the Creative Commons Attribution 4.0 License.
the Creative Commons Attribution 4.0 License.
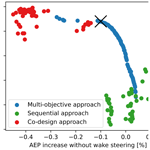
Evaluating the potential of a wake steering co-design for wind farm layout optimization through a tailored genetic algorithm
Pieter M. O. Gebraad
Jan-Willem van Wingerden
Wake steering represents a viable solution to mitigate the wake effect within a wind farm. New research that considers the effect of the control strategy within the layout optimization is emerging, adopting a co-design approach. This study estimates the potential of this technique within the layout optimization for a wide range of realistic conditions. To capture the benefits of such methods, a genetic algorithm tailored to the layout optimization problem has been developed in this work; hence this is referred to as a layout optimization genetic algorithm (LO-GA). The crossover phase is designed to recognize and exploit the differences and the similarities between parent layouts, whereas the randomness of the mutation is limited to improve the exploration of the design space. New relations have been introduced to calculate the geometric yaw angles based on the reciprocal positions between the turbines. For a base case of 16 turbines located at the Hollandse Kust Noord site, a gain in the annual energy production (AEP) between 0.3 % and 0.4 % is obtained when the co-design approach is adopted. This increases up to 0.6 % for larger farms, saturating after 25 turbines. However, the benefit of the co-design decreases in the case of low power densities or if the wind resource is highly unidirectional. On the other hand, in the case that wake steering is not applied during the operation of the farm, a decrease in the AEP up to 0.6 % is registered for a layout optimized with the co-design method. To prevent the risk related to future decisions on the control strategy, a multi-objective co-design approach is proposed. This is based on the simultaneous optimization of the layout for a scenario in which wake steering is applied versus a case where wake steering is not adopted during the operation of the farm. We have concluded that the solutions obtained with this method ensure an AEP gain higher than 0.3 % for a 16-turbine farm while limiting the loss to below 0.1 % in the case that wake steering is not applied. However, these AEP gains are affected by the size of the wind direction bins adopted in the simulations, enhancing the necessity of taking into account the wind direction errors and the yaw actuation constraints for a realistic evaluation of the co-design approach.
- Article
(6910 KB) - Full-text XML
- BibTeX
- EndNote
The mitigation of the wake interaction between wind turbines represents one of the major challenges for the design and the operation of wind farms (Meyers et al., 2022). Higher power generation and load reduction can be achieved by minimizing the wake effect, increasing the revenues associated with the electricity production while extending the lifetime of the farm (Cassamo, 2022). The rapid development of offshore wind energy has demonstrated the necessity of constraining a high number of turbines in limited areas, increasing the impact of these effects (Pettersen et al., 2023). Therefore, innovative solutions are required to address the wake interactions in order to extract the topmost value from a wind farm.
The minimization of the wake losses is generally addressed by appropriately selecting the positions of the turbines within the available surface (Mosetti et al., 1994). This design phase is usually referred to as the wind farm layout optimization problem (WFLOP) and aims to maximize one or multiple objectives while satisfying various types of constraints, e.g., geographical restrictions or minimum spacing (Feng and Shen, 2015). Different implementations of the WFLOP can be distinguished depending on how the positions of the turbines are related to the optimization variables. Specifically, they can be parameterized through a limited number of variables by introducing regular layouts, where periodic patterns are repeated throughout the farm. Otherwise, the positions of the turbines can be identified by discrete or continuous coordinates, depending on the requirements of the resolution of the design space. Therefore, the WFLOP can assume different qualities, with the choice often depending on the trade-off between the required accuracy and the computational cost, usually determined by the size of the farm and the level of fidelity of the models adopted to calculate the wake interactions. Depending on the purpose of the study, different objectives can be considered for the WFLOP. However, current methods mainly focus on the maximization of the annual energy production (AEP) or the minimization of the levelized cost of energy (LCOE) (Tao et al., 2020).
Wind farm control represents another viable solution for mitigating the wake effects during the operation of the plant, based on the performance optimization of the entire farm considered one entity instead of a summation of individually optimized turbines (van Wingerden et al., 2020). Relying on various concepts, different wind farm control techniques have been developed in the recent years (Meyers et al., 2022). Among these approaches, wake steering has been demonstrated to significantly improve the power production of a wind farm, deviating the wakes from the downstream turbines by actuating yaw control (Doekemeijer et al., 2021).
The design phase of a wind farm is often not influenced by the wind farm control technique, which is only considered during the operation of the plant (Stanley et al., 2023). However, different studies have proved that taking into account the wind farm control strategy already during the design stage could lead to significant improvements in the performance, especially within the WFLOP. This is usually referred to as the co-design approach, in contrast to the traditional sequential method in which design and operation phases constitute two separate blocks that are optimized individually (Fleming et al., 2016).
The co-design approach is included in the WFLOP by adapting the control variables during the computation of the objective function, e.g., the axial induction factor for static induction control or yaw angles for wake steering (Stanley et al., 2023). Aiming to optimize the wind farm layout considering its entire lifetime, the optimal control variables have to be determined for each possible case experienced by the farm, i.e., different combinations of wind speeds and directions. However, this leads to an optimization problem characterized by an extremely high number of variables, requiring expensive computational resources in terms of core numbers and/or simulation time (Fleming et al., 2016).
Various solutions have been introduced to tackle the “curse of dimensionality” while capturing the benefits of the co-design approach. Fleming et al. (2016) and Yin et al. (2023a) have decoupled the optimization problem; i.e., the control variables are optimized for an initial layout, and then these values are assumed within the WFLOP. A nested approach has been proposed by Pedersen and Larsen (2020), who have iterated for each step the calculation of the optimal coordinates followed by the optimization of the control variables. Another nested method has been adopted by Chen et al. (2022), decomposing the WFLOP for different wind scenarios and constraining the same turbines' positions through a coordination problem. Another possible strategy consists in the use of regular layouts to reduce the number of variables related to the WFLOP without affecting those related to the control optimization (Hou et al., 2017). This approach can be followed by a position refinement, as implemented by Tang et al. (2022). Alternatively, the number of variables can be diminished by limiting the simulations to one representative wind speed value for each wind direction (Gebraad et al., 2017; Song et al., 2023). Machine learning surrogate models are also implemented to fasten the computation of the objective function or to improve the exploration of the highly dimensional design space (Song et al., 2023; Yin et al., 2023b).
Recently, a novel approach has been introduced by Stanley et al. (2023), where analytical relations are used to obtain the optimal control variables within the AEP calculation, avoiding an expensive nested optimization. Specifically, this study focuses on the wake steering technique, and the yaw angle of each turbine is determined for each flow case based on the position of the downstream turbines; hence this approach is referred to as geometric yaw. This approximation of the optimal yaw angles has also been implemented in the open-source software FLORIS (National Renewable Energy Laboratory, 2024). In the study of Stanley et al. (2023), this method enables the integration of the wake steering within the WFLOP, increasing the AEP up to 0.8 % with respect to the traditional sequential approach. However, this value refers to a rather specific farm consisting of 16 wind turbines simulated in a site characterized by a Gaussian hill spatially varying inflow. Moreover, high power density and low minimum-distance spacing between turbines have been adopted. As mentioned by Stanley et al. (2023), these conditions boost the benefits of the co-design approach, coming close to the maximum improvement achievable with the proposed method. On the other hand, the geometric yaw relation introduced by Stanley et al. (2023) is based on a limited number of variables, enabling a straightforward interpretation and implementation. Therefore, there is a significant margin for improvement that could enhance the advantage of the co-design approach for wake steering. These considerations demonstrate the necessity to understand the real potential of the geometric yaw method within the WFLOP for more realistic conditions.
A crucial aspect of the WFLOP is the choice of the optimization algorithm to extract the optimal positions of the turbines. The literature lacks full agreement on the most appropriate optimization algorithm, and both gradient-based (GB) and gradient-free (GF) techniques are adopted to solve the WFLOP (Thomas et al., 2023). The non-convexity of the WFLOP challenges conventional GB methods in reaching the global optimum, requiring multiple runs from a variety of starting conditions (Guirguis et al., 2016). An attempt to reduce the multi-modality of the problem has been made by Thomas et al. (2022), who introduced a technique named wake expansion continuation, based on the gradual reduction in the wake diameter during each iteration. Moreover, GB methods cannot guarantee high performance with black-box objective functions, which would require the computationally expensive finite differences for the calculation of the gradient (Martins and Ning, 2022). On the other hand, GF approaches such as a genetic algorithm (GA) and particle swarm optimization (PSO) are usually favorable in the case of a design space characterized by many local optima. However, these methods could lead to a higher number of function calls than GB and tend not to scale effectively with a high number of variables (Rios and Sahinidis, 2013). The sparse nonlinear optimizer (SNOPT) (Gill et al., 2005) is often adopted for the WFLOP, and it has been used by Stanley et al. (2023) to test the co-design approach using the geometric yaw relation. However, the study from Thomas et al. (2023) compared eight promising optimization algorithms, including SNOPT, and concluded that the best performance is achieved by a discrete exploration-based optimization (DEBO) method, which combines a greedy initialization and discrete refinement of the solution, developed specifically for the WFLOP.
