the Creative Commons Attribution 4.0 License.
the Creative Commons Attribution 4.0 License.
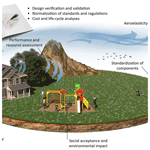
Current status and grand challenges for small wind turbine technology
Alessandro Bianchini
Galih Bangga
Ian Baring-Gould
Alessandro Croce
José Ignacio Cruz
Rick Damiani
Gareth Erfort
Carlos Simao Ferreira
David Infield
Christian Navid Nayeri
George Pechlivanoglou
Mark Runacres
Gerard Schepers
Brent Summerville
David Wood
Alice Orrell
While modern wind turbines have become by far the largest rotating machines on Earth with further upscaling planned for the future, a renewed interest in small wind turbines (SWTs) is fostering energy transition and smart grid development. Small machines have traditionally not received the same level of aerodynamic refinement as their larger counterparts, resulting in lower efficiency, lower capacity factors, and therefore a higher cost of energy. In an effort to reduce this gap, research programs are developing worldwide. With this background, the scope of the present study is 2-fold. In the first part of this paper, an overview of the current status of the technology is presented in terms of technical maturity, diffusion, and cost. The second part of the study proposes five grand challenges that are thought to be key to fostering the development of small wind turbine technology in the near future, i.e. (1) improving energy conversion of modern SWTs through better design and control, especially in the case of turbulent wind; (2) better predicting long-term turbine performance with limited resource measurements and proving reliability; (3) improving the economic viability of small wind energy; (4) facilitating the contribution of SWTs to the energy demand and electrical system integration; (5) fostering engagement, social acceptance, and deployment for global distributed wind markets. To tackle these challenges, a series of unknowns and gaps are first identified and discussed. Based on them, improvement areas are suggested, for which 10 key enabling actions are finally proposed.
A major portion of today's installed wind power is in the form of large wind power plants, which mainly consist of multi-megawatt machines (GWEC, 2020), while a clear trend in further upscaling of both rated power and dimension is ongoing (Veers et al., 2019). Small wind turbines (SWTs) are, however, still visible around the world for a variety of applications, including electric power generation for households, industrial centers, farms, and isolated communities; combining with other energy sources and storage in hybrid energy systems for electricity to support remote monitoring and telecommunications; and providing direct energy services for applications such as water pumping, desalination, and purification (Chagas et al., 2020). The use of wind turbines in rural areas is of particular relevance for some countries; for example, around the Horn of Africa, small wind systems are the most viable solution in the scarcely electrified parts of those countries (Gabra et al., 2019). Karekezi (2002) reported that South Africa has more than 100 000 wind pumps in operation used at over 45 818 farms. SWTs are a subset of a larger distributed wind market segment that can include large turbines installed in distributed applications. Figure 1 associates typical distributed turbine sizes with their main types of application.
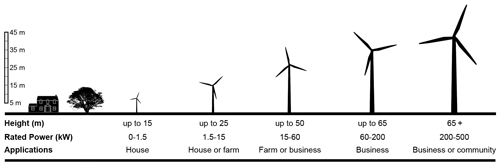
Figure 1Small and distributed wind turbine dimensions and rated power outputs as a function of various applications.
When SWTs are used for a variety of ancillary purposes other than electricity production such as ventilation or water pumping, different turbine concepts can come into play. These applications may use the Savonius vertical-axis turbine (Akwa et al., 2012) or the multi-blade American windmill (Baker, 1985), which constitute a small space on the market. Although these machines are in all respects SWTs, they are not discussed in the present study, which instead focuses on SWTs for electricity production.
Before moving forward, a key element of this study is defining what is meant by “small wind turbine”. A universal consensus on this has not been reached, with the International Electrotechnical Commission (IEC) Standards (IEC – International Standard, 2019b) defining SWTs as turbines with a maximum rotor swept area of 200 m2; the same threshold is applied to eligible turbines for certification by the AWEA Small Wind Turbine Performance and Safety Standard 9.1-2009; however, a new American National Standards Institute consensus standard, ACP 101-1, is being developed by the American Clean Power Association (ACP), the successor to the AWEA. ACP 101-1 is intended to eventually supersede the AWEA 9.1-2009 standard (Summerville et al., 2021). Several countries use rated power as the key differentiator, and ACP 101-1 thus defines SWTs as having a peak power of 150 kW or less and microturbines as having a peak power up to 1 kW. In Brazil, small wind systems are categorized as power stations (which could be composed of one or many wind turbines) with a total rated capacity below 100 kW, according to Resolution 438/2012 of the Brazilian Electricity Regulatory Agency (ANEEL) (Chagas et al., 2020).
The importance of having a more comprehensive definition of “small wind” has been recently put in the spotlight. For example, it has been suggested by the Small Wind Turbine Technical Committee of the European Academy of Wind Energy (EAWE) that many problems and technical challenges of SWTs are common to the majority of the rotors up to 500 kW (EAWE, 2020), i.e., also extending to distributed wind turbines (DWTs). As is further discussed in the present study, it is important to more clearly define those characteristics that make SWTs unique from utility-scale turbines. However, this is not an easy task because significant variability in wind turbine design is also apparent, with no specific size-based design threshold. Additionally, there are a variety of “alternative” configurations available on the open market (Bianchini, 2019), such as vertical-axis turbines (Aslam Bhutta et al., 2012), diffuser-augmented wind turbines (Evans et al., 2020), or first prototypes of airborne wind energy (AWE) converters (Meghana et al., 2022). Even though SWTs may still represent a niche application within the wind energy market, they have recently been exhibiting a notable rate of growth concomitant with the diffusion of smart energy systems (Tzen, 2020). This diffusion, however, is still hindered by the typically higher costs of small wind systems. These increased costs are driven by several factors, including a lack of development and system optimization and issues related to those cost items (i.e., electrical connection, resource assessment expenses, installation cost, etc.) that are not proportionally lower for smaller projects (Simic et al., 2013). The growth of the SWT sector is further notable in light of the several published reports showing that SWT installations have failed to reach their expected energy yield, resulting in underperforming turbines. This is particularly true in the case of installations in the urban or built environment (WINEUR project, 2005; Fields et al., 2016). Development in highly complex areas, such as urban locations, is complicated due to the wind conditions in the city's canopy layer, which typically have low intensity, high variability, high levels of turbulence, and inclined or even reversed airflows. While several studies have shown a theoretically good potential for urban wind (Balduzzi et al., 2012; Toja-Silva et al., 2013), a number of challenges still need to be tackled to effectively fit wind energy converters to this environment, as recently discussed by Micallef and Bussel (2018) and Stathopoulos et al. (2018). In the present study, the authors decided not to include a specific technical analysis of the needs for urban wind, although future work on the topic has to be encouraged (Battisti, 2018).
Even so, projections of SWT deployment in future scenarios of distributed energy production within smart grids (thus in proximity to populated areas) are considered promising. In this sense, SWTs are expected to provide a significant contribution, especially in combination with other renewable energy sources. However, the higher levelized cost of energy (LCOE) of SWTs, especially compared to residential solar photovoltaics (PVs), still hampers the massive diffusion of this technology.
1.1 A guide to this article
The present study has two main focuses. First, it provides an overview of the status of SWT technology. We present the market diffusion and economics of SWTs (Sects. 2–3) with the goal of placing the technology in the current energy market and defining some important threshold values. We then provide a description of the main technical features of SWTs (Sect. 4) and compare them to those of their utility-scale counterparts. Section 5 pursues the second focus of the work, defining five grand challenges that – per the authors' assessment – are key to fostering the development of SWTs in the near future. More specifically, a series of unknowns and gaps for SWTs is first defined, and then the main improvement areas and prospects are proposed to address those gaps. Finally, Sect. 6 synthesizes the main outcomes of the study into concluding remarks and defines 10 key enabling actions for achieving the grand challenges in the near future.
There is at least ∼ 1.8 GW of installed small wind capacity globally from over 1 million turbines (Orrell et al., 2021). The global spread of this electrical capacity, including all types of turbines and based on available reports from some key surveyed countries, is shown in Table 1 (asterisks denote a lack of validated data for that specific year). Figure 2 provides a more focused insight into several of those countries, which showed notably different trends in the first years of the last decade, where SWT technology saw one of its more interesting phases. While Denmark, the United Kingdom, and the United States have a long-recorded history of small wind installations, China has added larger amounts of small wind capacity more consistently in recent years. On the other hand, Italy and the United Kingdom, which saw many installations in the first decade of the century, both experienced recent decreases due to feed-in tariff (FIT) policy changes. FITs provide payments to owners of small-scale renewable generators at a fixed rate per unit of electricity produced, verifying that the cost of the installation is recovered over the lifetime of the generator. In the case of Italy, in particular, the significant increase in installations seen around 2016–2017 was due to a special program of incentives for turbines under 60 kW. The FIT rate in Italy declined over time before expiring in 2017. It was replaced by the FER1 Decree in 2019 (Dentons, 2020). In line with these changes, an estimated 77.46 MW of wind projects using turbines sized up through 250 kW was installed in Italy in 2017, no installation reports were available for 2018 and 2019, and 0.65 MW of projects was reported for 2020. The United Kingdom closed its FIT program to new applicants in 2019 and introduced the Smart Export Guarantee program. Under that program, applicants now receive a tariff determined by the buyer rather than a fixed price determined by the government (Ofgem, 2021). Consequently, small wind deployment went from 28.53 MW in 2014 to only 0.43 MW in 2019 (Orrell et al., 2021). In a scenario of decaying government incentives, an outlier case in Europe is Greece (Greek Government Gazette, 2021), which still offers an FIT for SWTs. At the time of writing this paper, the program was for 20 MW installed capacity, starting with a tariff of EUR 157 per megawatt-hour (USD 181 per megawatt-hour) that will be automatically reduced based on the cumulative contracted power of the projects. A bonus with respect to the tax break is also in place, which brings the FIT to EUR 163 per megawatt-hour (USD 187 per megawatt-hour).
Table 1Small wind turbine installations through 2020. Data from Orrell et al. (2021) and Chagas et al. (2020). Values in bold refer to years/countries with FIT schemes in place. Asterisks refer to missing data for that specific year.
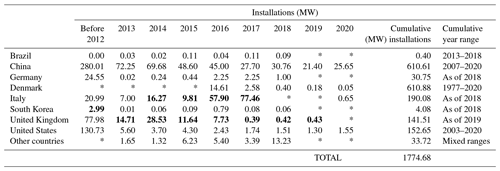
Other examples of these tariffs include those in Japan and the Republic of Korea. Japan's FIT program was established in the wake of the Fukushima Daiichi nuclear disaster. Its rates have steadily declined, from a peak of JPY 55 per kilowatt-hour in 2015 to JPY 19 (approximately1 EUR 0.125 or USD 0.175) per kilowatt-hour as of 2019 for turbines less than 20 kW (Orrell et al., 2021). The Republic of Korea also had an FIT program, but it was ended in 2012 and replaced with a renewable portfolio standard (Lo, 2018). While the switch from the FIT program increased capacities in some renewables in the Republic of Korea, such as biomass co-firing and fuel cell deployment, small wind installations dropped (Orrell et al., 2021).
The discontinuous nature of incentives and national programs makes it difficult for manufacturers to stay in the market, even in those countries where SWT technology is more present, as in the UK, Italy, and the United States. Six small wind manufacturers in the United States reported international exports in 2015, with just three doing so in 2020 (Orrell et al., 2021). Similarly, sales in China and exports from China have fluctuated with the number of Chinese small wind manufacturers in that market. In 2017, only 15 Chinese small wind turbine manufacturers reported sales, a decrease from 28 in 2014 (Duo, 2017), corresponding to a 60 % drop in sales from 2014 to 2017 (Orrell et al., 2021).
From a global perspective, at the time of writing this paper, the largest market for small wind still came from Europe, the United States, and China. SWTs are most commonly used for off-grid applications, such as telecommunication towers and farming. They are also used to power individual homes and small businesses, which can be tied to the grid. In 2019, 94 % of SWT sales went to off-grid applications (Global Info Research, 2021). Unfortunately, 2020 saw only about 30 MW worth of units being sold around the world (Orrell et al., 2021), with a global market in terms of revenues (Fig. 3) still on a flat trend. Regarding future perspectives (Global Info Research, 2021), no clear agreement on future perspectives was found at the time of writing, mainly as a consequence of the financial crisis connected to the global COVID-19 pandemic in 2020. Global Info Research (Global Info Research, 2021) predicted the SWT global market would reach USD 190 million (EUR 165 million) in 2025, with a compound annual growth rate of 11.45 % from 2020 to 2025. The market could thus become promising again, especially in connection with the increasing attention on the transition toward cleaner energy systems. Regarding the future share by region, Europe, Asia-Pacific, and the United States are expected to remain the key players in this sector. In particular, the Asia-Pacific market will lead the total worldwide SWT sales, while the European market will show a reduction in the global relative share (Fig. 4). In Asia, Japan is expected to deploy renewable energy generation at large scales following the Fukushima Daiichi nuclear disaster, whereas other countries such as Malaysia – which represents an untapped market with suitable conditions for SWTs (Wen et al., 2019) – might also see significant deployment.
As described in Sect. 2, the diffusion of SWTs has often gone hand in hand with dedicated financial incentive programs from individual countries. This is unfortunately because the high LCOE of SWTs has represented the main obstacle hampering wider deployment of SWT technology (Predescu, 2016).
The economic evaluation of small wind systems is particularly critical for three main reasons: (1) the capital investment is strongly dependent on the specific turbine and country; (2) the correct selection of the installation site has a much higher impact on actual annual energy production (AEP) than in the case of turbines with large rotors; and (3) as discussed, the real viability of a project may depend completely on the incentives ensured by the specific country.
To give the reader an overview of the aforementioned issues, the main cost factors are analyzed in the following subsections to facilitate the comparison of costs by country or region for the same technologies and to enable the identification of the key drivers in any cost differences. The four key indicators are total installation cost, operation and maintenance cost, capacity factors, and LCOE.
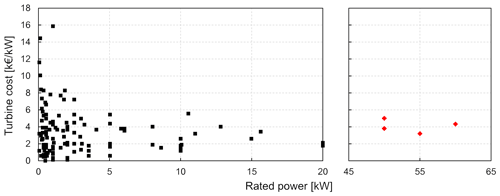
Figure 5Turbine purchase cost survey for rated power lower than 20 kW (Kaldellis and Zafirakis, 2012) and around 50 kW (authors' experience).
3.1 Total installation cost
The total investment for installation can be expressed as the sum of the purchase cost and installation cost. The purchase cost for a SWT is notably variable not only as a function of the turbine size but also over time, depending on the attention given to the technology. Kaldellis and Zafirakis (2012) present a survey on 142 SWT models up to 20 kW, showing – as expected – a turbine cost reduction as a function of the rated power (black square markers in Fig. 5). Recent data from the authors' direct experience are also added as red diamonds in Fig. 5 for the SWTs with rated power outputs around 50 kW. As seen in the figure, the decreasing cost trend for lower rated power values is somehow stopped for rated power outputs around 50 kW. This can be explained considering that, from this size up, turbines become more complex, requiring specific features (e.g., the yawing system) and a manufacturing quality higher than that of smaller turbines. Finally, Bortolini et al. (2014) provide a more up-to-date market survey considering several producers located worldwide and confirm that purchasing costs are not so highly correlated to the plant sizes because of aspects related to the specific producer, e.g., producer country, producer cost structure, and market policies. Having direct information on how the global, or total installed, cost comes together is very rare. In this study, thanks to support from the Eunice Energy Group, a cost breakdown is presented in Table 2 for the 60 kW machine EW16 Thesis (Eunice Energy Group, 2021).
Table 2Capital cost breakdown of a 60 kW turbine (courtesy of the Eunice Energy Group). Weights reported in metric tons.
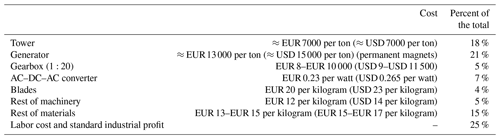
Wood (2011) reported a similar breakdown for a smaller machine (10 kW), showing how – in that case – the relative cost for blades becomes more relevant (7 %), while that of the generator becomes less significant (6 %) due to the lower power output.
The installation cost is probably the most critical parameter to evaluate and includes seven primary factors.
-
Raw material cost, i.e., expenditures to purchase the materials required for the turbine installation as well as to lay the foundation. All these elements are correlated to the wind turbine's weight and height and to the rotor diameter.
-
Earthworks' cost, i.e., foundations, grounding, etc., to enable SWTs' operation. This is more crucial for countries with higher seismic activity that require more expensive foundations and is dependent on the type of soil.
-
Installation labor cost, i.e., workers' salary, crane rental, standby times on windy days.
-
Engineering cost, i.e., expenditures for the preliminary and executive drawings, feasibility study and engineering, and site assessment and wind resource assessment activities to estimate expected AEP as well as documentation of all deliverables.
-
Land purchase cost, i.e., cost for the required ground surface. Considering the tower height, a surface area of the same swept radius is assumed to be necessary. Additional cost for access roads, where not present, may be necessary.
-
Grid connection cost, i.e., cables, power unit, and control system, including license fees.
-
Transportation costs, i.e., the expenditures necessary to get the turbine to the installation site. Transportation costs can include two different types of trips. In the case of imported turbines, transportation by both sea (e.g., to reach the EU mainland) and land (i.e., to reach the final site) is needed.
The relative impact of these factors has been quantified by Bortolini et al. (2014) and reported in Table 3.
The engineering cost in Table 3 includes the wind resource and site assessment activities conducted to estimate a SWT's expected AEP. The low percentage of total cost for this cost factor is in line with similar research that found that many small wind installers do only minimal wind resource and site assessments (Orrell and Poehlman, 2017). This is partly because of the challenges involved in achieving a low-cost and accurate wind resource assessment. First, there are not many tools available and appropriate for small wind assessments. Next, for those installers who do attempt assessments, the tools regularly do not provide accurate AEP estimates because they mischaracterize the wind resource and perform poorly in areas of complex terrain well (Sheridan et al., 2022). Based on the experience of some of the authors, the cost for a resource assessment for a SWT project may be in the order of EUR 15 000 (USD 172 000), although this price is strongly variable from case to case, especially as a function of the site topography. In addition, one should also remember that the complexity of the terrain also affects accessibility to the grid, roads, price of the land, foundations, and the excavation works needed, thus also impacting the other items of the table.
Referring again to the 60 kW EW16 Thetis machine by the Eunice Energy Group, even though real costs are strictly project-dependent, the foundation cost can be broken down into approximately EUR 3000 (USD 3450) for the excavation (23 %), EUR 8000 (USD 9200) for the concrete (61 %), and EUR 2000 (USD 2300) for civil works (16 %). The transportation cost is approximately EUR 5000 per day (USD 5750 per day) (up to two trucks and up to 600 km), while the crane costs for a 50 t, 40 m crane are about EUR 6000 (USD 7200).
