Dong, H., and Xu, C.: Review of digital twin about concepts, technologies, and industrial applications, J. Manuf. Syst., 58, 346–361, https://doi.org/10.1016/j.jmsy.2020.06.017, 2021.
Lucas, T. R., Ferreira, A. F., Santos Pereira, R. B., and Alves, M.: Hydrogen production from the WindFloat Atlantic offshore wind farm: A techno-economic analysis, Appl. Energ., 310, 118481, https://doi.org/10.1016/j.apenergy.2021.118481, 2022.
Marino, E., Giusti, A., and Manuel, L.: Offshore wind turbine fatigue loads: The influence of alternative wave modeling for different turbulent and mean winds, Renew. Energ., 102, 157–169, 2017.
Martinez-Luengo, M., Kolios, A., and Wang, L.: Structural health monitoring of offshore wind turbines: A review through the Statistical Pattern Recognition Paradigm, Renewable and Sustainable Energy Reviews, 64, 91–105, 2016.
Mathur, J., Agarwal, N., Swaroop, R., and Shah, N.: Economics of producing hydrogen as transportation fuel using offshore wind energy systems, Energ. Policy, 36, 1212–1222, 2008.
McKenna, R., D'Andrea, M., and González, M. G.: Analysing long-term opportunities for offshore energy system integration in the Danish North Sea, Advances in Applied Energy, 4, 100067, https://doi.org/10.1016/j.adapen.2021.100067, 2021.
Mehta, M., Zaaijer, M., and von Terzi, D.: Optimum Turbine Design for Hydrogen Production from Offshore Wind, J. Phys. Conf. Ser., 042061, https://doi.org/10.1088/1742-6596/2265/4/042061, 2022.
Meier, K.: Hydrogen production with sea water electrolysis using Norwegian offshore wind energy potentials, Int. J. Energy Environ. Eng., 5, 104, https://doi.org/10.1007/s40095-014-0104-6, 2014.
Melchers, R. E.: Progress in developing realistic corrosion models, Struct. Infrastruct. E., 14, 843–853, https://doi.org/10.1080/15732479.2018.1436570, 2018.
Melchers, R. E.: Predicting long-term corrosion of metal alloys in physical infrastructure, npj Materials Degradation, 3, 4, https://doi.org/10.1038/s41529-018-0066-x, 2019.
Miao, B., Giordano, L., and Chan, S. H.: Long-distance renewable hydrogen transmission via cables and pipelines, Int. J. Hydrogen Energ., 46, 18699–18718, https://doi.org/10.1016/j.ijhydene.2021.03.067, 2021.
Miyazaki, M., Paumier, L., and Caleyron, F.: Effect of Tension on Collapse Performance of Flexible Pipes, Proceedings of the ASME 2018 37th International Conference on Ocean, Offshore and Arctic Engineering, Volume 5: Pipelines, Risers, and Subsea Systems, Madrid, Spain, 17–22 June 2018, V005T04A006, ASME, https://doi.org/10.1115/OMAE2018-77286, 2018.
Moan, T.: Life cycle structural integrity management of offshore structures, Struct. Infrastruct. E., 14, 911–927, https://doi.org/10.1080/15732479.2018.1438478, 2018.
Momber, A.: Corrosion and corrosion protection of support structures for offshore wind energy devices (OWEA), Mater. Corros., 62, 391–404, https://doi.org/10.1002/maco.201005691, 2011.
Mrsnik, M., Slavic, J., and Boltezar, M.: Frequency-domain methods for a vibration-fatigue-life estimation – Application to real data, Int. J. Fatigue, 47, 8–17, https://doi.org/10.1016/j.ijfatigue.2012.07.005, 2013.
Murahara, M. and Seki, K.: On-site sodium production with seawater electrolysis as alternative energy for oil by offshore wind power generation, 2008 IEEE Energy 2030 Conference, Atlanta, GA, USA, 1–8, https://doi.org/10.1109/ENERGY.2008.4780994, 2008.
Nielsen, J. J. and Sørensen, J. D.: On risk-based operation and maintenance of offshore wind turbine components, Reliab. Eng. Syst. Safe, 96, 218–229, 2011.