The popularity of a GA to solve the WFLOP is due to its ability to explore the design space with a high degree of the solutions' variety. However, as the number of turbines increases, the capability of convergence is seriously affected. This is demonstrated in Fig. 1, which shows the results of a basic implementation of the GA using the open-source Python library PyGad (Gad, 2023). In this figure, the case where a regular layout is used to create an initial population is compared to a random initialization of the optimization variables. It can be observed that in the former case the GA is not able to further improve the initial layout, whereas in the latter the GA cannot converge to a solution better than a regular layout. This behavior is related to the excessive randomness that characterizes the exploration of the design space. Therefore, this study aims to exploit the ability of the GA to explore a non-convex design space while improving its convergence ability by capturing the physical meaning of the optimization variables. This is achieved by developing a novel method named the layout optimization genetic algorithm (LO-GA), where the selection, crossover and mutation phases are designed specifically for the WFLOP.
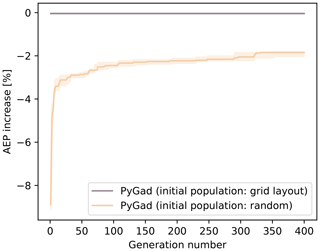
Figure 1WFLOP using PyGad GA: comparison between the use of a random initial population and a population generated from a regular layout. The solid lines represent the median AEP increase with respect to the regular layout, whereas the area refers to the range between the 25th and 75th percentiles, with that being the results of multiple simulations of the same case.
The contribution of this work is fourfold:
-
New geometric yaw relations are formulated to improve the capability of approximating the optimal yaw angles.
-
The effectiveness of the co-design approach is tested for different power densities, farm sizes and site types to understand the potential of this method in realistic conditions.
-
The impact of not applying wake steering for a layout optimized using the co-design method is quantified, and a multi-objective co-design approach is investigated.
-
A tailored genetic algorithm for the WFLOP is developed, referred to as the LO-GA.
The remainder of the paper is structured as follows. In Sects. 2–5 the methodology adopted in this work is explained, describing the LO-GA and the geometric yaw relations developed in this study, as well as introducing the case studies that have been selected. Then, Sect. 6 includes the results that quantify the potential of the co-design approach. These results are then discussed in Sect. 7, whereas Sect. 8 draws the conclusions and includes the recommendations for future work.
This section explains how the wind farm layout optimization can be solved by adopting a co-design approach. First, the WFLOP is defined by specifying objectives and constraints considered in this study. Second, the methodology adopted to apply and evaluate the co-design concept within the WFLOP is described.
2.1 Wind farm layout optimization problem
The WFLOP consists in optimizing the position of the turbines within a pre-defined area. In this study, the objective of the WFLOP is the maximization of the AEP, calculated as shown in Eq. (1) by summing the power (Pθ,u) generated by the farm for every wind direction (θ) and speed (u) multiplied by the correspondent probability of occurrence (ρθ,u). This is referred as the objective or fitness function. The optimization variables are identified by the Cartesian coordinates of the turbines (x,y); hence the total number of variables is equal to 2 nwt, with nwt indicating the total number of turbines. The turbines' positions are restricted to a rectangular area, as expressed in Eq. (2). Moreover, a spacing constraint is considered to guarantee a minimum distance (dmin) between the turbines, formulated in Eq. (3).
The AEP of the wind farm is computed using PyWake (Pedersen et al., 2023), an open-source tool developed by the Technical University of Denmark (DTU) which simulates the wake interaction between the turbines of a wind farm. The Bastankhah Gaussian deficit (Bastankhah and Porté-Agel, 2014) model is selected in this study to calculate the wake deficit, whereas the wake deflection is calculated according to Jiménez et al. (2010).
2.2 Co-design approach
Within the WFLOP, the co-design approach consists in considering the control strategy of the wind farm while computing the objective function. In this case, the wind farm control strategy is limited to wake steering, whereas the objective consists in the AEP calculation. Yaw angles are therefore specified for each wind speed and direction bin while computing the AEP through the PyWake function.
In this study, the improvement obtained through the co-design approach is determined as follows. First, the wind farm layout optimization is performed for both cases, namely neglecting and considering wake steering through the geometric yaw relations, obtaining two different layouts. The same starting layout is adopted to avoid the influence of different initial conditions. Second, an accurate yaw optimization is computed for both layouts, determining the optimal angles for each wind speed and direction. Specifically, the serial-refine yaw optimization method is adopted in this study for this phase (Fleming et al., 2022). Then, the AEP is calculated for both layouts considering the optimal yaw angles obtained in this last step. These AEP values are finally compared, expecting the wind farm layout obtained through the co-design approach to outperform the layout that resulted from the traditional method.
A genetic algorithm named the LO-GA tailored to the WFLOP is developed in this work, where new methods are introduced specifically for this optimization problem. These are explained in the next sections following the main blocks that constitute the classic implementation of a GA, namely initialization of the population, selection, crossover and mutation. Table 1 includes all the hyperparameters required by the algorithm, which will be described in the next sections in detail along with their tuning phase. Specifically, some of these hyperparameters allow for different values depending on the generation number, enabling dynamic selection and dynamic mutation (Hassanat et al., 2019). An overview of the LO-GA is included in Fig. 2, where the main blocks, i.e., selection, crossover and mutation, are highlighted.
3.1 Initial population
The starting point of a GA consists in providing an initial population of solutions that enables the algorithm to converge towards an optimal solution. Therefore, the initial population has to be sufficiently close to the optimal solution while preserving the randomness required to further improve such a starting solution. Specifically, an initial population with a low degree of randomness would achieve only limited improvements, whereas an excessive degree of randomness would require an unfeasible number of the generations for the algorithm to converge. In this study, a regular layout (xreg,yreg) is generated based on the number of turbines (nwt), where these occupy the positions of a squared grid. Such a layout is duplicated nwt times in order to form the population matrices (Xreg,Yreg). These matrices will be the base unit for the LO-GA iterations, where different solutions are contained along the first dimension (axis 0), whereas the coordinates of each solution are present in the second dimension (axis 1). To include the randomness within the initial population a mutation step is applied, obtaining the parent population matrices (Xpar,Ypar). The mutation phase is described in detail in Sect. 3.4, where it is mentioned that it requires the fitness value of the solutions, i.e., the AEP in this study. Specifically, the fitness value of each individual turbine is needed. Such a calculation is enabled by the PyWake method for AEP calculation, and it is performed for Xreg,Yreg. These values are stored in the fitness matrix (Freg), which has the same structure of Xreg,Yreg. Lastly, the fitness values are computed for the parent population matrices (Xpar,Ypar) and stored in the parent fitness matrix (Fpar). In conclusion, Xpar,Ypar and Fpar represent the starting point for the LO-GA iterations described in the following sections.
3.2 Selection
The selection phase developed in the LO-GA is divided into two different steps. First, a pre-selection is applied, where the solutions characterized by the lowest fitness are discarded. The fitness of the solutions is expressed through the fitness parent vector (fpar), obtained by the sum of the AEP of all the turbines for each layout in the population. After this pre-selection phase, the tournament technique is adopted to extract the best solutions while ensuring a sufficient degree of randomness (Miller and Goldberg, 1995). Therefore, the outputs of this phase are new parent population matrices (Xpar,Ypar) with the selected solution, along with their corresponding fitness parent matrix (Fpar).
3.3 Crossover
The purpose of the crossover phase is to generate children solutions from the parent population, aiming to capture and combine the optimal characteristics of each parent. This represents the main difference with respect to the traditional genetic algorithms, where the crossover is determined by the random combination of the parent solutions. On the other hand, the crossover phase integrated in the LO-GA relies on the fitness value of every individual turbine to prevent excessive randomness during the design space exploration. The first step consists in dividing the parent population into two different parent matrices, i.e., obtaining and , starting from Xpar,Ypar. Meanwhile, the values of the parent fitness matrices are inherited from Fpar since the parent solutions have not been modified yet. Then, each solution contained in is coupled with a solution of and the actual crossover phase starts. This is applied to each couple of solutions and is divided into two different steps, namely the turbine association and the linear/random crossover, where for every couple of parent solutions two different children solutions are generated. First, the turbine association aims to understand the similarities of the two coupled layouts, labeling each turbine as paired or outliers. In the case that a turbine from the first layout is positioned within a distance lower than dlim from a turbine of the second layout, these two turbines are labeled as paired. The condition that a turbine of the first layout can be paired with a maximum of one turbine of the second layout and vice versa is enforced. Otherwise, the turbines are labeled as outliers. An example of this process of turbine association is depicted in Fig. 3.
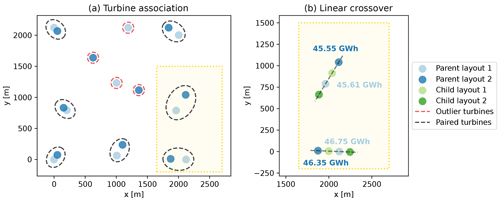
Figure 3(a) Example of the turbine association phase. (b) Linear-crossover technique for a limited number of turbines, highlighted by the yellow area. This example does not represent the optimized layout used in this study, and its only purpose is to clarify the process adopted to apply these techniques.