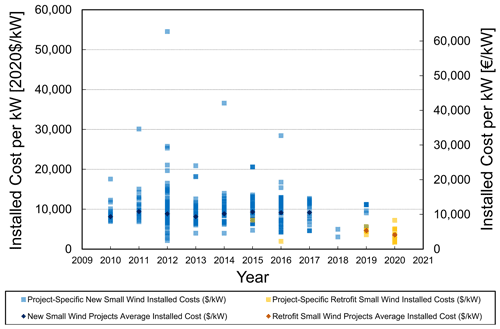
Figure 6Installed cost per kilowatt for newly installed or retrofit projects in the United States (Orrell et al., 2021).
An overview of the overall average annual and project-specific small wind installed cost (in 2020 USD) in the United States for 2010 through 2020 is presented in Fig. 6 (data from Orrell et al., 2021). Only new and retrofit projects with reported installed costs that use turbines with known rated capacities are included. Annual average capacity-weighted installed costs for new US small wind projects range from around EUR 3480 per kilowatt (USD 4000 per kilowatt) to nearly EUR 9565 per kilowatt (USD 11 000 per kilowatt). The small sample sizes and high variance in project-specific costs both contribute to this wide cost range. With the exception of 2018, the overall annual average capacity-weighted installed cost for this US dataset has remained relatively flat at approximately EUR 9260 per kilowatt (USD 9500 per kilowatt) (Orrell et al., 2021). This cost trend is in contrast with residential solar PV costs, which have been steadily dropping over several years (Barbose and Darghouth, 2015).
3.2 Operations and maintenance cost
Operations and maintenance (O&M) are conventionally clustered into a single cost term, but operation costs differ from maintenance costs, and not all distributed wind projects experience them equally. Operation costs for wind projects may include land lease payments, remote monitoring, various operations contracts, insurance, and property taxes. Operations are a significant expense for wind farms and large distributed wind projects; however, they typically are not substantial, or even present, for small, distributed wind projects. On the other hand, all wind projects, distributed or otherwise, require a significant maintenance cost (Orrell et al., 2021). For small wind systems, and especially in the case of complex areas, experience shows that usually an investor does not opt for installation sites with more than two SWTs in the same field or from the same owner. This consequently decreases the available room for the economy scaling on the O&M costs.
In most cases, the project installer or developer performs the maintenance for the system owner. Maintenance costs include labor, travel to the site, consumables, and any other related costs. Therefore, small wind maintenance costs can depend on the maintenance provider's proximity to the project site (i.e., travel costs), the availability of spare parts, and the complexity of maintenance and repairs. Maintenance costs can be categorized as scheduled or unscheduled. Scheduled maintenance activities can include inspecting the turbine, controller, and/or tower; adjusting blades; checking production meter and communications components; and providing an overall annual scheduled maintenance visit per the manufacturer's manual. Unscheduled maintenance activities can include a wide variety of activities, ranging from responding to a customer's complaint of noise from the turbine to replacing the generator, electrical components, inverter, blades, or anemometer. Scheduled maintenance site visit costs for a sample of small wind projects were collected for the Benchmarking US Small Wind Costs report (Orrell and Poehlman, 2017). Scheduled maintenance is typically performed annually. That data showed that the average scheduled maintenance cost per visit is about EUR 32 per kilowatt (USD 37 per kilowatt); the same value was confirmed by some European companies (Eunice Energy Group, personal communication, 2022). In general, upon combining different reference sources, it is reasonable to consider O&M cost for small wind projects in the range of 1 %–3 % of the initial investment (Tzen, 2020).
3.3 Capacity factors
The economic viability of SWTs depends in a complex way on several factors, including the life-cycle energy production and the possible presence of incentives. To address the first issue, i.e., to correctly evaluate actual production, a key metric is the capacity factor.
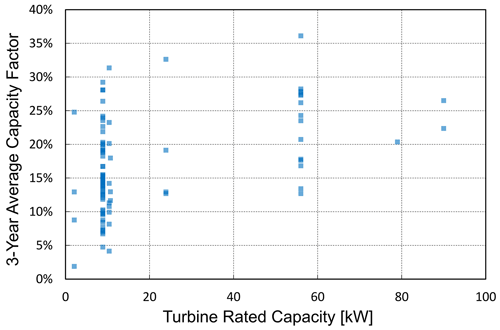
Figure 7The 3-year-average capacity factor for several US wind projects. Data from Orrell et al. (2020).
Boccard observed mean values below 21 % in 2009 (Boccard, 2009), while more recent works observed values between 37 % and 40 % (US DOE, 2015). Figure 7 presents calculated capacity factors for SWTs installed in the United States, based on the average of the first 3 years of reported generation for each project from the New York State Energy Research and Development Authority and US Department of Agriculture Rural Energy for America Program datasets and the turbine rated capacity (Orrell et al., 2020).
The 3-year-average capacity factor for small wind is 17 %, but the dataset includes a range from as small as 2 % to as high as 36 %. This large variability reflects, more than other variables, the challenges to SWT siting and site suitability. For example, the capacity factors for the 8.9 kW rated capacity turbines range from 5 % to 29 %. This means that the same turbine model sited in different locations can achieve very different capacity factors. Overall, the wind resource quality has the largest impact on capacity factors, even though technology improvements have raised turbine power outputs significantly. Therefore, the wide variation in capacity factors across markets is predominantly due to differing wind resource qualities and, to a lesser extent, the different site configurations and technologies used.
3.4 Levelized cost of energy
Scattered data regarding the LCOE of SWTs can be found in the literature and relevant reports. One of the most complete databases is provided by Orrell et al. (2020), who collected the data reported in Fig. 8 (prices are in cents of USD/EUR) for the US market.
The small wind average LCOE after incentives was EUR 0.2 per kilowatt-hour (USD 0.23 per kilowatt-hour) (from 86 US projects totaling 2 MW in rated capacity). To put these numbers in perspective, the LCOE of SWTs may be compared to the average residential retail electric rates ranging from approximately EUR 0.07 to EUR 0.17 per kilowatt-hour (USD 0.08 to 0.20 per kilowatt-hour) in the continental United States (Orrell et al., 2019) and to the LCOE of residential PVs, which is below EUR 0.087 per kilowatt-hour (USD 0.10 per kilowatt-hour). Recent experiences in Europe for turbines in the range of 50 to 60 kW showed potential for a significantly lower LCOE on the order of EUR 0.12 per kilowatt-hour (USD 0.0014 per kilowatt-hour) (Eunice Energy Group, personal communication, 2022). The relationship between calculated LCOEs after incentives and capacity factors is shown in Fig. 9. As expected, the higher the capacity factor, the lower the LCOE in general. Higher capacity factors, which in turn can reduce LCOEs, can be achieved by better siting, which can help increase energy production and better turbine operations (i.e., higher turbine availability).
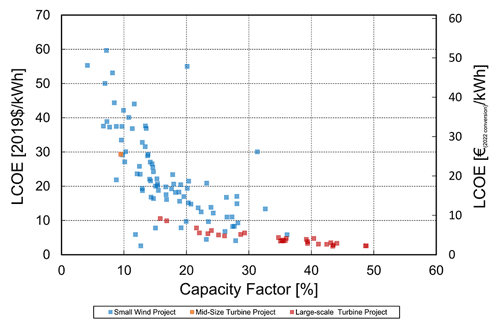
Figure 9Relationship between LCOE and capacity factor for SWT projects. Data from Orrell et al. (2020).
Regarding the European Union, to the best of the authors' knowledge, there is no systematic study of the LCOE of SWTs, but there are a number of studies that point to higher LCOEs than those reported for the United States. For a site with a mean annual wind speed of 4.77 m s−1, Bukala et al. (2016) estimate a yearly energy production of 7551 kWh for a SWT with a rated power of 5 kW, neglecting downtime. They estimate the investment cost of such a wind turbine at EUR 36 500 (USD 42 000), which is lower than that in the data reported for the United States. For a discount factor of 4 % and assuming a yearly operation and maintenance cost of 2 % of the investment cost, an LCOE of EUR 0.45 per kilowatt-hour (USD 0.52 per kilowatt-hour) is produced without incentives.
For a SWT with a rated power of 3.5 kW installed at an agricultural site in Belgium with a mean wind speed of 4.13 m s−1, Tordeur (2018) reports an LCOE of EUR 0.36 per kilowatt-hour (USD 0.415 per kilowatt-hour) without incentives. This, coupled with all the incentives from which a small to medium agricultural enterprise may benefit in Belgium at the time of the measurement campaign (2016) and accounting for a discount rate of 4 %, gives a discounted payback time of 19 years. It is worth noting that the true cost of this project was a very low EUR 4300 per kilowatt (USD 4950 per kilowatt). The low cost is partly explained by the fact that the farmer acquired the tower separately at reduced cost and performed most of the installation himself. Even with such major cost-cutting, the SWT is not economically viable, indicating that a mean wind speed of 4.13 m s−1 is too low for a viable SWT project.
Bryne (2017) reports the metered energy output for a number of sites in Ireland. For a site with a mean wind speed of 6.1 m s−1, the AEP of a 5.2 kW rated wind turbine is 14 947 kWh, and for a site with a mean wind speed of 4.7 m s−1, the AEP of a 2.1 kW rated wind turbine is 3816 kWh. Assuming again a discount rate of 4 %, a yearly operation and maintenance cost of 2 % of the investment cost results in LCOEs of EUR 0.33 per kilowatt-hour (USD 0.38 per kilowatt-hour) and EUR 0.51 per kilowatt-hour (USD 0.59 per kilowatt-hour) for the 5.2 kW and 2.1 kW turbines, respectively, if the average installed cost per kilowatt from Orrell et al. (2019) is used. LCOEs of EUR 0.14 per kilowatt-hour (USD 0.16 per kilowatt-hour) and EUR 0.22 per kilowatt-hour (USD 0.25 per kilowatt-hour) are produced, respectively, if the average installed cost per kilowatt from Tordeur (2018) is used.
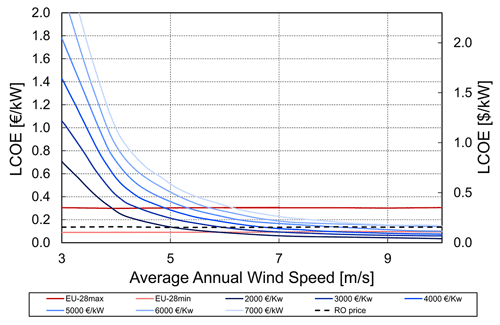
Figure 10LCOE trends versus annual average wind speed at different specific investment values in EU. Data from Predescu (2016).
Figure 10 presents the results of a study of the LCOE trend versus annual average wind speed at different specific investment values, with the household energy purchasing prices in EU also shown as references (Predescu, 2016).
Financial viability for small wind investment occurs in the region where the LCOE curve, computed for a specific investment value, is lower than the household energy price at the implementation location. The break-even point for a specific investment value is at the intersection of the respective LCOE curve with the line representing the household energy price. Beyond this point toward higher wind speeds, the savings obtained when using small wind technology brings long-term tax-free profit and savings to the investor. In countries where the household energy price is lower, financial viability can be reached at smaller specific investment costs and higher annual average wind speeds, which limits the geographical area where grid-connected small wind systems can be efficient. This analysis shows that in most situations, SWTs cannot compete with residential PVs in terms of economic viability (European Court of Auditors, 2018). Even at sites with high wind speeds, the cost reduction required to achieve viability is still substantial. Taking the best case from Bryne (2017) as a close-to-optimal performance example with a capacity factor of 33 %, the investment cost would need to be less than EUR 6000 per kilowatt (USD 6900 per kilowatt) for the LCOE to fall below EUR 0.20 per kilowatt-hour (USD 0.23 per kilowatt-hour), which is typical for residential retail electric rates in many European countries. This illustrates the main conclusion from the above analysis: SWTs may be viable, but only at very windy sites and with a serious additional effort to reduce the investment cost.
While Sects. 1–3 reported the status of the technology in terms of diffusion and costs, this section shifts the focus to the specific features of SWTs, which are the core of small wind systems. The philosophy with which this study has been prepared highlights those features that make SWTs different from utility-scale machines. This is important for introducing the resulting challenges that must be tackled to further progress SWT technology.
4.1 Typical features of small wind turbines compared to utility-scale turbines
Utility-scale wind turbines are usually located in clusters and in areas with high wind resources, from a few turbines to large wind plants located far (e.g., offshore) from the consumer. Although some utility-scale wind turbines may provide energy to the owner, they are typically owned by or provide power to a utility company. In contrast, SWTs are typically owned by the individual or organization that will use the power, such as a home or business, and are installed close to those loads. Because the siting driver for SWTs is proximity to loads and not the optimal wind resource, the winds at these locations often have low average speeds; are highly turbulent; and are more likely to have obstacles nearby, which can create flow structures of a scale commensurable to that of the turbine. On the one hand, this usually leads to lower peak power coefficients, ranging approximately from 0.25 to 0.40 (Wood, 2011), compared to values higher than 0.5 for utility-scale machines (Veers et al., 2019). However, full transparency regarding the real efficiency of SWTs is often missing. For example, in a relatively recent study, it was shown that 15 out of 43 manufacturers claim a power coefficient above the theoretical maximum or Betz–Joukowsky limit (Simic et al., 2013). Notwithstanding this, it is undisputable that the peculiar environment these rotors work in implies that SWTs must be specifically designed to work effectively in both low- and turbulent-wind-resource conditions. The implications of these peculiar working conditions are many and involve all aspects of turbine design and operation, as summarized below.
4.1.1 Aerodynamics
The combination of dimensions much smaller than those of utility-scale machines with turbulent winds may present significant problems for the aerodynamics of SWTs. First, the resulting low Reynolds numbers (Re) may cause a laminar separation bubble, which is associated with a local maximum of the drag coefficient in the polar and a reduced lift-to-drag ratio () (Selig, 2003). The presence of transition and the relative impact of inflow turbulence on it is key for airfoil performance (Abbott and Von Doenhoff, 2010). This has many implications for design, including the fact that airfoils for SWTs must be selected from those that provide good performance at low Re numbers, which favors airfoils with lower thicknesses that are, however, more sensitive to stall. A compromise in this regard must be pursued. The presence of transition makes the dependent on Re and thus is particularly challenging for blade designers. Because the angle needed for maximum is also Re-dependent, a constant-pitch turbine would not operate at maximum efficiency at a constant tip-speed ratio, making the control strategy in below-rated conditions more complicated (see the following subsection).
The aforementioned issues are particularly challenging in terms of proper simulation. Panel methods usually employed by companies to define polars likely fail to correctly model these phenomena in many instances, especially in the near- and post-stall regions. However, accurately modeling these phenomena is crucial for SWTs, particularly stall-controlled ones (Papi et al., 2021). High-fidelity models used in academia are often not affordable for SWT companies, and airfoil selection is therefore often based on published performance data. Examples of airfoils with good performance characteristics at low (around 5×105) Reynolds numbers can be found in Gigue`re and Selig (1998) and Timmer and van Rooij (2003). Even high-fidelity turbulence models, however, often do not predict lift and drag accurately in the presence of transition, let alone laminar separation, and the designer should rely on lift and drag data measured in reliable wind tunnel tests (Van Treuren, 2015).
The problem of low Reynolds numbers is further exacerbated by the possible installation of SWTs at high altitude (Pourrajabian et al., 2014), where the air density reduction can substantially reduce Re (up to more than 10 %), bringing it to those values where the effect of transition is more relevant. In this sense, it has been shown that the correction methods proposed in the standards (wind or power correction) often fail in correctly representing reality.
The influence of blade roughness, due to insect accumulation in dry areas or leading-edge erosion for example, also differs between SWTs and large turbines. Holst et al. (2016), for example, discuss the effects of roughness by comparing lift polars of low-Re airfoils to high-Re utility-scale wind turbine airfoils. Experiments in that study revealed lift deficits of up to 50 % and confirmed the importance of a proper profile selection. In addition, simulations showed that roughness can reduce AEP by up to 50 %. Furthermore, roughness sensitivity could lead to premature separation, especially near the blade root that is characterized by highly three-dimensional flow (Bangga et al., 2017). Thus, employing airfoils with good aerodynamic characteristics for the specific blade span and expected operational regime is compelling.
4.1.2 Control
Large wind turbines have yaw-drive mechanisms to align the rotor to the mean wind direction. Such devices are much more expensive for SWTs, especially for small rated power values (10 kW or less): in these applications, some form of free or passive yaw has been typically used. The most popular options are then a tail fin or the use of a downwind rotor, e.g., SD Wind (SD Wind Energy, 2022), Skystream (XZERES Wind Turbines, 2022), Carter Wind (Carter Wind Energy, 2022), and others. The downwind configuration solution is experiencing a revival for some specific applications in utility-scale machines, especially for floating offshore applications (Bortolotti et al., 2021). For larger turbines, the same yaw-drive technology in use for utility-scale machines is instead being increasingly applied.
Another control actuation commonly found in large wind turbines is the blade pitch system that can both regulate power and slow down the rotor for overspeed protection by aerodynamically changing the blades' angle of attack. However, pitch control is often not available at the scale of SWTs for economic reasons. Designing and manufacturing a fail-safe pitch system within the physical constraint of a small hub and the capital cost constraints needed to keep an overall low LCOE are one of the biggest challenges for the SWT industry. The need for a redundant brake mechanism, in fact, translates into either having independent pitch actuation (as for the utility-scale machines) or an oversized mechanical brake that could bring the rotor to a stop in the case of grid connection failure and associated runaway rotor. Both options have proven to be prohibitively expensive in the DWT space thus far, and more economical solutions for avoiding overspeed that have been widely adopted include stall regulation and/or rotating the rotor out of the wind direction via a furling mechanism. An attractive option for smaller SWTs is “electromagnetic braking” by shorting the generator output (McMahon et al., 2015). This obviates the need for a mechanical brake. Several current commercial SWTs such as the Bergey XL 15 (Bergey Wind Power, 2022) use this cost-reducing strategy. Regarding active pitch, however, a recent study (Papi et al., 2021) highlights how the use of advanced pitch-to-feather control strategies can significantly improve the performance of SWTs through more effective power regulation. It is speculated that the aerodynamic power coefficient could be improved significantly to reach CP≈0.5, which, together with simpler and therefore more accurate aerodynamic modeling performance, could then justify the higher cost of pitch actuation in a SWT. Also, another study (Papi et al., 2022) showed that a pitch control strategy can reduce peak loads in extreme conditions, thus potentially leading to lighter and more cost-effective blade designs. Blade pitch can also help with start-up torque at low wind speeds, whereas a fixed-pitch rotor must rely on its low wind speed and high angle-of-attack performance to overcome the resistive torque of the drivetrain and generator. A quick starting characteristic is crucial for SWTs because they tend to have more start and stop events compared to their larger counterparts due to higher turbulence levels and lower average wind speeds.