Nielsen, J. S. and Sørensen, J. D.: Risk-based derivation of target reliability levels for life extension of wind turbine structural components, Wind Energy, 24, 939–956, 2021.
Nøhr-Nielsen, L.: Corrosion Protection of Offshore Wind Power Plants, GfKORR, Gesellschaft für Korrosionsschutz, Annual Conference 2018 Bremerhaven, 6–7 November 2018, ISBN 3935406681, 2018.
Otter, A., Murphy, J., Pakrashi, V., Robertson, A., and Desmond, C.: A review of modelling techniques for floating offshore wind turbines, Wind Energy, 25, 831–857, https://doi.org/10.1002/we.2701, 2021.
Otter, A., Murphy, J., Pakrashi, V., Robertson, A., and Desmond, C.: A review of modelling techniques for floating offshore wind turbines, Wind Energy, 25, 831–857, https://doi.org/10.1002/we.2701, 2022.
Pakenham, B., Ermakova, A., and Mehmanparast, A.: A Review of Life Extension Strategies for Offshore Wind Farms Using Techno-Economic Assessments, Energies, 14, 1936, https://doi.org/10.3390/en14071936, 2021.
Patryniak, K., Collu, M., and Coraddu, A.: Multidisciplinary design analysis and optimisation frameworks for floating offshore wind turbines: State of the art, Ocean Eng., 251, 111002, https://doi.org/10.1016/j.oceaneng.2022.111002, 2022.
Patterson, B. D., Mo, F., Borgschulte, A., Hillestad, M., Joos, F., Kristiansen, T., Sunde, S., and van Bokhoven, J. A.: Renewable CO2 recycling and synthetic fuel production in a marine environment, P. Natl. Acad. Sci. USA, 116, 12212–12219, https://doi.org/10.1073/pnas.1902335116, 2019.
Pearson, H., Pearson, C., Corradi, L., and Almeida, A.: Offshore infrastructure reuse contribution to decarbonisation, SPE Offshore Europe Conference and Exhibition, Aberdeen, UK, September 2019, https://doi.org/10.2118/195772-MS, 2019.
Peters, J. L., Remmers, T., Wheeler, A. J., Murphy, J., and Cummins, V.: A systematic review and meta-analysis of GIS use to reveal trends in offshore wind energy research and offer insights on best practices, Renewable and Sustainable Energy Reviews, 128, 109916, https://doi.org/10.1016/j.rser.2020.109916, 2020.
Raut, G. and Goudarzi, N.: North Carolina Wave Energy Resource: Hydrogen Production Potential, Proceedings of the ASME 2018 Power Conference collocated with the ASME 2018 12th International Conference on Energy Sustainability and the ASME 2018 Nuclear Forum, Volume 1: Fuels, Combustion, and Material Handling, Combustion Turbines Combined Cycles, Boilers and Heat Recovery Steam Generators, Virtual Plant and Cyber-Physical Systems, Plant Development and Construction, Renewable Energy Systems, Lake Buena Vista, Florida, USA, 24–28 June 2018, V001T06A018, ASME, https://doi.org/10.1115/POWER2018-7388, 2018.
REM: Lhyfe Launches Offshore Renewable Green Hydrogen Production Pilot Site, Renewable Energy Magazine, https://www.renewableenergymagazine.com/hydrogen/lhyfe-launches-offshore-renewable-green-hydrogen-production-20220923, last access: 1 November 2022.
Rogeau, A., Vieubled, J., de Coatpont, M., Affonso Nobrega, P., Erbs, G., and Girard, R.: Techno-economic evaluation and resource assessment of hydrogen production through offshore wind farms: A European perspective, Renewable and Sustainable Energy Reviews, 187, 113699, https://doi.org/10.1016/j.rser.2023.113699, 2023.
Salvino, L. W. and Collette, M. D.: Monitoring Marine Structures, in: Encyclopedia of Structural Health Monitoring, https://doi.org/10.1002/9780470061626.shm112, 2009.
Saraygord Afshari, S., Enayatollahi, F., Xu, X., and Liang, X.: Machine learning-based methods in structural reliability analysis: A review, Reliab. Eng. Syst. Safe, 219, 108223, https://doi.org/10.1016/j.ress.2021.108223, 2022.