The second step consists in applying two novel techniques developed specifically for this optimization problem: “linear crossover” between paired turbines and “random crossover” between the outliers. The former technique aims to combine the positions of the two paired turbines, identified by and , in order to generate two different children turbines, identified by and , contained in the first and in the second children layouts and positioned along the line that connects the parent turbines. Specifically, is placed within the parent turbines, whereas is on the side of the parent turbine characterized by the highest fitness value. Indicating with f1 and f2 the fitness values of the two paired parent turbines extracted from , the coordinates of the children turbines are calculated as shown in Eqs. (4)–(6). Therefore, the children turbines move closer to the parent turbine characterized by the higher fitness. This process is shown through an example in Fig. 3. Lastly, to complete the children population, a random crossover is applied between the outlier turbines. This means that the remaining turbines for each children layouts are selected randomly among the outlier turbines of the parent coupled layouts.
3.4 Mutation
After the crossover phase the children solutions are compacted into the children population matrices Xchild,Ychild, which will be mutated to foster the diversity and the randomness of the solutions. Specifically, adaptive mutation is applied in this study while keeping the physical meaning of the design variables, i.e., spatial coordinates (Marsili Libelli and Alba, 2000). However, to apply an adaptive mutation the fitness values of the children solutions have to be calculated; hence the fitness children matrix (Fchild) is computed. Specifically, the concept of adaptive mutation is applied within each individual turbine of the children layouts through assigning a different probability of mutation to every turbine. Therefore, for every solution, the turbines are sorted based on their fitness, and a value increasing linearly from 0 (best turbine) to (worst turbine) is assigned to every turbine. Based on this probability of mutation, a Boolean matrix (Mx,y) is created to determine which of the turbines of Xchild,Ychild will mutate. Simultaneously, the matrices containing the step of mutation (Sm) and direction of mutation (Θm) are created by generating random values within [0,sm] and [0,360°], respectively. These values differ for each turbine in the children population matrices. Then, Eq. (7) is applied to perform the mutation of the children population. The presence of Mx,y ensures that only a limited number of turbines will mutate irrespective of the values of Sm and Θm. This type of mutation limits the degree of randomness but ensures that the new mutated solutions will not differ significantly from the optimal layout, obtaining faster convergence. An example of this mutation process is depicted in Fig. 4.
The last step of the LO-GA is to compute the fitness calculation of the children population after mutation, obtaining a new fitness matrix (Fchild), which will be the input for the next generation along with Xchild,Ychild.
3.5 Hyperparameter tuning
To ensure an effective usage of the GA described in the previous paragraphs, the hyperparameters mentioned in Table 1 have to be properly tuned. The tuning phase presented in this study focuses only on the values of ps, pm, sm and dlim, whereas nkeep is assumed equal to 3 for each simulation. On the other hand, ngen and npop are chosen depending on the specific analysis since a saturation behavior is expected instead of finding optimal values.
The concepts of dynamic mutation and selection are tested, which consist in changing the hyperparameters depending on the generation number (Hassanat et al., 2019). In this case, the purpose is to foster the mutation in the earliest generations to maximize the randomness and adopt less aggressive mutation in the last generations, where only a few refinements are intended. Specifically, the maximum and the minimum values are specified for each parameter to tune, and a linear increase/decrease is adopted to obtain the values for each generation. Therefore, different combinations of hyperparameters are tested in order to find the optimal values for this analysis. The WFLOP described in the base case in Sect. 5.2 is adopted at this stage.
The results of this tuning phase are depicted in Fig. 5, where the violin plots of different cases specified on the x axis are shown. To limit the computational resources of this phase, when a hyperparameter is tested, the others are kept constant and equal to a pre-defined value. The reason why violin plots are included instead of individual values is related to the random nature of the LO-GA, which requires a statistical interpretation of the results. The values present in the violin plot refer to the percentage difference in the AEP with respect to the average value of all the simulations performed in this hyperparameter-tuning analysis. The optimal values are summarized in Table 2 and are adopted in the other simulations performed in this study. It can be observed that the dynamic mutation is favorable for the performance of the LO-GA, whereas a constant value of a percentage of a selection for all the generations is more effective.
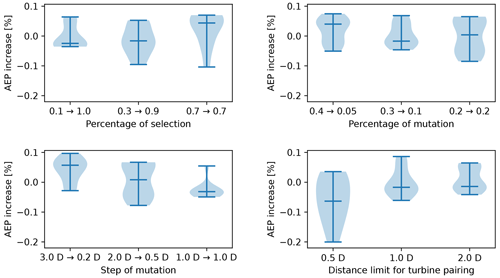
Figure 5Violin plots of the hyperparameter tuning. A total of 10 simulations of the same case are performed to create each plot. Unless explicitly mentioned in the x axis of each plot, the following hyperparameters are adopted: , , and dlim=2 D. The remaining hyperparameters are set as follows: npop=100, ngen=100 and nkeep=3.
3.6 Multi-objective LO-GA
A multi-objective version of the LO-GA described in the previous sections has been developed in this work to enable a wider evaluation of the co-design approach. Such an implementation requires some modifications to be applied to a multi-objective optimization problem, and it is based on the concepts of non-domination rank and crowding distance (Deb et al., 2002). As described in the previous sections, the fitness evaluation of every individual turbine is required for the crossover and the mutation phases. Specifically, these values are used to apply the linear-crossover technique to determine the probability of mutation, requiring the turbines to be ranked based on their fitness value. However, in the case of a multi-objective optimization problem, the ranking of the turbines is not unambiguous. Therefore, to avoid the ambiguity introduced by the multiple objectives, the fitness of the turbines is determined by the 1 − norm between the normalized fitness values of the different objectives. This allows for preserving the structure of the crossover and mutation phases described in Sect. 3.3 and 3.4.
This section describes the novel geometric yaw relations developed in this study and adopted for the co-design simulations. First, the dependence on the main variables is discussed and new relations are introduced, comparing these approaches to the work of Stanley et al. (2023). Second, various effects that impact the optimal yaw angle of a turbine are examined and approximated through a new expression that ensures a higher accuracy in optimal yaw predictions.
4.1 Dependence on geometric variables
Stanley et al. (2023) have introduced a geometric yaw relation to approximate the optimal yaw angle of a turbine based on the streamwise (dx) and the cross-stream (dy) distance to its nearest downstream waked turbine. This relation is linear with respect to dx, whereas the influence of dy is only limited to the sign of the geometric yaw value, as shown in Eq. (8) (Stanley et al., 2023).
However, it can be detected from the study of Stanley et al. (2023) that a decreasing trend is present between the absolute value of dy and the optimal yaw angles. Therefore, two novel relations are introduced to capture this behavior, included in Eqs. (9) and (10), respectively. The first relation extends the linear behavior of dx present in Eq. (8) to dy and is characterized by three coefficients () that have to be properly tuned. This relation is considered the linear approach in this study. On the other hand, Eq. (10) is based on exponential relations in order to guarantee higher flexibility in the shape of the curves, ensured by two more coefficients to tune. Therefore, this novel expression is referred as the exponential approach and is characterized by five coefficients ().
These approaches described in Eq. (9) and (10) focus only on the position of the nearest downstream waked turbine for the calculation of the geometric yaw, whose identification is performed as described by Stanley et al. (2023). However, it is preceded by a filtering phase based on the effective wind speed value assuming that wake steering is not applied. Specifically, the effective wind speed (wseff) is computed for each wind turbine of the farm using the appropriate PyWake function. Then, the turbines characterized by wseff>wsrated are filtered out from the identification of the nearest waked turbine. This stage is introduced to avoid a loss in power in the upstream turbine when an increase in the wind speed experienced by the downstream turbine does not affect its power generation; i.e., it is operating in the above-rated region. This step is referred as the wind speed filtering phase and slightly increases the computational time of the process. However, a gain in the accuracy of the geometric yaw approximation is expected.
4.2 Implementing corrections to the geometric yaw
The purpose of this section is to apply different corrections to the geometric yaw relation, aiming to improve the approximation of the optimal yaw angle. The novelty of this method is based on considering multiple waked turbines instead of limiting the relation to the nearest turbine. This new approach is referred as an exponential corrected relation since it is based on the Eq. (10). The following corrective/filtering steps applied in this approach are summarized in the following list and explained in detail in the next paragraphs:
-
wind speed filtering
-
initial optimal yaw approximation
-
optimal yaw correction
-
effective wind speed correction.
The wind-speed-filtering phase consists in the calculation of the effective wind speed assuming no wind farm control strategy. However, in this case filtered out from the identification of the waked turbines are not only the turbines characterized by wseff>wsrated but also those presenting ws. In this study, is assumed. The reasoning behind this additional correction is to avoid the penalization of the upstream turbine caused by the yaw misalignment if the gain in wind speed for the downstream turbine is not sufficient to achieve a value higher than wscut-in.