Due to the aforementioned technical and economic issues, stall control is still largely used in SWTs. This latter strategy, however, generates peak loads on the blades that are relatively much higher than those seen in utility-scale machines because the pitch cannot be varied in parking conditions. In addition to the lower efficiency in terms of regulation across the functioning range, the stall control strategy inherently introduces difficulties in predicting the aerodynamics of SWTs because three-dimensional flow aspects and unsteady characteristics make the near- and post-stall regions of the polar curves difficult to capture in aerodynamic models, especially in engineering methods (which can be economically used during the design phase). These difficulties are further compounded in the case of passive-yaw configurations. Skewed inflow and dynamic wake physics are still a topic of research in the wind energy community (Ning et al., 2015; Schepers et al., 2021) and in the case of SWTs, given their more dynamic nature (e.g., higher yaw rates, rotational velocities, and passive yaw), introduce further nonlinearities and unsteadiness in the rotor and tail induction fields, rotor aeroelasticity, and overall turbine response.
4.1.3 Structural design and (scarce) aeroelasticity modeling
In the field of large wind turbines, the use of aeroelastic simulation tools has been a consolidated practice for years (Bottasso et al., 2006) and is required for the certification of the machine itself. In the case of SWTs, the common approach up to a few years ago was to build stiff blades characterized by high safety factors in the structural design in order to avoid significant aeroelastic effects. As discussed, however, somewhat larger SWTs (from about 60 kW and up) are now practically equal in complexity to large wind turbines (e.g., they usually have a variable-speed pitch-torque control system and an active yaw control system and, because they often have a single actuation system for the blades, for safety they require mechanical brakes for the emergency stop). In addition, they are often designed for low to medium wind speeds, so the blade is very large (for the 60 kW blades, it is possible to reach 14–15 m). The experience of many authors of this paper, who had the opportunity in the last decade to collaborate with the small or medium enterprises (SMEs) producing these rotors (IEA, 2014), shows that the use of aeroelastic simulation tools is important to ensure a quality, safe, and economically sustainable project but is still very uncommon. One of the few aeroelastic analyses of a 5 kW turbine is described by Evans et al. (2018). The less frequent use of aeroelastic models in industry is due mainly to a lack of experience of these companies, which very often come from other industrial fields (e.g., producers of boats or heavy mechanical systems) where other design tools such as finite-element codes are primarily used. These companies are often not aware of the availability of good aeroelastic tools in the public domain (e.g., OpenFAST from the National Renewable Energy Laboratory, NREL; NREL, 2022). Finally, another limitation to the use of aeroelastic simulation tools for SWTs is connected to the lack of easy-to-handle post-processing tools. In fact, standards require the designer to simulate the wind turbine in power production for different wind values and gusts, but also for a variety of other operating conditions (starting phase, normal and emergency shutdown, transportation, faults, etc.). This results in a few thousand simulations that must be analyzed to extract maximum loading values for the various sub-components of the wind turbine, including blades, tower, and drivetrain, but also pitch and yaw, air gap in the generator, supports, bearings, brake discs, foundation, etc. In turn, these loads, together with fatigue loads and stress range cycles, need to be delivered to the different partner manufacturers. This process therefore requires automated tools and specific skills that are not always available outside academia or large manufacturers.
4.2 Innovative concepts and vertical-axis wind turbines
Whereas conventional horizontal-axis wind turbines (HAWTs) have become the reference technology for all scales up to 15 MW or higher, alternative concepts are still being proposed for SWTs (Damota et al., 2015).
A popular modification to small HAWTs is to enclose the rotor with a diffuser to induce more airflow through the blades and thereby increase the power output. This produces a diffuser-augmented wind turbine (DAWT), some examples of which are shown in the first row of Fig. 10. Adding a diffuser is indeed more attractive for small turbines than large ones because the additional structural and wind loads on the latter are likely to be excessive. A diffuser is a relatively simple modification to basic turbine design, but it is still not clear how to optimize the diffuser and rotor to extract maximum power and whether the extra power is worth the cost of the diffuser. An interesting review demonstrating the enduring fascination of the concept has been recently reported by Bontempo and Manna (2020). There are other advantages of DAWTs: the diffuser may contain a blade if it detaches from the rotor and probably make the turbine quieter and less harmful to birds. These may well be significant advantages for DAWTs in urban settings (Micallef and van Bussel, 2018). At least two companies have recently commercialized small DAWTs, as showcased by Evans et al. (2020) and Visser (2020). They have found a wide range of applications from remote communication systems where the turbine partners a photovoltaic system to more common stand-alone systems.
Beyond other pioneering studies on novel energy-conversion systems such as DAWTs, most of the research on novel SWT architectures has been directed to vertical-axis wind turbines (VAWTs) (Aslam Bhutta et al., 2012).
Among these, drag-type rotors like the Savonius turbine (Akwa et al., 2012) are relegated to very small applications due to their low power coefficients and high mass-to-power ratio. Nevertheless, thanks to their simplicity, Savonius VAWTs are still considered suitable in remote rural areas (e.g., the first electrification of developing countries) (Senthilvel et al., 2020).
On the other hand, despite a long absence from research agendas after the first generation of research culminated in the mid-1990s, lift-driven VAWTs (or Darrieus concepts) are being increasingly studied (Bianchini et al., 2019). Despite popular claims, the new understanding of the complex aerodynamics of Darrieus VAWTs achieved in the last decade has proven that these machines can achieve power coefficients comparable to those of small HAWTs (Bianchini et al., 2015a). More importantly, VAWTs present several advantages for small-scale applications, namely an intrinsic insensitivity to wind direction, misaligned flows (Bianchini et al., 2012), or turbulence (Balduzzi et al., 2020) as well as lower acoustic noise generation associated with generally lower tip speeds (Möllerström et al., 2016). The advantage of low blade speed, however, is offset by the need to have a physically bigger, and therefore more expensive, generator and mechanical brake. In addition, VAWTs allow for a variety of design solutions, which are considered aesthetically pleasant by the public and thus also suitable for integration in buildings (Dayan, 2006) or with other infrastructure such as streets (Khan et al., 2017). Therefore, a variety of small manufacturers entered the market either with downscaled VAWTs or with alternative concepts specifically intended for use on rooftops (Mertens, 2003). Among others, one concept that is receiving increasing attention is the exploitation of the so-called Magnus effect, which is a phenomenon associated with a solid object spinning in a fluid. This concept has been studied for both HAWT (e.g., Sedaghat, 2014) and VAWT (Shimizu, 2013) designs. The potential advantage of these solutions lies in the fact that they can operate in relatively low winds (Bychkov et al., 2007), thus covering a range of winds not typically exploited by conventional wind turbines.
For very small VAWTs (<3 kW), recent designs chose high-solidity rotors, i.e., rotors with larger chord-to-radius ratios, mainly because of the need for sufficiently long chords to increase the aerodynamic forces and the Reynolds number. Based on recent analyses, this aerodynamic solution seems to provide unprecedented specific power values for small rotors (Bianchini et al., 2015a). On the other hand, these models showed the significant shortcomings of existing simulation models (Bianchini et al., 2019), which were resolved largely by the new understanding of the role of flow curvature effects (Bianchini et al., 2015b, 2016). Renewed research efforts are being undertaken to determine whether VAWTs can fit the scope of distributed energy production in complex installation areas, as testified to by the recent EU project (Aeolus4Future, 2022). Parallel to these research trends, VAWTs are being investigated for deep-water offshore applications with floating substructures (Paulsen et al., 2013). The more favorable structural loads of the VAWT architecture and the possibility of placing the generator on the floating platform – and thus lowering the system's center of mass – may lead to smaller floating supporting structures, better control, reduced logistics and capital cost, and ultimately a lower LCOE (Arredondo-Galeana and Brennan, 2021). In the realm of offshore SWTs, floating VAWTs could be deployed in some niche applications like integration with beacons at the entrance of a port. A recent book, for example, explores the relationships between small wind and hydrokinetic turbines (Clausen et al., 2021). Overall, despite the benefits that could be provided by VAWTs in some applications, they still lack both theoretical understanding and technical maturity compared to HAWTs. Whereas the theoretical gap could be overcome by modern investigation techniques, gaining the same level of industrial maturity as HAWTs seems out of reach at this time. The potential impact of funded research projects at a national or a broader level could be relevant in proving the real prospects of the technology and driving their development.
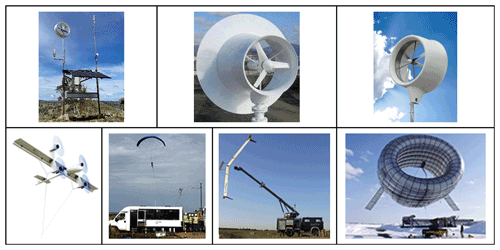
Figure 11Currently proposed DAWT (upper row) and AWE kite archetypes (lower row). First row (from left to right): the Diffuse Energy Hyland 920 diffuser-augmented turbine as part of a remote power system for a communication tower (the 200 W turbine has a maximum diameter of 0.92 m; photo supplied by Dr Joss Kesby), HAWT with flanged diffuser (Ohya et al., 2008), DonQi urban windmill (photo credit: DonQui Global). Second row (from left to right): cross-wind or fly-gen (a.k.a. drag-power) devices (image credit: Windlift), ground-gen (a.k.a. lift power) flexible kite (photo credit: KPS), ground-gen rigid kite (photo credit: Ampyx Power), aerostat ducted wind turbine (photo credit: Altaeros).
Other touted devices that, at least on paper, have demonstrated the potential for low LCOEs are airborne wind energy (AWE) kites (Fig. 11). They propose to extract wind power either through cross-wind by using lift and therefore flying faster than the wind speed and carrying turbine generators on board (fly-gen) or by pulling and unwinding a tether connected to a generator on the ground (ground-gen). Other concepts expect to take advantage of very-high-altitude winds via buoyant aerostat ducts. None of these concepts has thus far demonstrated an economically viable power curve or has shown successful size scalability in real-world settings. Yet, there is significant momentum in AWE research, with some pioneering industrial products already on the market, and the applicability of these devices will likely be in the distributed wind space. While it is difficult to assess the real costs and LCOE of AWE kites due to their nascent stage, the key advantage they provide is the absence of hefty and expensive support structures while maintaining a generous rotor swept area. This would have favorable effects on the balance of station costs that have plagued the DWT industry to date; this is the main reason why they are mentioned here as potential actors of the small- and, more likely, distributed wind market of the future. The challenges these devices face are numerous, however, from flight safety and reliability to the efficiency of power generation and from the issuing of design and certification standards to their acceptance by public and aviation authorities, and only future deployments will indicate whether they can compete in the DWT market.
4.3 Turbine archetypes and design standards
Unlike the typical utility-scale, three-bladed, upwind machines, SWTs have not coalesced into a dominant archetype, with many different layouts still being offered on the market. The variety of archetypes (upwind vs. downwind; HAWTs vs. VAWTs; two vs. three or more blades; even one like PowerHouse Wind, 2022; active pitch vs. stall-controlled; etc.; see Figs. 12 and 13) creates a challenge for the design standardization and certification of SWTs (Damiani et al., 2022). This challenge is made stronger by the intention of standards to facilitate the development of SWTs at relatively low cost; the “simplified loads methodology” (SLM) in IEC 61400-2 for small horizontal-axis turbines is the main example.
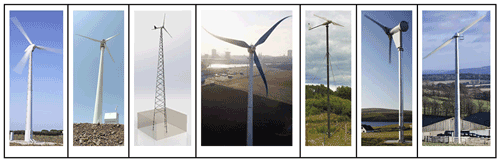
Figure 12Common HAWT archetypes found on the current DWT market. From left to right: upwind, active pitch and yaw (photo credit: Tozzi Nord); upwind, stall-controlled and active yaw (photo credit: Eunice); upwind, stall-controlled and tailed passive yaw (photo credit: NREL pix 49511); downwind, stall-controlled and passive yaw (photo credit: Eocycle – formerly XANT); upwind, tailed passive yaw, furling (photo credit: Bornay); downwind, pitch- or pitch-coning-controlled, passive yaw (photo credit: SD Wind, formerly Proven); downwind, stall-controlled, passive yaw and teeter (photo credit: Ryse Energy, formerly Gaia).
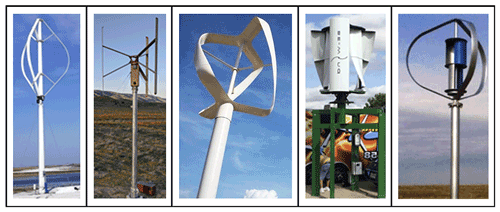
Figure 13Common VAWT archetypes found on the current DWT market. From left to right: Darrieus Troposkien (photo credit: Chava Wind), H-Darrieus (photo credit: Xflow Energy), H-Darrieus with helix shape (photo credit: PRAMAC), Savonius (photo credit: BE Wind), combined Savonius–Darrieus (photo credit: HiVAWT).
The lack of dominant archetypes complicates the development of standards and design tools for SWTs, resulting in a reduced refinement and robustness for all the archetypes as their counterparts for utility-scale machines.
Type certification for large wind turbines, which primarily follows IEC 61400-1 (IEC: International Standard, 2019a), are typically performed by large companies with extensive design teams who can afford multidisciplinary development departments, highly refined turbine-specific aeroelastic models, high-performance computing, and testing facilities. The much smaller companies that manufacture SWTs do not have access to such resources. For example, even though estimating the loads according to the design standards would require only a few hours of computational time with state-of-the-art engineering codes, these codes require resources and staff with very specific skills to be utilized correctly, and correlation to archetype-specific load measurements is needed to demonstrate confidence in the results.
The IEC standard for wind turbine design also includes the IEC 61400-2, dedicated to SWTs (IEC: International Standard, 2019b). It covers all mechanical and electrical subsystems and includes support structure and foundations as well as the grid connection (including power electronics where applicable). The section applies to wind turbines with a rotor swept area smaller than or equal to 200 m2 generating at a voltage below 1000 V AC or 1500 V DC and covers both grid-connected turbines and off-grid applications. IEC 61400-2 allows for a number of simplifications to the design and analysis of turbines, including the use of the SLM and a reduced number of design load cases (DLCs). However, the SLM currently captured in the standards is more than double the safety factor for ultimate loads, which may make the SLM process easier to use for the design phase and helps keep costs low but will create a heavier and more expensive product, which results in turbines that may not be competitive on the distributed generation market. By their nature, use of the SLM normally leads to a safe but over-designed product. For example, for very small SWTs, the critical DLC includes the gyroscopic loads on the blade roots and main shaft under yaw; however, in general terms our knowledge of the yaw behavior of SWTs is poor across the range of turbine configurations. The magnitude of the gyroscopic moment is given by a simplified load equation involving the blade moment of inertia, the blade angular velocity, and the yaw rate. Although the equation captures in principle the actual physics responsible for the gyroscopic moment (Wilson et al., 2008), the safety factor for this load is 3. The SLM stipulates the maximum yaw rate as a function of rotor area and then requires this to be multiplied by the maximum blade angular velocity. The limited information available on SWT yaw behavior (e.g., Wright and Wood, 2007, and Bradney et al., 2019) suggests however that high blade speed correlates with low yaw rate, but this is not used in the SLM.
As an alternative or if the turbine configuration is not covered by the SLM equations, then alternative simulation modeling or load measurements can be used, which may result in a more optimized final design. Additionally, many aspects of the turbine aeroelastic response that are missed by the SLM approach could, in principle, be captured by higher-fidelity aero-servo-elastic modeling. However, using aeroelastic modes for the design and certification of SWTs is challenged by the fact that while models are well tuned for active-yaw and active-pitch HAWTs, they are less validated for stall-controlled, passive-yaw HAWTs and progressively less so for non-traditional archetypes (e.g., teetering hubs, VAWTs, AWE kites) (Damiani et al., 2022).
Regardless of the initial design approach, the reliability of SWTs is guaranteed through duration testing, where at least 6 months of operation is required during which minimum operation at high winds is stipulated. The standard requires comprehensive documentation of the testing. In addition to the whole turbine testing, specific component tests are prescribed.
Some SWTs come with design variations. To limit the demands on the original equipment manufacturers, a full design evaluation is only required on a selected representative configuration. Other variations need only be evaluated or tested in the ways in which they are different from the representative configuration. Guidance on the conformity assessment, however, is rather limited in the design standards, and this has been lamented by the industry as an obstacle to the commercialization of new fleet products or in the case where changes to the product line, such as the use of a new manufacturing process for an individual component, may open the product to extensive work to maintain certification.
For power performance testing, IEC 61400-12-1 includes a normative Annex H specifically for the power performance testing of small turbines. This reflects the fact that testing according to the general standard using 10 min averages, where the complete wind speed range must be covered by sufficient data to minimize statistical uncertainty, can be a time-consuming and expensive process. To get around this difficulty, testing SWTs involves using 1 min averaged data, thus considerably reducing the time needed for testing, but also because 1 min averaging extends the frequency distribution of wind speed, making high-wind-speed data points more common.
The SWT test standard also covers battery charging. Procedures are prescribed that minimize the influence of the specific battery configuration and condition (state of charge). SWTs that use inverters for grid connection are tested together with the inverters, and the power measured is the power available to the consumer. Most SWTs lack a clear definition of rated power and wind speed; instead, a reference power is defined as the averaged power in the 11 m s−1 bin.
Comparisons of 10 min averaged power curves with those based on 1 min averaged data have been presented in Elliott and Infield (2014). Fortunately, the systematic distortion of power curves due to so-called errors in bins was found to be small. However, if the 1 min power curve is used together with a 10 min averaged wind speed distribution, then an error of 1.15 % in the estimated annual energy yield is shown in the study. To avoid this, the energy yield calculation should ideally be based on 1 min averaged wind speed data. Because the calculation of turbulence intensity depends strongly on the averaging period, it would be better for this aspect of site characterization to be based on 10 min data, even if the power curve itself is based on 1 min data as prescribed in the SWT test standard.
From this overview, it is clear that the SWT design standards can be substantially improved on multiple fronts, from the design requirements to the testing, validation, and conformity assessment. The preparation of a new edition of IEC 61400-2 has just started. It is anticipated that the SLM will be improved and there are likely to be further divisions of SWTs depending on size, power rating, and archetype. Rotor swept area combined with rotor orientation, type of power regulation, and type of yaw control, for example, can lead to a matrix organization to determine requirements for design load calculations, structural verification, and numerical model validation that would also depend on the experience of the numerical codes with the different turbine archetypes (Damiani et al., 2022). A rigorous differentiation of certification requirements that depend on the turbine configuration appears as the most urgent need in the design standards to arrive at a substantiated assessment of the load categories for SWT. All these desired changes should make the standard significantly more useful to the manufacturers and end-users of SWTs.