Scafidi, J., Wilkinson, M., Gilfillan, S. M. V., Heinemann, N., and Haszeldine, R. S.: A quantitative assessment of the hydrogen storage capacity of the UK continental shelf, Int. J. Hydrogen Energ., 46, 8629–8639, https://doi.org/10.1016/j.ijhydene.2020.12.106, 2021.
Scheu, M., Matha, D., Schwarzkopf, M.-A., and Kolios, A.: Human exposure to motion during maintenance on floating offshore wind turbines, Ocean Eng., 165, 293–306, https://doi.org/10.1016/j.oceaneng.2018.07.016, 2018.
Schmitz, M. and Madlener, R.: Economic Viability of Kite-Based Wind Energy Powerships with CAES or Hydrogen Storage, Enrgy Proced., 75, 704–715, https://doi.org/10.1016/j.egypro.2015.07.497, 2015.
Serna, A., Nonney-Rico, J. E., and Tadeo, F.: Model predictive control of hydrogen production by renewable energy, IREC2015 The Sixth International Renewable Energy Congress, Sousse, Tunisia, 2015, 1–6, https://doi.org/10.1109/IREC.2015.7110959, 2015.
Shafiee, M. and Sørensen, J. D.: Maintenance optimization and inspection planning of wind energy assets: Models, methods and strategies, Reliab. Eng. Syst. Safe, 192, 105993, https://doi.org/10.1016/j.ress.2017.10.025, 2019.
Shittu, A. A., Kolios, A., and Mehmanparast, A.: A Systematic Review of Structural Reliability Methods for Deformation and Fatigue Analysis of Offshore Jacket Structures, Metals, 11, 50, https://doi.org/10.3390/met11010050, 2021.
Shittu, A. A., Mehmanparast, A., Shafiee, M., Kolios, A., Hart, P., and Pilario, K.: Structural reliability assessment of offshore wind turbine support structures subjected to pitting corrosion-fatigue: A damage tolerance modelling approach, Wind Energy, 23, 2004–2026, https://doi.org/10.1002/we.2542, 2020.
Shojai, S., Schaumann, P., and Brömer, T.: Probabilistic modelling of pitting corrosion and its impact on stress concentrations in steel structures in the offshore wind energy, Mar. Struct., 84, 103232, https://doi.org/10.1016/j.marstruc.2022.103232, 2022.
Silva, J. E., Garbatov, Y., and Guedes Soares, C.: Ultimate Strength Assessment of Rectangular Steel Plates Subjected to a Random Non-Uniform Corrosion Degradation, Eng. Struct., 52, 295–305, 2013.
Song, S., Lin, H., Sherman, P., Yang, X., Nielsen, C. P., Chen, X., and McElroy, M. B.: Production of hydrogen from offshore wind in China and cost-competitive supply to Japan, Nat. Commun., 12, 6953, https://doi.org/10.1038/s41467-021-27214-7, 2021.
Sørensen, J. D.: Reliability-based calibration of fatigue safety factors for offshore wind turbines, Int. J. Offshore Polar, 22, 234–241, 2012.
Steinberger-Wilckens, R.: Der Aufbau einer Infrastruktur für Wasserstoff als Treibstoff – Wie kann es gehen?, in: VDI Berichte, No. 1704, https://research.birmingham.ac.uk/en/publications/der-aufbau-einer-infrastruktur-für-wasserstoff-als-treibstoff-wie (last access: 4 March 2024), 2002.
Stetco, A., Dinmohammadi, F., Zhao, X., Robu, V., Flynn, D., Barnes, M., Keane, J., and Nenadic, G.: Machine learning methods for wind turbine condition monitoring: A review, Renew. Energ., 133, 620–635, https://doi.org/10.1016/j.renene.2018.10.047, 2019.
Stewart, G., Lackner, M., Haid, L., Matha, D., Jonkman, J., and Robertson, A.: Assessing fatigue and ultimate load uncertainty in floating offshore wind turbines due to varying simulation length, Conference Paper NREL/CP-5000-58518, July 2013, 11th International Conference on Structural Safety and Reliability, Columbia University, New York, New York, 16–20 June 2013, https://www.nrel.gov/docs/fy13osti/58518.pdf (last access: 4 March 2024), 2013.