After the wind speed filtering, an initial approximation of the optimal yaw angle (γinitial) is calculated based on Eq. (10). Unlike the previous approaches focused only on the nearest waked turbine, the geometric yaw is calculated considering every downstream waked turbine individually, identified through the variables dx and dy. Among these multiple geometric yaw values, γinitial is given by the highest of these values. Even though in many cases this value is determined by the nearest downstream waked turbine, there are some situations when such a turbine does not coincide with the one that influences the optimal yaw of the upstream turbine the most. This is explained through an example depicted in Fig. 6. In this illustration, three turbines are considered, and the optimal yaw angle of the first turbine is studied in relation to the position of the third turbine. These optimal yaw angles depicted in the figure on the right are calculated through the serial-refine method; hence they represent the target for the geometric yaw relation. The dashed line represents the optimal yaw angle of the first turbine in the case that only the second turbine is present, i.e., the nearest turbine. It can be observed that for high values of dy, the third turbine does not influence the optimal yaw angle of the first turbine. However, in the case of a better alignment with the first turbine, i.e., dy≈0, the third turbine has an impact on the value even though it is not the nearest turbine. In summary, this initial yaw approximation identifies the downstream waked turbine that has the highest impact on the optimal yaw angle and calculates the geometric yaw based on the dx and dy of this turbine.
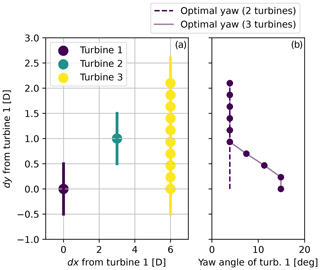
Figure 6Example introduced to explain the reasoning behind the initial optimal yaw approximation. The influence on the optimal yaw angle of the upstream turbine is studied depending on the positions of two downstream turbines. The optimal yaw angle of turbine 1 is studied in relation to the position of turbine 3. (a) Different positions considered in this example. (b) Optimal yaw angle of turbine 1 for two cases: neglecting the presence of turbine 3 (dashed line) and considering different positions (identified by dy) of turbine 3 (solid line).
The initial yaw approximation is then corrected considering the influence of the other downstream waked turbines. The aim of this correction is to avoid the wake of the upstream turbine being steered towards other downstream turbines after the initial yaw approximation. Suppose that the most impactful downstream turbine on the optimal yaw angle of the upstream turbine is characterized by sign(dy)>0. The initial yaw approximation causes a steering of the wake towards the region such that sign(dy)<0. Therefore, only the turbines characterized by a sign(dy) opposite to the sign(dy) of the turbine that has determined the initial yaw approximation are relevant for this correction. Similarly to the previous case, an example is introduced to clarify the need for this correction, illustrated in Fig. 7. It can be observed that the third turbine has no influence on the optimal yaw angle of the first turbine in the case of dy≪0. However, as the dy of the third turbine increases, the optimal yaw angle decreases to avoid the wake being steered toward this turbine. However, if dy≈0, it becomes more convenient to increase the magnitude of the yaw of the first turbine in order to steer the wake away from both turbines.
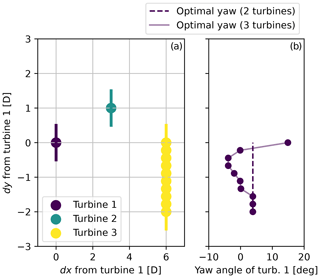
Figure 7Example introduced to explain the reasoning behind the optimal yaw correction. The influence on the optimal yaw angle of the upstream turbine is studied depending on the positions of two downstream turbines. The optimal yaw angle of turbine 1 is studied in relation to the position of turbine 3. (a) Different positions considered in this example. (b) Optimal yaw angle of turbine 1 for two cases: neglecting the presence of turbine 3 (dashed line) and considering different positions (identified by dy) of turbine 3 (solid line).
This situation is tackled as follows. First, the wake deflection caused by γinitial is calculated using the approach of Jiménez et al. (2010). Therefore, the local change in wind direction experienced by the downstream waked turbine is calculated through Eq. (11) (Jiménez et al., 2010). CT and k refer to the thrust coefficient and the wake expansion coefficient, respectively. The former is extracted from the turbine data, depending on the free-stream wind speed, whereas the latter is assumed equal to 0.1.
The values of dx and dy of the turbine of interest, i.e., such that sign(dy) is opposite to the value from which γinitial is calculated, are then modified through a rotation of δwd. Therefore, the new values of d and d are obtained, describing the position of the relevant downstream waked turbines based on the direction of the deflected wake. Subsequently, the method used to calculate γinitial is repeated using d and d as input for the exponential relation of Eq. (10). Therefore, a new geometric yaw value for the upstream turbine is obtained, considered the geometric yaw correction (γcorr) and used to improve the initial approximation as described in Eq. (12). The coefficient αcorr is properly tuned to weight this yaw correction accordingly.
Lastly, a wind speed correction factor (fws) is multiplied with the geometric yaw to penalize high values of γgeom in the case that the deviation of the effective wind speed from the free-stream value is limited. The motivation to include such a correction in the geometric yaw is related to cubic dependence of the generated power with respect to the incident wind speed. fws is calculated as described in Eq. (13), where the coefficient αws is part of the tuning process.
Table 3 summarizes the geometric yaw relations analyzed in this study along with their coefficients, which are properly tuned as described in the next section.
4.3 Tuning of the coefficients
The tuning of the coefficients of the relations introduced in the previous paragraphs aims to guarantee a precise approximation of the optimal yaw angles. The method adopted for this tuning phase assumes that the optimal values of the coefficients are those that lead to the maximization of the AEP when the geometric yaw relations are applied. Specifically, the tuning of the coefficients can be divided into two different steps. First, different wind farm layouts are generated to evaluate the geometric yaw relations. Second, an optimization problem is solved to extract the values of the coefficients that maximize the AEP for the given layouts.
Since in the second step the AEP is calculated for all the layouts for each evaluation of the objective function, the total number of layouts has to be limited to avoid excessive computational requirements. On the other hand, these layouts have to be chosen in order to prevent the geometric yaw relations becoming effective only for few specific cases. Therefore, 20 different layouts are generated through few generations of the LO-GA. Specifically, the population size and number of generations are set equal to 100 and 10, respectively, whereas the number of turbines and the power density are selected randomly in the ranges of 16–72 and 10–20 W m−2.
After the generation of these layouts, the optimization problem of tuning the coefficients of geometric yaw relations is structured as follows. The objective function consists in the average percentage increase in the AEP among the 20 different layouts when applying the geometric yaw relation with respect to the case without wake steering. The optimization variables are the coefficients of the geometric yaw relations, which are bounded in ranges determined by the experience based on preliminary simulations. This optimization problem is solved using a basic GA implementation in PyGad (). The results of this tuning phase, i.e., the optimal coefficients, are included in Table 4 and adopted during the simulations performed in this study.
Among the various coefficients present in the geometric yaw relations and included in Table 4, γmax has a clear physical interpretation since it represents the maximum absolute value for the yaw angles of the turbines. In this study, γmax has been tuned targeting the maximization of the AEP without applying any restriction. However, the tuning of γmax could be constrained to take into account actuation limits or requirements on the structural loading, since it has been demonstrated that wake steering can have a negative impact on some load channels (Shaler et al., 2022).
This section defines the case study adopted in this work to evaluate the co-design approach for the WFLOP. First, the wind scenario and the turbines adopted in the simulations are defined. Second, the base case selected to evaluate the different geometric yaw relations is introduced. Lastly, the modifications introduced to the base case to perform a sensitivity analysis are explained.
5.1 Site and turbines
The wind conditions adopted for the simulations in this study refer to the Hollandse Kust Noord (HKN) site in the Netherlands (Netherlands Enterprise Agency, 2019). The wind rose is computed assuming a uniform Weibull distribution from the scale and shape factor of 12 sectors, as shown in Fig. 8. The turbine type chosen for the simulation is the reference DTU 10 MW, available in PyWake.
5.2 Base case
The aim of this base case is to evaluate the potential of the co-design approach in comparison with the study of Stanley et al. (2023), assuming HKN site conditions. Therefore, a 16-turbine wind farm is adopted, characterized by a power density of 20 W m−2 and a squared available area. A total of 36 and 23 bins are used during the simulations for the wind direction and the wind speed, respectively. Lastly, the minimum-distance constraint (dmin) is set equal to 2 D. This information is summarized in Table 5.
5.3 Sensitivity analysis
Due to the limited size and the large power density of the farm studied in the base case, a sensitivity analysis is performed to understand the potential of the co-design approach for a wider range of conditions. Specifically, different power density values are tested to match conditions similar to current wind farm development projects. This is achieved by keeping the same number of turbines included in the base case while extending the available area. On the other hand, a larger size of wind farms is simulated to investigate the benefits of this method for future large plants. Therefore, new simulations are performed, increasing both the number of turbines and the available area while keeping the power density equal to 20 W m−2. Lastly, the impact of the site is analyzed in terms of the distribution of the wind probability among the different wind sectors. For this purpose, the average scale and shape factors of the HKN site are assumed, while the probability of occurrence of each wind direction is modified. Specifically, this is modeled as a Gaussian distribution, and different values for the standard deviation are used. Adopting this method, various conditions are obtained, ranging from unidirectional wind roses to omnidirectional cases. These are depicted in Fig. 9, where the HKN site is included as well. In general, the same conditions of the base case are adopted in the sensitivity analysis, unless explicitly specified.