The transition to a more distributed production of energy, combined with the evolution of grids toward “smart” architectures and control logics, which are more resilient, is leading to an evolution in the way electric services are being provided. Distributed solar has already demonstrated wide-scale acceptance (IEA, 2019) in this more distributed energy system. While SWTs have yet to reach general acceptance, they can play a similar and supporting role. To become more commercially accepted, marked cost and performance improvements are needed. Although significant reductions can be achieved through understood technology improvements, additional innovations are needed that lie beyond our current knowledge of critical physics, with particular reference to turbulence, applicability of design assumptions, and the existing modeling and simulation capabilities. Cost reductions that have been demonstrated within the distributed wind industry show that with adequate investment, significant hardware cost reductions are possible (NREL, 2022). However, the generally low investment in small wind technology research and a lack of consistent and substantial incentive programs have relegated SWTs to niche applications with minimal economies of scale. The success of solar PVs, which has benefited from significantly more incentive programs than SWTs on the distributed generation market, demonstrates the importance of stable incentive programs of this type in achieving market share.
Among other considerations, a recurring research gap noted in many studies is that SWTs often fail to achieve predicted or published AEP. This is likely due to a host of considerations such as overly optimistic resource assessments, rotor underperformance at low wind speeds and during high turbulence, or poor final turbine siting. The two flow features, rotor underperformance in low winds and/or turbulent winds, are typical of installations on top of short towers and in proximity to natural or artificial obstacles.
Based on the status of the technology described in the previous sections, the present study identifies five specific grand challenges (GCs) that must be overcome to spur SWT development and meet the globally expected demand for a wider variety of distributed energy resources. The grand challenges are visually presented in Fig. 14, which represents the graphical abstract of this study. To address these challenges, a number of unknowns and gaps to be filled are identified (Sect. 5.1). Future enablers (Sect. 5.2) are also suggested as the keys to elevate SWTs to a more mature technology.
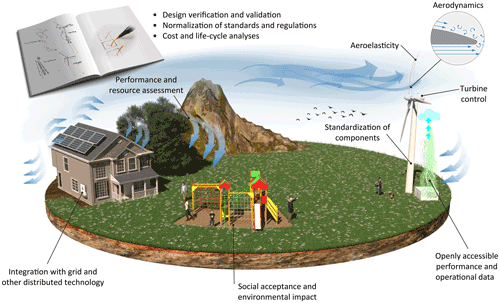
Figure 14Visual synopsis on how the key enablers identified in this study may help tackle the five grand challenges for SWT technology.
Grand challenge 1 – improve energy conversion of modern SWTs through better design and control, especially in the case of turbulent wind
Because SWTs are typically installed in areas with lower (less energetic) and more turbulent wind resources, maximizing the amount of energy that can be harvested from the wind (i.e., maximizing the SWT's capacity factor) while ensuring turbine longevity and survival through infrequent high-wind events is critical. Many wind turbines have been shown to underperform in comparison to performance based on simulations. This is due to a combination of simulation tools that overpredict turbine performance, driven largely by the simplification of flow features that these turbines are subject to and the actual complexity of the oncoming flow. In particular, better insight into the impact of turbulence and gustiness on turbine performance is needed. This can be achieved with a combination of more detailed testing data and more advanced design tools capable of modeling the complex blade–flow interactions. Additionally, advancements focused to exploit oncoming winds more effectively, including the use of taller towers or the design of lower specific power rotors to better exploit lower winds, must be continued.
To this end, it is now possible to undertake multidimensional blade design to minimize starting time, blade mass, and noise while maintaining good power extraction and adequate blade strength (e.g., Sessarego and Wood, 2015). Among other aspects, blade mass is paramount because it correlates with manufacturing costs and blade inertia. In turn, the ability of a turbine to start quickly to maximize power extraction at low wind speeds depends on the inertia, as do the gyroscopic loads discussed above, giving this feature an importance that it does not have for large turbines. SWT blades are naturally stiff and benefit from additional centrifugal stiffening at high angular speeds, so further optimization should be possible. Because the gyroscopic loads are major fatigue (as well as ultimate) loads, an improved understanding of turbine yaw behavior should allow more optimized turbine design. This should be seen as the key challenge in the modeling of complex unsteady aerodynamics in the presence of passively yawing rotors, either downwind of the tower or yawed by tail fins.
Grand challenge 2 – improve prediction and reliability of long-term turbine performance despite limited resource measurements
Going beyond accurately optimizing and then predicting the power production of a SWT based on specific wind characteristics, for SWT projects to receive financing, the industry must be able to accurately predict turbine power production over the full life of the project. This accuracy of long-term performance prediction is needed to lower the risk associated with SWTs as seen from the perspective of consumers, insurers, city planning professionals, project financiers, and regulators.
Long-term performance prediction is built on a number of factors, primarily the turbine performance characteristics combined with accurate wind resource estimation and any changes due to local obstacles over the life of the project. Additionally, turbine availability due to mechanical, electrical, and weather conditions at the specific site must be considered in addition to long-term turbine reliability and performance degradation. Although not directly related to turbine design, the availability of spare and replacement parts, approved turbine repair technicians, company warranty commitments, and specific turbine location relative to all these factors will also drive long-term power generation.
Beyond corporate credibility of the installer and turbine manufacturer, long-term production reliability can be categorized in two main areas, i.e., wind-driven resource performance and turbine reliability. Discussions with the SWT development community have identified several key challenges to conducting low-cost but accurate resource assessments (Fields et al., 2016). These include the availability of low-cost anemometer and remote sensing; the lack of high-quality mesoscale-modeled wind speed data at heights typical for SWT installation; and the availability of validated and easy-to-run obstacle modeling to understand the potential impacts of local obstacles on the wind resource, especially in complex terrain (Duplyakin et al., 2021). Once an accurate assessment of the resource at the site in question is available, typically for a model year, additional parameters such as the conditional changes over time, growth of obstructions such as tree cover, and potential weather-driven availability reduction will need to be added. Tools making resource recommendations must also be verified, providing confidence to installers, consumers, and the financial community (Tinnesand and Sethuraman, 2019).
Many turbine manufacturers can point to turbines that have operated reliably for many years, but to be successful in today's market, a long turbine life must be balanced with economic viability (see GC 3). The second element of this challenge is developing methods that prove that SWT technology will operate reliably over the turbine's design life. For example, the SLM of IEC 61400-2 mandates a simple determination of the total number of fatigue cycles experienced by the blades of a SWT. Because of the higher angular velocities of SWTs, the fatigue cycles for SWT blades are on the order of 100 times the number for large turbine blades. Despite this, the standard does not mandate fatigue tests for small blades, and there is not strong operational evidence that fatigue is a major issue for most SWT blades. On the other hand, the fatigue load case in the SLM appears to be very conservative (Evans et al., 2021), which increases turbine costs and may not identify the likely locations for fatigue-driven failures in operating turbines. Addressing this challenge will center on developing a better understanding of the likely failure modes of SWTs, improved knowledge of the role of yaw behavior in generating gyroscopic fatigue loads, the development and use of validated design tools that address the likely failure modes, and standards and certification processes to help ensure that turbines operate reliably over their design life. This improved understanding and these improved tools will also need to be validated for the wide array of SWT configurations, including free and damped yaw. For the future SWT market to be successful, this effort will need to be accepted by large-scale financial organizations, which are driving investment in distributed-scale power generations.
Grand challenge 3 – improve the economic viability of small wind energy
For a SWT to be economically successful, it must provide reliable power at a cost comparable to other similar technologies, such as distributed solar PVs, and be acceptable by the market. A reduction in the LCOE can be achieved by balancing better capacity factors (see GC 1) and reducing unit installed cost. Reductions can come from design optimization; using new materials and manufacturing techniques; developing standardized solutions for components that can be applied across multiple turbine models, such as power inverters; and promoting or incentivizing production economies of scale. Moreover, improvements in installation techniques, reducing the cost of foundations, and other related balance-of-station costs will be needed.
Many strategies have been considered to lower the cost of turbine hardware, with some solid success in specific turbines. A balance must however be made to optimize lower turbine costs, which is largely driven by reducing turbine materials and ensuring successful operation over the turbine's designed life (see GC 2). This optimization must also be balanced with international standards, which may drive up turbine system costs through the SLM. For example, tools used to predict the impact of turbulence on component fatigue while load-reducing turbine control, such as adopting pitch regulation typical in larger rotors, can also help ensure long-term turbine operation while optimizing turbine material needs. The expanded use of validated aeroelastic design tools will also become more critical to help optimize this balance of reliability and low cost.
Recent increases in commodity prices as well as supply chain interruptions are causing increased costs for most SWT manufacturers. Although some of these challenges could be overcome with expanded manufacturing, leading to larger economies of scale and increased industry purchasing power, expanded research into material substitution for high-cost or hard-to-access materials would help lower and stabilize turbine manufacturing costs. Expanded work in aligning component supply across multiple SWT vendors may also help address some high costs and lower component availabilities, especially if supply chain disruption becomes more common.
Overall, a lower LCOE will also help communities access SWT technology (see GC 5), allowing wind technology to play a more active role in addressing issues of energy poverty and energy access while reducing the needs for financial incentives, which typically favor wealthier consumers.
Grand challenge 4 – facilitate the contribution of SWTs to energy demand and electrical system integration
Having more distributed wind in the energy mix could contribute significantly to energy justice and power system decarbonization. The ability of distributed wind to provide low-cost energy close to consumers with a higher energy density and smaller footprint of other distributed technologies provides an important tool to achieve low-carbon-energy-system goals. Additionally, SWT lends itself to local development and deployment. Many developing countries, for example, are more likely to have the capacity to build an indigenous SWT than the solar cells necessary for a PV system. If the fulfillment of GC 2 is pivotal to make investment in SWTs attractive to many more customers, the introduction of many SWTs to the grid is non-trivial, although the expanded use of distributed energy resources will generally require improved energy control and likely distribution system enhancements. The highly discontinuous power production of SWTs, which can be hampered by some energy grids with restrictive ramp rate requirements or that are particularly susceptible to faults, requires additional thinking. SWT technology must not only advance to meet the rapidly evolving grid code requirements for distributed generation (Preus et al., 2021), but the value they may add to grid reliability and resilience should be highlighted and monetized. Standardization through improved future revisions of IEC 61400-2 will bring the industry to a similar technical level for remote control and safety in the smart grids of tomorrow. Due to their distributed nature, the ability of SWTs to assist load reduction or load shifting in behind-the-meter applications, especially in markets that are expanding electrification in an effort to reduce carbon production, must be fully assessed and articulated. The ability of SWTs to complement distributed solar PV technologies will allow improved cost and operability to high-renewable-contribution systems for both behind- and in-front-of-the-meter applications (Reiman et al., 2020), especially with expanded consumer electrification for heating and transportation. The role of energy storage, and particularly of batteries, will be important not only for wind, but in general for enabling the transition to a smart-user-based grid paradigm.
The increasing interconnection requirements of all distributed generation, including in many cases two-way communication with grid control systems, require new SWTs to be more responsive, such as providing low-voltage ride-through, more advanced grid services, and potentially direct grid support. Additionally, with these expanded communication needs, additional cybersecurity considerations will be required of future SWT technology.
The role of SWTs, however, should not be limited to grid-connected installations. Large global markets for isolated energy systems and the provision of energy access as well as off-grid energy services such as ice making, water pumping, irrigation, or direct heat could further increase the market potential of the technology and again aid in global decarbonization by offsetting typically fossil-based means of providing these services.
Grand challenge 5 – foster engagement, social acceptance, and deployment for global distributed wind markets
Engaging communities, societies, and regulatory authorities is key for SWT development. Actions need to be taken to enhance the social understanding of SWTs and to provide evidence that modern turbines are expected to be significantly more efficient than their predecessors. Turbines must also be designed and deployed while taking into account their installation in proximity to people and within communities, with a clear understanding of their social and environmental impacts. Expanded research on community-based impact, such as ice throw and safety setbacks, needs to be carried out, leading to improved standards and guidelines for turbine installation. While some virtuous examples have been presented recently (e.g., the RELY COST Action; Roth et al., 2018; US DOE WindExchange, 2022) additional programs are seen as key enablers to increase awareness and acceptance about the technology.
Political and regulatory actions, especially if coordinated among countries on a larger scale, must be enhanced to allow deployment of the technology in a more effective way. Common regulatory and permitting requirements, based on science and modern understandings of potential impacts, are needed to streamline development timelines and reduce costs. Incentives, standards, and promotional policies should also be aligned. This is needed not only in the context of governments, but also within multi-lateral nongovernmental organizations, development banks, and foundations. For example, the creation of equal incentives across nations, including a clearly defined timeline for them to stay in place, is needed to encourage investment and the creation of economies of scale that will be important to sustain each of the other grand challenges.
5.1 Unknowns and knowledge gaps
Associated with the grand challenges identified above, the following Sects. 5.1.1–5.1.6 identify specific areas that will need ongoing global focus if SWT technology is going to be successfully developed to support long-term global needs for power generation to meet local loads. In particular, these sections identify the main unknowns and knowledge gaps that need to be addressed to allow the five grand challenges to be resolved.
5.1.1 Higher LCOE due to a lack of an economy of scales, resulting in high balance-of-station cost
As discussed, the total global installed cumulative small wind2 capacity was estimated to be about 1.8 GW as of 2020 (Orrell et al., 2021). In contrast, an estimated 19 GW of residential solar PVs was installed worldwide in 2020 alone (IEA, 2020). The difference in installed capacities is driven by a number of factors, including intrinsic siting requirements, availability of incentives, market acceptance, and differences in costs. High deployment costs are driven by a number of factors. In particular, a lack of economies of scale and high balance-of-station costs.
Currently, most manufacturing of SWTs is conducted in small plants using batch processes because of the relatively small manufacturing volume and limited corporate cash flow. Small commercial volumes increase component costs, reduce purchasing power, and in times of restricted supply chains necessitate the ability to substitute components if traditional ones are unavailable. Each of these items increase cost and complexity and reduce the reliability of SWT products. As has been clearly demonstrated within the solar industry, large efficiencies and cost reductions can be gained across the SWT industry by significantly increasing production (Pillai, 2015). A transition to serial production, large-volume component purchasing, and advanced manufacturing techniques will significantly reduce the equipment costs for small turbines while also improving product quality control. An effort to greatly expand manufacturing capacity should be placed against an industry desire to continue using small plants that are located in the communities they are serving to meet energy justice, diversity, local development, and product reliability while also reducing climate impacts associated with global shipping.
Balance-of-station costs include all costs of a turbine system outside of the wind turbine and tower equipment and can represent up to 60 % of a small wind project's total installed cost (Orrell and Poehlman, 2017). These costs typically include customer acquisition; zoning, permitting, inspection, and incentive application; engineering and design; transportation and logistics; foundation design and installation; electrical infrastructure; turbine and tower installation and erection; taxes; and overhead and profit. Zoning and permitting costs in particular can be burdensome for small wind. For example, at one point it was reported that potential customers in the Republic of Korea needed written approval from neighbors within a given radius to install a SWT (Kim, 2018).
Although not typically a direct one-to-one substitution, the generally lower cost, in great part due to governmental incentives, and easier siting of solar PVs gives it a competitive advantage over small wind. From 2008 to 2012, the drop in the overall installed cost of PV systems was mainly due to the drop in cost of crystalline silicon. Since 2012, installed costs have continued to drop due to decreases in other costs, focusing on greatly reducing balance-of-station costs (Barbose and Darghouth, 2015). In addition, as demand for solar PVs increases, production of PV modules can enjoy the benefit of economies of scale, helping to further decrease installed costs.
5.1.2 Uncertainty in power curves and local wind conditions, resulting in poor estimations of AEP
The estimation of the AEP of a wind turbine has two main components: the power curve of the wind turbine and the knowledge of the wind conditions on the site. Nordic Folkecenter's Catalogue of Small Wind Turbines (8th edition) lists 302 types of wind turbines with a rated power below 50 kW, only a fraction of which have independently measured power curves (Nordic Folkecenter for Renew. Energ., 2016). This is in stark contrast to large wind turbines, where the vast majority of turbines have independently measured power curves.
Over the past decades, there have been multiple facilities developed for SWT testing, some of which are still in operation, providing the performance testing needed to increase the number of SWTs with independently measured power curves. However, the IEC 61400-2 is still the most credited reference to standardized performance measurements, but some discrepancies still exist with other references, and some aspects are still not completely covered. Further improving this standard could contribute significantly to closing the gap between small-scale and large-scale wind turbines. Only when a standard is applied to all these aspects will wind turbines be reliable. Generally, PV modules, inverters, and ancillary systems are more standardized than SWTs, and this is one of their keys to lower costs and market success.
Because tower heights are commensurate with rotor diameter, SWTs are placed on relatively short towers. Furthermore, tower heights are often restricted below their optimal values by local planning regulations. Due to wind shear, low towers result in lower mean wind speeds and therefore lower production. As discussed, SWTs are also strongly affected by installation at high altitude, where the reduction in air density leads to low Reynolds numbers and in turn to a lower aerodynamic efficiency. Furthermore, the wind flow for SWTs is more likely to be perturbed by nearby obstacles. This has two important effects: (1) the wind pattern can change over very short distances, making the micrositing of SWTs complex, and (2) the wind is likely more turbulent. As a result, even when power curves have been independently measured at a certified test site, those power curves may not be representative of real-life performance at the installation site.
The uncertainty in power curves and local wind conditions leads to considerable uncertainty in the estimate of the AEP.
In absence of new remote-sensing- or model-based assessment technologies, the way to reduce uncertainty in the characterization of local wind conditions is to take on-site wind measurements. However, site assessment through on-site measurement is often expensive in relation to the installed cost of SWTs and their generation potential. Deploying instruments for measurement is also far more expensive and more time-consuming than using model-based approaches to estimate a wind resource, which has led to limited uptake in the use of on-site measurements for small wind (Tinnesand and Sethuraman, 2019). Although expanded consideration of remote sensing and high-fidelity, model-based resource assessment techniques are being developed, which may prove reliable for energy production estimation, these are likely to be insufficient in areas with complex terrain, especially because the SWTs are close to the ground. In these cases, a site assessment is necessary for the project to be successful.
5.1.3 Intermittent incentives and regulations between countries
Incentives applicable to small wind can include net-metering, FITs, other types of production-based payments, grants, rebates, and tax credits. Regulations that affect small wind can include government renewable energy goals and mandates, interconnection standards and rules, and utility programs and interconnection rules. Both incentive programs and regulations vary widely across countries and utilities. Incentive programs can vary with respect to the amount and type of funding they provide, what types of projects are eligible to apply, the cap on the number of projects they support, and the length of time they are available. Regulations are highly country- and utility-specific. For example, in countries with complex terrain good spots are mostly remote (on hills and mountains rather than in large land fields); to exploit these remote areas, network expansion from low-voltage to medium-voltage connection is therefore needed. This increases costs for the investment but simultaneously – and indirectly – helps the distribution companies expand their network with new equipment.