Sunday, K. and Brennan, F.: A review of offshore wind monopiles structural design achievements and challenges, Ocean Eng., 235, 109409, https://doi.org/10.1016/j.oceaneng.2021.109409, 2021.
Temiz, M. and Javani, N.: Design and analysis of a combined floating photovoltaic system for electricity and hydrogen production, Int. J. Hydrogen Energ., 45, 3457–3469, https://doi.org/10.1016/j.ijhydene.2018.12.226, 2020.
Thöns, S.: On the Value of Monitoring Information for the Structural Integrity and Risk Management, Comput.-Aided Civ. Inf., 33, 79–94, https://doi.org/10.1111/mice.12332, 2018.
Thöns, S., Faber, M. H., and Rücker, W.: Life Cycle Cost Optimized Monitoring Systems for Offshore Wind Turbine Structures, in: IRIS Industrial Safety and Life Cycle Engineering: Technologies/Standards/Applications, edited by: VCE Vienna Consulting Engineers, Vienna, Austria, 75–90, https://www.vce.at/iris/pdf/irisbook/iris_chapter04.pdf (last access: 4 March 2024), 2013.
Tsujimoto, M., Uehiro, T., Esaki, H., Kinoshita, T., Takagi, K., Tanaka, S., Yamaguchi, H., Okamura, H., Satou, M., and Minami, Y.: Optimum routing of a sailing wind farm, J. Mar. Sci. Tech., 14, 89–103, https://doi.org/10.1007/s00773-008-0034-1, 2009.
Tuegel, E. J., Ingraffea, A. R., Eason, T. G., and Spottswood, S. M.: Reengineering Aircraft Structural Life Prediction Using a Digital Twin, Int. J. Aerospace Eng., 2011, 154798, https://doi.org/10.1155/2011/154798, 2011.
Turner, M. W., Cleland, J. G., and Baker, J.: Salt Water Activated Power System (SWAPS) for ocean buoys and related platforms, OCEANS 2009, 26–29 October 2009, 1–8, https://doi.org/10.23919/OCEANS.2009.5422338, 2009.
VanDerHorn, E. and Mahadevan, S.: Digital Twin: Generalization, characterization and implementation, Decis. Support Syst., 145, 113524, https://doi.org/10.1016/j.dss.2021.113524, 2021.
VATTENFALL: World’s first hydrogen-producing offshore wind turbine gets £9.3million funding boost, https://group.vattenfall.com/uk/newsroom/pressreleases/2022/aberdeen-hydrogen#:~:text=The pilot project at Vattenfall's,production as early as 2025, last access: 1 November 2022.
Veers, P., Bottasso, C. L., Manuel, L., Naughton, J., Pao, L., Paquette, J., Robertson, A., Robinson, M., Ananthan, S., Barlas, T., Bianchini, A., Bredmose, H., Horcas, S. G., Keller, J., Madsen, H. A., Manwell, J., Moriarty, P., Nolet, S., and Rinker, J.: Grand challenges in the design, manufacture, and operation of future wind turbine systems, Wind Energ. Sci., 8, 1071–1131, https://doi.org/10.5194/wes-8-1071-2023, 2023.
Wagg, D. J., Worden, K., Barthorpe, R. J., and Gardner, P.: Digital Twins: State-of-the-Art and Future Directions for Modeling and Simulation in Engineering Dynamics Applications, ASCE-ASME J. Risk. and Uncert. in Engrg. Sys. Part B Mech. Engrg., 6, 030901, https://doi.org/10.1115/1.4046739, 2020.
Wang, L., Kolios, A., Liu, X., Venetsanos, D., and Cai, R.: Reliability of offshore wind turbine support structures: A state-of-the-art review, Renewable and Sustainable Energy Reviews, 161, 112250, https://doi.org/10.1016/j.rser.2022.112250, 2022.
Woznicki, M., Le Solliec, G., and Loisel, R.: Far off-shore wind energy-based hydrogen production: Technological assessment and market valuation designs, J. Phys. Conf. Ser., 1669, 012004, https://doi.org/10.1088/1742-6596/1669/1/012004, 2020.