This section illustrates the results of the simulations performed in this analysis to evaluate the potential of the co-design approach for the WFLOP. First, the LO-GA is evaluated in comparison to a general GA implementation. Second, the geometric yaw relations introduced in this work are assessed through a preliminary test, and the results obtained in the base-case simulations are shown. Then, the influence of the power density, the number of turbines and the site type is studied through a sensitivity analysis. Lastly, the results concerning a multi-objective implementation of the co-design approach are shown, and the impact of the wind direction discretization is investigated.
6.1 Evaluation of the genetic algorithm
The LO-GA is compared to the basic implementation of the GA in PyGad, introduced in Fig. 1. The results are depicted in Fig. 10, where it can be observed that the LO-GA outperforms the PyGad implementation, with it being able to improve the regular layout from which the population is initialized.
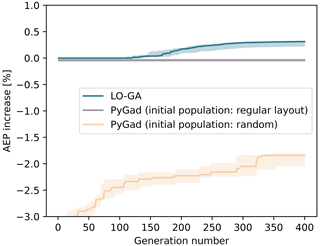
Figure 10Comparison between the LO-GA and PyGad GA to solve the WFLOP. The solid lines represent the median AEP increase with respect to the regular layout, whereas the area refers to the range between the 25th and 75th percentiles, with that being the results of multiple simulations of the same case.
6.2 Preliminary test on geometric yaw relations
To evaluate the effectiveness of the geometric yaw relations summarized in Table 3, a preliminary analysis is performed and the results are depicted in Fig. 11. Specifically, for different farm sizes, the percentage difference in the AEP is calculated between the case when the geometric yaw angles are applied and the case when wake steering is not considered. This is also compared with the AEP value obtained from the yaw angles computed through the serial-refine method (Fleming et al., 2022), considered the optimal yaw angles in this study. For each size of the farm, this calculation is performed on 10 different layouts optimized using the LO-GA (npop=100, ngen=200), assuming a power density of 20 W m−2. It can be observed that the linear and the exponential relation guarantee approximately the same increase in the AEP, whereas higher values are obtained for the exponential corrected relation. This indicates that the corrections included in this approach improve the optimal yaw estimation. The results concerning the Stanley relation are not included in the figure since significantly lower values of AEP increase are produced.
6.3 Base case
The results obtained for the base case are included in Fig. 12, where the procedure explained in Sect. 2.2 is followed, namely comparing optimized layouts resulting from including or neglecting the geometric yaw angles within the objective function of the WFLOP. In both cases, the optimal yaw angles are then applied to calculate the actual AEP associated with the layout. Due to the random nature of the LO-GA, 100 iterations of each case are performed, obtaining the distributions shown in the plots. In this case, the hyperparameters adopted for the layout optimizations are npop=100 and ngen=400. It is evident that the relations introduced in this paper, i.e., linear, exponential and exponential corrected, outperform the Stanley relation. However, no significant difference can be detected among the three new approaches. Specifically, the higher gains of the exponential corrected relation observed in Fig. 11 do not guarantee significantly better performance for the co-design method. Overall, considering median values, an AEP increase between 0.3 % and 0.4 % is obtained for this base case.
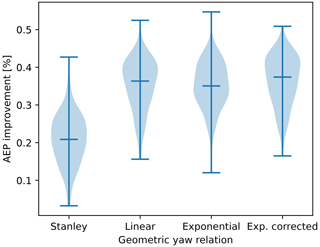
Figure 12AEP improvement obtained with the co-design approach for the WFLOP using different geometric yaw relations. The distributions of multiple iterations for each case are included, highlighting the median value.
The improvements in the AEP obtained with the co-design approach for the WFLOP can be achieved only if wake steering is applied during the operation of the farm. Therefore, in the case that wake steering is not adopted, a drop in performance is experienced for the layouts optimized using the co-design method. Assuming no wake steering during the operation, Fig. 13 illustrates the reduction in the AEP with respect to layouts optimized with the traditional approach. These results are generated using the same method and parameters of Fig. 12. From this analysis it can be concluded that the drop in performance has the same magnitude and follows the same trend of the gains shown in Fig. 12.
6.4 Sensitivity analysis
This section presents the results concerning the sensitivity analysis of the co-design approach in relation to three different aspects: power density, farm size and site type.
6.4.1 Power density
The AEP increase obtained through the co-design approach is dependent on the power density of the wind farm, as highlighted by the solid lines in Fig. 14. Specifically, it can be observed that the benefits of this method diminish for values below 15 W m−2, representing a threshold after which the gain stabilizes. These results demonstrate the effectiveness of the co-design method only for wind farms constrained in a limited area, i.e., characterized by a higher power density. For this analysis the optimization hyperparameters are set to npop=100 and ngen=400, and the randomness associated with the results is handled by computing each case 25 times. Similarly to the base case, the drop in performance in the case that wake steering is not applied during the operation is investigated for different power densities. These results are included in Fig. 14 using dashed lines, exhibiting an opposite trend with respect to the case when wake steering is applied, as observed for the base case. However, the saturation behavior observed for values higher than 15 W m−2 is not present, since the performance worsens for larger values.
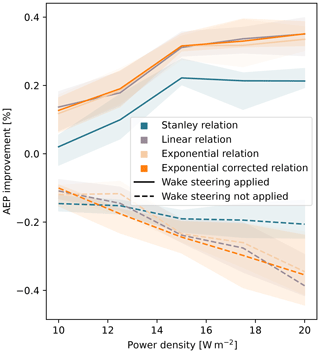
Figure 14AEP gain obtained with the co-design method for different power densities, showing the cases when wake steering is applied (solid lines) and not applied (dashed lines) during the operation of the farm. The area surrounding the lines (median values) refers to the range between the 25th and 75th percentiles, with that being the results of multiple simulations of the same case.
Further analysis is performed to investigate whether the saturation limit of 15 W m−2 is dependent on the squared shape of the domain or if it remains valid for other geometries. For this purpose, the simulations are repeated for two different rectangular areas, characterized by a ratio between the sides equal to 1.5 and 2.0, respectively. The results are limited to the exponential corrected relation and are included in Fig. 15. It can be observed that the magnitude of the AEP gains decreases and the saturation behavior identified in the previous case is not evident anymore, concluding that such results are dependent on the shape of the area where the turbines can be positioned. However, the decreasing trend for the AEP gains in the case of lower power density values remains valid; hence it can be considered a general conclusion for this sensitivity analysis.
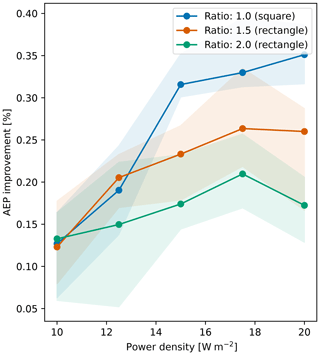
Figure 15AEP gain obtained with the co-design method (exponential corrected relation) for different power densities, showing the trend for different shapes of the available surface, identified through the ratio between the sides of a rectangle. The area surrounding the lines (median values) refers to the range between the 25th and 75th percentiles, with that being the results of multiple simulations of the same case.
6.4.2 Number of turbines
The co-design approach is tested for different farm sizes to explain its potential if the number of turbines increases. The results are included in Fig. 16, where each case is simulated 20 times, adopting npop=100 and ngen=600 as optimization hyperparameters. The choice of a higher number of generations is needed to ensure the convergence when the number of optimization variables increases. In this case, it can be observed that the AEP improvement increases up to 0.6 % and a saturation behavior can be detected when nwt > 25. However, as nwt increases, the trend becomes less evident due to the higher oscillations between different runs, caused by the limited hyperparameters values in proportion to the number of optimization variables. This also occurs in the case that the robustness of the method is tested when wake steering is not applied for a co-design optimized layout, as observed from the dashed lines in Fig. 16.
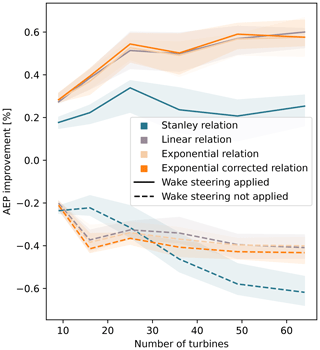
Figure 16AEP gain obtained with the co-design method for farm sizes, showing the cases when wake steering is applied (solid lines) and not applied (dashed lines) during the operation of the farm. The area surrounding the lines (median values) refers to the range between the 25th and 75th percentiles, with that being the results of multiple simulations of the same case.
6.4.3 Wind direction variability
Various site types are investigated to determine the effectiveness of the co-design method in different wind conditions. As mentioned in Sect. 5.3, this study focuses on the shape of the wind rose in terms of the probability of occurrence for the wind directions. Figure 17 shows that the co-design approach becomes less convenient for sites characterized by an evident dominant wind direction, i.e., low standard deviation of the probability of occurrence along 360°. This can be observed not only by a drop in the increase in AEP when wake steering is applied during the operation but also by a significant reduction in the case that wake steering is not adopted. On the other hand, the increase in the AEP does not vary for values of standard deviations higher than 0.4. Similarly to the power density, these results have been obtained from 25 iterations, adopting npop=100 and ngen=400.