As discussed in Sect. 2, Japan, Italy, the United Kingdom, and the Republic of Korea are examples of countries where intermittent incentive availability and funding levels have changed greatly due to the changes to their FIT programs over the past approximately 10 years. Changing the availability of incentives is one reason why many SWT manufacturers have not been able to remain in the market or do not participate in certain markets. The fluctuating sales presence of small wind manufacturers both in and exporting from the United States and China provides examples of how small wind manufacturers must adapt to different market conditions across countries. In the past, Japan, Italy, and the United Kingdom had been key export markets for SWT manufacturers. With the programs discontinued or drastically reduced, the markets are much less attractive, and this contributes to manufacturers leaving the market. Long-term consistency across incentive programs would greatly improve the development of the SWT sector. The lack of consistency also holds for national certification requirements and is another possible reason for manufacturers leaving the SWT market. If there was a unification (IEC certification, for example), then all the manufacturers could sell globally. For example, six US small wind manufacturers reported international exports in 2015, with just three in 2020 (Orrell et al., 2021). Similarly, sales in China and exports from China have fluctuated with the number of Chinese small wind manufacturers in that market. In 2017, only 15 Chinese SWT manufacturers reported sales, a decrease from 28 in 2014 (Duo, 2017), corresponding to a 60 % drop in sales from 2014 to 2017 (Orrell et al., 2021).
5.1.4 Lack of openly available data for detailed validation and development of design tools
Aeroelastic modeling should be the primary methodology for structural and performance assessment of any wind turbine. Such modeling allows the turbine designer to understand and predict the load and power behavior of the turbine before witnessing it in the field, to demonstrate and optimize the control parameters that have the highest impact on the design, and to optimize the configuration most efficiently.
For the results of an aeroelastic model to be used for design and certification, the aeroelastic code (the software), the turbine-specific inputs, the aeroelastic model setup and usage with those inputs, and the post-processing of the results must achieve a certain level of verification and validation. Most distributed wind modelers utilize the open-source aeroelastic code OpenFAST or the proprietary code HAWC2. While these tools have received adequate validation in past research work, there remains a need for experimental field data to validate turbine-specific models, especially in the case of SWTs. Publicly available aeroelastic models are well tuned for traditional three-bladed HAWTs, although less so for downwind HAWTs, and are progressively less and less validated for passive yaw, pitch-to-stall, furling, and VAWT machines (Forsyth et al., 2019). Scarcity of these data is seen in many aspects related to SWTs.
In the validation process, the model results are compared to experimental datasets to ascertain the degree to which the model represents the actual physics. Therefore, the validation datasets must be properly collected and quality assured. Validation, however, is not a binary statement about whether a model is valid or invalid, but rather a critical part in the overall assessment of the suitability of the computational model for the intended application (Hills et al., 2015).
A successful validation exercise requires close collaboration between the experimentalists, the modelers, certification bodies, and the relevant stakeholders throughout the conceptualization, design, execution, and post-processing phases of the experiments. Additionally, the computational model should be used to help design the details of the experimental campaign, which is effectively another (physical) simulation of the true behavior of the systems.
5.1.5 Social acceptance and environmental issues (noise, visual impact, vibrations)
In 2016, some studies suggested that around 70 % to 80 % of people in Europe support wind farms (Allen, 2016), although there were still concerns around noise and aesthetics. However, little was known about public attitudes toward locally developed SWTs. According to Ellis and Ferraro (2016), the social acceptance of wind energy is influenced by a much wider and complex set of mutual effects between individuals, communities, place, wind energy operators, regulatory regimes, and technology operating at a variety of geographical scales. Social acceptance should therefore be viewed within this wider set of relationships and as part of the transition to a low-carbon economy. In particular, small wind is commonly located closer to the customers that benefit but may also have more expanded impacts on the other local members of the community. For this reason, SWTs may stimulate social acceptance of wind energy if the installation and the technology used is really adequate and if local benefits are shown.
In 2016, a research survey was completed looking at the drivers of public attitudes toward SWTs in the UK (Tatchley et al., 2016). The results showed that half of respondents felt that SWTs were acceptable across a range of settings, with those on road signs being most accepted and those in hedgerows and gardens being least accepted.
Similar to the results obtained in a survey developed in Europe for the SWIP Project (SWIP Project, 2014) about the awareness level and public opinion of SWTs, more than 75 % of people interviewed showed a positive reaction to the installation of SWTs in their environment and only 5 % showed a negative reaction. Even for all demographic groups involved, the response was more positive to SWTs than large, utility-scale wind turbines. “Energy Communities” schemes increased this acceptance rate because more people are able to invest and benefit from a wind turbine investment. Generally, people feel detached from large, utility-scale wind facilities because they do not see the same direct benefits as in the case of SWT investments. Another conclusion was that industrial sites were regarded as the most acceptable places for installing SWTs, far ahead of the second-place response of roofs in residential areas. Even so, a bad attitude toward SWTs is still noticeable in politics and local administration in many regions, especially in those countries where historical or aesthetic restrictions are present (e.g., Italy).
In relation to noise emissions, SWT manufacturers have identified noise as a concern (also because some countries do require noise emission evaluations), and new SWT designs are typically less noisy. However, the general opinion is still that SWTs are noisy, especially if they are compared with solar PVs.
For visual impact (including visual flicker), noise, or safety issues, considerably less concern was shown than toward performance issues or high investment costs. This is supported by the fact that when an adequate support program for small wind is established, social concerns decline. Nevertheless, their visual impact in an urban area can still be a source of concern. According to Emblin (2017), developers must find smart ideas and designs to integrate turbines into communities and to educate local populations about the long-term benefits and impacts that SWT can bring. The visual impact can also be minimized if the turbines are placed carefully and sensitively, although turbine design also plays a significant role. These are all issues that may be addressed through expanded social science research, science-based community engagement, and innovations in design and software.
Vibration is another relevant issue, especially in roof-mounted wind turbines with no adequate damping solution and/or SWTs operating under high-wind conditions regulated by passive power regulation techniques. In those cases, vibration is transmitted through the pole to the roof or to the ground. When the turbine is sited near dwellings, residents have been known to express annoyance.
5.1.6 Real and perceived concerns with SWT reliability and the high cost of certification
As discussed, financial incentives in the form of FITs, direct-pay grants, and tax credits help strengthen the global distributed wind market. Incentive agencies and other industry stakeholders have worked to formulate and implement program eligibility requirements to ensure the public funds used in these programs are directed to successful projects, and embarrassing failures are avoided. One common strategy is to require third-party certification of the wind turbine system according to national and international standards. The goal of the standards is to provide meaningful criteria upon which to assess the quality of the engineering that has gone into a SWT and to provide consumers with performance data that will help them make informed purchasing decisions (e.g., IEC: International Standard, 2019b). While certification attests that a wind turbine has been tested and designed according to requirements in the relevant standards, a third party cannot guarantee that a turbine model will exhibit perfect reliability in the field. Therefore, a level of surveillance must be put in place by the certification body to monitor and respond to field failures, in collaboration with the turbine manufacturer.
While certification helps improve the reliability of deployed wind turbines, it comes at a significant cost, although efforts have been made to reduce the complexity and cost of meeting standards for SWTs. To achieve certification, the turbine must be field-tested for power performance, acoustic noise, safety and function, and durability. The turbine designer must also generate a significant engineering report documenting the calculation of turbine loads, both extreme and fatigue, and the structural analysis of the major components in the load path. These test and design reports are then evaluated by a third party, usually an internationally accredited certification body. If the work is found to conform to the applicable standards, certification is granted, making the turbine model eligible for financial incentives. The validity of the certificate must then be maintained because of design changes or other factors.
Other certifications or dedicated studies are typically required as part of the installation process, including structural engineering of the tower, the foundation (mostly within the permitting phase), and electrical safety (part of the IEC certification) related to protection from electrical shock and fire.
While it is very difficult to find publicly available data for field-testing and reporting, industrial contacts of the authors in Europe determined that it costs about EUR 200 000 (USD 230 000) for the complete design assessment of a SWT, while field-testing and reporting alone can cost upwards of EUR 85 000 (USD 100 000) and third-party certification can cost up to about EUR 43 000 (USD 50 000). Small and medium wind turbine manufacturers in the United States have reported that certification costs, including fees, direct expenses, and labor time, range from USD 150 000 (EUR 134 000) to USD 500 000 (EUR 435 000) (Orrell et al., 2020).
5.2 Improvement areas
By addressing the five identified grand challenges, SWT technology is expected to decrease significantly in cost, become more accepted within the distributed energy investment community, and demonstrate acceptable community impact to allow direct community-based acceptance. To this scope, the following section reviews some main improvement areas where major research and development is suggested to allow the global SWT market to flourish.
5.2.1 Changes in turbine design and control
The task of designing, manufacturing, and installing SWTs has always been challenging. Suppliers of small wind technology must produce a product that will be deployed in a wide variety of sites around the globe, maintain reliable operation with minimal maintenance, and be an economically viable choice. For small wind to maintain a competitive stance on the international distributed clean energy market, future designs must be further optimized, lowering the LCOE. Unlike the process used largely for current SWT products on the market, future optimized SWT designs will need to utilize validated aero-servo-elastic modeling as a design tool starting at the concept phase; utilize low-cost, reliable overspeed protection methods; and incorporate strategies including design for manufacturing, design for certification, design for installation, and design for recycling, all before initial prototype testing and ideally in the framework of improved and more detailed, internationally accepted design standards.
While addressing all these things is beyond the scope of this study, some key enabling actions are proposed in the following, clustered together based on the main technical areas.
Aerodynamics
Basic wind turbine aerodynamics lead to the statement that a good blade is composed of good airfoils: “good” in the sense of having a high lift-to-drag ratio. At the low Reynolds numbers of SWTs, this is a major design challenge that has languished for over 2 decades. Given the developments in Reynolds-averaged Navier–Stokes (RANS) turbulence and transition models, a design methodology is becoming available to overcome the limitations of conventional panel methods in use up to now. In particular, better modeling of the near- and post-stall region of airfoil polars is key not only to improve stall-controlled machines, but also to get more reliable estimations of loads in a variety of DLCs prescribed by the standards, thus leading to better prediction of turbine lifetime and possibly enabling lower safety factors. Innovations at the airfoil level should focus not only on pure aerodynamic performance (in terms of high glide ratio, resistance to stall, and low sensitivity to Re variations), but also on further lowering noise levels to make turbines more suitable for installations in proximity to populated areas (improved certification labeling could also be useful in this regard).
The introduction of smart blade technologies for flow control in SWTs may provide a significant boost toward better designs in the near future. For example, the potential of retrofitting SWTs with passive flow control elements such as vortex generators and Gurney flaps to improve their starting behavior and to reduce the risk of stall caused by roughness has recently shown very promising prospects (Holst et al., 2017).
Aeroelastic modeling
Up to now, SWT blades have been much stiffer and protected by large safety factors in their structural design than blades for large turbines. To enable wider use of this simulation tool for design and optimization, gaps and barriers to its use must be identified and solutions implemented (Damiani et al., 2022). Growth in the theoretical knowledge possessed by SWT-producing companies and a wider availability of easy-to-set, open-source tools will also be required. To evaluate the impact of the above, Evans et al. (2018, 2021) investigated blade fatigue by undertaking aeroelastic simulations of six SWTs up to 50 kW in rated power using OpenFAST (NREL, OpenFAST, 2019). Their research shows that the fatigue DLC in IEC 61400-2 is unduly pessimistic and that more detailed aeroelastic modeling to allow the design of fatigue-resistant blades at lower cost will be needed. To support more efficient designs while reducing blade cost and weight, aeroelastic modeling should be increasingly used in SWT design, as it has been used for utility-scale turbines. To enable wider use of this simulation tool for design and optimization, several gaps and barriers to its use across the SWT industry must be identified and addressed (Damiani et al., 2022). Growth in the theoretical knowledge possessed by typically small SWT-producing companies and a wider availability of easy-to-set-up, open-source tools will also be required. Additionally, the challenge of expanding the use of aeroelastic models must be supported through dedicated verification and validation campaigns on a number of different turbine archetypes, sizes, and computational codes. One particular area of importance for very small turbines is the need for better understanding of yaw behavior of turbines with a tail fin. Yaw response gives rise to gyroscopic ultimate and fatigue loads, which can be the largest loads on a turbine of around 1 kW (Wood, 2011). None of the currently available aeroelastic codes contain a tail fin model.
Control
Control strategies for SWTs must also evolve to become more robust and cost-effective. We see an example of this evolution in the contemporary trend of turbine designers moving from tail furling to stall regulation and in some cases pitch regulation. An example of this transition is the evolution of the Bergey Excel 10 turbine toward the Excel 15 (Bergey Wind Power, 2022). The change was in both the increase in power capture via a larger, more efficient rotor and the moving away from the furling strategy toward a more controlled-stall strategy. Other manufacturers (e.g., Tozzi Nord, 2022) are proposing models with both active yaw and pitch. The difficulty here is to package these controls in relatively tight spaces while still guaranteeing reliability and redundancy. A recent research article (Damiani and Davis, 2022) explores the technical and economic viability of retrofitting a stall-controlled turbine with pitch control together with an extended rotor for increased power capture. Both pitch-to-stall and pitch-to-feather approaches are investigated, and the advantages of each solution are discussed. The authors devise a compact, redundant independent pitch control system but conclude that, for power regulation, the economics do not warrant the extra complexity of the pitch control, which is then relegated to overspeed protection alone. More research and technical support in this direction are needed because the experience of utility-scale machines is not directly applicable in SWTs due to cost and physical constraints. However, as discussed in Sect. 4, recent studies suggest that the use of pitch control could significantly improve the efficiency of SWTs (Papi et al., 2021), and new grid integration requirements being driven by the expanded use of distributed generation may require more active power control than what can be achieved through traditional controlled stall designs.
Generator and drivetrain
The unsteady behavior of SWTs, especially during start-up, depends on drivetrain and generator resistance (Vaz et al., 2018). Typically, the wind speed at which a SWT begins power production as the wind increases in strength is significantly higher than the speed at which it ceases production as the wind dies away (Wood, 2011). The cut-in wind speed is usually an average of these two speeds and therefore can give a misleading indication of what wind speed is needed for a SWT to start producing power. In particular, the cogging torque of permanent magnet generators (PMGs) can be a major impediment to very-low-wind-speed start-up of small turbines. This problem is exacerbated because, due to their relatively small size, SWT manufacturers are typically forced to purchase third-party generators that may not match their blade design, resulting in the need for higher wind speeds to overcome the cogging torque of the generator. Additionally, because there appears to be few uses for PMGs in the sub-10 kW capacity, there is little market pressure on generator manufacturers to optimize their designs for SWT applications. Eventually, SWT manufacturers may design and build their own generators, but turbine sales must expand greatly to warrant this large investment. The design of turbine-specific generators, optimized with specific blade and rotor design, would require improved understanding of generators, control systems, permanent magnet design, and the use of modern additive manufacturing.
Design strategies
Knowing that a SWT must be manufactured, tested, certified, installed, maintained, and then recycled at the end of its life puts pressure on the designer to incorporate this thinking into the design from the initial concept. Key market drivers, such as subsidies that may incentivize capital costs compared to operational costs, must be considered carefully to balance up-front and operating costs, in turn making the LCOE of SWTs more competitive. Several, sometimes competing, additional design strategies that may be implemented that will impact turbine performance and cost include design for manufacturing (incorporating the manufacturing in the design process to avoid future issues in fabrication and assembly); design for certification (incorporating conformity with the relevant design standards early in the design process to avoid future issues in the design evaluation and turbine certification); and lastly, since the SWT must be shipped, installed, and commissioned, design for installation strategies, which must be considered, especially if the turbine is to be deployed in remote or isolated locations. With this in mind, the complete small wind system, including the foundation, tower, inverter, wiring, disconnects, monitoring, nacelle, access platforms, and rotor, will need to be designed in a way that makes the installation process efficient, well thought-out, innovative, and safe.
Novel concepts
While continuously improving existing concepts and archetypes, the recent novel designs discussed in Sect. 4 like DAWT, Darrieus VAWTs, and mostly recently AWE still deserve attention and research efforts, since they could represent an important future contribution to distributed power production. Novel turbine concepts, however, are not limited only to the individual turbine performance but should also include holistic considerations of different elements, from economics to social perspectives, which are further discussed in subsequent sections.
5.2.2 Open data from field experiments
Many, but not all, SWT manufacturers remotely monitor the operation of their turbine fleets. For many smaller turbines, monitoring focuses on electrical parameters that are measured as part of the inverter system, but ongoing measurement of many turbine-specific parameters simply increases the cost and maintenance requirements of turbine systems. Sharing any available remote monitoring data is an opportunity for researchers and manufacturers to collaborate on a variety of potential research areas that could expand small wind markets while also helping reduce costs. These areas include isolating and identifying the factors that affect why actual performance differs from predicted performance in real-world conditions and then improving performance prediction tools accordingly, improving wind resource assessment data and models for small wind, calculating actual LCOEs, using the performance data to understand wind's complementarity to solar PVs, and enabling wind to complement and communicate with other distributed energy resources in the grid of the future. The inability to predict performance consistently and accurately can negatively affect customer confidence in small wind and access to financing. Increasing investor confidence, reducing perceived risk, and decreasing assessment costs with improved tools and datasets will help small wind achieve large-scale deployment. In this regard, however, it must be clarified that the real “performance” of a wind turbine system is the amount of achievable AEP. As discussed in Sect. 5.1.2, this actually is driven by variables beyond just turbine technology, including, but not limited to, the project's available wind resource, siting (i.e., tower height, local obstructions, and other micrositing issues), and turbine availability (i.e., downtime for expected or unexpected maintenance or grid outages). These variables contribute to why accurately estimating small wind project performance can be challenging. A better prediction of performance can then be synthesized into the proper combination of good resource estimation coupled with accurate power performance and then with the guarantee that the turbine will provide that same level of power over its design life. While the current performance prediction tools generally focus on the first of these questions, which is driven by good resource assessment and accurate representation of the turbine power curve as discussed above, they largely do not address the second part, which is failure analysis. Open data on turbine failure mechanisms for the verification and tuning of performance prediction tools will then need to cover not only turbine performance vs. actual wind resource but also real production vs. time, fatigue, and failure analyses.