Wu, X., Hu, Y., Li, Y., Yang, J., Duan, L., Wang, T., Adcock, T., Jiang, Z., Gao, Z., and Lin, Z.: Foundations of offshore wind turbines: A review, Renewable and Sustainable Energy Reviews, 104, 379–393, 2019.
Xu, K., Zhang, M., Shao, Y., Gao, Z., and Moan, T.: Effect of wave nonlinearity on fatigue damage and extreme responses of a semi-submersible floating wind turbine, Appl. Ocean Res., 91, 101879, https://doi.org/10.1016/j.apor.2019.101879, 2019.
Yeter, B. and Garbatov, Y.: Structural integrity assessment of fixed support structures for offshore wind turbines: A review, Ocean Eng., 244, 110271, https://doi.org/10.1016/j.oceaneng.2021.110271, 2022.
Yeter, B., Garbatov, Y., and Guedes Soares, C.: Evaluation of fatigue damage models predictions for fixed offshore wind turbine support structures, Int. J. Fatigue, 87, 71–80, https://doi.org/10.1016/j.ijfatigue.2016.01.007, 2016.
Yeter, B., Garbatov, Y., and Guedes Soares, C.: Risk-based life-cycle assessment of offshore wind turbine support structures accounting for economic constraints, Struct. Saf., 81, 101867, https://doi.org/10.1016/j.strusafe.2019.06.001, 2019.
Yeter, B., Garbatov, Y., and Guedes Soares, C.: Risk-based maintenance planning of offshore wind farms, Reliability Engineering and System Safety, 202, 107062, https://doi.org/10.1016/j.ress.2020.107062, 2020.
Yeter, B., Garbatov, Y., and Guedes Soares, C.: Structural Health Monitoring Data Analysis for Ageing Fixed Offshore Wind Turbine Structures, Proceedings of the ASME 2021 40th International Conference on Ocean, Offshore and Arctic Engineering. Volume 2: Structures, Safety, and Reliability, Virtual, Online, 21–30 June 2021, V002T02A030, ASME, https://doi.org/10.1115/OMAE2021-63007, 2021.
Young, R. B., Barr, I. R., and Marianowski, L. R.: Production of methane using offshore wind energy, 11th Intersociety Energy Conversion Engineering Conference, SAO/NASA Astrophysics Data System, 1, 541–546, https://ui.adsabs.harvard.edu/abs/1976iece.conf..541Y (last access: 4 March 2024), 1976.
Zhao, P., Dai, Y., Wang, J., and Xie, D.: Dynamic Analysis of a Wind Energy Storage System in Remote Offshore Areas, Proceedings of the ASME 2011 Turbo Expo: Turbine Technical Conference and Exposition. Volume 1: Aircraft Engine, Ceramics, Coal, Biomass and Alternative Fuels, Wind Turbine Technology, Vancouver, British Columbia, Canada, 6–10 June 2011, 831–839, ASME, https://doi.org/10.1115/GT2011-46058, 2011.
Zhu, X., Lei, Q., Meng, Y., and Cui, X.: Analysis of tensile response of flexible pipe with ovalization under hydrostatic pressure, Appl. Ocean Res., 108, 102451, https://doi.org/10.1016/j.apor.2020.102451, 2021.
Zulkifli, M., Husain, M. A., Zaki, N. M., Jaafar, A., Mukhlas, N., Ahmad, S. S., Soom, E. M., and Azman, N.: Environmental impacts of utilization of ageing fixed offshore platform for ocean thermal energy conversion, J. Phys. Conf. Ser., 2259, 012019, https://doi.org/10.1088/1742-6596/2259/1/012019, 2022.
- Abstract
- Introduction
- Overview of hydrogen systems for offshore deployment
- Key design requirements
- Key support structure design considerations
- Discussion
- Conclusions
- Appendix A: Abbreviations and nomenclature
- Data availability
- Author contributions
- Competing interests
- Disclaimer
- Acknowledgements
- Financial support
- Review statement
- References
- Abstract
- Introduction
- Overview of hydrogen systems for offshore deployment
- Key design requirements
- Key support structure design considerations
- Discussion
- Conclusions
- Appendix A: Abbreviations and nomenclature
- Data availability
- Author contributions
- Competing interests
- Disclaimer
- Acknowledgements
- Financial support
- Review statement
- References