Figure 17AEP gain obtained with the co-design method for site types, showing the cases when wake steering is applied (solid lines) and not applied (dashed lines) during the operation of the farm. The x axis refers to the standard deviation of the probability of occurrence of each wind direction, i.e., from unidirectional (low values) to omnidirectional (high values) wind roses. The area surrounding the lines (median values) refers to the range between the 25th and 75th percentiles, with that being the results of multiple simulations of the same case.
6.5 Multi-objective co-design approach
The previous results have highlighted the negative impact in terms of AEP losses in the case that wake steering is not applied during the operation phase in a layout optimized through the co-design approach. This is tackled by performing a multi-objective optimization that maximizes the AEP for the cases when wake steering is applied and when this does not occur during operation. This analysis is limited to the base case and to the exponential corrected geometric yaw relation, and it is performed using the multi-objective version of the LO-GA introduced in Sect. 3.6. The results are outlined in Fig. 18, where the Pareto front is visible on the top right, resulting from a max–max optimization. These have been obtained after 50 iterations of each case, for which the hyperparameters adopted for the base case are used. As highlighted by the cross in Fig. 18, a layout that limits the AEP losses to 0.1 % in the case that wake steering is not applied can be extracted from the Pareto front while ensuring a gain higher than 0.3 % if wake steering takes place.
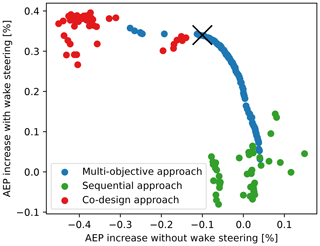
Figure 18Multi-objective co-design approach based on the multi-objective optimization. Each data point indicates an optimized layout. Multiple data points are included also for the sequential and the co-design approach, resulting from different simulations and providing a probabilistic interpretation of the results in accordance with the other graphs. The axis of the plot refers to the AEP increase with respect to the average AEP value obtained through the traditional sequential approach. The Pareto front is present on the top right of the plot, resulting from a max–max problem. A cross is included to identify a possible robust solution.
6.6 Effect of wind direction discretization
The AEP calculation within this study is based on the traditional procedure of discretizing the wind direction, selecting appropriate bins at which the power production of the farm is computed. The resolution of this discretization can have a significant impact on the WFLOP since a sufficiently high resolution is required to consider all the wake interactions between the turbines. On the other hand, using a fine resolution for the wind directions can significantly increase the computational cost of the optimization. As mentioned in Sect. 5.2, 36 wind direction bins are adopted in our simulations, namely the wind direction is discretized using bins of 10°. The purpose of this section is to investigate the influence of this parameter on the co-design approach described in this study.
The simulations of the base case are repeated, modifying the size of the bins adopted for the wind direction, hence altering the objective function used to calculate the AEP. Since such a function is also used during the tuning phase of the LO-GA hyperparameters, their values are recalculated accordingly. Specifically, a higher randomization of the initial population has been shown to be beneficial for both the sequential and the co-design approach, obtaining higher AEP values. This is applied for all the wind direction resolutions tested in this section to provide consistency between the results. Moreover, for each case the same resolution is applied for the layout optimization and the subsequent yaw optimization performed with the serial-refine method.
The results are presented in Fig. 19, which shows a significant drop in the AEP improvement obtained through the co-design approach as the wind direction resolution is increased; i.e., the size of the bins becomes smaller. Moreover, the AEP values corresponding to the sequential and the co-design layouts are also shown individually so as to gain further insights into this behavior. These results are limited to exponential corrected relation since the influence of the wind direction resolution does not vary for the different geometric yaw approaches. In general, the values of AEP improvement obtained for the 10° bin size are lower with respect to the results presented in Fig. 12, as a consequence of the higher randomization of the initial population.
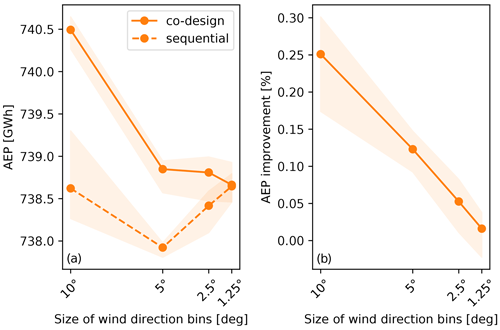
Figure 19Effect of wind direction resolution on the co-design approach, in terms of (a) AEP for the sequential and the co-design layouts and (b) AEP improvement. The area surrounding the lines (median values) refers to the range between the 25th and 75th percentiles, with that being the results of multiple simulations of the same case.
Two different effects can be detected from this analysis. First, the AEP values decrease for both the sequential and the co-design methods when the bin size is halved from 10 to 5°. Increasing the wind direction resolution, more wake interactions are simulated within the farm, amplifying the wake losses. This sensitivity regarding the wind direction resolution is enhanced by the characteristics of the base case, where the limited number of turbines and the higher power density lead to fewer wake interactions and prevent wake expansions. Moreover, the squared shape of the domain causes the wind directions that are multiples of 45° to be characterized by high wake losses. This occurs due to the tendency of the turbines to be positioned at the corners of the domain to maximize the use of the available area. All of these directions cannot be simulated in the case that the bin size is set to 10°, limiting the accuracy of the results. However, the AEP reduction obtained for the 5° bin size is more evident for the co-design case, diminishing the improvement obtained through this approach. Nevertheless, this effect is expected to decrease when the number of turbines is larger, due to the occurrence of wake interaction for a wider range of wind directions. The second effect that can be detected from Fig. 19 concerns the AEP trends as the wind direction bin size is reduced from 5° to lower values. It can be observed that AEP values of the co-design layouts remain stable, whereas those of the sequential layouts increase when a finer resolution is adopted. Therefore, they tend to converge towards the AEP values of the layouts optimized using the co-design method, i.e., leading to an AEP improvement equal to 0 % and nullifying the usefulness of this approach. However, such a result is highly conditioned by the application of the serial-refine method for yaw optimization with a fine wind direction resolution. For instance, when a bin size of 1.25° is adopted for the simulations, the optimal yaw angle is recalculated for every 1.25°. Therefore, it is assumed that during the farm operation the wind direction is measured with an accuracy higher than 1.25 and the yaw angles of turbines are modified every time such a change of 1.25° is detected. These conditions are far from being realistic, as mentioned by Quick et al. (2020). Therefore, the results presented in Fig. 19 are altered by this assumption, which is not consistent with current wind farm operational limits. Nevertheless, it can be concluded that the application of an extremely precise wake steering control would saturate the benefits of the co-design approach proposed in this study.
This section aims to interpret and provide a further explanation of the results presented in the previous paragraphs. In general, the methodology introduced in this work to solve the WFLOP based on co-design approach, namely the LO-GA and the different geometric yaw relations, has succeeded to improve upon the methods available in literature. However, the increase in the AEP of 0.8 % described by Stanley et al. (2023) for a site characterized by Gaussian hill spatially varying inflow cannot be obtained for common sites such as the HKN location adopted for this study. Specifically, values up to 0.6 % have been obtained in this analysis, when farms composed by more than 25 wind turbines are considered. As mentioned by Stanley et al. (2023), this limited percentage can be translated into significant amounts in terms of revenue and energy production. Specifically, since HKN wind farm plans to fulfill the energy demand equivalent to 1 million households, this increase of 0.6 % can be quantified as the consumption of 6000 households in this case (Crosswind, 2024). Most importantly, this approach based on geometric yaw angles does not involve a significantly higher computational cost with respect to traditional methods, unlike other co-design implementations. On the other hand, the limited improvement in the AEP obtained with the co-design approach is affected by the uncertainty related to the engineering models adopted for the calculations. Moreover, this modest increase in the AEP can be difficult to detect during wind tunnel experiments or field tests. These considerations can challenge the reliability of this method despite the promising results obtained from the simulations.
Besides the benefits associated with the co-design approach in the case that wind farm control is applied during operation, this study has also highlighted the downsides of not implementing such a control strategy. A decrease in the AEP is considered in this case to be a consequence of adapting the objective function of the WFLOP to the wake steering technique. The magnitude of such a loss in energy production is similar to the gain observed if the coherent procedure is applied. Therefore, it is essential that the wind farm operator makes firm decisions regarding the control strategy prior to the design phase. Otherwise, the limited improvement of the co-design approach would be further challenged by the uncertainty caused by the future decisions of the wind farm operator. To prevent such a situation, a multi-objective co-design approach is proposed in this study, optimizing the wind farm layout for both the case when wake steering is applied and the case when this does not happen. Therefore, such a method increases the reliability of the wind farm layout, minimizing the risk related to a future decision regarding the control strategies made during the operation of the farm.