Regarding prediction tools, in particular, special attention is also needed to make available open data to calibrate and further develop and design aero-servo-elastic tools (see Sect. 5.2.1) in operating conditions outside of turbine-specific validation that may be needed as part of turbine certification processes. Having detailed field data that may only be available from heavily instrumented research-grade turbines in the wind tunnel (e.g., those shared in internationally coordinated programs like those from the International Energy Agency (IEA) Wind Technical Collaboration Programme) will foster the development of more robust design tools for SWTs, enabling the modelers to improve the accuracy of the turbine design tools. Data must also be collected over a wide range of operating conditions, from the standard steady-state operation to predicting the turbine loads, performance, and lifetime in actual operating conditions. In this sense, the tools can be validated for scenarios that can be significantly different from one particular site to another site, e.g., different turbulence levels, anisotropy, wind speed, wind direction, and ground stability. An overview of measurement data collected within IEA projects is given in Schepers and Schreck (2019). These projects also provide examples of how international consensus on sharing data will help the users validate models while maintaining any needed confidentiality.
5.2.3 Improvements in installation, maintenance, and life-cycle analysis
Over the 10 years from 2010 to 2020, the cost for installing residential-scale solar PV systems in the United States has seen an approximately 64 % reduction in benchmark costs. A total of 42 % of these costs has been attributed to installation labor and additional soft costs, such as siting, permitting, sales tax, and overhead (IEA, 2020). Although a smaller percentage of overall total costs, significant reductions are seen in structural and electrical hardware costs outside of the inverter and solar module. These installation costs (the total cost outside of the module and inverter) now make up almost 70 % of the total installed cost of a modern residential-scale solar PV system (Feldman et al., 2021). Limited published data exist for similar installation-specific balance-of-station costs for small wind (Orrell et al., 2021, as an example), but a 2017 study of the US distributed wind market shows that similar costs represent 63 % of the cost of residential wind systems (Orrell and Poehlman, 2017), which indicates that if a cost reduction of a similar magnitude as that demonstrated in the solar industry can be achieved for small wind, this would represent a 25 % reduction in the installed costs of small wind systems.
To date, limited systematic analysis has been undertaken to identify methods to reduce the installation costs of small wind technology. Having more of these studies for different countries and environments is considered a key research area for the evolution of small wind systems.
The SMART Wind Roadmap (DWEA, 2016) identifies a set of potential cost-reduction opportunities based on a consensus-based collaboration of small wind industry members. Most of the focus of this work was in the area of turbine hardware cost reductions, but the report does identify tower, foundation, and turbine erection costs as significant cost drivers for small wind, on par with the costs of the turbine hardware itself. Recent work by industry has focused primarily on reducing the costs of towers, primarily developing self-erecting mono-pole towers that provide lower installation and turbine maintenance costs. Recent efforts to reduce installation costs through the DOE-funded Competitiveness Improvement Project (NREL, 2021) have focused on tower and foundation design, including the use of low or no concrete foundations for SWTs, which can greatly reduce turbine installation timelines and costs. Expanded cost reductions could also be expected in site assessment with the expanded use of modeling tools, simplified installation procedures, and reductions in project acquisition and project permitting, each of which needs to be explored in more detail.
Similarly, a full understanding of O&M costs of DWTs is limited. As introduced in Sect. 3.2, the most recent US Distributed Wind Market Report (Orrell et al., 2021) provides an estimate of cost of USD 37 per kilowatt (EUR 32 per kilowatt) per scheduled maintenance site visit, which is typically required annually. This cost has not seemed to decrease over time. In comparison, O&M expenses on the basis of USD (EUR) per kilowatt-hour per year for residential-scale solar PV systems has dropped by almost 50 % over the last 10 years, again demonstrating strong potential for cost savings (Feldman et al., 2021). Maintenance needs of small turbines cover a range of requirements. Most residential and small commercial turbines are designed to require minimal ongoing maintenance, such as bi-annual inspections and potentially blade reconditioning, depending on the environment. Turbines greater than 50 kW in capacity are assumed to undergo more ongoing maintenance, similar to large wind turbines. Ideas that have been identified to support lower long-term maintenance costs include the expanded use of remote monitoring to understand service needs before maintenance is required and expanded turbine structural modeling to eliminate unplanned maintenance. Systematic approaches to reduce maintenance for the distributed wind fleet should also be pursued. Although individual manufacturers have a good sense of long-term turbine-specific component failure rates, no system-wide assessment has been undertaken to focus research efforts on components that have higher service requirements, such as power electronics. This would also represent a key enabler. Focusing on local and national standards will isolate the SWT manufacturers in the borders of their countries. Unification under a common standard (such as IEC) should be proposed as for PVs. History also shows how the SWT market has failed to follow the large wind turbine and PV pace for growth.
Although stories abound of particular SWTs operating for decades, factual data on the full life-cycle cost and performance of many SWTs is limited, reducing the ability to assess the long-term cost of energy for small wind systems. Additionally, the wide variety of turbines, their almost constant change in design, and limited number of operational small turbines that have undergone a full certification to national and international standards also make it challenging to develop meaningful, information-based estimates of life-cycle cost as has been done with other technologies. To support the better full assessment of life-cycle costs, NREL developed a cost taxonomy for distributed wind (Forsyth et al., 2017) that has been applied in a small number of cases such as Orrell and Poehlman (2017). Most work today focuses on articulating costs based on the installed cost of wind technology, making assumptions on maintenance costs and long-term turbine performance. Estimates of life-cycle costs for SWTs at and below USD 0.10 per kilowatt-hour (EUR 0.087 per kilowatt-hour) are being reported but have not been independently demonstrated or verified. A better estimation of life-cycle costs of SWTs is considered a key enabler. In doing so, of critical concern is an accurate accounting of long-term turbine production. Work has been undertaken in relation to an improved estimation of the site-specific wind resource, a topic that is more complicated due to the higher likelihood of local obstructions (Drew et al., 2015). Long-term performance production, which could include consideration of long-term wind turbine availability, turbine performance degradation, and increased impact of obstacles such as vegetation growth, has not been systematically considered to date and would definitely improve these estimations (see also Sect. 5.2.2).
5.2.4 Regional appreciation of distributed generation and integration with storage systems
Although historically used in remote and edge-of-grid applications (Hemeida et al., 2022; Duchaud et al., 2019), the continued decrease in the costs of renewable energy generation and storage technologies, combined with incentive programs and policies to support local generation, has resulted in a wider acceptance of grid-connected distributed generation. With the advent of lower-cost controls, advanced power electronics, and improved communication systems, the use of more distributed power generation is becoming common. Additionally, new efforts to expand clean energy development, paired with the high costs and typically long project development timelines for transmission development, make the use of distributed generation even more cost-effective as a way to support local power development. Lastly, although it typically requires additional expenses and planning, distributed generation can also be used to support grid resilience when combined with storage and other grid-forming technologies. The bold plans of the European Union as well as many other countries around the world in the direction of e-mobility require significant infrastructure investments to facilitate the millions of electric vehicle chargers that will be installed. This expansion will, however, put an additional large load on existing low-voltage grid infrastructure that, in most countries, is old and extremely expensive to upgrade. The strain on the low-voltage grid cascades toward the medium-voltage infrastructure, which is also coming much closer to its capacity limits.
Enhancing this development while maintaining a reasonable cost involves simultaneously unloading the low- and medium-voltage grid from some capacity through local energy generation and storage. This is possible when buildings and households in local communities are able to become “net prosumers”, meaning that they are simultaneously energy producers and consumers. In the future, these prosumers can serve as active members of the energy system network with the ability to exchange energy and offer stabilizing services to the grid. This is achieved through the integration of renewables with storage in combination with decentralized control. Solar has been the first technology to be successfully combined with storage on a residential or local community level, contributing effectively to the “net prosumer” concept. SWTs have been traditionally very simplistic with respect to their design and control, making their combination with storage more difficult. However, numerous current designs include variable-speed full-converter AC–DC–AC turbine concepts and have been successfully integrated with modern storage technologies. The combination of SWTs with fast-response storage systems allows for the generation of significant quantities of energy at the low-voltage grid level with a simultaneous grid stabilization capability that is able to unload capacity in an effective manner from the grid. Similarly, combining wind, solar, and storage in many parts of the world where wind and solar are not typically coincident, either daily or seasonally, could provide expanded benefits to the low- and medium-voltage energy distribution network. Actions can also be carried out directly on wind turbine design and control, e.g., integrating fault ride through technologies.
The biggest challenges for this integration involve the volatile nature of wind turbine operation, which requires a very fast response from the power electronics and storage technology to maintain constant production levels and allow for fast-response voltage and frequency regulation. However, building on the distributed generation concept into regional development, the wider use of distributed wind combined with solar and storage at small scales across a region will reduce the variability experienced with just single units, providing more reliable and less transient power, likely at a reduced cost and certainly faster than large-scale transmission system development.
To address the expanded need for energy to remote areas not served by current energy infrastructure across the globe, SWTs in combination with solar, storage, and advanced load control technology are likely to play an expanding role. Although most investments within the energy access space currently focus on solar and storage, growing energy needs will make it difficult and expensive to rely on oversized solar and storage facilities to provide full-time power. The use of SWTs and other renewable energy devices such as pico hydro and biomass can provide energy at different times than solar, reducing the cost and space requirements of large storage systems. The limited civil infrastructure and difficulties in providing the on-site service expertise that is required for larger wind turbines will make SWT technologies more applicable for these more remote applications.
5.2.5 Shared programs of incentives and social actions to improve acceptance
The majority of renewable energy incentives are targeted at large-scale wind projects and wind farms, where scale is a critical component in a country's wind energy development success rate (Wolsink, 2013). Social acceptability can also be construed as commercial acceptance in the case of small wind. Wind energy is naturally more complex to diffuse than other energy alternatives such as solar panels because it frequently involves infrastructure (foundation, tower, and grid interconnection).
If the economic competitiveness of SWTs can progress significantly as a result of improvements in efficiency, manufacturing, and siting, then the technology could be sustained in the transitory phase by more coordinated political and regulatory actions at a large scale. For example, a federation like Europe could promote the harmonization of incentives between the countries, although energy policies are still managed individually by the members. This could in turn create a common, broader market for SWTs, promoting the development of an economy of scales. Moreover, different from previous practices, the time framework for these incentives to stay in place should be clearly assessed to reassure investors and companies and prompt them to bid on the technology. In this context, networks of research institutions like EAWE in Europe and NAWEA in the United States or of wind energy industries like WindEurope can play an important role advising regulatory bodies and politicians.
Social acceptance of SWTs could potentially be improved if the drawback on local ecology such as the habitats of birds, insects, and other small animals, as well as noise and vibrations, can be minimized. While these concerns are largely debated in utility-scale machines, and a vast body of literature does exist, the environmental impacts of SWTs are not so well defined as a result of less scientific research on the topic. Additional studies and projects on the topic would also represent an important enabler to improve acceptance of small wind.
Finally, it is worth mentioning that the diffusion of small wind technology could also be supported by actions that are somehow a combination of technical and social aspects. A good example of this is a virtual net-metering approach (Hellenic Electricity Distribution Network Operator S.A., 2021). Under this scheme, consumers could install SWTs away from the consumption meter and liquidate the energy as a classic net-metering. There is a trend where companies try to get “green electricity” from their providers or through their own investments to compensate for their footprint (Wang, 2013). This will and should get amplified in the next few years as companies of all sizes try to become greener. These efforts will boost the sector but also in a more secure and professional way because this “green point system” will push the wind turbine makers toward real power curves and better products (Simic et al., 2013). Additionally, a link between this type of investment with ESG (environmental, social, and governance) policies will boost the market even more due to the comparative advantages of SWTs. For example, many industrial consumers who have already installed PVs may be eager to increase their green electricity, but they may not have space available for additional PVs.
5.3 Key enablers
As a final product of the work, the aforementioned areas of focus are synthesized below in 10 key enablers that, in the authors' opinion, more than others would represent the catalysts for a significant development of SWTs worldwide.
-
Aeroelasticity for SWTs. If aeroelasticity has represented the main driver of the size and capacity factor of utility-scale machines, its diffusion to SWTs could also be extremely beneficial. For example, an improved aeroelastic design could contribute to reducing the structural safety factors, in turn enabling a blade weight and cost reduction and more efficient designs. To enable wider use of aero-servo-elastic simulation tools for design and optimization, gaps and barriers still need to be identified and solutions implemented, including growth in the theoretical knowledge possessed by SWT-producing companies and wider availability of easy-to-set, open-source tools.
-
Improvement in control strategies. To achieve more effective and robust control, thus maximizing the energy conversion, a transition away from furling toward more controlled-stall strategies is also seen in very small machines. Moreover, some manufacturers are proposing models with both active yaw and pitch. While the implementation of these controls in SWTs is not straightforward due to the difficulty of packaging them in relatively tight spaces while still guaranteeing reliability and redundancy, recent studies suggest that the use of active-pitch and active-yaw controls could significantly improve the efficiency of future SWTs.
-
Improvement in design, with a focus on the characterization of airfoil aerodynamics at low Re. Improvements in the design of SWTs will be needed at any level, from the rotor–nacelle assembly (e.g., minimization of drivetrain and generator resistance, with particular reference to the cogging torque) to blades' material and cost or use of cheaper materials for some of the most expensive components such as the towers. Among others, a key area for improvement is defining (possibly validated with experiments) accurate and reliable airfoil polars with the low-Reynolds-number range that SWT blades usually work with, remembering their strong sensitivity to air density variations due to installations in altitude for example. Having those data available will produce benefits at different levels, including more effective aerodynamic designs, better prediction of loads, and a more reliable definition of turbine control (especially in stall-controlled machines). Special attention should also be given to aerodynamic noise in view of turbine installation in proximity to populated areas.
-
Open data from both wind tunnel and field experiments. Open data for verification, validation, and optimization of SWTs are seen as a key enabler for the future evolution of the technology. In particular, thanks to the smaller size of SWTs compared to utility-scale machines, they can be placed at full scale or at low scale in a wind tunnel, meaning that reliable testing can take place in the controlled and known wind tunnel environment. Data collected in these conditions would be of particular use for the evolution and calibration of simulation tools. On the other hand, there is also an urgent need for different open datasets, i.e., related to field measurements of real turbine performance. These will need to cover not only turbine performance vs. actual wind resource, but also real production vs. time, fatigue, and failure analyses.
-
More accurate performance and resource assessments. More accurate assessments of both the real performance of SWTs and the wind resource are key to improving design, siting, and operation. Regarding performance assessment, a better quantification of several factors could be beneficial, including the impact of turbulence or the effect of obstacles. For example, a DOE-funded project plans to include obstacle modeling research results as an add-on feature to wind resource data for the United States available via an application programming interface. Regarding resource assessment, high-fidelity computational fluid dynamics (CFD) simulations could provide a significant contribution, even though the economic convenience of their computational cost must still be proven.
-
Variable validation and verification of SWTs, especially for non-traditional archetypes. Balancing certification requirements from a regulatory point of view, which prioritizes design thoroughness, model validation, and public safety, against requests from the original equipment manufacturers for more streamlined and economical approaches to certification is difficult. Therefore, there is an immediate need for breaking SWTs into categories for load assessment and validation requirements that account for both size and archetype. Smaller turbines and more established archetypes would benefit from less onerous requirements in terms of load assessment and validation, whereas more complicated machines would require a more in-depth review of the prediction capabilities of the code used for design and load analysis. Verification and validation guidance in the current design standards is limited, and this is one area that requires more research and data to increase the diffusion of DWT and SWTs.
-
Standardization. Standardization at different levels is key for further development of SWT technology. First, standardization is needed for components to promote an economy of scale. In particular, it is suggested that generic products are designed and produced to achieve economies of scale, in turn enabling reduction in the purchase cost of SWTs. Examples of this could be the design and production of a generic rotor blade family or lighter and easier-to-install towers. Similarly, research must be focused on the utilization of lower-cost generators, possibly available on the market with a standardized design. Standardization would come with non-negligible technical challenges but could represent the key catalyst for reducing the LCOE in the near future. Moreover, more effective standardization is needed for regulations and standards. Regulations for SWT installation among different countries are also largely variable, and making those regulations more uniform through international coordination would represent another pillar toward the creation of a stable market for the technology. Standards should instead evolve along with the changes in the design and operation of new machines, with a special focus on aeroelastic design and certification. In particular, we suggest that a major enabler could be the differentiation of standards as a function of turbine archetype.
-
Detailed studies on cost and life-cycle analysis. To date, limited systematic analysis has been undertaken to identify methods to reduce the installation costs of small wind technology. Having more of these studies for different countries and environments is proposed as a key enabler for the evolution of small wind systems, in connection with the impulse toward standardization. The same applies to life-cycle costs, in which a critical concern is accurate accounting for long-term turbine production. This should include consideration of long-term wind turbine availability; turbine performance degradation; and increased impact of obstacles, such as vegetation growth, which have not been systematically considered to date and would definitely improve the estimations.
-
Grid compliance and integration, including storage systems. To comply with most of the current grid codes as well as the upcoming grid code modifications, SWTs of larger rated power should probably mostly become variable speed and make full use of AC–DC–AC converters. Also, new SWT developments will likely make larger use of fault ride through technologies because they are becoming compulsory for small-scale generating systems. Beyond this, the combination of SWTs with fast-response storage systems is thought to be key for allowing generation of significant quantities of energy at the low-voltage grid level with a simultaneous grid stabilization capability that is able to unload capacity in an effective manner from the grid. Similarly, combining wind, solar, and storage in many parts of the world where wind and solar are not typically coincident, either daily or seasonally, could provide expanded benefits to the low- and medium-voltage energy distribution network and support the establishment of a significant market for small wind technology.
-
Shared programs of incentives and new paradigms to support SWT diffusion, with a special focus on social acceptance. Both incentive programs and regulations have been widely variable across different countries, making it difficult for producers to stay in the market. More coordinated political and regulatory actions at a large scale should be fostered in view of the creation of a broader market for SWTs, thus promoting the development of an economy of scale. Different from previous practices, the time framework for these incentives to stay in place should be clearly assessed to assure investors and companies and prompt them to bid on the technology. In this context, networks of research institutions or wind energy industrials could play an important role in advising regulatory bodies and politicians. All these actions must be coordinated with a better understanding of the environmental impacts of SWTs so that greater social acceptance can be achieved.
For SWTs to be widely successful, tomorrow's technology will require a new generation of turbines optimized for complex, low-wind-speed locations with high turbulence that can also successfully and reliably operate throughout their design life, producing the power expected when they were installed. Such turbine designs will require higher-fidelity modeling and simulation to support lower-order tools for design and optimization of turbine systems in complex installation contexts. These models will need additional open data for validation and calibration, which are currently very scarce. Also, advancements in control and materials will be needed to improve the energy capture in gusty flows and to reduce the overall cost. Additionally, these higher-efficiency and reliable turbines must be paired with accurate performance assessment tools to ensure life-cycle power production, providing confidence to consumers and financiers alike. Finally, these turbines will be more effectively integrated with storage systems to achieve higher appreciation of small wind for distributed generation.