The perspective and the limitations of the co-design approach for wake steering have been shown by the sensitivity analysis performed in this study. First, a decrease in the AEP gain is observed for low power densities, irrespective of the shape of the available surface. Such behavior proves that including the geometric yaw within the WFLOP is more effective when wake steering plays a major role. In particular, higher gains are obtained when the distances between the turbines decrease; hence the wake effect is more impactful. However, after a certain power density this improvement can saturate due to the impossibility of further mitigation of the wake deficit. Second, similar explanations can be provided to justify the dependence of the AEP improvement on the farm size, expressed in terms of number of turbines. In principle, extending the size of the farm increases the number of downstream turbines that experience lower wind speeds, hence boosting the potential of wake steering and consequently of the co-design approach. However, a saturation trend can also be observed in this case, caused by the impossibility of deflecting the wake towards a turbine-free region when the number of turbines surpasses a certain limit. Lastly, when analyzing the effect of different wind resources it can be observed that the sites characterized by unidirectional wind do not benefit significantly from the co-design approach. In this case, the traditional methods adopted to solve the WFLOP arrange the positions of the turbines in order to avoid alignment along the dominant wind direction, limiting the necessity of applying wake steering.
The results described in these sections are limited to the conditions tested in this study, giving a broad quantitative overview of the co-design potential but leaving some points of discussion that can be addressed qualitatively as follows. First, the wake models adopted in this work can influence the results of this analysis. Specifically, the adoption of a wake-added turbulence model such as that of Crespo and Hernandez (1996) is expected to widen the wake shape and enhance its recovery. This could decrease the effectiveness of wake steering and the co-design approach in the case of large wind farms. However, these choices are not expected to significantly impact either the geometric yaw relations or the magnitude of the AEP gains described in this study. Second, the results presented in this research refer to the chosen reference turbine, i.e., the DTU 10 MW, and therefore can differ in the case of a different turbine type. Nevertheless, all the geometric relations presented here are normalized with the rotor diameter; hence they are not sensitive to the size of the turbine. However, the mismatch between the geometric models, which generally scale with D, and the wind turbine power, proportional to D2, can influence the analysis. This is expected to have a consequence on the coefficients of the geometric yaw relations, requiring additional tuning, whereas the final conclusion should not be impacted significantly.
Lastly, the analysis of the effect of the wind direction resolution adopted for AEP calculation with wake steering has highlighted the importance of this parameter for the evaluation of the co-design approach. Specifically, the simplicity of the base case chosen to enable a straightforward comparison between the different methods has caused high sensitivity with respect to the wind direction bin size. In general, the use of a fine resolution seems to decrease the benefits of the co-design method, increasing the uncertainty in the results presented in this work. However, whereas the magnitude of the AEP improvement is seriously affected by the size of the wind direction bins, the trends with the variables of interest are expected to remain valid. Overall, this analysis has emphasized the necessity of including uncertainties within the yaw optimization process, as suggested by the work of Quick et al. (2020). This would enable a more realistic evaluation of the co-design approach.
A genetic algorithm tailored to the layout optimization and referred to as the LO-GA has been developed in this study, where the crossover and the mutation phases are implemented to capture the physical meaning of the optimization variables in order to improve the exploration of the design space. This method enables the improvement of regular layouts, usually not achievable with basic versions of a GA. Moreover, three novel relations have been introduced to calculate the geometric yaw angles, namely linear, exponential and exponential corrected approaches. Whereas the former two methods are based only on the streamwise and cross-stream distances of the nearest turbine, the last approach considers all the downstream turbines within the wake, enabling a more accurate prediction.
A base case consisting in a 16-turbine farms located at the HKN site has been used to calculate the improvement achieved with the co-design method, for which an increase in the AEP between 0.3 % and 0.4 % has been obtained. To evaluate the potential of the co-design approach based on wake steering, a wider range of cases have been tested, and the conclusions are summarized in the following list:
-
The wind farms characterized by a high power density benefit the most from the co-design approach, irrespective of the shape of the available surface where the turbines can be positioned.
-
By increasing the number of turbines, an AEP increase up to 0.6 % can be obtained. However, this value stabilizes for a number of turbines higher than 25.
-
Sites characterized by unidirectional wind do not benefit significantly from the co-design approach.
Besides the advantages in terms of AEP increase that we have mentioned, this study has investigated the effect of not applying the control strategy during the operation phase in a layout optimized using the co-design method. Specifically, it has been shown that a decrease in the AEP would occur, prompting a recommendation that firm decisions about the control strategy have to be taken prior to the design phase. To minimize the risk of losses related to future decisions regarding the control strategy, a multi-objective co-design method has been proposed, for which the layout is optimized simultaneously for the case when wake steering is applied and, when this does not occur, during the operation phase. Adopting this approach, the AEP losses in a 16-turbine layout can be limited to 0.1 % if wake steering is not adopted, while the AEP gain is kept above 0.3 % in the case that wake steering is applied.
An analysis of the effect of the wind direction resolution has shown that the magnitude of the AEP gains is significantly affected by this parameter. Decreasing the size of the wind direction bins has resulted in a negative effect on the benefit of the co-design approach. However, such an influence is partially caused by the unrealistic assumption of minimal error in wind direction measurements and the absence of constraints in yaw actuation. Therefore, this analysis has considered the necessity of integrating uncertainties within the yaw optimization to provide an accurate evaluation of the co-design method, indicating an interesting pathway for future research.
Lastly, some other recommendations for future work are mentioned. First, the geometric yaw relations can be improved to provide a more accurate approximation of the optimal yaw angles. Specifically, the relations developed in this study neglect the scenario when wake steering is not applied when two aligned turbines are too close to each other. Second, the integration of grey-/black-box machine learning models in the co-design framework is recommended to understand if a further increase in the AEP can be achieved in the case of a better approximation of optimal yaw angles. This study has shown that better predictions of the optimal yaw angles do not lead to a significant improvement in the co-design approach. However, there is still a gap between the yaw angles obtained with the serial-refine method and the geometric yaw relations which could be filled using models based on machine learning techniques. Third, another recommendation for future work concerns the objective of the WFLOP, which could be extended further than the AEP, for instance to load mitigation.
Code and data adopted in this study are available from the corresponding author on request.
MB: conceptualization, methodology, software, validation, investigation, writing (original draft), visualization. PMOG: writing (review and editing), supervision. JWvW: writing (review and editing), conceptualization, supervision, resources, funding acquisition.
At least one of the (co-)authors is a member of the editorial board of Wind Energy Science. The peer-review process was guided by an independent editor, and the authors also have no other competing interests to declare.
Publisher’s note: Copernicus Publications remains neutral with regard to jurisdictional claims made in the text, published maps, institutional affiliations, or any other geographical representation in this paper. While Copernicus Publications makes every effort to include appropriate place names, the final responsibility lies with the authors.
This research has been supported by the European Union's Horizon Europe 2020 program (grant no. 101122256).
This paper was edited by Yi Guo and reviewed by two anonymous referees.
Bastankhah, M. and Porté-Agel, F.: A new analytical model for wind-turbine wakes, Renew. Energ., 70, 116–123, https://doi.org/10.1016/j.renene.2014.01.002, 2014. a
Cassamo, N.: Active Wake Control Validation Methodology, Tech. rep., TNO, https://resolver.tno.nl/uuid:8f05d03f-1d1b-44e1-885b-12e638914ec2 (last access: 4 November 2024), 2022. a
Chen, K., Lin, J., Qiu, Y., Liu, F., and Song, Y.: Joint optimization of wind farm layout considering optimal control, Renew. Energ., 182, 787–796, https://doi.org/10.1016/J.RENENE.2021.10.032, 2022. a
Crespo, A. and Hernandez, J.: Turbulence characteristics in wind-turbine wakes, J. Wind Eng. Ind. Aerod., 61, 71–85, https://doi.org/10.1016/0167-6105(95)00033-X, 1996. a
Crosswind: Crosswind HKN, https://www.crosswindhkn.nl/ (last access: 4 November 2024), 2024. a
Deb, K., Pratap, A., Agarwal, S., and Meyarivan, T.: A fast and elitist multiobjective genetic algorithm: NSGA-II, IEEE T. Evolut. Comput., 6, 182–197, https://doi.org/10.1109/4235.996017, 2002. a
Doekemeijer, B. M., Kern, S., Maturu, S., Kanev, S., Salbert, B., Schreiber, J., Campagnolo, F., Bottasso, C. L., Schuler, S., Wilts, F., Neumann, T., Potenza, G., Calabretta, F., Fioretti, F., and van Wingerden, J.-W.: Field experiment for open-loop yaw-based wake steering at a commercial onshore wind farm in Italy, Wind Energ. Sci., 6, 159–176, https://doi.org/10.5194/wes-6-159-2021, 2021. a
Feng, J. and Shen, W.: Modelling Wind for Wind Farm Layout Optimization Using Joint Distribution of Wind Speed and Wind Direction, Energies, 8, 3075–3092, https://doi.org/10.3390/en8043075, 2015. a
Fleming, P. A., Ning, A., Gebraad, P. M., and Dykes, K.: Wind plant system engineering through optimization of layout and yaw control, Wind Energy, 19, 329–344, https://doi.org/10.1002/we.1836, 2016. a, b, c
Fleming, P. A., Stanley, A., Bay, C., King, J., Simley, E., Doekemeijer, B., and Mudafort, R.: Serial-Refine Method for Fast Wake-Steering Yaw Optimization, J. Phys. Conf. Ser., 2265, 032109, https://doi.org/10.1088/1742-6596/2265/3/032109, 2022. a, b
Gad, A. F.: Pygad: An intuitive genetic algorithm python library, Multimedia Tools and Applications, 1–14, https://pypi.org/project/pygad (last access: 4 November 2024), 2023. a
Gebraad, P., Thomas, J. J., Ning, A., Fleming, P., and Dykes, K.: Maximization of the annual energy production of wind power plants by optimization of layout and yaw-based wake control, Wind Energy, 20, 97–107, https://doi.org/10.1002/we.1993, 2017. a
Gill, P. E., Murray, W., and Saunders, M. A.: SNOPT: An SQP algorithm for large-scale constrained optimization, Society for Industrial and Applied Mathematics, https://doi.org/10.1137/S0036144504446096, 2005. a
Guirguis, D., Romero, D. A., and Amon, C. H.: Toward efficient optimization of wind farm layouts: Utilizing exact gradient information, Appl. Energ., 179, 110–123, https://doi.org/10.1016/j.apenergy.2016.06.101, 2016. a
Hassanat, A., Almohammadi, K., Alkafaween, E., Abunawas, E., Hammouri, A., and Prasath, V. B. S.: Choosing Mutation and Crossover Ratios for Genetic Algorithms – A Review with a New Dynamic Approach, Information, 10, 390, https://doi.org/10.3390/info10120390, 2019. a, b
Hou, P., Hu, W., Soltani, M., Chen, C., Zhang, B., and Chen, Z.: Offshore Wind Farm Layout Design Considering Optimized Power Dispatch Strategy, IEEE T. Sustain. Energ., 8, 638–647, https://doi.org/10.1109/TSTE.2016.2614266, 2017. a
Jiménez, A., Crespo, A., and Migoya, E.: Application of a LES technique to characterize the wake deflection of a wind turbine in yaw, Wind Energy, 13, 559–572, https://doi.org/10.1002/we.380, 2010. a, b, c
Marsili Libelli, S. and Alba, E.: Adaptive mutation in genetic algorithms, Soft Comput., 4, 76–80, https://doi.org/10.1007/s005000000042, 2000. a
Martins, J. R. R. A. and Ning, A.: Engineering Design Optimization, Cambridge University Press, Cambridge, UK, ISBN 9781108833417, https://doi.org/10.1017/9781108980647, 2022. a
Meyers, J., Bottasso, C., Dykes, K., Fleming, P., Gebraad, P., Giebel, G., Göçmen, T., and van Wingerden, J.-W.: Wind farm flow control: prospects and challenges, Wind Energ. Sci., 7, 2271–2306, https://doi.org/10.5194/wes-7-2271-2022, 2022. a, b
Miller, B. L. and Goldberg, D. E.: Genetic Algorithms, Tournament Selection, and the Effects of Noise, Complex Syst., 9, https://api.semanticscholar.org/CorpusID:6491320 (last access: 4 November 2024), 1995. a
Mosetti, G., Poloni, C., and Diviacco, B.: Optimization of wind turbine positioning in large windfarms by means of a genetic algorithm, J. Wind Eng. Ind. Aerod., 51, 105–116, https://doi.org/10.1016/0167-6105(94)90080-9, 1994. a
National Renewable Energy Laboratory: FLORIS Version 3.5, GitHub [code], https://github.com/NREL/floris/releases/tag/v3.5 (last access: 16 August 2024), 2024. a
Netherlands Enterprise Agency: Holland Kust (noord) – Wind & Water, https://offshorewind.rvo.nl/page/view/3ce5f11f-d39c-4de4-a877-6daf6b945c5c/wind-en-water (last access: 17 August 2024), 2019. a
Pedersen, M. M. and Larsen, G. C.: Integrated wind farm layout and control optimization, Wind Energ. Sci., 5, 1551–1566, https://doi.org/10.5194/wes-5-1551-2020, 2020. a
Pedersen, M. M., Forsting, A. M., van der Laan, P., Riva, R., Romàn, L. A. A., Risco, J. C., Friis-Møller, M., Quick, J., Christiansen, J. P. S., Rodrigues, R. V., Olsen, B. T., and Réthoré, P.-E.: PyWake 2.5.0: An open-source wind farm simulation tool, GitLab [code], https://gitlab.windenergy.dtu.dk/TOPFARM/PyWake (last access: 4 November 2024), 2023. a
Pettersen, S. S., Aarnes, O., Arnesen, B., Pretlove, B., Ervik, A. K., and Rusten, M.: Offshore wind in the race for ocean space: A forecast to 2050, J. Phys. Conf. Ser., 2507, 012005, https://doi.org/10.1088/1742-6596/2507/1/012005, 2023. a
Quick, J., King, J., King, R. N., Hamlington, P. E., and Dykes, K.: Wake steering optimization under uncertainty, Wind Energ. Sci., 5, 413–426, https://doi.org/10.5194/wes-5-413-2020, 2020. a, b
Rios, L. M. and Sahinidis, N. V.: Derivative-free optimization: A review of algorithms and comparison of software implementations, vol. 56, Journal of Global Optimization, 1247–1293, https://doi.org/10.1007/s10898-012-9951-y, 2013. a
Shaler, K., Jonkman, J., Barter, G. E., Kreeft, J. J., and Muller, J. P.: Loads assessment of a fixed-bottom offshore wind farm with wake steering, Wind Energy, 25, 1530–1554, https://doi.org/10.1002/we.2756, 2022. a
Song, J., Kim, T., and You, D.: Particle swarm optimization of a wind farm layout with active control of turbine yaws, Renew. Energ., 206, 738–747, https://doi.org/10.1016/J.RENENE.2023.02.058, 2023. a, b
Stanley, A. P. J., Bay, C. J., and Fleming, P.: Enabling control co-design of the next generation of wind power plants, Wind Energ. Sci., 8, 1341–1350, https://doi.org/10.5194/wes-8-1341-2023, 2023. a, b, c, d, e, f, g, h, i, j, k, l, m, n, o
Tang, X. Y., Yang, Q., Stoevesandt, B., and Sun, Y.: Optimization of wind farm layout with optimum coordination of turbine cooperations, Comput. Ind. Eng., 164, 107880, https://doi.org/10.1016/J.CIE.2021.107880, 2022. a
Tao, S., Xu, Q., Feijóo, A., Zheng, G., and Zhou, J.: Nonuniform wind farm layout optimization: A state-of-the-art review, Energy, 209, 118339, https://doi.org/10.1016/j.energy.2020.118339, 2020. a
Thomas, J. J., McOmber, S., and Ning, A.: Wake expansion continuation: Multi-modality reduction in the wind farm layout optimization problem, Wind Energy, 25, 678–699, https://doi.org/10.1002/we.2692, 2022. a
Thomas, J. J., Baker, N. F., Malisani, P., Quaeghebeur, E., Sanchez Perez-Moreno, S., Jasa, J., Bay, C., Tilli, F., Bieniek, D., Robinson, N., Stanley, A. P. J., Holt, W., and Ning, A.: A comparison of eight optimization methods applied to a wind farm layout optimization problem, Wind Energ. Sci., 8, 865–891, https://doi.org/10.5194/wes-8-865-2023, 2023. a, b
van Wingerden, J. W., Fleming, P. A., Göçmen, T., Eguinoa, I., Doekemeijer, B. M., Dykes, K., Lawson, M., Simley, E., King, J., Astrain, D., Iribas, M., Bottasso, C. L., Meyers, J., Raach, S., Kölle, K., and Giebel, G.: Expert Elicitation on Wind Farm Control, J. Phys. Conf. Ser., 1618, 022025, https://doi.org/10.1088/1742-6596/1618/2/022025, 2020. a
Yin, X., Zhao, Z., and Yang, W.: Ensemble prediction aided multi-objective co-design optimizations of grid-connected integrated renewables for green hydrogen production, J. Clean. Prod., 425, 138585, https://doi.org/10.1016/J.JCLEPRO.2023.138585, 2023a. a
Yin, X., Zhao, Z., and Yang, W.: Optimizing cleaner productions of sustainable energies: A co-design framework for complementary operations of offshore wind and pumped hydro-storages, J. Clean. Prod., 396, 135832, https://doi.org/10.1016/J.JCLEPRO.2022.135832, 2023b. a
- Abstract
- Introduction
- Co-design within wind farm layout optimization
- Layout optimization genetic algorithm (LO-GA)
- Geometric yaw relations
- Case study
- Results
- Discussion
- Conclusions
- Code and data availability
- Author contributions
- Competing interests
- Disclaimer
- Financial support
- Review statement
- References
- Abstract
- Introduction
- Co-design within wind farm layout optimization
- Layout optimization genetic algorithm (LO-GA)
- Geometric yaw relations
- Case study
- Results
- Discussion
- Conclusions
- Code and data availability
- Author contributions
- Competing interests
- Disclaimer
- Financial support
- Review statement
- References