To make this scenario possible in the near future, the present study suggests five grand challenges for the small wind community, to which common and synergic efforts should be devoted. These grand challenges translate into
-
improving energy conversion of modern SWTs through better design and control, especially in the case of turbulent wind;
-
better predicting long-term turbine performance with limited resource measurements and proving reliability;
-
improving the economic viability of small wind energy;
-
facilitating the contribution of SWTs to the energy demand and electrical system integration;
-
fostering engagement, social acceptance, and deployment for global distributed wind markets.
To overcome these challenges, the main unknowns and gaps that must be filled have been presented, as well as the main improvement areas to which major research and development actions should be devoted. As a final product of the work, 10 key enablers are proposed by the authors as the proper catalysts for a significant development of SWTs worldwide:
- I.
more effective use of aeroelasticity for SWTs;
- II.
improvement in control strategies;
- III.
improvement in design, with a focus on the characterization of airfoil aerodynamics at low Re;
- IV.
open data from both wind tunnel and field experiments;
- V.
more accurate performance and resource assessments;
- VI.
variable validation and verification of SWTs, especially for non-traditional archetypes;
- VII.
standardization;
- VIII.
detailed studies on cost and life-cycle analysis;
- IX.
grid compliance and integration, including storage systems;
- X.
shared programs of incentives and new paradigms to support SWT diffusion, with a special focus on social acceptance.
All relevant data are included in the paper.
All authors were involved in the original draft preparation, review, and editing. AB directed the work and was responsible for much of the introduction, recommendations, and summary material. AO was the main author responsible for Sects. 2 and 3, with IBG, GE, and RD. GB, AC, JIC, RD, CSF, DI, CNN, GP, MR, GS, BS, and DW contributed with all their expertise to Sect. 4. All the authors contributed to Sects. 5 and 6. Much material was shared or moved between sections, and editing responsibilities were comprehensive, so section authorship is never exclusive.
At least one of the (co-)authors is a member of the editorial board of Wind Energy Science. The peer-review process was guided by an independent editor, and the authors also have no other competing interests to declare.
Publisher's note: Copernicus Publications remains neutral with regard to jurisdictional claims in published maps and institutional affiliations.
This study was originally promoted by the Small Wind Turbine Technical Committee of the European Academy of Wind Energy (EAWE), which is sincerely acknowledged for their support. Experts from around the world have joined the authors' group in a joint effort to provide a comprehensive view of the topic and a critical analysis on the status of the SWT and DWT technology. Special thanks are also due to the National Renewable Energy Laboratory (NREL) and Pacific Northwest National Laboratory for providing access to their most recent data. Moreover, appreciation is shown to the Eunice Energy Group for supporting the study with its industrial experience. The authors would like to acknowledge the members of “IEA Task 41: Enabling Wind to Contribute to a Distributed Energy Future” for great collaborations and to the numerous experts who did not author the paper but directly contributed via private discussions and friendly reviews; in particular, the assistance provided by Vasilis Papatsiros from the Eunice Energy Group was greatly appreciated. Finally, Francesco Papi from Università degli Studi di Firenze is acknowledged for his contribution in the consolidation of the document and the final editing.
This work was supported in part by the National Renewable Energy Laboratory (preparation of some graphics), the Pacific Northwest National Laboratory (text editing), and the Publications Committee of the European Academy of Wind Energy (coverage of part of the APC).
This paper was edited by Gerard J. W. van Bussel and reviewed by Phil Clausen and one anonymous referee.
Abbott, I. H. and Von Doenhoff, A. E.: Theory of wing sections: including a summary of airfoil data, Dover Publ., New York, USA, 691 pp., ISBN 0486605868, 2010.
Aeolus4Future: Efficient Harvesting of the Wind Energy, Marie Skłodowska-Curie, grant agreement no. 643167, https://cordis.europa.eu/article/id/386860-a-breath-of-fresh-air-for-wind-energy, last access: 17 August 2022.
Akwa, J. V., Vielmo, H. A., and Petry, A. P.: A review on the performance of Savonius wind turbines, Renew. Sustain. En. Rev., 16, 3054–3064, https://doi.org/10.1016/j.rser.2012.02.056, 2012.
Allen, M.: Gauging public opinion on small wind turbines, https://www.youris.com/energy/renewables/gauging-public-opinion-on-small-wind-turbines.kl (last access: 17 August 2022), 2016.
Arredondo-Galeana, A. and Brennan, F.: Floating Offshore Vertical Axis Wind Turbines: Opportunities, Challenges and Way Forward, Energies, 14, 8000, https://doi.org/10.3390/en14238000, 2021.
Aslam Bhutta, M. M., Hayat, N., Farooq, A. U., Ali, Z., Jamil, S. R., and Hussain, Z.: Vertical axis wind turbine – A review of various configurations and design techniques, Renew. Sustain. Energ. Rev., 16, 1926–1939, https://doi.org/10.1016/j.rser.2011.12.004, 2012.
Baker, T. L.: A field guide to American windmills, 1st ed., University of Oklahoma Press, Norman, 516 pp., ISBN 0806119012, 1985.
Balduzzi, F., Bianchini, A., and Ferrari, L.: Microeolic turbines in the built environment: Influence of the installation site on the potential energy yield, Renewable Energy, 45, 163–174, https://doi.org/10.1016/j.renene.2012.02.022, 2012.
Balduzzi, F., Zini, M., Molina, A. C., Bartoli, G., De Troyer, T., Runacres, M. C., Ferrara, G., and Bianchini, A.: Understanding the aerodynamic behavior and energy conversion capability of small darrieus vertical axis wind turbines in turbulent flows, Energies, 13, 2936, https://doi.org/10.3390/en13112936, 2020.
Bangga, G., Lutz, T., and Krämer, E.: Root flow characteristics and 3D effects of an isolated wind turbine rotor, J. Mech. Sci. Technol., 31, 3839–3844, https://doi.org/10.1007/s12206-017-0728-6, 2017.
Barbose, G. and Darghouth, N.: Tracking the Sun VIII, The Installed Price of Residential and Non-Residential Photovoltaic Systems in the United States, https://eta-publications.lbl.gov/sites/default/files/lbnl-188238_0.pdf (last access: 17 August 2022), 2015.
Battisti, L.: Wind Energy Exploitation in Urban Environment, 2018th ed., Springer International Publishing, ISBN 3319749439, 2018.
Bergey Wind Power: Bergey Wind Power, http://www.bergey.com/ (last access: 17 August 2022), 2022.
Bianchini, A.: Trends, Prospects, and R&D Directions in Wind Turbine Technology?, in: Reference Module in Earth Systems and Environmental Sciences, Elsevier, https://doi.org/10.1016/B978-0-12-409548-9.11864-0, 2019.
Bianchini, A., Ferrara, G., Ferrari, L., and Magnani, S.: An improved model for the performance estimation of an H-Darrieus wind turbine in skewed flow, Wind Engineer., 36, 667–686, https://doi.org/10.1260/0309-524X.36.6.667, 2012.
Bianchini, A., Ferrara, G., and Ferrari, L.: Design guidelines for H-Darrieus wind turbines: Optimization of the annual energy yield, Energ. Convers. Manage., 89, 690–707, https://doi.org/10.1016/j.enconman.2014.10.038, 2015a.
Bianchini, A., Balduzzi, F., Rainbird, J. M., Peiró, J., Graham, J. M. R., Ferrara, G., and Ferrari, L.: On the influence of virtual camber effect on airfoil polars for use in simulations of Darrieus wind turbines, Energ. Convers. Manage., 106, 373–384, https://doi.org/10.1016/j.enconman.2015.09.053, 2015b.
Bianchini, A., Balduzzi, F., Ferrara, G., and Ferrari, L.: Virtual incidence effect on rotating airfoils in Darrieus wind turbines, Energ. Convers. Manage., 111, 329–338, https://doi.org/10.1016/j.enconman.2015.12.056, 2016.
Bianchini, A., Balduzzi, F., Ferrara, G., Persico, G., Dossena, V., and Ferrari, L.: A critical analysis on low-order simulation models for darrieus vawts: How much do they pertain to the real flow?, J. Eng. Gas Turb. Power, 141, 011018, https://doi.org/10.1115/1.4040851, 2019.
Boccard, N.: Capacity factor of wind power realized values vs. estimates, Energy Policy, 37, 2679–2688, https://doi.org/10.1016/j.enpol.2009.02.046, 2009.
Bontempo, R. and Manna, M.: Diffuser augmented wind turbines: Review and assessment of theoretical models, Appl. Energy, 280, 115867, https://doi.org/10.1016/j.apenergy.2020.115867, 2020.
Bortolini, M., Gamberi, M., Graziani, A., Manzini, R., and Pilati, F.: Performance and viability analysis of small wind turbines in the European Union, Renew. Energ., 62, 629–639, https://doi.org/10.1016/j.renene.2013.08.004, 2014.
Bortolotti, P., Ivanov, H., Johnson, N., Barter, G. E., Veers, P., and Namura, N.: Challenges, opportunities, and a research roadmap for downwind wind turbines, Wind Energy, 25, we.2676, https://doi.org/10.1002/we.2676, 2021.
Bottasso, C. L., Croce, A., Savini, B., Sirchi, W., and Trainelli, L.: Aero-servo-elastic modeling and control of wind turbines using finite-element multibody procedures, Multibody Syst. Dyn., 16, 291–308, https://doi.org/10.1007/s11044-006-9027-1, 2006.
Bradney, D., Evans, S., and Clausen, P.: The Effect of Tail Fin Size on the Yaw Performance of Small Wind Turbines Operating in Unsteady Flow, in: Wind Energy Exploitation in Urban Environment, Research Topics in Wind Energy, vol. 8, Springer, Cham, 55–70, https://doi.org/10.1007/978-3-030-13531-7_4, 2019.
Bryne, R. and MacArtain, P.: The 15-year operational experiences of an 850 kW peri-urban wind turbine: Lessons learned from a behind-the-meter installation in Ireland, Energ. Sustain. Develop., 70, 342–360, https://doi.org/10.1016/j.esd.2022.08.011, 2022.
Bukala, J., Damaziak, K., Kroszczynski, K., Malachowski, J., Szafranski, T., Tomaszewski, M., Karimi, H. R., Jozwik, K., Karczewski, M., and Sobczak, K.: Small Wind Turbines: Specification, Design, and Economic Evaluation, in: Wind Turbines – Design, Control and Applications, edited by: Aissaoui, A. G. and Tahour, A., InTechOpen 2016, London, https://doi.org/10.5772/62821, 2016.
Bychkov, N. M., Dovgal, A. V., and Kozlov, V. V.: Magnus wind turbines as an alternative to the blade ones, J. Phys.-Conf. Ser., 75, 012004, https://doi.org/10.1088/1742-6596/75/1/012004, 2007.
Carter Wind Energy: Carter Wind Turbines, https://carterwind.com/, last access: 17 August 2022.
Chagas, C. C. M., Pereira, M. G., Rosa, L. P., da Silva, N. F., Freitas, M. A. V., and Hunt, J. D.: From Megawatts to Kilowatts: A Review of Small Wind Turbine Applications, Lessons From The US to Brazil, Sustainability, 12, 2760, https://doi.org/10.3390/su12072760, 2020.
Clausen, P., Whale, J., and Wood, D.: Small wind and hydrokinetic turbines, ISBN 9781839530722, 2021.
Damiani, R. and Davis, D.: Engineering a Reduction of the Levelized Cost of Energy of Distributed Wind Turbines via Rotor and Control Enhancements, J. Phys.-Conf. Ser., 2265, 042080, https://doi.org/10.1088/1742-6596/2265/4/042080, 2022.
Damiani, R., Davis, D., and Summerville, B.: Challenges and Possible Solutions in Aeroelastic Modeling for the Distributed Wind Turbine Industry, J. Phys.-Conf. Ser., 2265, 042075, https://doi.org/10.1088/1742-6596/2265/4/042075, 2022.
Damota, J., Lamas, I., Couce, A., and Rodríguez, J.: Vertical Axis Wind Turbines: Current Technologies and Future Trends, REPQJ, 1, 530–535, https://doi.org/10.24084/repqj13.389, 2015.
Dayan, E.: Wind energy in buildings, Power generation from wind in the urban environment – where it is needed most, Refocus, 7, 33–34, 36, 38, https://doi.org/10.1016/S1471-0846(06)70545-5, 2006.
Dentons: Italy: The 2019–2020 incentives regime for renewable energy plants, https://www.dentons.com/en/pdf-pages/-/media/fcaeaba3d7424b2da0b0110ec08f6b06.ashx (last access: 17 August 2022), 2020.
Drew, D. R., Barlow, J. F., Cockerill, T. T., and Vahdati, M. M.: The importance of accurate wind resource assessment for evaluating the economic viability of small wind turbines, Renew. Energ., 77, 493–500, https://doi.org/10.1016/j.renene.2014.12.032, 2015
Duchaud, J.-L., Notton, G., Fouilloy, A., and Voyant, C.: Hybrid renewable power plant sizing – Graphical decision tool, sensitivity analysis and applications in Ajaccio and Tilos, Appl. Energy, 254, 113601, https://doi.org/10.1016/j.apenergy.2019.113601, 2019.
Duo, C.: China Medium/Small Wind Industry, Austrian Small Wind Conference, Wien, Austria, https://smallwindconference.com/wp-content/uploads/2018/04/22-Chinas-Medium-and-Small-Wind-Industry-1.pdf (last access: 17 August 2022), 2017.
Duplyakin, D., Zisman, S., Phillips, C., and Tinnesand, H.: Bias Characterization, Vertical Interpolation, and Horizontal Interpolation for Distributed Wind Siting Using Mesoscale Wind Resource Estimates, https://www.nrel.gov/docs/fy21osti/78412.pdf (last access: 17 August 2022), 2021.
DWEA: Smart Wind Roadmap: A Consensus-Based, Shared Vision for the Sustainable Manufacturing, Advanced Research & Technology Action Plan for Distributed Wind, https://distributedwind.org/wp-content/uploads/2016/05/SMART-Wind-Roadmap.pdf (last access: 17 August 2022), 2016.
EAWE: Small Wind Turbine Technical Committee, https://eawe.eu/organisation/committees/small-wind-turbines-technical-committee/ (last access: 17 August 2022), 2020.
Elliott, D. and Infield, D.: An assessment of the impact of reduced averaging time on small wind turbine power curves, energy capture predictions and turbulence intensity measurements: Impact of reduced averaging time on small wind turbine performance, Wind Energ., 17, 337–342, https://doi.org/10.1002/we.1579, 2014.
Ellis, G. and Ferraro, G.: The social acceptance of wind energy, JRC Science for Policy Report, https://pureadmin.qub.ac.uk/ws/portalfiles/portal/123202364/Ellis_Ferraro_2016_JRC103743_Registered.pdf (last access: 17 August 2022), 2016.
Emblin, D.: Small wind turbines: the art of disguise, https://www.youris.com/Energy/Renewables/Small-Wind-Turbines-The-Art-Of-Disguise.kl (last access: 17 August 2022), 2017.
Eunice Energy Group: EW16 Thetis, https://eunice-group.com/projects/ew16-thetis/ (last access: 17 August 2022), 2021.
European Court of Auditors: Electricity production from wind and solar photovoltaic power in the EU, https://www.eca.europa.eu/en/Pages/DocItem.aspx?did=45188 (last access: 17 August 2022), 2018.
Evans, S., Dana, S., Clausen, P., and Wood, D.: A simple method for modelling fatigue spectra of small wind turbine blades, Wind Energy, 24, 549–557, https://doi.org/10.1002/we.2588, 2021.
Evans, S. P., Bradney, D. R., and Clausen, P. D.: Assessing the IEC simplified fatigue load equations for small wind turbine blades: How simple is too simple?, Renew. Energ., 127, 24–31, https://doi.org/10.1016/j.renene.2018.04.041, 2018.
Evans, S. P., Kesby, J. E., Bradley, J., and Clausen, P. D.: Commercialization of a Diffuser Augmented Wind Turbine for Distributed Generation, J. Phys.-Conf. Ser., 1452, 012014, https://doi.org/10.1088/1742-6596/1452/1/012014, 2020.
Feldman, D., Ramasamy, V., Fu, R., Ramdas, A., Desai, J., and Margolis, R.: U.S. Solar Photovoltaic System Cost Benchmark: Q1 2020, https://www.nrel.gov/docs/fy22osti/80694.pdf (last access: 17 August 2022), 2021.
Fields, M. J., Tinnesand, H., and Baring-Gould, E. A.: Distributed Wind Resource Assessment: State of the Industry, https://www.nrel.gov/docs/fy16osti/66419.pdf (last access: 17 August 2022), 2016.
Forsyth, T., Jimenez, T., Preus, R., Tegen, S., and Baring-Gould, I.: The Distributed Wind Cost Taxonomy, https://www.nrel.gov/docs/fy17osti/67992.pdf (last access: 17 August 2022), 2017.
Forsyth, T., Van Dam, J., and Preus, R.: Summary of the International Standards Assessment Forum (ISAF) 2019, 2019.
Gabra, S., Miles, J., and Scott, S. A.: Techno-economic analysis of stand-alone wind micro-grids, compared with PV and diesel in Africa, Renew. Energ., 143, 1928–1938, https://doi.org/10.1016/j.renene.2019.05.119, 2019.
Gigue`re, P. and Selig, M. S.: New Airfoils for Small Horizontal Axis Wind Turbines, J. Sol. Energy Eng., 120, 108–114, https://doi.org/10.1115/1.2888052, 1998.
Global Info Research: Global Small wind Market 2020 by Manufacturers, Regions, Type and Application, Forecast top 2025, https://www.marketstudyreport.com/reports/global-small-wind-turbines-market-2020-by-manufacturers-regions-type-and-application-forecast-to-2025 (last access: 17 August 2022), 2021.
Greek Government Gazette: FEK 3150/B/30-7-2020, 2021.
Hellenic Electricity Distribution Network Operator S. A.: DEDDIE, https://deddie.gr/en/kentro-enhmerwsis/xrhsima-nea/ (last access: 17 August 2022), 2021.
Hemeida, A. M., Omer, A. S., Bahaa-Eldin, A. M., Alkhalaf, S., Ahmed, M., Senjyu, T., and El-Saady, G.: Multi-objective multi-verse optimization of renewable energy sources-based micro-grid system: Real case, Ain Shams Engineering Journal, 13, 101543, https://doi.org/10.1016/j.asej.2021.06.028, 2022.
Hills, R. G., Maniaci, D. C., and Naughton, J. W.: V&v framework, USA, SAND2015-7455, https://www.osti.gov/biblio/1214246-framework (last access: 17 August 2022), 2015.
Holst, D., Pechlivanoglou, G., Kohlrausch, C. T., Nayeri, C. N., and Paschereit, C. O.: sHAWT Design: Airfoil Aerodynamics Under the Influence of Roughness, ASME Turbo Expo 2016: Turbomachinery Technical Conference and Exposition, Seoul, South Korea, 13–17 June 2016, https://doi.org/10.1115/GT2016-56377, 2016.
Holst, D., Pechlivanoglou, G., Wegner, F., Nayeri, C. N., and Paschereit, C. O.: Potential of Retrofit Passive Flow Control for Small Horizontal Axis Wind Turbines, J. Eng. Gas Turbines Power, 139, 032604, https://doi.org/10.1115/1.4034543, 2017.
IEA: IEA WIND 2013 Annual Report, https://nachhaltigwirtschaften.at/resources/iea_pdf/reports/iea_wind_annual_report_2013.pdf (last access: 17 August 2022), 2014.
IEA: Renewables 2019, IEA, Paris, France, Market analysis and forecast from 2019 to 2024, https://www.iea.org/reports/renewables-2019 (last access: 17 August 2022), 2019.
IEA: Solar PV net capacity additions by application segment, 2017–2022, IEA, Paris, France, https://www.iea.org/data-and-statistics/charts/ (last access: 17 August 2022), 2020.
IEC: International Standard: 61400-1 Wind turbines – Part 1: Design Requirements, https://webstore.iec.ch/publication/26423 (last access: 17 August 2022), 2019a.
IEC: International Standard: 61400-2 Wind turbines – Part 2: Design requirements for small wind turbines, https://webstore.iec.ch/publication/5433 (last access: 17 August 2022), 2019b.
Kaldellis, J. K. and Zafirakis, D. P.: Trends, Prospects, and R&D Directions in Wind Turbine Technology, in: Comprehensive Renew. Energ., 2, 671–724, https://doi.org/10.1016/B978-0-08-087872-0.00224-9, 2012.
Karekezi, S.: Renewables in Africa – meeting the energy needs of the poor, Energy Policy, 30, 1059–1069, https://doi.org/10.1016/S0301-4215(02)00058-7, 2002.
Khan, M., Alavi, M., Mohan, N., Azeez, A., Shanif, A., and Javed, B.: Wind Turbine design and fabrication to power street lights, MATEC Web Conf., 108, 08010, https://doi.org/10.1051/matecconf/201710808010, 2017.
Kim, S.: IEA, Country Report: Small Wind in Korea, 2018.
Lo, K.: Renew. Energ.: Are feed-in tariffs going out of style?, Power Technology, April 2018, https://www.power-technology.com/analysis/featurerenewable-energy-are-feed-in-tariffs-going-out-of-style-5718419/ (last access: 17 August 2022), 2018.
McMahon, N. M., Burton, P. R., and Sharman, D. M.: On Electrodynamic Braking for Small Wind Turbines, Wind Engineering, 39, 549–555, https://doi.org/10.1260/0309-524X.39.5.549, 2015.
Meghana, A., Smitha, B., and Jagwani, S.: Technological Advances in Airborne Wind Power: A Review, in: Emerging Research in Computing, Information, Communication and Applications, vol. 790, edited by: Shetty, N. R., Patnaik, L. M., Nagaraj, H. C., Hamsavath, P. N., and Nalini, N., Springer Singapore, Singapore, 349–359, https://doi.org/10.1007/978-981-16-1342-5_28, 2022.
Mertens, S.: The energy yield of roof mounted wind turbines, 27, 507–518, https://doi.org/10.1260/030952403773617472, 2003.
Micallef, D. and van Bussel, G.: A Review of Urban Wind Energy Research: Aerodynamics and Other Challenges, Energies, 11, 2204, https://doi.org/10.3390/en11092204, 2018.
Möllerström, E., Ottermo, F., Hylander, J., and Bernhoff, H.: Noise Emission of a 200 kW Vertical Axis Wind Turbine, Energies, 9, 19, https://doi.org/10.3390/en9010019, 2016.
NREL: Competitiveness Improvement Project, Wind Research, NREL, https://www.nrel.gov/wind/competitiveness-improvement-project.html, last access: 17 August 2022.
NREL, OpenFAST: OpenFAST, https://github.com/OpenFAST, last access: 31 October 2019.
Ning, A., Hayman, G., Damiani, R., and Jonkman, J. M.: Development and Validation of a New Blade Element Momentum Skewed-Wake Model within AeroDyn, in: 33rd Wind Energy Symposium, American Institute of Aeronautics and Astronautics, 33rd Wind Energy Symposium, 5–9 January 2015, Kissimmee, Florida, USA, https://doi.org/10.2514/6.2015-0215, 2015.
Nordic Folkecenter for Renew. Energ.: Folkecenter's Catalogue of small wind turbines – 8th Edition, https://www.folkecenter.eu/PDF/Wind/353.Catalogue-of-small-wind-turbines-8th-edition.pdf (last access: 17 August 2022), 2016.
Ofgem: Environmental programmes, Environmental and social schemes, https://www.ofgem.gov.uk/environmental-programmes (last access: 17 August 2022), 2021.
Ohya, Y., Karasudani, T., Sakurai, A., Abe, K., and Inoue, M.: Development of a shrouded wind turbine with a flanged diffuser, J. Wind Engin. Ind. Aerodynam., 96, 524–539, https://doi.org/10.1016/j.jweia.2008.01.006, 2008.
Orrell, A. C. and Poehlman, E. A.: Benchmarking U.S. Small Wind Costs with the Distributed Wind Taxonomy, Pacific Northwest National Lab. (PNNL), Richland, Washington, USA, https://doi.org/10.2172/1400355, 2017.
Orrell, A. C., Preziuoso, D., Morris, D., and Homer, J.: 2019 Distributed Wind Data Summary, PNNL-30168, https://www.pnnl.gov/sites/default/files/media/file/2019 Distributed Wind Data Summary-10Aug20.pdf (last access: 17 August 2022), 2020.
Orrell, A. C., Kazimierczuk, K., and Sheridan, L.: Distributed Wind Market Report: 2021 Edition, DOE/GO-102021-5620, https://www.energy.gov/eere/wind/articles/distributed-wind-market-report-2021-edition-released (last access: 17 August 2022), 2021.
Papi, F., Pagamonci, L., and Bianchini, A.: Design Loads in Small Wind Turbines: a Detailed Comparison Between Pitch and Stall Regulation, IOP Journal of Physics Conference Series, ATI2022 Conference, paper in publishing, 2022.
Papi, F., Nocentini, A., Ferrara, G., and Bianchini, A.: On the Use of Modern Engineering Codes for Designing a Small Wind Turbine: An Annotated Case Study, Energies, 14, 1013, https://doi.org/10.3390/en14041013, 2021.
Paulsen, U. S., Madsen, H. A., Hattel, J. H., Baran, I., and Nielsen, P. H.: Design Optimization of a 5 MW Floating Offshore Vertical-axis Wind Turbine, Energy Procedia, 35, 22–32, https://doi.org/10.1016/j.egypro.2013.07.155, 2013.
Pillai, U.: Drivers of cost reduction in solar photovoltaics, Energy Economics, 50, 286–293, https://doi.org/10.1016/j.eneco.2015.05.015, 2015.
Pourrajabian, A., Mirzaei, M., Ebrahimi, R., and Wood, D.: Effect of air density on the performance of a small wind turbine blade: A case study in Iran, J. Wind Engin. Ind. Aerodynam., 126, 1–10, https://doi.org/10.1016/j.jweia.2014.01.001, 2014.
PowerHouse Wind: Powerhouse Wind, https://www.powerhousewind.co.nz/, last access: 17 August 2022.
Predescu, M.: Economic evaluation of small wind turbines and hybrid systems for residential use, Renew. Energy Environ. Sustain., 1, 33, https://doi.org/10.1051/rees/2016023, 2016.
Preus, R., Reilly, J., Johnson, J., Baring-Gould, I., and Coddington, M.: Distributed Wind Considerations from the IEEE 1547–2018 Revision, https://www.nrel.gov/docs/fy21osti/78948.pdf (last access: 17 August 2022), 2021.
Reiman, A. P., Homer, J. S., Bhattarai, B., and Orrell, A. C.: Quantifying Technical Diversity Benefits of Wind as a Distributed Energy Resource, in: 2020 IEEE Power & Energy Society Innovative Smart Grid Technologies Conference (ISGT), 2020 IEEE Power & Energy Society Innovative Smart Grid Technologies Conference (ISGT), Washington, DC, USA, 1–5, https://doi.org/10.1109/ISGT45199.2020.9087665, 2020.
Roth, M., Eiter, S., Röhner, S., Kruse, A., Schmitz, S., Frantál, B., Centeri, C., Frolova, M., Buchecker, M., Stober, D., Karan, I., and Van der Horst, D.: Renewable energy and landscape quality, Jovis, Berlin, 295 pp., https://www.jovis.de/en/books/renewable-energy-and-landscape-quality.html (last access: 17 August 2022), 2018.
Schepers, J. G. and Schreck, S. J.: Aerodynamic measurements on wind turbines, WIREs Energy Environ., 8, e320, https://doi.org/10.1002/wene.320, 2019.
Schepers, J. G., Boorsma, K., Madsen, H. A., Pirrung, G. R., Bangga, G., Guma, G., Lutz, T., Potentier, T., Braud, C., Guilmineau, E., Croce, A., Cacciola, S., Schaffarczyk, A. P., Lobo, B. A., Ivanell, S., Asmuth, H., Bertagnolio, F., Sørensen, N. N., Shen, W. Z., Grinderslev, C., Forsting, A. M., Blondel, F., Bozonnet, P., Boisard, R., Yassin, K., Hoening, L., Stoevesandt, B., Imiela, M., Greco, L., Testa, C., Magionesi, F., Vijayakumar, G., Ananthan, S., Sprague, M. A., Branlard, E., Jonkman, J., Carrion, M., Parkinson, S., and Cicirello, E.: IEA Wind TCP Task 29, Phase IV: Detailed Aerodynamics of Wind Turbines, Zenodo [technical report], https://doi.org/10.5281/zenodo.4813068, 2021.
SD Wind Energy: Small Wind Turbines and Energy Systems, https://sd-windenergy.com/, last access: 17 August 2022.
Sedaghat, A.: Magnus type wind turbines: Prospectus and challenges in design and modelling, Renew. Energ., 62, 619–628, https://doi.org/10.1016/j.renene.2013.08.029, 2014.
Selig, M. S.: Low Reynolds Number Airfoil Design – Lecture Notes, Department of Aerospace Engineering, University of Illinois at Urbana-Champaign, Urbana, Illinois, USA, https://m-selig.ae.illinois.edu/pubs/Selig-2003-VKI-LRN-Airfoil-Design-Lecture-Series.pdf (last access: 17 August 2022), 2003.
Senthilvel, G., Vivekanandan, M., Nawas Shareef, H., and Sivabalamurugan, V.: Rural Areas using Savonious Wind Turbine, Renew. Energ., 3, 1–6, https://doi.org/10.5281/zenodo.3903587, 2020.
Sessarego, M. and Wood, D.: Multi-dimensional optimization of small wind turbine blades, Renewables, 2, 9, https://doi.org/10.1186/s40807-015-0009-x, 2015.
Sheridan, L. M., Phillips, C., Orrell, A. C., Berg, L. K., Tinnesand, H., Rai, R. K., Zisman, S., Duplyakin, D., and Flaherty, J. E.: Validation of wind resource and energy production simulations for small wind turbines in the United States, Wind Energ. Sci., 7, 659–676, https://doi.org/10.5194/wes-7-659-2022, 2022.
Shimizu, A.: Vertical axis type magnus wind turbine generator patent, https://patentimages.storage.googleapis.com/67/47/6f/f587d85bee20b5/EP2735733A1.pdf (last access: 17 August 2022), 2013.
Simic, Z., Havelka, J. G., and Bozicevic Vrhovcak, M.: Small wind turbines – A unique segment of the wind power market, Renew. Energ., 50, 1027–1036, https://doi.org/10.1016/j.renene.2012.08.038, 2013.
Sheridan, L. M., Phillips, C., Orrell, A. C., Berg, L. K., Tinnesand, H., Rai, R. K., Zisman, S., Duplyakin, D., and Flaherty, J. E.: Validation of wind resource and energy production simulations for small wind turbines in the United States, Wind Energ. Sci., 7, 659–676, https://doi.org/10.5194/wes-7-659-2022, 2022.
Stathopoulos, T., Alrawashdeh, H., Al-Quraan, A., Blocken, B., Dilimulati, A., Paraschivoiu, M., and Pilay, P.: Urban wind energy: Some views on potential and challenges, J. Wind Engin. Ind. Aerodynam., 179, 146–157, https://doi.org/10.1016/j.jweia.2018.05.018, 2018.
Summerville, B., Van Dam, J., Preus, R., Baring-Gould, I., Forsyth, T., and Bergey, M.: Justification for Updates to ANSI/ACP Small Wind Turbine Standard, NREL/TP-5000-79775, https://www.nrel.gov/docs/fy21osti/79775.pdf (last access: 17 August 2022), 2021.
SWIP Project: European SWIP Project: small wind energy in cities, FuturEnergy, http://swipproject.eu/wp-content/uploads/2015/04/FuturEnergy-Magazine_SWIP.pdf (last access: 17 August 2022), 2014.
Tatchley, C., Paton, H., Robertson, E., Minderman, J., Hanley, N., and Park, K.: Drivers of Public Attitudes towards Small Wind Turbines in the UK, PLoS ONE, 11, e0152033, https://doi.org/10.1371/journal.pone.0152033, 2016.
Timmer, W. A. and van Rooij, R. P. J. O. M.: Summary of the Delft University Wind Turbine Dedicated Airfoils, J. Sol. Energy Eng., 125, 488–496, https://doi.org/10.1115/1.1626129, 2003.
Tinnesand, H. and Sethuraman, L.: Distributed Wind Resource Assessment Framework: Functional Requirements and Metrics for Performance and Reliability Modeling, NREL/TP-5000-72523, https://www.nrel.gov/docs/fy19osti/72523.pdf (last access: 17 August 2022), 2019.
Toja-Silva, F., Colmenar-Santos, A., and Castro-Gil, M.: Urban wind energy exploitation systems: Behaviour under multidirectional flow conditions – Opportunities and challenges, Renew. Sustain. Energ. Rev., 24, 364–378, https://doi.org/10.1016/j.rser.2013.03.052, 2013.
Tozzi Nord: wind turbines, Tozzi Nord, https://www.tozzinord.com/en/categoria-prodotto/wind-turbines, last access: 17 August 2022.
Tzen, E.: Small wind turbines for on grid and off grid applications, IOP Conf. Ser.-Earth Environ. Sci., 410, 012047, https://doi.org/10.1088/1755-1315/410/1/012047, 2020.
US DOE: Wind Technologies Market Report, https://www.energy.gov/sites/prod/files/2016/08/f33/2015-Wind-Technologies-Market-Report-08162016.pdf (last access: 17 August 2022), 2015.
US DOE WindExchange: Community Wind Energy, https://windexchange.energy.gov/markets/community, last access: 17 August 2022.
Van Treuren, K. W.: Small-Scale Wind Turbine Testing in Wind Tunnels Under Low Reynolds Number Conditions, J. Energy Resour. Technol., 137, 051208, https://doi.org/10.1115/1.4030617, 2015.
Vaz, J. R. P., Wood, D. H., Bhattacharjee, D., and Lins, E. F.: Drivetrain resistance and starting performance of a small wind turbine, Renew. Energ., 117, 509–519, https://doi.org/10.1016/j.renene.2017.10.071, 2018.
Veers, P., Dykes, K., Lantz, E., Barth, S., Bottasso, C. L., Carlson, O., Clifton, A., Green, J., Green, P., Holttinen, H., Laird, D., Lehtomäki, V., Lundquist, J. K., Manwell, J., Marquis, M., Meneveau, C., Moriarty, P., Munduate, X., Muskulus, M., Naughton, J., Pao, L., Paquette, J., Peinke, J., Robertson, A., Rodrigo, J. S., Sempreviva, A. M., Smith, J. C., Tuohy, A., and Wiser, R.: Grand challenges in the science of wind energy, Science, 366, p. eaau2027, https://doi.org/10.1126/science.aau2027, 2019.
Visser, K. D.: Real-world development challenges of the Clarkson University 3 meter ducted wind turbine, J. Phys.-Conf. Ser., 2265, 042072, https://doi.org/10.1088/1742-6596/2265/4/042072, 2022.
Wang, U.: Why corporations like Microsoft are investing in renewable energy, The Guardian, online newspaper, https://www.theguardian.com/sustainable-business/microsoft-walmart-google-renewable-energy-wind-farm-solar (last access: 17 August 2022), 2013.
Wen, T. W., Palanichamy, C., and Ramasamy, G.: Small Wind Turbines as Partial Solution for Energy Sustainability of Malaysia, International Journal of Energy Economics and Policy, 9, 257–266, 2019.
Wilson, S. V. R., Clausen, P. D., and Wood, D. H.: Gyroscopic moments on small wind turbine blades at high yaw rates, Australian Journal of Mechanical Engineering, 5, 1–8, https://doi.org/10.1080/14484846.2008.11464529, 2008.
WINEUR project: Publishable Result-Oriented Report – WINEUR Wind Energy Integration in the Urban Environment Grant agreement no. EIE/04/130/S07.38591, https://adoc.pub/publishable-result-oriented-report.html (last access: 17 August 2022), 2005.
Wolsink, M.: Wind Power wind power: Basic Challenge Concerning Social Acceptance wind power social acceptance, in: Renewable Energy Systems, edited by: Kaltschmitt, M., Themelis, N. J., Bronicki, L. Y., Söder, L., and Vega, L. A., Springer New York, New York, USA, 1785–1821, https://doi.org/10.1007/978-1-4614-5820-3_88, 2013.
Wood, D.: Small wind turbines, Springer, ISBN 9781849961752, 2011.
Wright, A. K. and Wood, D. H.: Yaw Rate, Rotor Speed and Gyroscopic Loads on a Small Horizontal Axis Wind Turbine, Wind Engineer., 31, 197–209, https://doi.org/10.1260/030952407781998837, 2007.
XZERES: Wind Turbines, XZERES Wind Europe Ltd, https://it.wind-turbine-models.com/manufacturers/533-xzeres-wind, last access: 17 August 2022.
- Abstract
- Introduction
- Diffusion of small wind turbines
- Economic aspects
- Status of the technology
- Grand challenges for small wind turbine technology
- Conclusions
- Code and data availability
- Author contributions
- Competing interests
- Disclaimer
- Acknowledgements
- Financial support
- Review statement
- References
- Article
(6219 KB) - Full-text XML
- Abstract
- Introduction
- Diffusion of small wind turbines
- Economic aspects
- Status of the technology
- Grand challenges for small wind turbine technology
- Conclusions
- Code and data availability
- Author contributions
- Competing interests
- Disclaimer
- Acknowledgements
- Financial support
- Review statement
- References